How To Make Stainless Steel?
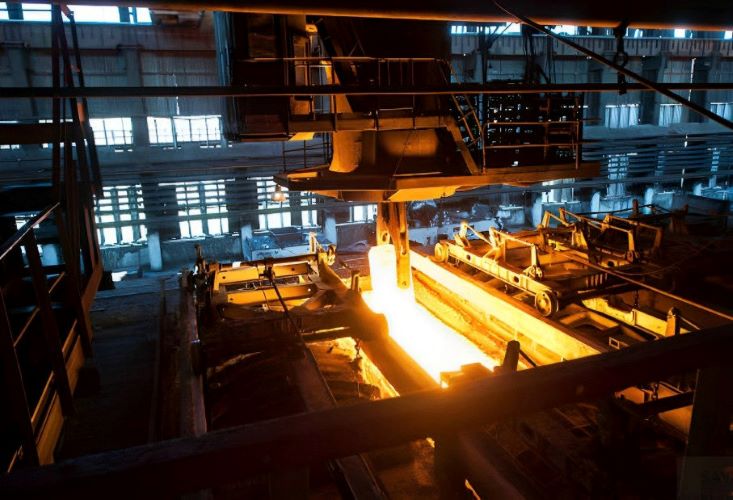
With the roar of heat in the blazing furnace fire, a powerful alloy is being formed. It is strong, durable and shines with a unique light. Are you curious as to how this amazing material is made? Making stainless steel is a true craft, requiring a mixture of elements and undergoing a precise machining process. There are many secrets and techniques hidden behind its creation, so let’s unravel this mystery and explore the amazing journey of making stainless steel.
How is stainless steel made?
Stainless steel, a remarkable alloy used extensively across various industries, is produced through a complex and precise process. It typically involves the following steps:
Melting and Refining: The primary materials – iron, chromium, nickel, and other alloying elements – are carefully weighed and blended in a furnace, creating the desired chemical composition. Additional alloy components are heated to high temperatures in electric arc or induction furnaces, resulting in a molten steel pool.
Continuous Casting: Once the molten stainless steel is prepared, it undergoes continuous casting to form semi-finished products like slabs or billets. In this process, the molten steel is poured into water-cooled molds to solidify and take shape, ensuring temperature uniformity, enhancing mechanical properties, and reducing segregation.
Hot Rolling: The next essential step is hot rolling, where the semi-finished products are heated and gradually reduced in thickness by passing through rolling mills. This process subjects stainless steel to high pressures and temperatures.
Annealing: Following hot rolling, the stainless steel undergoes annealing, a heat treatment process that relieves internal stresses and restores ductility and corrosion resistance.
Cold Rolling: For specific applications requiring a thinner gauge, stainless steel is cold-rolled. This process improves surface finish, enhances mechanical properties, and achieves precise dimensions.
Finishing and Coating: Stainless steel is given its final surface finish, which may include processes like pickling, passivation, and coating to enhance corrosion resistance and appearance.
These meticulously controlled steps in stainless steel production guarantee the material’s outstanding properties, such as corrosion resistance, strength, and versatility across a wide array of applications.
how to make stainless steel?
Melting and Refining
In the production of stainless steel, the process of melting and refining is a crucial step that lays the foundation for the material’s exceptional properties. This stage begins with the precise measurement and blending of primary materials. These primary materials include iron, chromium, nickel, and other alloying elements, each carefully weighed to achieve the desired chemical composition.
The heart of this process takes place in electric arc or induction furnaces. These furnaces are designed to handle extreme temperatures, reaching levels high enough to melt the selected materials, which typically have high melting points. By using an electric arc or electromagnetic induction, these furnaces efficiently transform the solid raw materials into a superheated, molten state.
The alloying process is where stainless steel’s unique characteristics come to life. Additional elements like manganese, silicon, and carbon can be introduced to achieve specific alloy recipes. Chromium and nickel play pivotal roles in enhancing corrosion resistance and providing stainless steel’s distinctive shine. The precise control over these alloying elements is a testament to the craftsmanship of stainless steel manufacturers.
Once the alloy is homogenized, it forms a pool of molten steel with the desired chemical composition, setting the stage for the subsequent steps in the stainless steel manufacturing process. This meticulously controlled melting and alloying phase ensures the resulting stainless steel is not only durable but also possesses excellent corrosion resistance for which it is renowned.
Role of chemical elements
Chromium
- is the basic element that constitutes stainless steel
Chromium is the most basic element that determines the corrosion resistance of stainless steel. In the oxidizing medium, chromium can make the surface of the steel quickly form a layer of actual corrosion medium can not pass through and do not dissolve the chromium-rich oxide film, the oxide film is very dense, and the metal basic combination is very solid, protecting the steel from further oxidation of external media leaching; chromium can also effectively improve the electrode potential of steel.
Nickel
-alone can not make stainless steel
The effect of nickel on the corrosion resistance of stainless steel, only when it is combined with chromium can be fully displayed. Because low carbon nickel steel to obtain pure austenite organization, nickel content needs to reach 24%; to make the steel in some media corrosion resistance significantly changed, nickel content needs to be more than 27%. Therefore, nickel can not make stainless steel alone.
manganese and nitrogen
- can replace nickel in chromium-nickel stainless steel
Manganese and nitrogen in stainless steel have a role similar to that of nickel. The role of manganese in stabilizing austenite is one-half of nickel, while the role of nitrogen is much larger than nickel, about 40 times as much as nickel. Thus, manganese and nitrogen can obtain a single austenite organization instead of nickel. But the addition of manganese will make the low chromium stainless steel corrosion resistance reduced. At the same time, high manganese austenitic steel is not easy to process. Therefore, stainless steel does not use manganese alone, only partly instead of nickel.
Molybdenum and copper
- can improve corrosion resistance of some stainless steels
Molybdenum and copper can improve the corrosion resistance of stainless steel to, acetic acid and other corrosive media. Molybdenum can also significantly improve the corrosion resistance to media containing chloride ions (for example) as well as in organic acids. However, molybdenum-containing stainless steel should not be used in nitric acid, molybdenum-containing stainless steel in boiling 65% nitric acid corrosion rate than the non-molybdenum doubled; copper added to chromium manganese nitrogen stainless steel, will accelerate the stainless steel intergranular corrosion.
Boron
- can replace nickel in chromium-nickel stainless steel
High chromium ferritic stainless steel (Cr17MO2Ti) with 0.005% boron, can make the steel in the boiling 65% acetic acid corrosion resistance; austenitic stainless steel with trace amounts (0.0006 ~ 0.0007%) of boron, can make the steel thermal plasticity improvement; boron to improve the thermal strength of steel has a good effect, can make the stainless steel thermal strength significantly improved; boron-containing chromium-nickel Austenitic stainless steel has a special use in the atomic energy industry.
However, the boron content in stainless steel will make the steel plasticity and impact toughness is reduced.
Silicon and aluminum
- can improve the oxidation resistance of stainless steel
The role of silicon in improving the oxidation resistance of chromium steel is very significant, containing 5% chromium and 1% silicon steel, the ability to resist oxidation can be equal to 12% chromium steel.
The purpose of adding silicon and aluminum to high-chromium steel: one is to further improve the antioxidant properties of steel, and the second is to save chromium. Although the role of silicon and aluminum to improve the oxidation resistance of chromium steel is great, but also has many disadvantages. The most important is that it makes the steel grain coarsening and brittle tendency to increase.
Tungsten and vanadium
- can improve the thermal strength of the steel
Tungsten is a high melting point metal that is added to steel to improve its heat and wear resistance. Tungsten increases the lattice stability of steel and improves its resistance to deformation and high temperature strength. Vanadium is a strengthening element that can be added to steel to improve its hardness, strength and wear resistance. The addition of vanadium improves the lattice structure of the steel, increasing the strength and stability of the grain boundaries, thereby increasing the strength and hardness of the steel. In addition, vanadium is able to form carbides with carbon, further increasing the hardness and wear resistance of the steel.
how to make stainless steel?
Continuous Casting
Continuous casting is a pivotal step in the stainless steel manufacturing process that transforms the molten alloy into semi-finished products such as slabs or billets. The process begins with the precisely controlled molten steel produced during the melting and refining phase.
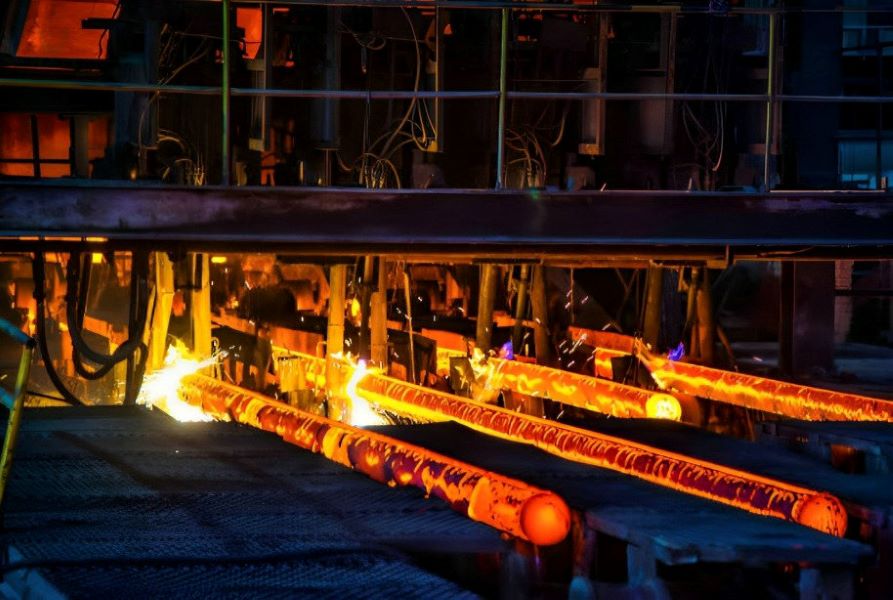
In continuous casting, maintaining temperature uniformity is of utmost importance. The molten stainless steel retains its extreme heat throughout this step, ensuring that it remains in a liquid state. As the steel flows from the furnace into a water-cooled mold, it gradually solidifies.
By carefully managing the cooling rate, the thickness of the cast material, and the movement of the mold, stainless steel manufacturers create semi-finished products with consistent dimensions and a uniform microstructure. Temperature control prevents the development of unwanted segregations, which can compromise the quality of the final stainless steel.
Stainless steel manufacturers play a crucial role in ensuring that this phase results in semi-finished products with the required characteristics, setting the stage for further processing and the eventual production of a wide range of stainless steel products.
how to make stainless steel?
hot rolled
The hot rolled process is a critical step in shaping stainless steel into its final form. It involves heating the semi-finished products, such as slabs or billets, and reducing their thickness through the use of rolling mills.
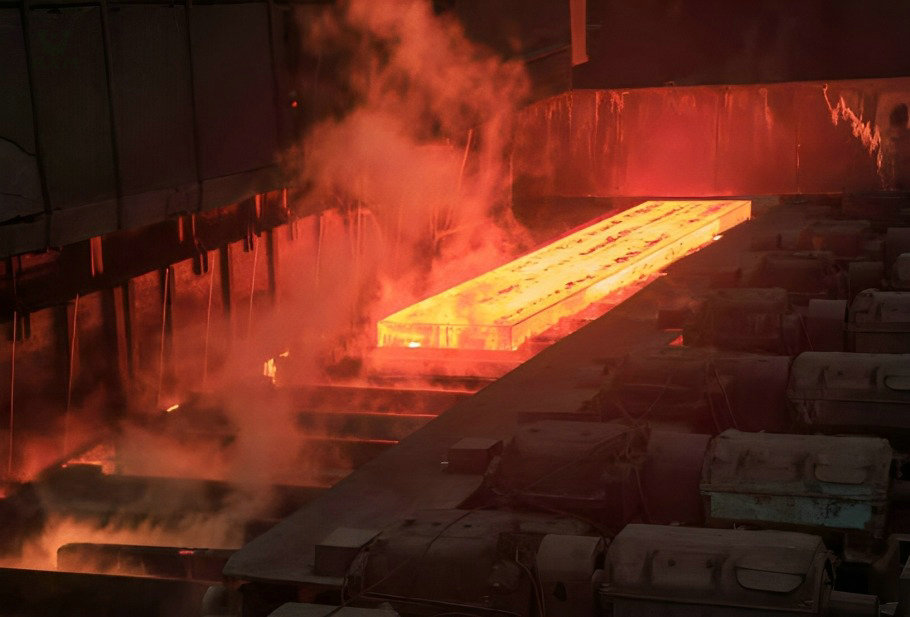
Heating is a crucial part of this process. The semi-finished products need to be at a high temperature, typically over 1,000°C, to become malleable enough for rolling. Once the stainless steel reaches the desired temperature, it passes through a series of rolling mills. These mills apply substantial pressure to the material while simultaneously reducing its thickness.
The combination of high pressure and temperature leads to plastic deformation of the stainless steel. As a result, the material becomes more workable and can be further processed into various shapes, including sheets, plates, and coils. This process’s precise control is essential for achieving the desired thickness, mechanical properties, and surface finish of the stainless steel products. Stainless steel manufacturers play a critical role in managing these parameters to ensure the final product meets the required specifications.
how to make stainless steel?
Annealing
Annealing is a crucial heat treatment process in the production of stainless steel. It serves multiple purposes:
Heat treatment to relieve internal stresses
Heat treatment to relieve internal stresses is a critical step in the production of stainless steel. During previous manufacturing processes like hot rolling or forging, stainless steel can accumulate internal stresses due to temperature fluctuations and mechanical deformation. The goal of this heat treatment is to eliminate these stresses and ensure the steel’s structural integrity and performance.
The process begins by heating the stainless steel to a specific temperature, which varies depending on the type of stainless steel being produced. For austenitic stainless steels like 304, this temperature is often around 1,050°C. Once the steel reaches this temperature, it is held there for a specified period to allow for uniform heating throughout the material.
Maintaining the right temperature for the correct amount of time is crucial because it enables the stresses to redistribute and even out within the steel’s microstructure. This reduces the risk of cracks, warping, or other defects that can occur if the stresses remain unaddressed.
Stainless steel manufacturers carefully control the annealing process to ensure that the internal stresses are effectively relieved. They must also manage the cooling phase following annealing, as the rate of cooling can further impact the material’s properties. The ultimate goal is to produce stainless steel that is not only structurally sound but also exhibits enhanced ductility and corrosion resistance, crucial for its various applications. Proper heat treatment, as overseen by stainless steel manufacturers, is fundamental to meeting these requirements.
Restoration of ductility and corrosion resistance
The restoration of ductility and corrosion resistance is a critical outcome of the annealing process in stainless steel manufacturing, overseen by stainless steel manufacturers. This heat treatment plays a vital role in enhancing the material’s properties.
- Ductility Restoration: Annealing allows for the restoration of ductility in stainless steel. Ductility is the ability of a material to deform plastically under tensile stress without breaking. During prior manufacturing processes like hot rolling or forging, the stainless steel may have lost some of its ductility due to the accumulation of internal stresses. Annealing at specific temperatures allows the material's crystalline structure to regain flexibility and reduce brittleness, making it more workable and formable.
- Corrosion Resistance: Annealing also contributes to the improvement of stainless steel's corrosion resistance. The formation of a protective oxide layer on the surface of stainless steel is a key factor in its resistance to corrosion. Annealing helps in the removal of impurities and inclusions that might have formed during earlier manufacturing stages. Additionally, it allows for the reformation of a consistent, corrosion-resistant oxide layer, providing long-term protection against rust, oxidation, and other forms of corrosion.
Stainless steel manufacturers carefully control the annealing process to achieve the right balance of ductility and corrosion resistance specific to the intended applications of stainless steel. By restoring these properties, annealing ensures that the stainless steel meets the high standards required for a wide range of industries, from construction to medical equipment and more.
how to make stainless steel?
cold rolled
Cold rolled is a crucial step in the manufacturing of stainless steel, carefully managed by stainless steel manufacturers. This process significantly influences the material’s thickness, surface finish, and mechanical properties.
- Thinning Stainless Steel Gauge: Cold rolling aims to reduce the thickness of stainless steel, ensuring that it meets the precise thickness requirements for various applications. In this process, the stainless steel strip, coil, or sheet passes through a series of rollers, each exerting increasing pressure. The material gradually thins to the desired gauge while maintaining its structural integrity.
- Enhancement of Surface Finish: The cold rolling process contributes to an improved surface finish in stainless steel. As the material passes through the rollers, any imperfections or irregularities on the surface are smoothed out, resulting in a clean, smooth, and often shiny appearance. The finish can range from a matte or brushed surface to a highly polished one, depending on the specific requirements of the end product.
- Mechanical Properties: Cold rolling also enhances the mechanical properties of stainless steel. It increases the material's tensile strength, making it stronger and more resistant to deformation under load. Additionally, it can improve hardness and overall durability while maintaining the desirable properties of ductility and corrosion resistance.
Stainless steel manufacturers pay meticulous attention to the cold rolling process, ensuring that the final product meets the precise thickness and surface finish requirements necessary for its intended use. This process plays a critical role in producing stainless steel products that meet the high standards demanded by a variety of industries, including construction, automotive, and manufacturing.
how to make stainless steel?
Finishing and Coating
The final steps in stainless steel manufacturing focus on finishing and coating, which are critical for enhancing material properties and corrosion resistance. Stainless steel manufacturers carefully manage these processes to meet the specific needs of various applications.
Final Surface Finish for Improved Properties
The final surface finish of stainless steel significantly influences its properties. This finish can range from a matte or brushed texture to a highly polished, mirror-like appearance, depending on the intended use. A smoother finish often leads to improved corrosion resistance, easier cleaning, and an aesthetically pleasing appearance. For specific applications, such as medical instruments or food processing equipment, a highly polished surface may be required to minimize the risk of bacterial growth and facilitate maintenance.
Processes like Pickling, Passivation, and Coating for Corrosion Resistance
- Pickling: This process involves immersing stainless steel in an acid solution to remove any surface scale, oxide, or other contaminants that may have formed during manufacturing. Pickling is essential for maintaining the material's corrosion resistance and ensuring a clean, unblemished surface.
- Passivation: After pickling, stainless steel is often passivated to encourage the formation of a passive oxide layer on the surface. This oxide layer enhances corrosion resistance by providing a protective barrier against environmental factors, such as moisture and chemicals. Passivation can be achieved through various methods, such as nitric acid passivation or citric acid passivation, depending on the grade of stainless steel and specific requirements.
- Coating: In some applications where exceptional corrosion resistance is required, stainless steel may receive additional coatings or plating. These coatings can include electroplating with metals like zinc or nickel, or applying specialized polymer coatings. These coatings enhance the material's resistance to specific corrosive agents or extreme environmental conditions.
Overall, the finishing and coating processes are crucial for ensuring that stainless steel products meet the highest standards of corrosion resistance, durability, and appearance, making them suitable for a wide range of industries, from construction to healthcare. Stainless steel manufacturers carefully select the most appropriate finishing techniques to meet the specific needs of diverse applications.
Quality control and inspection
To ensure that stainless steel products meet international standards, quality control measures go beyond in-process monitoring during manufacturing. Each batch must undergo both chemical and mechanical evaluations to guarantee it meets the necessary specifications.
Mechanical Testing
Mechanical testing evaluates the material’s ability to withstand physical stress, such as pressure, impacts, and weight. It involves tensile, Brinell, and other toughness tests to confirm the strength and durability of the stainless steel.
Chemical Testing
Chemical analysis is performed to determine the precise composition of the steel. Non-destructive methods such as spectrochemical analysis are typically used. Corrosion resistance is a crucial factor in stainless steel, and salt spray tests help gauge its performance over time in harsh conditions. The longer the material resists corrosion in these tests, the more reliable it is.
how to make stainless steel?
Conclusion
In summary, make stainless steel is a complex and delicate process that involves several key steps and technologies. From raw material selection to smelting, casting, rolling, and processing, each stage requires precise control and rigorous operations. Through these steps, we are able to create stainless steel materials with superior performance and a wide range of applications.
In the manufacture of stainless steel, fine craftsmanship, and strict quality control are key to ensuring the final product. By carefully selecting raw materials, controlling alloy ratios, and optimizing processing, stainless steel suppliers ensure that all properties of stainless steel are superior and meet expected standards. Stainless steel suppliers play a vital role in the process of making stainless steel. They provide high quality raw materials and professional technical support to ensure that the stainless steel produced meets the strict standards and requirements. Their expertise and experience are indispensable in providing manufacturers and users with reliable stainless steel solutions.
In short, making stainless steel requires a combination of material composition, process flow and partner selection. Through rational design and a quality supply chain, we are able to obtain high-quality stainless steel that meets the needs of various industries and contributes to the development of society. Whether in construction, automotive, energy, medical or other fields, stainless steel will continue to play an important role and bring more innovation and convenience to our lives.