-Huaxiao stainless steel manufacturers
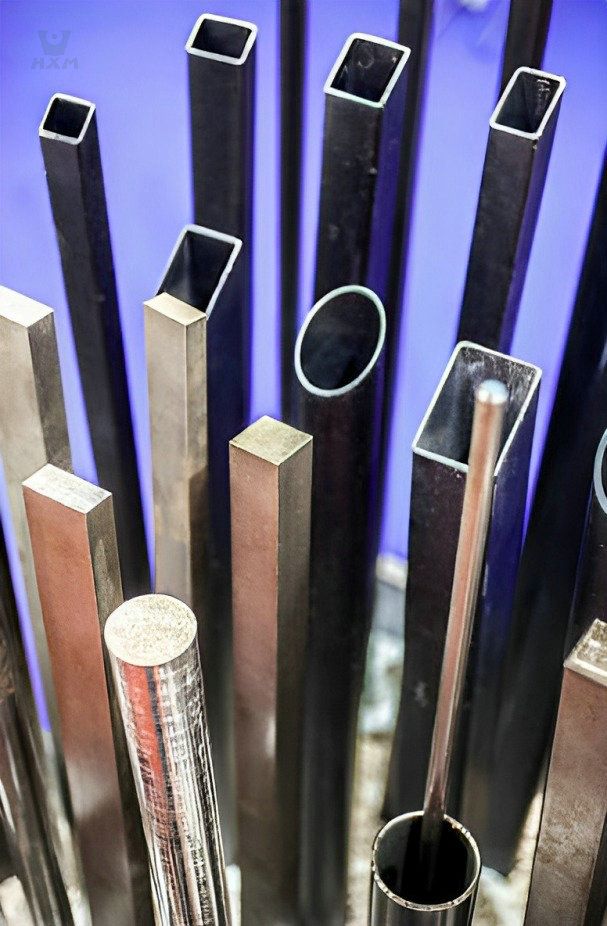
316 VS 316L:
what's the difference?
Stainless steel is an alloy known for its resilience and versatility, making it a star in industries ranging from architecture to healthcare. But within the stainless steel realm, a subtle yet significant distinction exists – the difference between 316 and 316L. These two grades might seem almost identical, but hidden beneath their surface lie crucial disparities. In this exploration, we’ll dissect these stainless steel cousins, revealing their unique properties and applications, ensuring that you can confidently choose the one that suits your needs.
what's the difference between 316 and 316L?
The primary difference between 316 and 316L stainless steel lies in their carbon content. Both alloys consist of iron, chromium, nickel, and molybdenum, which provide excellent corrosion resistance. However, 316L contains lower carbon content, making it ‘low carbon.‘ This reduction in carbon levels enhances its weldability and minimizes the risk of sensitization, a process that can make stainless steel vulnerable to corrosion. As a result, 316L is the preferred choice for applications that involve welding and exposure to corrosive environments, such as chemical processing, medical devices, and marine equipment, ensuring both strength and longevity.
316 VS 316L
table of content
316 VS 316L
composition
Element | 316 Stainless Steel | 316L Stainless Steel |
---|---|---|
Chromium (Cr) | 16-18% | 16-18% |
Nickel (Ni) | 10-14% | 10-14% |
Molybdenum (Mo) | 2-3% | 2-3% |
Carbon (C) | ≤0.08% | ≤0.03% |
Iron (Fe) | Balanced (Remaining) | Balanced (Remaining) |
The Composition of 316 Stainless Steel
Stainless steel, a remarkable material known for its corrosion resistance, durability, and versatility, is the result of an intricate alloying process. Among its many grades, 316 stainless steel stands out for its remarkable properties. To truly comprehend what makes 316 stainless steel unique, we must dive into its composition.
-
Iron as the Foundation:
At the core of 316 stainless steel is iron (Fe), comprising approximately 62% to 72% of its composition. Iron serves as the structural backbone, providing strength and stability to the alloy. -
The Role of Chromium (Cr):
Chromium is a pivotal element in 316 stainless steel, making up about 16% to 18% of the composition. This element is responsible for the alloy's exceptional corrosion resistance. When exposed to oxygen, a thin, self-healing oxide layer of chromium oxide forms on the surface, preventing further oxidation and rust. -
Nickel (Ni) for Versatility:
Nickel, accounting for approximately 10% to 14%, enhances 316 stainless steel's versatility. It provides excellent resistance to various corrosive environments, particularly those containing acids and seawater. Nickel also plays a role in maintaining the stability of the austenitic structure. -
Molybdenum (Mo) for Enhanced Resistance:
The addition of molybdenum in a range of 2% to 3% significantly improves 316 stainless steel's resistance to pitting and crevice corrosion in chloride-rich environments, such as marine settings and chemical processing. -
Additional Alloying Elements:
While the elements mentioned above are the primary constituents, 316 stainless steel may also contain small amounts of other elements like carbon, silicon, manganese, phosphorus, sulfur, and nitrogen. These trace elements can influence various properties of the alloy, such as weldability and machinability. -
The Scientific Precision in Manufacturing:
The production of 316 stainless steel is a carefully controlled process. The alloy's composition is meticulously measured and mixed. Each element is added by stainless steel manufacturers with precision to achieve the desired chemical makeup, ensuring that the final product exhibits the exceptional characteristics it's known for.
Stainless steel manufacturers, with their deep understanding of material science, employ state-of-the-art methods like electric arc furnaces to melt and refine the alloy’s composition. The resulting liquid steel is then cast into various forms such as bars, sheets, or pipes, where it will find its way into numerous applications, from marine equipment to medical devices.
In summary, 316 stainless steel’s composition is a blend of iron, chromium, nickel, molybdenum, and trace elements. Each component plays a crucial role in imparting the alloy’s exceptional corrosion resistance, mechanical strength, and overall performance. Its precise control during the manufacturing process, carried out by skilled stainless steel manufacturers, is a testament to the scientific precision behind this remarkable material.
The Composition of 316L Stainless Steel
316L stainless steel is a low-carbon variation of the widely used 316 stainless steel. Its composition primarily consists of:
- Chromium (Cr): Comprising approximately 16-18% of its composition, chromium contributes to the alloy's exceptional corrosion resistance. By forming a thin, self-healing oxide layer on the surface when exposed to oxygen, it prevents corrosion and staining.
- Nickel (Ni): With about 10-14% nickel content, this element enhances the steel's resistance to various corrosive environments. Nickel also plays a role in maintaining an austenitic crystal structure, which is vital for its non-magnetic property and excellent formability.
- Molybdenum (Mo): Constituting 2-3% of its composition, molybdenum significantly boosts resistance to pitting and crevice corrosion, particularly in chloride-rich settings. This element expands the alloy's suitability for applications involving marine environments and chemical processing.
- Iron (Fe): Iron forms the matrix of the alloy, providing structural integrity and the ability to maintain its form under various conditions.
- Carbon (C): 316L stainless steel contains a low carbon content, usually less than 0.03%. This minimal carbon content is a key differentiator from standard 316 stainless steel. It is essential in preventing sensitization during welding, where carbon can combine with chromium to form carbides at grain boundaries. This process can compromise the alloy's corrosion resistance.
In conclusion, the careful balance of elements in 316L stainless steel makes it a versatile and highly reliable material for various critical applications. Stainless steel manufacturers recognize its significance, and its usage continues to expand in industries that demand exceptional corrosion resistance, formability, and weldability.
316 VS 316L
Mechanical Properties
Mechanical Property | 316 Stainless Steel | 316L Stainless Steel |
---|---|---|
Tensile Strength (MPa) | 515 – 695 | 485 – 680 |
Yield Strength (0.2% Offset) (MPa) | 205 – 240 | 170 – 186 |
Elongation (%) | 35 – 45 | 35 – 45 |
Hardness (Brinell, HB) | 149 (typical) | 149 (typical) |
Impact Resistance (Joules) | 77 (at -60°C) (typical) | 74 (at -70°C) (typical) |
The mechanical property of 316 Stainless Steel
- Tensile Strength: 316 stainless steel, due to its composition of chromium and nickel, exhibits high tensile strength, typically in the range of 515-620 MPa. This means it can withstand significant tensile loads before deformation or fracture occurs.
- Yield Strength: The yield strength of 316 stainless steel is about 205 MPa, indicating the stress at which the material starts to deform plastically. It's an important parameter for design considerations.
- Hardness: 316 stainless steel is known for its excellent hardness, typically with a Rockwell hardness of 79 HRB. This hardness level ensures its durability in various applications.
- Ductility: One of the mechanical advantages of 316 stainless steel is its high ductility. It can undergo extensive deformation without breaking. This property is crucial in applications where bending and forming are involved.
- Fatigue Resistance: 316 stainless steel also demonstrates good resistance to fatigue. It can endure repeated cyclic loads, making it suitable for applications that undergo stress variations over time.
- Toughness: Toughness is an essential mechanical property, indicating a material's ability to absorb energy and resist brittle fracture. 316 stainless steel's toughness is enhanced by its nickel and molybdenum content.
- Corrosion Resistance: While not a typical mechanical property, the excellent corrosion resistance of 316 stainless steel should be noted. This resistance to corrosion is vital in various environments, especially those exposed to moisture, salt, or chemicals.
316 stainless steel manufacturers take these mechanical characteristics into account during the production process to ensure that the final product meets the required standards and specifications. These properties make 316 stainless steel a versatile material suitable for applications in various industries.
The mechanical property of 316L Stainless Steel
- Improved Weldability: The lower carbon content in 316L (typically limited to 0.03% maximum) significantly improves its weldability compared to 316 stainless steel. Excessive carbon can lead to sensitization, which makes the material susceptible to intergranular corrosion after welding. 316L's lower carbon content minimizes this risk, making it the preferred choice for welding applications.
- Enhanced Corrosion Resistance: While this aspect is more related to corrosion resistance than pure mechanical properties, the lower carbon content in 316L contributes to its resistance against sensitization. Sensitization is a process where the chromium-carbide precipitation at grain boundaries can lead to reduced corrosion resistance. The low carbon content in 316L helps maintain its corrosion resistance, even after exposure to high-temperature welding.
- Slightly Lower Hardness: Due to the reduced carbon content, 316L may exhibit slightly lower hardness than 316 stainless steel. However, this variation is generally minimal and may not be significant in most practical applications.
- Unaltered Tensile and Yield Strength: While the carbon content affects various aspects of steel behavior, it typically has little to no effect on the tensile and yield strengths of 316L. Thus, the tensile strength remains high, usually within the range of 485-585 MPa, and the yield strength at around 170 MPa.
316L stainless steel manufacturers take meticulous steps in controlling and adjusting the carbon content during production to achieve the desired mechanical properties. By doing so, they ensure that the material maintains its strength, durability, and corrosion resistance while being more suitable for welding applications.
When to choose 316 VS 316L based on mechanical needs
Mechanical Requirement | 316 Stainless Steel | 316L Stainless Steel |
---|---|---|
Weldability | Suitable for welding, but may be susceptible to sensitization during high-temperature welding processes. | Excellent weldability with minimal risk of sensitization or intergranular corrosion, making it ideal for welding applications. |
Tensile Strength | Similar tensile strength between 316 and 316L. | Similar tensile strength between 316 and 316L. |
Hardness | Similar hardness; minimal difference between the two. | Similar hardness; minimal difference between the two. |
Corrosion Resistance | Excellent corrosion resistance in both materials. | Excellent corrosion resistance in both materials. |
Cost | Generally slightly more cost-effective. | Slightly more expensive due to additional processing to reduce carbon content. |
316 VS 316L
Corrosion Resistance
The key difference between 316 vs 316L stainless steel lies in the lower carbon content of 316L. This seemingly minor change significantly enhances its resistance to corrosion. In the case of 316 stainless steel, the presence of a higher carbon content makes it more susceptible to sensitization, a process where chromium carbides form along the grain boundaries during welding or high-temperature exposure. These carbides can deplete the chromium in the surrounding regions, reducing the steel’s corrosion resistance.
316L, on the other hand, with its reduced carbon content, effectively prevents the formation of chromium carbides, maintaining the steel’s full corrosion resistance even in challenging environments. It’s highly resistant to various forms of corrosion, including pitting and crevice corrosion, which makes it suitable for marine applications and environments with exposure to chlorides like swimming pools or desalination equipment.
316 VS 316L
Weldability
Weldability is a critical factor in determining the practical utility of stainless steel. Both 316 and 316L stainless steel exhibit good weldability. However, the presence of a lower carbon content in 316L provides a notable advantage in this aspect.
The lower carbon content in 316L, typically below 0.03%, minimizes the risk of sensitization during welding. Sensitization occurs when chromium carbides form along the grain boundaries of stainless steel, depleting the surrounding regions of chromium. This can compromise the steel’s corrosion resistance. In 316 stainless steel, with a higher carbon content, there’s a greater propensity for sensitization during welding or exposure to high temperatures.
In contrast, 316L’s lower carbon content effectively prevents sensitization, ensuring that the weld zone and the adjacent areas maintain their corrosion resistance. This makes 316L an excellent choice for welding applications, particularly when joining pieces or constructing equipment for industries where corrosion resistance is paramount, such as chemical processing, food production, and pharmaceutical manufacturing.
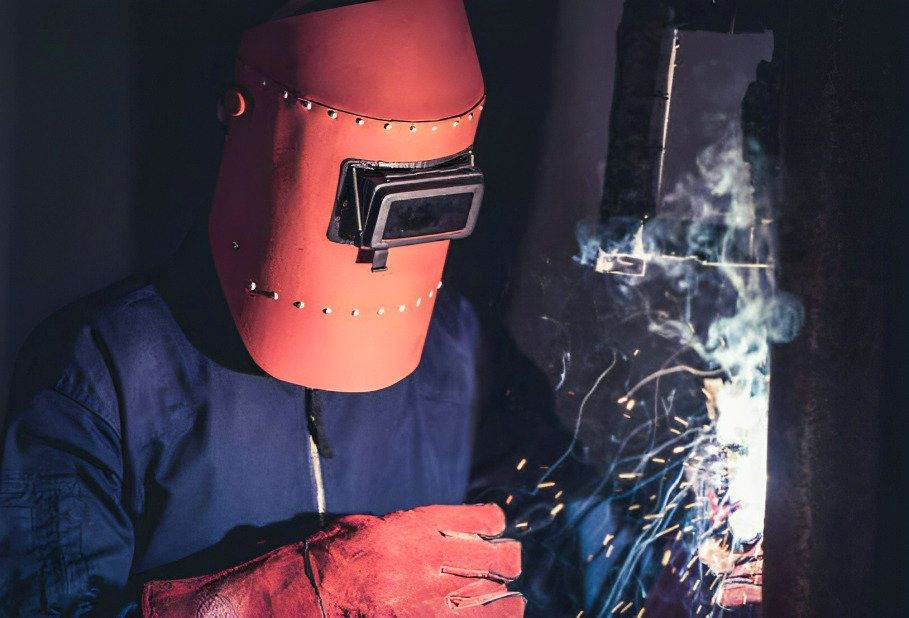
-Huaxiao stainless steel manufacturers
Choosing between 316 VS 316L for welding applications
Aspect | 316 Stainless Steel | 316L Stainless Steel |
Sensitization & Corrosion Resistance | – Contains higher carbon (typically around 0.08%) | – Contains lower carbon (usually below 0.03%) |
– May be prone to sensitization during welding | – No risk of sensitization during welding | |
– Corrosion resistance in welded areas may be compromised | – Consistent corrosion resistance in weld zones and adjacent areas | |
Versatility & Application Needs | – Excellent corrosion resistance, suitable for corrosive environments | – Ideal for welding applications demanding corrosion resistance |
– Suitable for high-corrosion environments | – Often preferred in industries like chemical processing, pharmaceuticals, and food production | |
Considerations | – Choose when exceptional corrosion resistance is the top priority | – Choose for applications demanding both corrosion resistance and welding properties |
316 VS 316L
Cost Considerations
1
Analyzing cost differences:316 VS 316L
Typically, 316L stainless steel is slightly more expensive than 316 stainless steel due to the extra refining process required to reduce carbon content.
It’s essential to obtain accurate pricing from reputable stainless steel manufacturers to make informed cost-related decisions.
2
Balancing material costs with the benefits of each alloy
For applications where exceptional corrosion resistance is the top priority, the slightly higher cost of 316L may be justified.
In situations where welding properties and corrosion resistance are both required, the additional cost of 316L might be offset by its advantages.
3
Factors to consider when making cost-based decisions
When considering costs, factors like material availability, project budget, and long-term performance should be assessed.
Evaluate the entire life cycle of the project to determine whether the cost difference between 316 and 316L justifies the chosen alloy.
316 VS 316L
conclusion
In conclusion, the distinction between 316 and 316L stainless steel lies primarily in their carbon content and the subsequent impact on their mechanical, corrosion resistance, and weldability properties. While 316 offers excellent general-purpose corrosion resistance, 316L, with its lower carbon content, excels in applications where sensitization and intergranular corrosion are concerns.
Stainless steel manufacturers provide these alloys to cater to diverse industry needs, emphasizing the significance of informed alloy selection. Depending on your project’s requirements, it’s vital to make a conscious choice between these two outstanding materials.
The proper selection of 316 vs 316L can greatly affect the long-term performance and durability of your application, which makes understanding the differences between them crucial. The key to success is to consult with stainless steel suppliers, carefully evaluate your project’s specific demands, and make well-informed decisions that align with your goals.