what is 316 stainless steel?
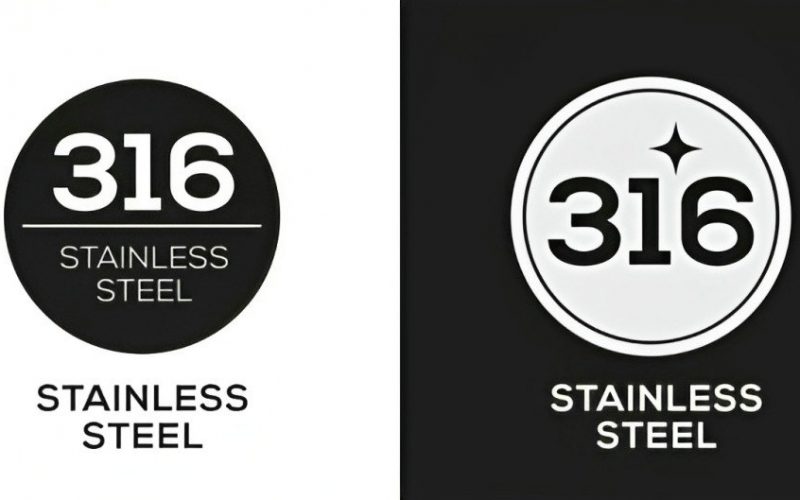
In modern society, we often come into contact with a variety of stainless steel products, from kitchen utensils to building structures, all show excellent performance and diverse applications. Among them, items made of 316 stainless steel are even more ubiquitous, they may be your daily life in the use of kitchen utensils, watch on the delicate parts, and even the important components of marine engineering. This metal that shines all around us has exceptional corrosion resistance and superior strength. So what is 316 stainless steel?
what is 316 stainless steel?
316 stainless steel is a kind of austenitic stainless steel, its chemical composition is mainly composed of iron, chromium, nickel, and other elements. Compared with 304 stainless steel, 316 stainless steel has more chromium and nickel elements added, and the increase of these elements makes 316 stainless steel have better corrosion resistance and higher strength.
In metallurgy, austenite is a metal crystal structure, which has a face-centered cubic dot structure. 316 stainless steel is austenitic structure at room temperature, this structure makes it has good plasticity and toughness, at the same time can be heat-treated to obtain higher strength.
316 stainless steel has excellent corrosion resistance, it can show good corrosion resistance in a variety of corrosive media, such as dilute sulfuric acid, dilute nitric acid, formic acid and so on. Compared with 304 stainless steel, 316 stainless steel has better resistance to chloride ion corrosion, which makes it show superior performance in certain highly corrosive environments.
In addition, 316 stainless steel also has good high temperature performance, can maintain excellent mechanical properties and corrosion resistance at high temperatures. Therefore, in high temperature environments, such as high temperature chemical plants, oil refineries and other fields, 316 stainless steel is a commonly used material.
In short, 316 stainless steel is a kind of stainless steel material with excellent corrosion resistance and high strength, which has a wide range of applications in many fields, such as chemical industry, petroleum, food processing, medical equipment and so on.
Composition composition of 316 stainless steel
316 stainless steel is a stainless steel alloy with excellent corrosion resistance, and its chemical composition plays a key role in its performance. The main chemical composition is as follows:
316 | C% | Si% | Mn% | P% | S% | Ni% | Cr% | Mo% |
ASTM A240/A240M | ≤ 0.08 | ≤ 1.00 | ≤ 2.00 | ≤ 0.045 | ≤ 0.030 | 10.0-14.0 | 16.0-18.0 | 2.0-3.0 |
EN 10028-7 | ≤ 0.08 | ≤ 1.00 | ≤ 2.00 | ≤ 0.045 | ≤ 0.030 | 10.0-14.0 | 16.0-18.0 | 2.0-2.5 |
JIS G4304 | ≤ 0.08 | ≤ 1.00 | ≤ 2.00 | ≤ 0.045 | ≤ 0.030 | 10.0-14.0 | 16.0-18.0 | 2.0-3.0 |
GB/T 4237 | ≤ 0.08 | ≤ 1.00 | ≤ 2.00 | ≤ 0.045 | ≤ 0.030 | 10.0-14.0 | 16.0-18.0 | 2.0-3.0 |
- Chromium (Cr): Chromium is one of the main components of 316 stainless steel, accounting for between 16-18%. The presence of chromium gives stainless steel its resistance to corrosion. It combines with oxygen to form a dense oxide film that prevents further oxidation of the metal, thus protecting the stainless steel from most chemical agents.
- Nickel (Ni): Nickel is another major component of 316 stainless steel and its content ranges from 10-14%. The addition of nickel increases the corrosion resistance of the stainless steel and improves its resistance to high temperatures. Nickel also contributes to the strength and toughness of stainless steel.
- Molybdenum (Mo): Molybdenum content is around 2-3%. Molybdenum is especially critical for improving the corrosion resistance of 316 stainless steel. It enables stainless steel to maintain good corrosion resistance at high temperatures and in highly chlorinated environments, such as in seawater or environments containing acidic chemicals.
- Iron (Fe): Iron is the basic component of stainless steel and makes up the remainder of 316 stainless steel. It provides structure and stability to the stainless steel.
- Other Elements: In addition, 316 stainless steel may contain small amounts of carbon, manganese, silicon and other elements. Minor variations in these elements can adjust the properties of the stainless steel, for example, fine adjustments in carbon content can affect the hardness and workability of the stainless steel.
The precise proportions and combined forms of these chemical components give 316 stainless steel its excellent corrosion resistance, high-temperature stability, and mechanical properties, making it one of the materials of choice in many industrial fields.
properties of 316 stainless steel
316 stainless steel possesses a number of outstanding physical and mechanical properties that make it widely used in a variety of applications. Below is a detailed description of the physical and mechanical properties of 316 stainless steel:
Physical Properties of 316 stainless steel
Physical Properties | Value and Unit |
---|---|
Density | ~8,000 kg/m³ |
Melting Point | 1375-1400 °C |
Freezing Point | ~1400 °C |
Thermal Conductivity | 16.3 W/(m·K) |
Electrical Conductivity | 1.25 × 10^6 S/m |
Magnetic Properties | Generally Non-Magnetic |
- Density: 316 stainless steel has a relatively high density of about 8 grams per cubic centimeter. This density gives it an advantage when constructing parts that require weight support.
- Melting and Freezing Point: The melting point of 316 stainless steel is around 1375-1400 degrees Celsius, while the freezing point is around 1400 degrees Celsius. This indicates that the alloy maintains its stability in high temperature environments.
- Thermal and Electrical Conductivity: 316 stainless steel has good thermal and electrical conductivity, making it popular for many electrical and thermal conductivity applications.
- Magnetism: 316 stainless steel is non-magnetic in most cases. However, high temperature treatment processes may cause localized magnetism to appear.
mechanical Properties of 316 stainless steel
Mechanical Properties | Value and Unit |
---|---|
Tensile Strength | 500-700 MPa |
Yield Strength | ≥ 205 MPa |
Elongation at Break | ≥ 40% |
Hardness (Brinell) | ≤ 217 HB |
Hardness (Rockwell B) | ≤ 95 HRB |
Impact Strength | 100 J |
Fatigue Strength | 186 MPa (at 2×10^7 cycles) |
- Strength: 316 stainless steel has excellent mechanical strength, with tensile strengths typically in the range of 500-700 megapascals (MPa) and compressive strengths above 200 MPa.
- Ductility: It also shows good ductility and plasticity, with high yield strength and large elongation, so that it can withstand tensile and impact loads without easy deformation or fracture.
- Hardness: 316 stainless steel can be cold worked to increase its hardness. After heat treatment, it can reach a high level of hardness for specific applications requiring high strength and wear resistance.
- Fatigue Resistance: This stainless steel has a high retention of fatigue strength and is able to maintain its properties after many stress cycles.
- Coefficient of Thermal Expansion: 316 stainless steel has a relatively low coefficient of thermal expansion, which allows it to maintain its shape and dimensional stability at high temperatures.
These physical and mechanical properties make 316 stainless steel a versatile material with many applications in manufacturing, aerospace, medical, chemical, and many other fields.
Comparison of 316 stainless steel with other grades
Properties | 304 Stainless Steel | 316 Stainless Steel | 316L Stainless Steel | 430 Stainless Steel | 2205 Stainless Steel |
---|---|---|---|---|---|
Chromium Content | 18-20% | 16-18% | 16-18% | 16-18% | 21-23% |
Nickel Content | 8-10.5% | 10-14% | 10-14% | 0.75% | 4.5-6.5% |
Molybdenum Content | – | 2-3% | 2-3% | – | 3-3.5% |
Carbon Content | ≤ 0.08% | ≤ 0.08% | ≤ 0.03% | ≤ 0.12% | ≤ 0.03% |
Tensile Strength | 515 MPa | 500-700 MPa | 485 MPa | 450 MPa | > 621 MPa |
Yield Strength | 205 MPa | ≥ 205 MPa | ≥ 170 MPa | 205 MPa | ≥ 450 MPa |
Corrosion Resistance | High | Very High | Very High | Low | Very High |
Applications | Common general purpose | High-corrosion environments, medical, food | Chemical, medical, food | Interior components, corrosion-resistant parts | Chemical, marine, shipbuilding |
This table provides a comparison of 304, 316, 316L, 430, and 2205 stainless steels in terms of their key components, performance characteristics, and typical applications. Please note that these data may vary slightly based on different manufacturers or specific applications.
1. 316 vs 304 Stainless Steel
Both 316 and 304 are part of the austenitic family of stainless steels, known for their good mechanical properties and corrosion resistance. However, 316 is considered a premium option, primarily because of the addition of molybdenum.
Corrosion Resistance: 316 contains about 2-3% molybdenum, which provides significantly better resistance to chloride environments, such as seawater and salt exposure. This makes 316 an ideal choice for marine and coastal applications, whereas 304 can suffer from pitting corrosion in such conditions.
Cost: 304 is more affordable than 316 because it lacks molybdenum. For most general applications where chloride exposure isn’t an issue, 304 is sufficient, making it a more cost-effective option.
Applications: 304 is commonly used in kitchens, appliances, and architectural structures, whereas 316 is preferred in harsh environments like chemical processing, marine equipment, and medical implants.
2. 316 vs 430 Stainless Steel
Grade 430 is a ferritic stainless steel, which has different properties compared to the austenitic grades like 316.
Magnetic Properties: Unlike 316, 430 is magnetic due to its ferritic structure. If magnetic properties are a requirement, 430 may be more suitable.
Corrosion Resistance: 430 has lower corrosion resistance compared to 316 and is not suitable for environments with high moisture or salt content. 316 offers superior resistance to chlorides and harsh chemicals.
Cost: 430 is more economical than 316 and is often used in interior environments where corrosion resistance is less of a concern, such as in decorative applications or appliance interiors.
3. 316 vs 317 Stainless Steel
Grade 317 is similar to 316 but has higher levels of molybdenum, which enhances its corrosion resistance.
Corrosion Resistance: 317 offers better overall corrosion resistance, particularly in highly corrosive environments such as sulfuric acid and chloride-heavy atmospheres. This makes it a more suitable choice for extreme chemical conditions compared to 316.
Cost: 317 is more expensive than 316 due to its increased alloy content, but it may be worth the investment for more severe conditions.
Applications: 317 is typically used in chemical and petrochemical plants where higher corrosion resistance is needed, whereas 316 is more common in marine, pharmaceutical, and food processing industries.
4. 316 vs 2205 Duplex Stainless Steel
2205 is a duplex stainless steel that contains both austenitic and ferritic structures, offering a balance of both strength and corrosion resistance.
Strength: 2205 has nearly twice the yield strength of 316, making it ideal for structural applications requiring high strength and toughness.
Corrosion Resistance: 2205 offers superior resistance to stress corrosion cracking, particularly in chloride environments. While 316 performs well in these environments, 2205 is better suited for high-pressure or high-stress applications.
Cost: 2205 is generally more expensive than 316, but its higher strength allows for reduced material thickness, which may offset the higher material cost in some cases.
5. 316 vs 904L Stainless Steel
904L is a super-austenitic stainless steel with high amounts of chromium, nickel, and molybdenum, offering excellent corrosion resistance.
Corrosion Resistance: 904L significantly outperforms 316 in extremely corrosive environments, such as sulfuric or phosphoric acid conditions. Its high nickel and molybdenum content make it resistant to pitting and crevice corrosion, even in highly aggressive environments.
Cost: 904L is considerably more expensive than 316 due to its higher alloy content. It’s usually used in highly specific, aggressive environments where 316 would not provide sufficient longevity.
Applications: 904L is typically used in chemical processing, pollution control equipment, and seawater handling, whereas 316 is more common in less severe environments.
Conclusion
In conclusion, let’s recap the key points discussed about 316 stainless steel. We explored its composition, including the role of iron, chromium, nickel, and molybdenum, and highlighted its excellent corrosion resistance and mechanical properties. We also discussed the considerations when using 316 stainless steel, such as environmental conditions, temperature extremes, surface finish, and fabrication techniques. Additionally, we mentioned the limitations and potential drawbacks, such as the higher cost and susceptibility to chloride stress corrosion cracking.
The significance of 316 stainless steel in various industries cannot be overstated. Its superior corrosion resistance makes it a preferred choice in applications where exposure to harsh environments or corrosive substances is common. Industries such as chemical processing, marine, food and beverage, pharmaceutical, and architecture rely on the durability and reliability of 316 stainless steel to ensure long-lasting performance.
As with any material, continuous exploration and research on 316 stainless steel are encouraged. Advancements in manufacturing techniques, surface treatments, and alloy modifications can further enhance its properties and expand its applications. Consulting with stainless steel suppliers and experts will provide valuable insights into the latest developments and best practices for utilizing 316 stainless steel effectively.