Is Stainless Steel Non-Ferrous?
Have you ever wondered about the composition of stainless steel and whether it falls into the category of non-ferrous materials? It's a question that often arises when discussing metals and their properties, and the answer might not be as straightforward as you think. Stainless steel is a remarkable alloy known for its corrosion resistance, making it a popular choice for various applications, from kitchen utensils to architectural structures. However, the question of whether stainless steel can be classified as non-ferrous or if it has some connection to ferrous materials like iron and steel remains a topic of debate among metallurgy enthusiasts and engineers. To unravel this intriguing conundrum, let's delve into the characteristics of stainless steel, its composition, and its position within the realm of metallurgy.
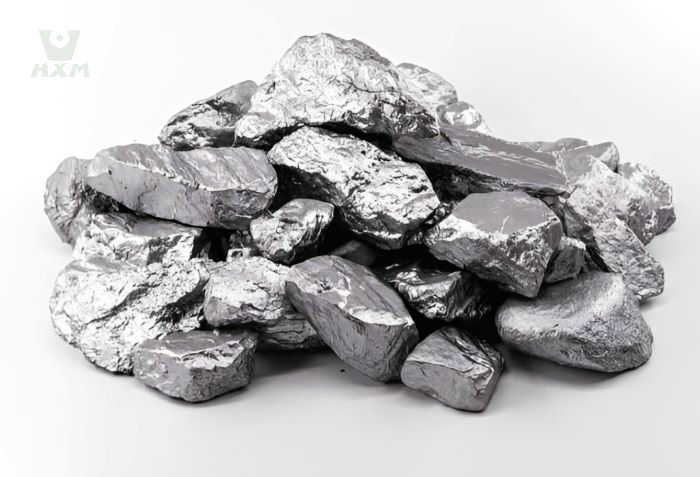
-Huaxiao Stainless Steel Manufactures
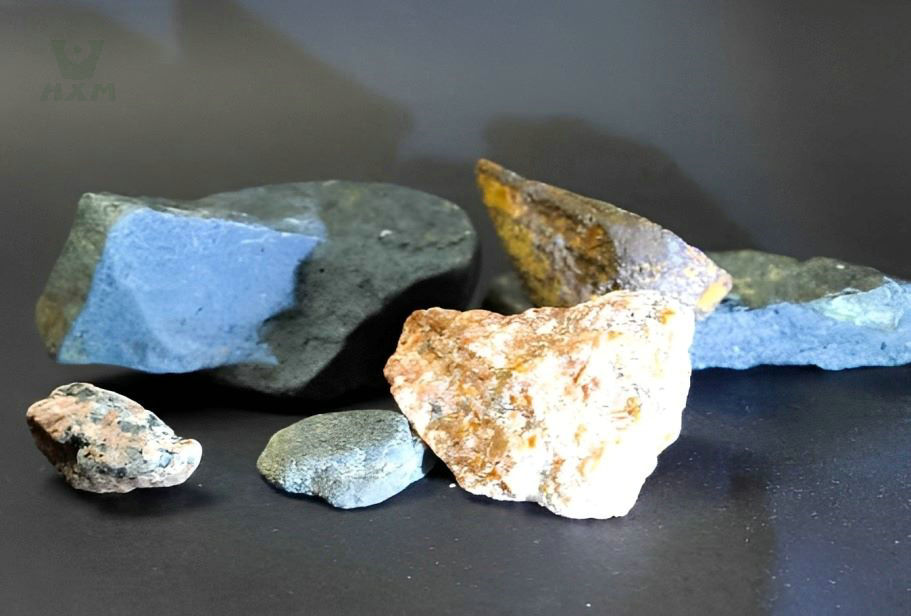
is stainless steel non ferrous?
Stainless steel is not non-ferrous; it is, in fact, a ferrous alloy. To understand this categorization, we need to delve into the fundamental definitions and properties of ferrous and non-ferrous materials.
Ferrous materials contain iron (Fe) as a principal component, and stainless steel is no exception. Although stainless steel is celebrated for its corrosion resistance and distinct properties, it is primarily composed of iron, with the addition of at least 10.5% chromium (Cr) by mass. This chromium content contributes to its anti-corrosive nature and distinguishes it from plain carbon steel. Other elements, such as nickel, molybdenum, and manganese, can also be present in various grades of stainless steel.
Non-ferrous materials, on the other hand, do not contain iron as a principal component. Common non-ferrous metals include aluminum, copper, and titanium, which lack the significant iron content seen in stainless steel.
Ferrous and Non-Ferrous Materials
Ferrous materials are those that primarily consist of iron (Fe) as a major component. Iron is the base metal in ferrous materials, and it typically makes up a significant proportion of the material’s composition, often more than 50%. Ferrous materials are known for their magnetic properties and include various types of iron-based alloys. The most common ferrous materials are plain carbon steel, alloy steel, and cast iron. These materials exhibit properties such as high strength, good thermal conductivity, and the ability to be magnetized.
Non-ferrous materials, in contrast, do not contain iron as their principal component. Instead, they are primarily composed of metals and alloys that do not have iron as the main element. Common non-ferrous metals include aluminum (Al), copper (Cu), brass (a copper-zinc alloy), bronze (a copper-tin alloy), and various types of alloys like titanium (Ti), nickel (Ni), and lead (Pb). Non-ferrous materials often exhibit properties such as corrosion resistance, high electrical conductivity, and lightweight characteristics. They are typically not magnetic, or their magnetic properties are very weak.
Characteristics of ferrous materials
Ferrous materials, characterized by their iron-rich composition, exhibit a set of distinctive characteristics with particular relevance to industrial applications. These characteristics play a significant role in the choices made by manufacturers, including stainless steel manufacturers, for specific applications. Below, we will delve into the defining features of ferrous materials:
- Magnetic Properties: Ferrous materials are inherently magnetic. This magnetic property is a result of the alignment of atomic dipoles within the iron structure. This characteristic is crucial in various applications, such as in the production of electric motors and transformers, where magnetic materials are essential.
- Strength and Durability: Ferrous materials, especially steel alloys, are known for their exceptional strength and durability. They can withstand heavy loads and exhibit high tensile strength, making them valuable in construction, automotive, and manufacturing industries.
- High Melting Points: Ferrous materials typically have high melting points, which is advantageous in applications where materials need to withstand high temperatures. This characteristic makes them suitable for use in high-temperature environments, like in the aerospace and automotive sectors.
- Conductivity: Ferrous materials, though not as conductive as non-ferrous metals like copper, still exhibit reasonable electrical and thermal conductivity. This property is utilized in applications where a balance between strength and conductivity is required, such as in electrical power transmission.
- Corrosion Susceptibility: A significant drawback of ferrous materials, particularly plain carbon steel, is their susceptibility to corrosion when exposed to moisture and oxygen. This limitation has led to the development of stainless steel, a specific ferrous alloy with enhanced corrosion resistance, often used by stainless steel manufacturers for various applications.
- Machinability: Ferrous materials can be readily machined, which makes them attractive for manufacturing processes. They are often used in the production of intricate components and structures.
- Recyclability: Ferrous materials, including steel, are highly recyclable, contributing to sustainability and reduced environmental impact.
In summary, ferrous materials possess magnetic properties, exceptional strength and durability, high melting points, reasonable conductivity, and good machinability. However, they can be prone to corrosion, a limitation that led to the development of corrosion-resistant ferrous alloys like stainless steel. Stainless steel manufacturers, in particular, leverage the unique properties of stainless steel to provide materials with superior corrosion resistance for various applications.
Characteristics of non-ferrous materials
Non-ferrous materials, distinct from ferrous materials due to their lack of significant iron content, exhibit a range of characteristics that are particularly advantageous in various applications. Stainless steel manufacturers, in particular, often employ non-ferrous materials to complement or replace ferrous ones. Let’s delve into the defining characteristics of non-ferrous materials:
- Corrosion Resistance: Non-ferrous materials, such as aluminum, copper, and their alloys, are renowned for their exceptional resistance to corrosion. They develop protective oxide layers when exposed to the environment, which shields them from deterioration. This property is especially valuable in applications where exposure to moisture and aggressive chemicals is a concern, such as in aerospace and marine industries.
- Lightweight: Non-ferrous metals are generally lighter than ferrous ones, making them ideal for applications where weight reduction is critical. For instance, aluminum's low density is a key reason for its use in the aerospace industry, where reducing the weight of aircraft is paramount.
- High Electrical Conductivity: Copper, in particular, is renowned for its excellent electrical conductivity. This property makes it the material of choice for electrical wiring and components, allowing efficient transmission of electricity with minimal loss.
- Thermal Conductivity: Non-ferrous materials often exhibit good thermal conductivity, making them suitable for applications where heat transfer is essential. Copper, for example, is widely used in heat exchangers and HVAC systems.
- Non-Magnetic: Unlike ferrous materials, non-ferrous materials are typically non-magnetic. This property is advantageous in applications where magnetism can interfere with electronic devices, such as in MRI machines and certain industrial sensors.
- Malleability and Ductility: Many non-ferrous metals, like copper and aluminum, are highly malleable and ductile. This allows for intricate shaping and forming, making them valuable in the production of various components and structures.
- Recyclability: Non-ferrous materials are highly recyclable, which aligns with sustainability goals and reduces the environmental footprint.
- Aesthetic Appeal: Non-ferrous materials are often chosen for their aesthetic qualities. For example, the luster of copper and its alloys makes them a popular choice in decorative applications.
In summary, non-ferrous materials exhibit excellent corrosion resistance, lightweight properties, high electrical and thermal conductivity, non-magnetic behavior, malleability, ductility, and recyclability, and often have aesthetic appeal. These characteristics make them valuable in a wide range of applications, including those where stainless steel manufacturers opt for non-ferrous materials to capitalize on their unique properties, especially their corrosion resistance.
ferrous vs non-ferrous metals, what's the differences?
1. Iron Content:
- Ferrous Metals: Contain iron. Examples include steel, cast iron, and wrought iron.
- Non-Ferrous Metals: Do not contain iron. Examples include aluminum, copper, lead, zinc, and precious metals like gold and silver.
2. Magnetism:
- Ferrous Metals: Generally magnetic due to the iron content. This property makes them useful in applications requiring magnetic properties, like motors and transformers.
- Non-Ferrous Metals: Usually non-magnetic, making them suitable for electronic applications where magnetism could be problematic.
3. Corrosion Resistance:
- Ferrous Metals: More prone to rust and corrosion because of their iron content, especially when exposed to moisture. Exceptions include stainless steel, which is alloyed with chromium for corrosion resistance.
- Non-Ferrous Metals: Typically more resistant to corrosion. This makes them ideal for applications involving exposure to water, moisture, and harsh environments (e.g., marine applications).
4. Weight:
- Ferrous Metals: Tend to be heavier due to the iron content.
- Non-Ferrous Metals: Lighter, which is why they are commonly used in applications where weight is a concern, such as in aerospace and automotive industries.
5. Strength:
- Ferrous Metals: Generally stronger and harder, making them suitable for construction, infrastructure, and heavy industrial applications.
- Non-Ferrous Metals: Though lighter, some can still offer high strength. For example, titanium is both light and strong.
6. Recyclability:
- Ferrous Metals: Highly recyclable, especially steel, which can be recycled many times without losing its properties.
- Non-Ferrous Metals: Also recyclable and often retain high value when recycled, such as copper and aluminum.
Summary Table:
Property | Ferrous Metals | Non-Ferrous Metals |
---|---|---|
Iron Content | Contains iron | Does not contain iron |
Magnetism | Typically magnetic | Non-magnetic |
Corrosion | Prone to corrosion | Corrosion-resistant |
Weight | Heavier | Lighter |
Strength | High strength | Strength varies but can be high |
Common Examples | Steel, cast iron | Aluminum, copper, zinc |
Common Applications:
- Ferrous Metals: Used in construction (rebar, beams), automotive (car bodies, engines), and manufacturing tools.
- Non-Ferrous Metals: Found in wiring (copper), aircraft (aluminum), and decorative items (silver, gold).
Distinguish between stainless steel and ferrous metals
Characteristic | Stainless Steel | Ferrous Metals (e.g., Carbon Steel) |
---|---|---|
Principal Component | Iron (Fe) with a significant chromium (Cr) content | Iron (Fe) |
Corrosion Resistance | Excellent resistance to corrosion, due to the formation of a protective chromium oxide layer on the surface. Suitable for harsh environments. | Prone to corrosion, requiring protective coatings or surface treatments to prevent rusting. |
Magnetic Properties | Austenitic stainless steel is non-magnetic. Other stainless steel types may have varying levels of magnetism. | Typically magnetic, especially plain carbon steel. |
Strength and Durability | High strength and durability, suitable for various applications. | High strength, but may require additional corrosion protection. |
Weight | Stainless steel is relatively heavy. | Ferrous metals are relatively heavy. |
Thermal Conductivity | Varies depending on the stainless steel type but is generally lower than ferrous metals. | Typically has higher thermal conductivity. |
Electrical Conductivity | Varies depending on the stainless steel type, but it is generally lower than ferrous metals. | Typically has higher electrical conductivity. |
Resistance to Staining | Stainless steel resists staining and is easy to clean. | Ferrous metals may stain or rust, requiring maintenance. |
Recyclability | Stainless steel is highly recyclable. | Ferrous metals, including steel, are also highly recyclable. |
Common Applications | Used in a wide range of applications, including kitchen appliances, architectural structures, medical instruments, and more. | Used in construction, automotive, machinery, and industrial equipment. |
Stainless Steel Manufacturers | Specialized manufacturers produce various grades of stainless steel tailored to specific applications. | Numerous manufacturers produce a wide range of ferrous metal products. |
This table summarizes the key differences between stainless steel and ferrous metals, highlighting the specific characteristics and applications of each. Stainless steel’s superior corrosion resistance and other unique properties make it a valuable choice in various industries, and stainless steel manufacturers produce a range of specialized alloys to meet specific needs. Ferrous metals, on the other hand, are widely used but require additional protection against corrosion in many applications.
Composition of Stainless Steel
Stainless steel, a renowned alloy, consists primarily of iron (Fe), which forms the foundational matrix. Its corrosion resistance is mainly attributed to the inclusion of chromium (Cr), with a minimum content of 10.5%, enabling the formation of a protective oxide layer. Nickel (Ni) is often a significant addition, enhancing corrosion resistance and mechanical properties. While carbon (C) content is relatively low compared to plain carbon steel, it influences strength and hardness. Stainless steel manufacturers meticulously control these major components and often incorporate other alloying elements to tailor the material for specific applications, ensuring a balance of strength, durability, and corrosion resistance.
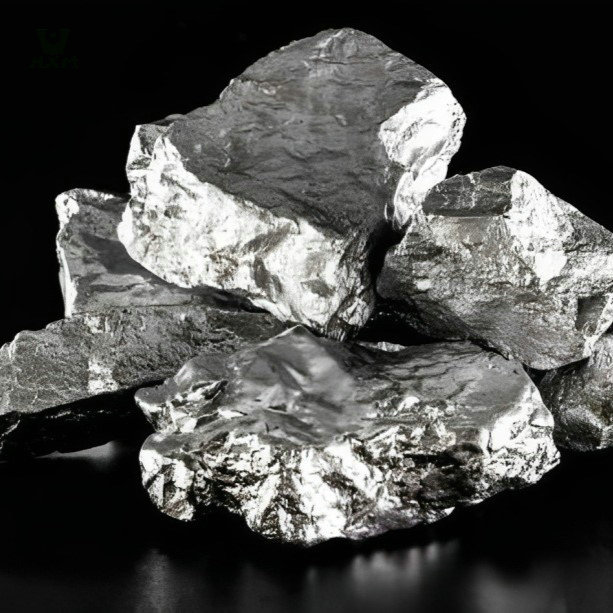
Iron (Fe)
Iron is the primary component of stainless steel. It forms the structural matrix of the alloy and provides its basic mechanical properties. The iron content in stainless steel serves as the foundation upon which other elements are added to create specific grades and types.
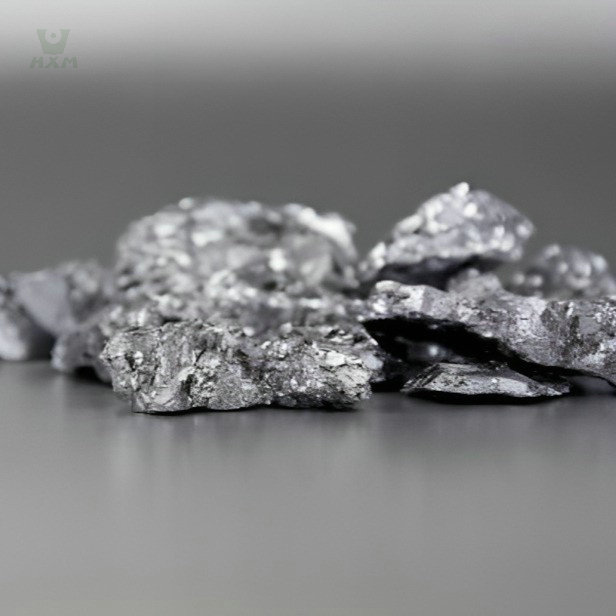
Chromium (Cr)
Chromium is one of the defining elements of stainless steel. It typically makes up at least 10.5% of the alloy by mass. When exposed to oxygen, it forms a thin, self-repairing oxide layer on the surface of the steel, known as the passive layer. This layer acts as a barrier, preventing further oxidation and corrosion, even in aggressive environments.
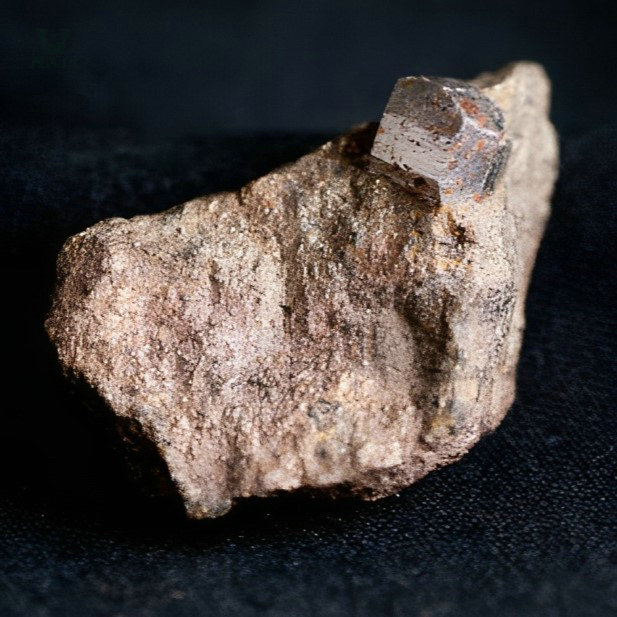
Nickel (Ni)
Nickel is often a significant component of stainless steel, and it contributes to the alloy's resistance to corrosion, especially in harsh or acidic conditions. Nickel also enhances the material's mechanical properties, such as strength, ductility, and toughness. It can also help stabilize the austenitic structure of stainless steel.
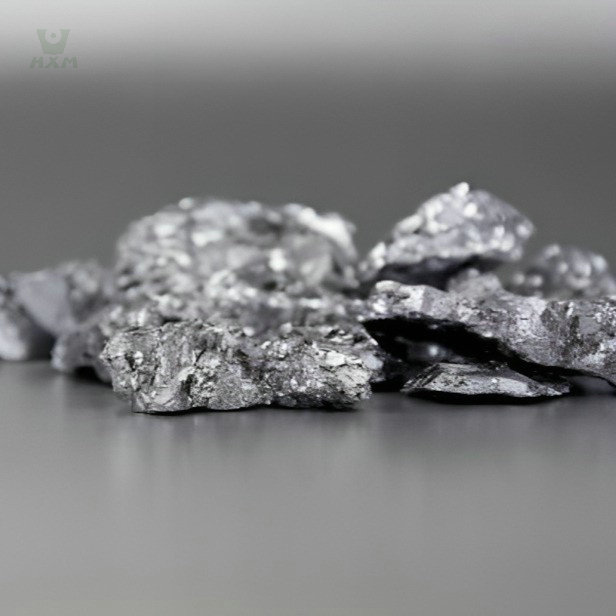
Carbon (C)
Carbon is another essential element in stainless steel, although its content is relatively low compared to plain carbon steel. Carbon influences the alloy's strength and hardness. Too much carbon can reduce corrosion resistance, while too little can impact hardness and machinability. Controlling the carbon content is a critical aspect of stainless steel manufacturing.
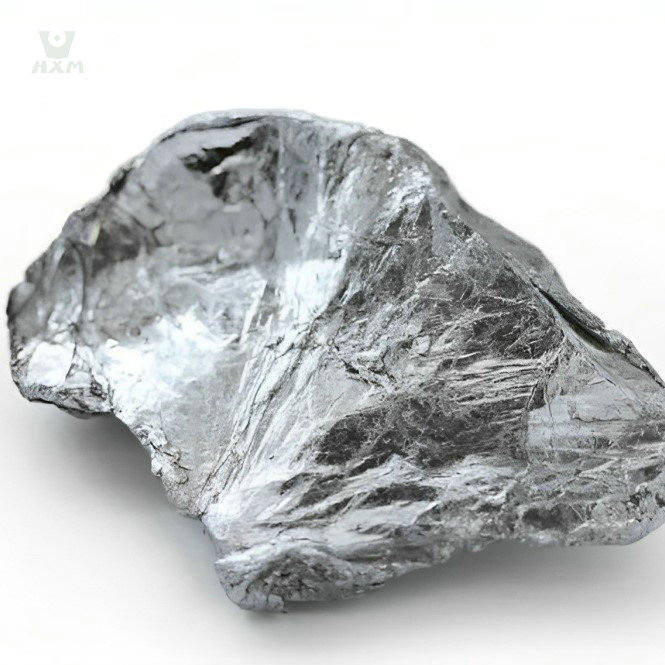
Molybdenum (Mo)
Molybdenum is an alloying element often added to certain stainless steel grades, particularly those intended for use in aggressive environments, such as marine applications or chemical processing. Molybdenum enhances the alloy's resistance to pitting and crevice corrosion.
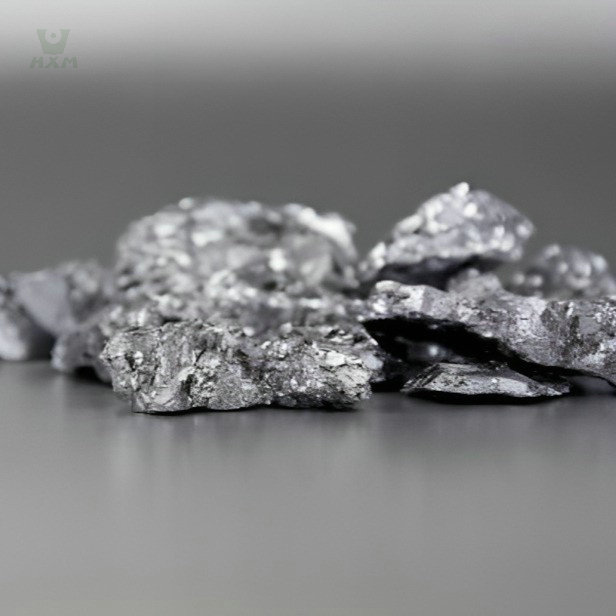
Manganese (Mn)
Manganese is added to stainless steel to improve ductility, formability, and weldability. It also aids in deoxidizing the steel during the manufacturing process.
Other Alloying Elements: Depending on the specific grade and intended application of stainless steel, various other alloying elements can be included. These can include elements such as titanium (Ti), niobium (Nb), and nitrogen (N), among others. These additional elements are used to fine-tune the material’s properties to meet specific requirements.
Stainless steel manufacturers carefully control the composition of these major components to produce stainless steel alloys with desired properties, ensuring the alloy is well-suited to a wide range of applications while maintaining its core characteristic of corrosion resistance.
Corrosion Resistance of Stainless Steel
Mechanisms of corrosion in stainless steel
- General Corrosion: Stainless steel is generally resistant to corrosion due to the presence of chromium, which forms a passive oxide layer on the surface. However, in certain aggressive environments or due to extreme conditions, this protective layer may break down. This can lead to the gradual and uniform dissolution of the metal, a process known as general corrosion.
- Pitting Corrosion: Pitting corrosion is a localized form of corrosion that can occur in stainless steel. It results from the formation of small pits or craters on the material's surface. Pitting is often caused by the presence of chloride ions in the environment, such as in marine or industrial settings. High-chromium stainless steel alloys are particularly resistant to pitting corrosion due to their robust passive layer.
- Crevice Corrosion: Crevice corrosion occurs in confined spaces or crevices on the surface of stainless steel. These areas can trap corrosive agents, leading to accelerated corrosion. High-chromium stainless steel alloys are better equipped to withstand crevice corrosion, thanks to their superior resistance to chemical attack.
High Chromium Alloys and Corrosion Resistance
High-chromium stainless steel alloys, which often contain more than 20% chromium, are especially renowned for their exceptional corrosion resistance. This enhanced resistance can be attributed to several factors:
- Formation of a Stable Passive Layer: The high chromium content in these alloys results in the formation of a stable and self-repairing passive oxide layer on the material's surface. This layer acts as a barrier, preventing further oxidation and corrosion. The more substantial the chromium content, the more robust and effective this passive layer becomes.
- Reduced Susceptibility to Pitting: High-chromium alloys have a decreased susceptibility to pitting corrosion. The elevated chromium content improves the material's resistance to chloride-induced pitting, making it suitable for use in marine environments and chemical processing.
- Enhanced Resistance to Crevice Corrosion: These alloys are also better equipped to withstand crevice corrosion, as the stable passive layer and high chromium content minimize the corrosive effects of trapped electrolytes within crevices and joints.
In conclusion, stainless steel’s resistance to corrosion is due to the formation of a protective oxide layer, with high-chromium alloys exhibiting superior corrosion resistance. Stainless steel manufacturers often utilize these high-chromium alloys in applications where extreme corrosion resistance is required, such as in the chemical, pharmaceutical, and food processing industries.
Comparison of stainless steel with plain carbon steel
Characteristic | Stainless Steel | Plain Carbon Steel |
---|---|---|
Composition | Primarily iron (Fe) with at least 10.5% chromium (Cr) and other alloying elements (e.g., Ni, Mo, Mn) | Iron (Fe) with a low carbon (C) content, typically ranging from 0.05% to 2.0%, with no significant alloying elements |
Corrosion Resistance | Exceptional corrosion resistance due to the formation of a protective chromium oxide layer. Suitable for harsh environments | Susceptible to corrosion and rust when exposed to moisture and oxygen, requiring protective measures |
Magnetic Properties | Exhibits varying magnetic properties depending on the specific grade | Generally magnetic |
Strength and Durability | Offers high strength and durability, suitable for a wide range of applications | Strong but requires protection against corrosion, limiting durability |
Applications | Used in various industries including kitchenware, medical instruments, architectural structures, aerospace, and automotive manufacturing. Stainless steel manufacturers produce specialized grades. | Commonly used in construction, automotive, machinery, and industrial equipment. Produced in various forms including mild steel and high-strength low-alloy steel. |
Conclusion
In conclusion, our exploration of stainless steel, a remarkable ferrous alloy, has shed light on its composition, properties, and its standing within the realm of metallurgy.
Stainless steel is primarily composed of iron (Fe) with a minimum of 10.5% chromium (Cr) by mass, along with various alloying elements such as nickel (Ni), molybdenum (Mo), and manganese (Mn). Its exceptional resistance to corrosion arises from the formation of a protective chromium oxide layer, allowing it to thrive in environments where corrosion is a critical concern.
Addressing the question at the heart of our discussion, it is crucial to clarify that stainless steel is indeed a ferrous material, as iron constitutes its principal component. Its unique qualities, particularly its resistance to corrosion, make it an invaluable material in various applications.
Stainless steel’s importance cannot be overstated. It serves as a cornerstone in numerous industries, including kitchenware, medical instruments, architectural construction, aerospace, and automotive manufacturing. Stainless steel manufacturers play a pivotal role in producing specialized grades tailored to meet the stringent requirements of these diverse fields.
In essence, stainless steel’s significance lies in its versatile nature and its ability to provide strength, durability, and corrosion resistance. Its legacy in the world of materials science continues to evolve, contributing to the progress and innovation in engineering and technology across a multitude of disciplines.