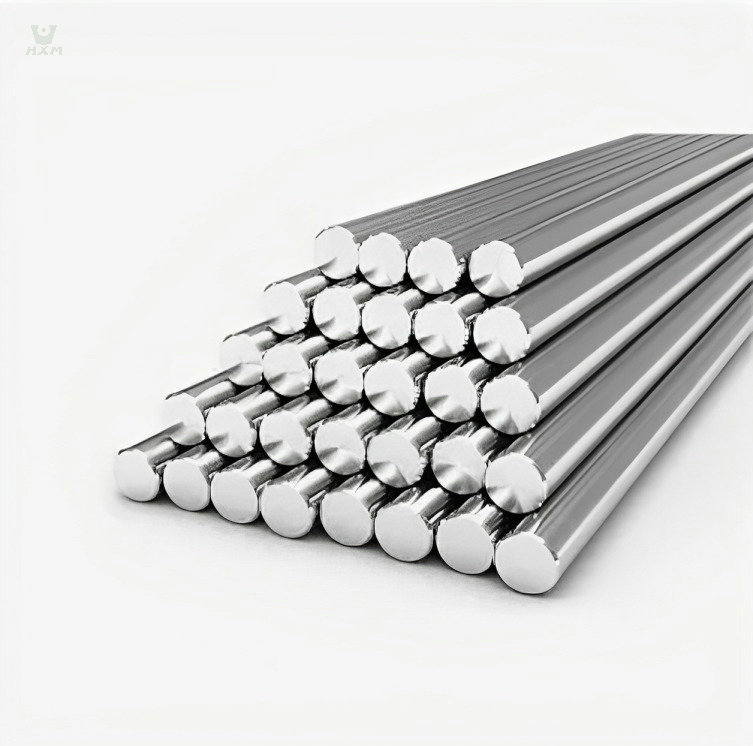
430 Stainless Steel Bar Supplier In China
Diameter: 3mm-480mm, 1/8″ to 2 1/4″
Standard: GB1220, ASTM A484/484M, EN 10060/ DIN 1013 ASTM A276, EN 10278, DIN 671
Shape: round, flat, square, angle, hexagonal
Finish: Black, NO.1, mill finish, cold draw, H9, H11
product description of 430 stainless steel bar
The 430 stainless steel bar is a versatile and widely utilized ferritic stainless steel with excellent mechanical properties. It stands out for its remarkable combination of properties, making it an ideal choice for various applications. With a substantial chromium content, typically ranging from 12-18%, this stainless steel exhibits remarkable ductility and formability, making it an appealing option for manufacturers.
What sets the 430 stainless steel bar apart is its remarkable resistance to strong acid corrosion, which is attributed to its high chromium levels. Moreover, it exhibits exceptional resistance to oxidation, making it a preferred material in challenging environments.
For applications where maximum corrosion resistance is paramount, polishing or buffing the 430 stainless steel bar is highly recommended. Its ability to resist nitric acid attack makes it an excellent choice for specific chemical applications. However, it’s important to note that extended exposure to temperatures in the 400-600°C range can result in brittleness at room temperature.
When it comes to processing and fabrication, the 430 stainless steel bar is not hardenable by thermal treatment. In cases where welding is necessary, pre-heating at temperatures between 150-200°C is advised to mitigate potential issues. Post-weld annealing at temperatures ranging from 790-815°C can help alleviate embrittlement in the weld metal and heat-affected zone.
In summary, the 430 stainless steel bar’s impressive combination of mechanical properties, resistance to corrosion, and suitability for diverse applications makes it a reliable choice for various industries. Whether you need it for automotive components, kitchen appliances, or challenging chemical environments, this stainless steel grade is a versatile and robust material.
specification of 430 stainless steel bar
Chemical Composition Of 430 Stainless Steel Bar
Element | Composition (%) |
---|---|
Chromium (Cr) | 12.0 – 18.0 |
Nickel (Ni) | ≤ 0.75 |
Manganese (Mn) | ≤ 1.00 |
Silicon (Si) | ≤ 1.00 |
Phosphorus (P) | ≤ 0.040 |
Sulfur (S) | ≤ 0.030 |
Carbon (C) | ≤ 0.12 |
physical property Of 430 Stainless Steel Bar
Property | Value |
---|---|
Density (g/cm³) | 7.75 |
Melting Range (°C) | 1425-1510 |
Specific Heat (J/kg·K) | 460 |
Electrical Resistivity (μΩ·m) | 600 |
Thermal Conductivity (W/m·K) | 24.2 (at 100°C) |
Coefficient of Expansion (μm/m·K) | 10.4 (at 20-100°C) |
mechanical property Of 430 SS Bar
Property | Value |
---|---|
Tensile Strength (MPa) | 450 – 600 |
Yield Strength (MPa) | ≥ 205 |
Elongation (%) | ≥ 22 |
Hardness (Brinell, HB) | ≤ 183 |
Modulus of Elasticity (GPa) | 200 |
features of 430 stainless steel bar
The 430 stainless steel bar is distinguished by its elevated chromium content, which typically falls within the range of 12-18%. This high chromium content is a pivotal contributor to its exceptional ductility and formability characteristics. Chromium, a transition metal, plays a fundamental role in enhancing the material’s mechanical properties. It promotes the formation of a stable and protective oxide layer on the surface of the stainless steel, which is crucial for its corrosion resistance.
In a more detailed explanation, the presence of chromium facilitates the creation of a passive chromium oxide layer (Cr2O3) on the surface of the steel. This oxide layer acts as a barrier, effectively shielding the underlying material from corrosive elements and oxidative processes. Furthermore, it significantly improves the steel’s ability to withstand deformation without fracture, thereby imparting notable ductility and formability. This makes the 430 stainless steel bar highly versatile, allowing it to be readily shaped and manipulated to suit a variety of applications, ranging from automotive components to kitchenware. The balance between its high chromium content and its resulting mechanical properties makes it an excellent choice for engineering solutions that require both durability and malleability.
Corrosion resistance is a defining characteristic of the 430 stainless steel bar. This specific stainless steel grade exhibits exceptional resistance to the corrosive effects of strong acids, rendering it particularly well-suited for deployment in environments where corrosive substances are prevalent. The basis of its impressive corrosion resistance lies in its high chromium content, typically ranging between 12% and 18%.
The resistance to strong acid corrosion is primarily a result of the robust passivation behavior of chromium. In the presence of oxygen, chromium forms a chromium oxide (Cr2O3) protective layer on the surface of the steel. This oxide layer serves as a formidable barrier against the corrosive action of acids, effectively preventing them from penetrating the underlying material. The stability and tenacity of the chromium oxide layer make it particularly resistant to dissolution in acidic solutions, further enhancing the steel’s durability in harsh chemical environments.
Moreover, the high levels of chromium contribute to the steel’s resistance to oxidation, which extends its service life and maintains its structural integrity even in challenging conditions. Oxidation resistance is critical as it safeguards the steel from the detrimental effects of environmental factors such as moisture, heat, and the presence of oxygen. By inhibiting the formation of iron oxide (rust) on the surface, the high chromium content enhances the 430 stainless steel bar’s ability to endure prolonged exposure to oxidizing agents, making it a reliable choice for applications where durability is paramount.
In summary, the 430 stainless steel bar’s extraordinary corrosion resistance, particularly against strong acids, is rooted in the formation of a protective chromium oxide layer, while its high chromium content further fortifies its resistance to oxidation. These attributes collectively render it a valuable material for use in challenging and corrosive environments, where the preservation of material integrity is essential.
Polishing, when employed meticulously on the 430 stainless steel bar, plays a pivotal role in optimizing its corrosion resistance. This process is particularly advantageous in applications where the utmost corrosion resistance is a primary concern. The key to this enhancement lies in the refinement of the steel’s surface topography, which, when executed with precision, contributes to its enduring performance.
Polishing, in essence, is the methodical alteration of the steel’s surface texture, resulting in a smoother and more uniform finish. This mechanical alteration involves the removal of minute imperfections, irregularities, and micro-scale asperities that might exist on the steel’s surface. As a consequence, the polished surface is notably more homogeneous, and this consistency aids in the formation of a robust protective chromium oxide (Cr2O3) layer on the steel’s exterior.
The critical mechanism at play is the ability of the polished surface to facilitate the adherence and stability of the chromium oxide layer. A smoother and more even surface provides a superior platform for the formation of this protective barrier. The chromium oxide layer, once established, acts as a formidable shield against the corrosive actions of environmental factors, including moisture and aggressive chemicals.
Furthermore, the enhanced corrosion resistance attributed to polishing significantly extends the lifespan of the 430 stainless steel bar. This is especially important in applications where the material is exposed to prolonged and demanding conditions. The polished surface’s efficacy in preserving the steel’s structural integrity and preventing corrosion-related degradation makes it a vital consideration in environments where long-term performance and corrosion resistance are paramount.
In conclusion, the meticulous process of polishing the 430 stainless steel bar is a scientifically driven approach to optimizing its corrosion resistance. By refining the surface topography, it fosters the formation of a durable chromium oxide layer, thereby ensuring a long-lasting performance, which is of great significance in applications where maximum corrosion resistance is a critical requirement.
Chemical resistance is a defining characteristic of the 430 stainless steel bar, and its capacity to withstand the corrosive effects of specific chemicals, notably nitric acid, makes it an excellent choice for applications where durability and resistance to corrosive substances are of paramount importance.
The steel’s ability to resist nitric acid attack can be elucidated by understanding the underlying chemical reactions. Nitric acid (HNO3) is a powerful oxidizing agent that poses a significant challenge to many materials due to its highly reactive nature. When in contact with the 430 stainless steel, the high chromium content of the steel plays a central role in mitigating the corrosive effects.
Chromium in the stainless steel forms a chromium oxide (Cr2O3) layer on the surface, which acts as a barrier against chemical attack. In the presence of nitric acid, this chromium oxide layer remains stable, even in acidic conditions. It effectively prevents the acid from penetrating the underlying steel substrate and hinders the oxidation of the steel. This resistance to nitric acid is a testament to the robust and enduring nature of the protective oxide layer.
The 430 stainless steel bar’s resistance to nitric acid positions it as a valuable material in applications where exposure to aggressive chemicals is a constant. Whether in chemical processing, laboratory settings, or industrial environments, its ability to endure the corrosive impact of nitric acid ensures that it maintains its structural integrity and performance over time.
In summary, the 430 stainless steel bar’s chemical resistance, particularly its resistance to nitric acid, is underpinned by the formation and stability of the chromium oxide layer. This property makes it exceptionally well-suited for specific chemical applications where durability and resistance to corrosive substances are essential requirements.
Heat sensitivity is an essential consideration when dealing with the 430 stainless steel bar. While this stainless steel grade exhibits impressive mechanical and corrosion-resistant properties, it is imperative to acknowledge its susceptibility to changes in temperature, particularly when exposed to a range of 400-600°C. This temperature range can induce a phenomenon known as embrittlement, which may compromise the material’s structural integrity.
The brittleness observed in the 430 stainless steel bar after extended exposure to temperatures between 400-600°C can be attributed to the transformation of its microstructure. At elevated temperatures within this range, the steel undergoes a process known as sensitization, where chromium carbides (Cr23C6) tend to precipitate along the grain boundaries. This precipitation depletes the steel of available chromium, which is essential for the formation and stability of the protective chromium oxide (Cr2O3) layer. As a result, the material becomes more susceptible to corrosion and more brittle at room temperature.
To mitigate the adverse effects of heat sensitivity, careful consideration of temperature conditions is imperative for specific applications. This is particularly relevant in industries where the 430 stainless steel bar is exposed to elevated temperatures. Precautionary measures, such as maintaining the material within a temperature range that avoids sensitization or selecting alternative stainless steel grades with higher temperature resistance, may be warranted to ensure the material’s long-term performance.
In conclusion, the heat sensitivity of the 430 stainless steel bar, manifested as embrittlement after prolonged exposure to temperatures in the 400-600°C range, is a scientifically understood phenomenon. Prudent management of temperature conditions is essential to safeguard the material’s mechanical properties and corrosion resistance, making it suitable for a variety of applications while avoiding the risk of sensitization-induced brittleness.
application of 430 stainless steel bar
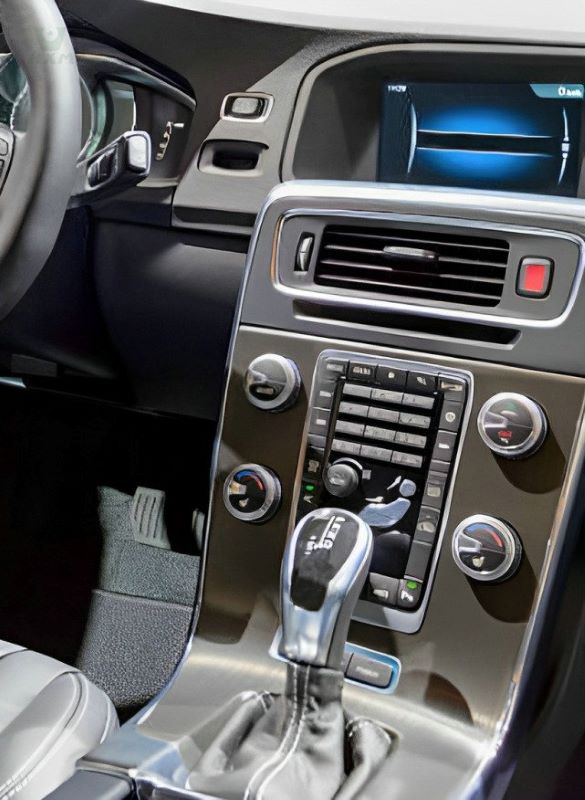
Automotive Trim
The incorporation of 430 stainless steel in automotive trim components is a strategic choice. Its utilization enhances not only the aesthetics but also the durability of these elements. The material's corrosion resistance, attributed to its chromium content, plays a pivotal role in safeguarding trim components against environmental factors, such as moisture and road salts. Additionally, the steel's excellent formability and ductility characteristics make it amenable to precise shaping and detailing, allowing manufacturers to achieve intricate and aesthetically pleasing designs. This, in turn, contributes to the overall aesthetics and visual appeal of the vehicle.
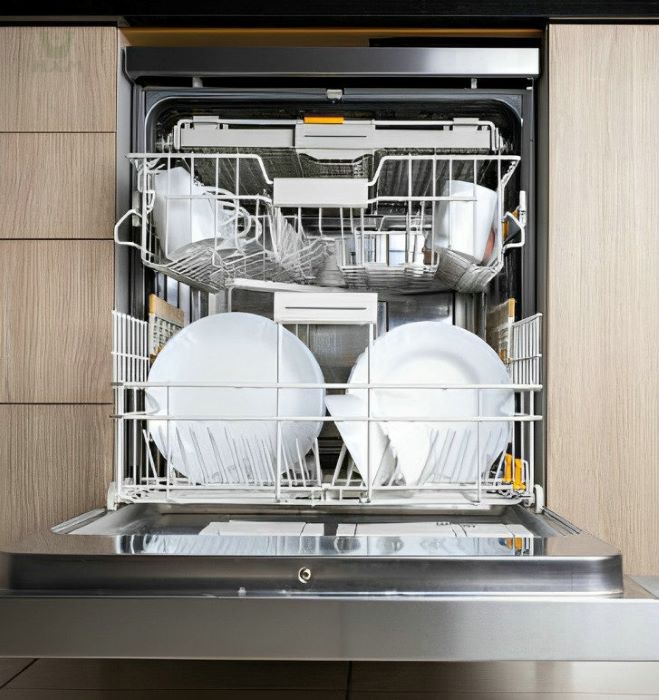
Dishwashers
The 430 stainless steel's resistance to corrosion renders it a primary candidate for use in the production of dishwasher parts. Dishwashers operate in a demanding environment, subject to constant exposure to water, detergents, and high humidity levels. The stainless steel's innate ability to withstand these corrosive conditions is a result of its high chromium content, which enables the formation of a stable chromium oxide layer on its surface. This protective layer acts as a shield against the corrosive effects of detergents and moisture, ensuring the longevity and reliability of dishwasher components.
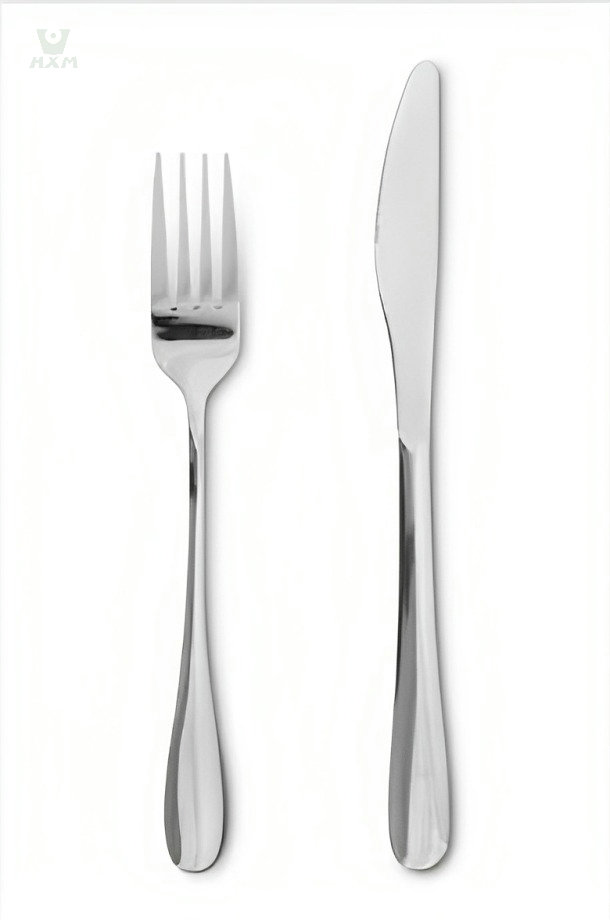
Flatware
The formability and ductility of 430 stainless steel are highly advantageous in the creation of flatware items. Its malleability allows for intricate and precise shaping, resulting in well-crafted and aesthetically pleasing flatware. Moreover, the steel's corrosion resistance ensures that flatware remains durable and hygienic, even when exposed to various food acids and washing processes. This makes it a preferred choice for flatware items, where both functionality and visual appeal are critical.
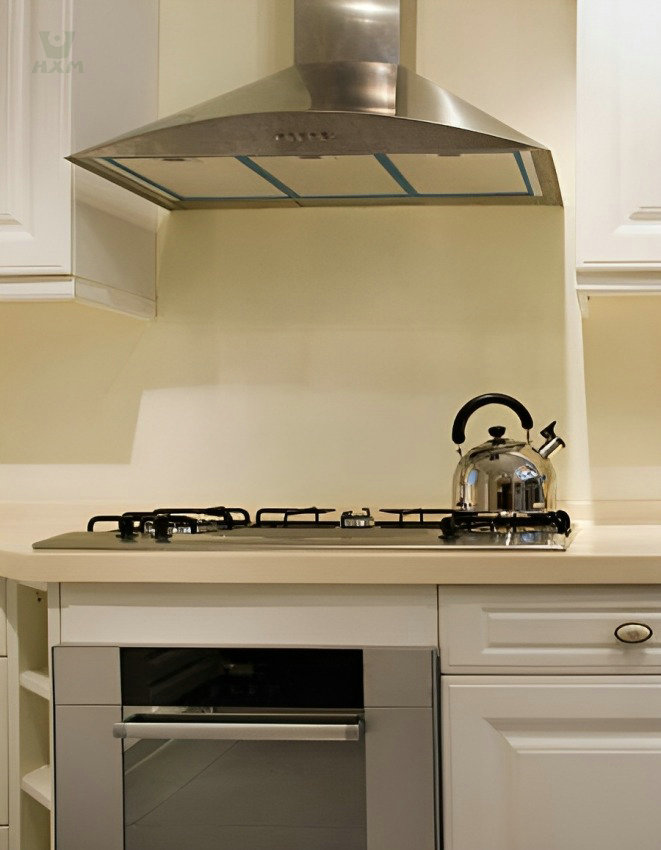
Range Hoods
Range hoods are exposed to a mixture of airborne contaminants, including grease and cooking fumes, which can be corrosive over time. The 430 stainless steel bar's resistance to such corrosive environments makes it a suitable choice for constructing range hoods. The steel's high chromium content enables it to develop a protective chromium oxide layer, which effectively prevents the corrosive substances from degrading the material. This property ensures that range hoods made from 430 stainless steel continue to function optimally while maintaining their appearance and structural integrity.
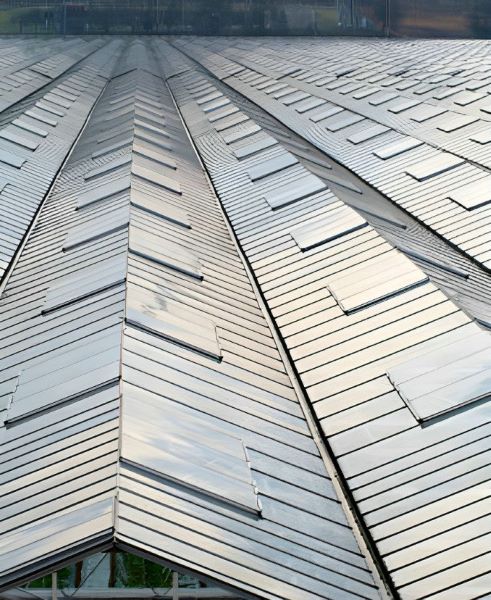
Roofing Equipment
Roofing equipment fabricated from the 430 stainless steel grade offers a combination of long-lasting performance and resistance to environmental factors. The steel's ability to withstand exposure to moisture, temperature fluctuations, and the effects of the external environment is a result of its corrosion-resistant properties. This, in turn, ensures that roofing equipment remains structurally sound and visually appealing over its operational lifespan, even in challenging weather conditions.
FAQ
The term “430” in stainless steel corresponds to a specific grade within the austenitic-ferritic or ferritic stainless steel category. It signifies the chemical composition and material properties of the stainless steel alloy. In scientific terms, “430” represents a stainless steel alloy primarily composed of iron (Fe), chromium (Cr), and varying levels of other alloying elements. The designation “430” specifically designates the material as a ferritic stainless steel alloy.
The key elements and their content in 430 stainless steel include:
Chromium (Cr): Typically, the 430 stainless steel grade contains a significant chromium content, usually ranging between 12-18%. Chromium is a crucial element that endows the material with its corrosion-resistant properties. It forms a passive chromium oxide (Cr2O3) layer on the steel’s surface, acting as a protective barrier against corrosion.
Iron (Fe): Iron is the predominant element in 430 stainless steel, serving as the base metal. Its presence provides the structural integrity and mechanical properties of the material.
Other Elements: While chromium and iron are the primary constituents, 430 stainless steel may also contain small amounts of other alloying elements, such as nickel (Ni), manganese (Mn), and silicon (Si), among others, to fine-tune its material properties. The specific composition may vary based on the manufacturer and the desired characteristics of the final product.
As a supplier of 430 stainless steel bars, it’s important to emphasize that the “430” designation conveys important information about the material’s chemical composition, specifically its chromium content, which is responsible for its corrosion resistance. This knowledge is critical for both manufacturers and end-users to ensure the stainless steel is suitable for their intended applications, be it in automotive, kitchen appliances, construction, or various industrial settings.
The strength of a 430 stainless steel bar can be evaluated based on its mechanical properties, and it is essential to understand that the term “strength” can encompass various aspects, including tensile strength, yield strength, and hardness. To provide a comprehensive scientific perspective:
Tensile Strength: Tensile strength is a critical indicator of a material’s ability to withstand axial loads or stretching forces without permanent deformation. For 430 stainless steel bars, the tensile strength typically falls within the range of 450-600 megapascals (MPa). This level of tensile strength classifies it as a relatively strong material, suitable for various applications.
Yield Strength: The yield strength represents the point at which a material experiences plastic deformation under tensile stress. For 430 stainless steel bars, the minimum specified yield strength is typically equal to or greater than 205 MPa. This indicates the point at which the material will undergo permanent deformation when subjected to mechanical stress. Therefore, it is deemed strong in this aspect as well.
Hardness: Hardness is another measure of strength, indicating a material’s resistance to penetration or deformation. The hardness of 430 stainless steel bars, often measured using the Brinell scale, is typically less than or equal to 183 HB. This level of hardness suggests a degree of strength, which is essential for withstanding wear and abrasion in various applications.
It’s important to note that the strength of 430 stainless steel bars is influenced by various factors, including their chemical composition, heat treatment, and processing. As a supplier of 430 stainless steel bars, it’s crucial to provide products with consistent and well-defined mechanical properties to meet the specific needs of your customers.
Therefore, to address your query, 430 stainless steel bars exhibit notable strength in terms of tensile strength, yield strength, and hardness. Their strength, combined with other desirable properties, makes them a suitable choice for a wide range of applications in different industries.
Yes, 430 stainless steel bars are typically magnetic. This magnetic property is a result of their ferritic microstructure, which differs from non-magnetic austenitic stainless steel grades. The presence of iron as the primary constituent in 430 stainless steel contributes to its magnetic behavior.
The magnetic nature of 430 stainless steel bars can have implications for certain applications, especially those where magnetic properties are either advantageous or need to be considered:
Magnetic Applications: In some applications, having magnetic properties is a requirement. For example, 430 stainless steel bars are used in components for magnetic resonance imaging (MRI) machines and in electromagnets due to their magnetic characteristics.
Sorting and Separation: The magnetic nature of 430 stainless steel can be exploited in sorting and separation processes. It’s often used in magnetic separators to efficiently separate ferrous materials from non-ferrous materials.
Appliance Use: In the manufacturing of certain household appliances, the magnetic properties of 430 stainless steel are taken into account. For instance, in applications like refrigerator doors, the ability to attach magnetic elements such as magnets and magnetic clips can be a desirable feature.
Architectural Considerations: In architectural and design applications, where the appearance of exposed fasteners is not desired, the magnetic nature of 430 stainless steel can be advantageous for concealed fastening systems.
It’s important for a 430 stainless steel bar supplier to understand the magnetic properties of this material and how it can impact the selection and application of stainless steel in various industries and use cases.
Yes, 430 stainless steel bars can be welded, but there are specific precautions that should be taken during the welding process to ensure a successful and reliable weld. As a 430 stainless steel bar supplier, it’s essential to be aware of these considerations:
Preheating: Preheating the material to a temperature between 150-200°C before welding is advisable. This precaution helps to reduce the risk of cracking and enhances the weld’s integrity.
Filler Material: Selecting the appropriate filler material is crucial. Typically, a low carbon, ferritic stainless steel filler, such as AWS E430 is recommended for welding 430 stainless steel bars. This minimizes the potential for sensitization and cracking.
Welding Technique: Employing the correct welding technique is vital. Utilize techniques like TIG (Tungsten Inert Gas) or MIG (Metal Inert Gas) welding, which provide good control over the heat input.
Post-Weld Annealing: To alleviate any embrittlement in the weld metal and heat-affected zone, post-weld annealing is recommended. This involves heating the welded area to a temperature between 790-815°C, followed by a controlled cooling process.
Avoiding Overheating: Overheating, or prolonged exposure to high temperatures, should be avoided during welding. It can lead to sensitization, which reduces corrosion resistance and may result in cracking.
Cleanliness: Ensure that the welding area and the filler materials are free from contaminants, as impurities can affect the quality of the weld and lead to defects.
Proper Shielding: Maintain adequate shielding with an inert gas to prevent oxidation and ensure a clean, strong weld.
Qualified Welders: Utilize experienced and qualified welders who are familiar with the specific properties and requirements of welding 430 stainless steel.
Understanding these precautions and best practices is crucial for a 430 stainless steel bar supplier, as it ensures that customers receive the material with its integrity intact and that they are informed about the appropriate welding procedures and considerations for their applications.
Yes, there are limitations to the temperature range within which 430 stainless steel bars can be safely used, and it’s important for a 430 stainless steel bar supplier to convey this information to customers.
430 stainless steel has a notable susceptibility to heat sensitivity, particularly when exposed to extended periods of elevated temperatures. The critical temperature range that can impact the material’s properties is generally between 400°C and 600°C.
Within this temperature range, sensitization can occur. Sensitization is a phenomenon where chromium carbides (Cr23C6) precipitate along the grain boundaries of the steel. This precipitation depletes the steel of available chromium, which is essential for the formation and stability of the protective chromium oxide (Cr2O3) layer. As a result, the material becomes more susceptible to corrosion, and its mechanical properties may be compromised. Specifically, this can lead to a reduction in corrosion resistance, potentially resulting in localized corrosion and pitting.
Therefore, it’s essential to avoid prolonged exposure of 430 stainless steel bars to temperatures within the range of 400-600°C to ensure their optimal performance. Precautions such as proper material selection, insulation, or the use of alternative stainless steel grades with higher temperature resistance may be necessary for applications that involve exposure to temperatures within this critical range. Customers and end-users should be made aware of these limitations to ensure the safe and effective use of 430 stainless steel bars in their respective applications.
Comparing 430 stainless steel bars to 304 stainless steel bars is important for making informed material selection decisions. As a stainless steel bar supplier, understanding the distinctions between these two grades is crucial for assisting customers in choosing the most suitable material for their specific applications.
Chemical Composition:
- 430 Stainless Steel: 430 stainless steel is a ferritic stainless steel characterized by a higher chromium content (typically 12-18%) and lower nickel content. It also contains small amounts of other alloying elements.
- 304 Stainless Steel: 304 stainless steel is an austenitic stainless steel with a higher chromium content (typically 18-20%) and a significant nickel content (usually around 8-10.5%). It has lower carbon content compared to 430 stainless steel.
Corrosion Resistance:
- 430 Stainless Steel: While 430 stainless steel exhibits good general corrosion resistance, it is more susceptible to corrosion compared to 304 stainless steel, particularly in acidic and chloride-rich environments.
- 304 Stainless Steel: 304 stainless steel provides excellent corrosion resistance and is highly resistant to a wide range of corrosive substances, making it suitable for a broader spectrum of applications.
Magnetic Properties:
- 430 Stainless Steel: 430 stainless steel is generally magnetic due to its ferritic microstructure.
- 304 Stainless Steel: 304 stainless steel is typically non-magnetic or exhibits weak magnetic properties due to its austenitic microstructure.
Strength and Durability:
- 430 Stainless Steel: 430 stainless steel offers good strength and durability but may be more susceptible to sensitization and heat-induced embrittlement compared to 304 stainless steel.
- 304 Stainless Steel: 304 stainless steel provides high strength, durability, and excellent high-temperature performance. It is more robust against sensitization and embrittlement.
Applications:
- 430 Stainless Steel: 430 stainless steel is often chosen for applications where cost-effectiveness, moderate corrosion resistance, and magnetic properties are acceptable. Common applications include automotive trim, kitchen appliances, and architectural elements.
- 304 Stainless Steel: 304 stainless steel is preferred for applications demanding superior corrosion resistance, such as food processing equipment, chemical industry components, and medical devices.
In summary, 430 stainless steel bars are a cost-effective option with good corrosion resistance for less demanding environments and when magnetic properties are acceptable. On the other hand, 304 stainless steel bars are chosen for their superior corrosion resistance, non-magnetic properties, and broader range of applications, especially in industries where hygiene and durability are essential. Stainless steel bar suppliers should guide their customers in selecting the most suitable grade based on the specific needs of their projects.
Comparing 430 stainless steel bars to 316 stainless steel bars is vital for selecting the appropriate material for various applications. As a stainless steel bar supplier, understanding the differences between these two grades is essential for assisting customers in making well-informed decisions:
Chemical Composition:
- 430 Stainless Steel: 430 stainless steel is a ferritic stainless steel with a higher chromium content (typically 12-18%) and a lower nickel content. It contains small amounts of other alloying elements.
- 316 Stainless Steel: 316 stainless steel is an austenitic stainless steel with a higher chromium content (typically 16-18%) and a significant nickel content (usually around 10-14%). It also contains molybdenum, which enhances corrosion resistance.
Corrosion Resistance:
- 430 Stainless Steel: While 430 stainless steel offers good general corrosion resistance, it is more susceptible to corrosion compared to 316 stainless steel, especially in corrosive and chloride-rich environments.
- 316 Stainless Steel: 316 stainless steel is renowned for its superior corrosion resistance, making it an ideal choice for applications where exposure to saltwater, acids, and aggressive chemicals is prevalent.
Magnetic Properties:
- 430 Stainless Steel: 430 stainless steel is typically magnetic due to its ferritic microstructure.
- 316 Stainless Steel: 316 stainless steel is generally non-magnetic or exhibits weak magnetic properties due to its austenitic microstructure.
Strength and Durability:
- 430 Stainless Steel: 430 stainless steel provides good strength and durability, but it may be more susceptible to sensitization and heat-induced embrittlement.
- 316 Stainless Steel: 316 stainless steel offers high strength, exceptional durability, and superior high-temperature performance. It is more resistant to sensitization and embrittlement.
Applications:
- 430 Stainless Steel: 430 stainless steel is typically chosen for applications where cost-effectiveness, moderate corrosion resistance, and magnetic properties are acceptable. Common applications include automotive trim, kitchen appliances, and architectural elements.
- 316 Stainless Steel: 316 stainless steel is preferred for applications requiring the highest level of corrosion resistance, such as marine environments, pharmaceutical and chemical processing equipment, and medical devices.
In summary, 430 stainless steel bars are cost-effective with good corrosion resistance in less demanding environments and when magnetic properties are acceptable. In contrast, 316 stainless steel bars are the superior choice for applications demanding exceptional corrosion resistance, non-magnetic properties, and exposure to aggressive chemicals or marine conditions. Stainless steel bar suppliers should assist their customers in selecting the most appropriate grade based on the specific requirements and environmental conditions of their projects.
recent stainless steel bar products
Get In touch
Ready to Elevate Your Projects? Dive into our Stainless Steel Collection and Submit Your Specifications Today!
Phone/WhatsApp/WeChat:
+86 13052085117
Email: [email protected]
Address: RM557, NO.1388 Jiangyue Road, Shanghai China