Steel Products
Cold Working and Its Effects on Stainless Steel
In the manufacturing industry, cold working is a crucial process used to enhance the properties of metals, including stainless steel. Cold working, also known as work hardening, involves deforming the metal at a temperature below its recrystallization point. This process results in significant changes in the material’s physical and mechanical properties, making it more suitable for specific applications. In this blog, we will delve into the effects of cold working on stainless steel, exploring how it alters the metal’s strength, hardness, ductility, and other key characteristics.
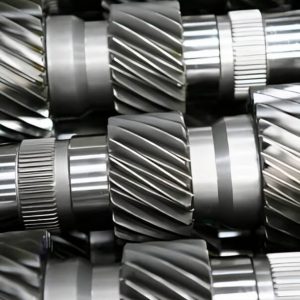
What is Cold Working?
Cold working refers to the process of strengthening metal by plastic deformation at room temperature. Unlike hot working, where the metal is heated above its recrystallization temperature, cold working involves mechanical processes like rolling, drawing, forging, and bending without applying heat.
The primary objective of cold working is to increase the metal’s strength and hardness while reducing its ductility. This is achieved through the rearrangement of the metal’s crystal structure, which leads to the development of dislocations within the grain structure. These dislocations hinder further movement of atoms, thereby increasing the metal’s resistance to deformation.
Effects of Cold Working on Stainless Steel
1. Increased Strength and Hardness
One of the most significant effects of cold working on stainless steel is the increase in strength and hardness. As the metal undergoes plastic deformation, dislocations are introduced into the crystal structure, making it more difficult for further dislocations to occur. This results in a higher yield strength and tensile strength.
For instance, the tensile strength of 304 stainless steel can increase from approximately 515 MPa in its annealed state to over 900 MPa after substantial cold working. This makes cold-worked stainless steel ideal for applications where high strength is essential, such as in the construction of high-pressure vessels and components for the aerospace industry.
2. Reduction in Ductility
While cold working enhances the strength and hardness of stainless steel, it simultaneously reduces its ductility. Ductility refers to the material’s ability to deform plastically without breaking. As the metal becomes stronger, it also becomes more brittle, which can limit its formability in certain applications.
For example, after significant cold working, 304 stainless steel may lose up to 50% of its ductility compared to its annealed state. This trade-off between strength and ductility must be carefully considered when designing components that require both high strength and some degree of flexibility.
3. Improved Surface Finish
Cold working can also improve the surface finish of stainless steel. Processes like cold rolling and drawing not only increase the metal’s strength but also produce a smoother, shinier surface. This is particularly beneficial in applications where both aesthetic appeal and corrosion resistance are important, such as in architectural cladding and kitchen appliances.
The smoother surface achieved through cold working can enhance the stainless steel’s resistance to corrosion by reducing the number of surface imperfections where corrosive agents might initiate. Additionally, the improved surface finish can also enhance the metal’s wear resistance.
4. Residual Stresses
Cold working introduces residual stresses into the stainless steel, which can affect the metal’s performance in service. These stresses arise from the non-uniform deformation of the material during the cold working process. If not managed properly, residual stresses can lead to warping, cracking, or premature failure of the component under load.
For this reason, cold-worked stainless steel is often subjected to additional treatments, such as stress-relief annealing, to reduce the residual stresses and improve the material’s stability.
5. Altered Magnetic Properties
Cold working can also affect the magnetic properties of stainless steel. While austenitic stainless steels (such as 304 and 316 grades) are generally non-magnetic, cold working can induce a small amount of magnetism. This is due to the formation of martensitic structures within the stainless steel as a result of the deformation process.
For applications where non-magnetic properties are critical, it is essential to account for this potential change and choose an appropriate stainless steel grade or apply further heat treatment to restore the material’s non-magnetic state.
6. Enhanced Corrosion Resistance in Certain Conditions
In some cases, cold working can enhance the corrosion resistance of stainless steel by creating a more uniform and compact grain structure. This improvement is particularly noticeable in stainless steels used in mildly corrosive environments. However, the opposite can also occur if the cold working process introduces surface defects or residual stresses that serve as initiation sites for corrosion.
Therefore, the specific effects of cold working on corrosion resistance depend on the type of stainless steel, the degree of deformation, and the intended service environment.
Applications of Cold-Worked Stainless Steel
The enhanced properties of cold-worked stainless steel make it suitable for a wide range of applications across various industries:
1. Automotive Industry
Cold-worked stainless steel is commonly used in the automotive industry for components that require high strength and excellent surface finish, such as exhaust systems, structural components, and fasteners.
2. Aerospace and Defense
In the aerospace and defense sectors, cold-worked stainless steel is valued for its high strength-to-weight ratio and resistance to fatigue. It is often used in the manufacturing of aircraft components, missile parts, and other critical applications where reliability is paramount.
3. Medical Devices
The medical industry utilizes cold-worked stainless steel for surgical instruments, implants, and other medical devices that require high strength, wear resistance, and biocompatibility.
4. Construction and Architecture
Cold-worked stainless steel is used in the construction of bridges, buildings, and other structures where both strength and aesthetic appeal are important. Its improved surface finish and corrosion resistance make it an ideal material for architectural elements and structural supports.
Expand your knowledge :
4 ways to deal with the damage of cold working to the corrosion resistance of stainless steel pipes
Stainless steel, especially austenitic stainless steel, has excellent plasticity, which makes cold processing methods such as cold drawing, cold rolling, cold rolling, cold bending, cold expansion, cold twisting, etc. easy to achieve. However, all these cold processing methods, like welding, will inevitably damage the performance of stainless steel pipes, especially corrosion resistance or heat resistance.
Specifically, adverse effects can be seen from five aspects:
1. It will lead to the increase of microscopic defects such as lattice dislocation and surface roughness of the material, and induce martensitic phase transformation and precipitation of carbides. For example, austenitic steel shows an increase in magnetism after cold working.
2. If the lattice dislocation or phase transformation of the material occurs on the surface, it will become the starting point of local corrosion such as pitting corrosion. This phenomenon will have a direct adverse effect when the deformation degree reaches 20% of the section reduction rate.
3. After cold working, residual stress will be left in the material, which is extremely unfavorable for the material’s resistance to stress corrosion cracking (SCC). Any degree of cold working will greatly increase the material’s sensitivity to SCC.
4. The degree of cold working also has an adverse effect on the high-temperature endurance strength of austenitic stainless steel. Generally, the higher the working temperature or the higher the fracture life requirement, the lower the allowable degree of cold working.
5. For stainless steel pipe applications subjected to alternating loads, cold working will increase the crack propagation rate due to the decrease in elongation and residual elongation.
According to industry insiders, there are four ways to eliminate it:
1. The stainless steel pipe standards of most countries, especially the unified European stainless steel pipe standards, stipulate that all stainless steel seamless pipes must be supplied in a solid solution or annealed state to eliminate the performance damage caused by cold working and welding.
2. Three key parameters should be paid attention to in solid solution treatment: heating temperature, rapid cooling method and high temperature residence time. Excessive solid solution treatment temperature or residence time will be detrimental to the corrosion resistance of the material. To determine whether the solid solution is in place, hardness measurement, flaring, curling, flattening and stretching data can all be determined, among which hardness measurement is the simplest.
3. Because solid solution or annealing significantly increases manufacturing costs and production cycles due to high-temperature heating and pickling treatment, and there are waste gases and wastewater emissions such as acid mist, some companies omit this process and use this product, which is prone to production and personal accidents after use.
4. For some products or application conditions that may be difficult to implement solid solution or annealing, controlling the degree of cold working (cold working deformation) and performing local low-temperature stress relief annealing are practical methods to reduce harmful effects.
Conclusion of Cold Working's Effects on Stainless Steel
Cold working is a powerful tool in stainless steel manufacturing that allows engineers to tailor the material’s properties to meet specific requirements. By increasing strength and hardness while reducing ductility, cold working produces stainless steel that is suitable for high-performance applications across a variety of industries.
However, it is essential to understand the trade-offs involved in cold working, such as the reduction in ductility and the introduction of residual stresses, to ensure that the final product meets the intended specifications. When properly managed, cold working can significantly enhance the performance and durability of stainless steel, making it a valuable process in modern manufacturing.
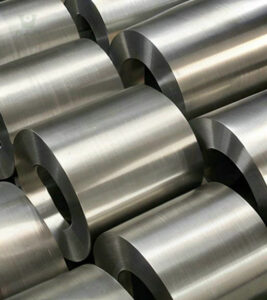
Duplex Steel 2205 Coils: Understanding the Applications and Uses
Duplex Steel 2205 Coils: Understanding the Applications and Uses Duplex Steel 2205 Coils Duplex Steel 2205 coils are widely used duplex stainless steel alloy known
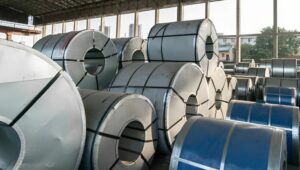
What Are Steel Coils Used For ?
What are steel coils used for? stainless steel coils supplier in China Steel has been at the core of industrial development for centuries, and steel coils play
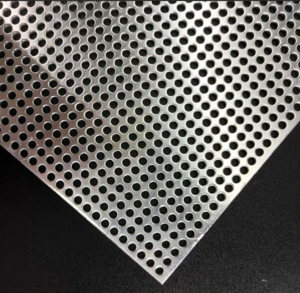
Top 10 Applications of Perforated Metal in Architectural Projects
Top 10 Applications of Perforated Metal in Architectural Projects perforated metal (stainless steel sheet) Perforated metal has long been a staple in industrial design, but
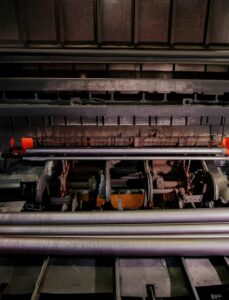
Guide to Stainless Steel Pipe Rolling: Process, Benefits, and Applications
Guide to Stainless Steel Pipe Rolling: Process, Benefits, and Applications stainless steel pipe What is Stainless steel pipe rolling? Stainless steel pipe rolling is a
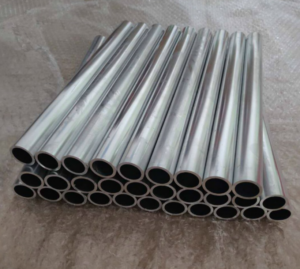
How Are Stainless Steel Welded Tubes Made?
How Are Stainless Steel Welded Tubes Made? stainless steel welded tubes Stainless steel welded tubes are a vital component in various industries, including construction, automotive,
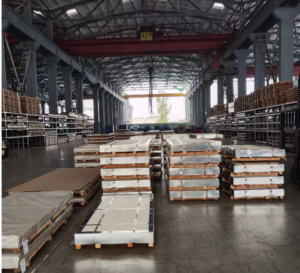
Comparing Stainless Steel Sheets: 409 vs. 410 vs. 410S vs. 420 vs. 430 vs. 440 vs. 446
Comparing Stainless Steel Sheets: 409 vs. 410 vs. 410S vs. 420 vs. 430 vs. 440 vs. 446 Each stainless steel sheet has its own unique