Hot Rolling vs. Cold Rolling: Differences in Stainless Steel Manufacturing
Hot Rolling vs. Cold Rolling
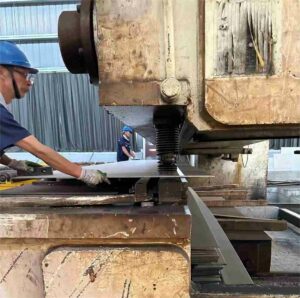
In the manufacturing of stainless steel, the processes of hot rolling vs cold rolling are fundamental to shaping and enhancing the material’s properties. Each method offers distinct advantages and is suited to specific applications. Understanding the differences between hot rolling and cold rolling, as well as their impact on the performance of stainless steel, is crucial for selecting the right process for your needs.
Hot rolling and cold rolling are both processes for forming steel or steel plates. They have a great influence on the structure and performance of steel. Hot rolling is the main rolling method for steel, while cold rolling is only used to produce small steel and thin plates.
Hot Rolling vs. Cold Rolling: What's the differences?
What is Hot Rolling?
The Process
Hot rolling involves passing heated stainless steel through large rolls at high temperatures, typically above the recrystallization temperature of the steel (approximately 1700°F or 927°C). This process helps to shape the steel into sheets, plates, bars, or other forms. Because the steel is rolled at such high temperatures, it remains malleable and can be shaped with less force.
Characteristics and Benefits
Surface Finish: Hot rolled stainless steel typically has a rougher surface texture compared to cold rolled steel. This is due to the scale that forms on the steel’s surface as it cools.
Size Tolerances: Hot rolling allows for larger size tolerances. The steel may shrink slightly as it cools, leading to less precision in dimensions compared to cold rolled steel.
Ductility and Formability: Hot rolled steel is more ductile, making it easier to form into complex shapes without the risk of cracking.
Cost-Effectiveness: The hot rolling process is less expensive than cold rolling due to the reduced need for precise control and the ability to produce larger quantities in less time.
Disadvantages of Hot Rolling
1. After hot rolling, the non-metallic inclusions (mainly sulfides and oxides, as well as silicates) inside the steel are pressed into thin sheets, resulting in stratification (interlayer) phenomenon. Stratification greatly deteriorates the tensile performance of the steel along the thickness direction, and interlayer tearing may occur when the weld shrinks. The local strain induced by weld shrinkage often reaches several times the yield point strain, which is much larger than the strain caused by load;
2. Residual stress caused by uneven cooling. Residual stress is the internal self-balanced stress without external force. Hot-rolled steel sections of various cross-sections have this type of residual stress. Generally, the larger the cross-sectional size of the steel section, the greater the residual stress. Although the residual stress is self-balanced, it still has a certain impact on the performance of steel components under external forces. For example, it may have an adverse effect on deformation, stability, fatigue resistance, etc.
Common Applications
Hot rolled stainless steel is often used in applications where precise dimensions are not critical, and where the material will be subjected to further processing or machining. Typical applications include:
- Structural components (e.g., I-beams, rails)
- Automotive parts
- Agricultural equipment
- Industrial machinery
What is Cold Rolling?
The Process
Cold rolling involves passing stainless steel through rolls at room temperature, below its recrystallization temperature. This process follows the hot rolling process and involves additional steps to achieve finer dimensional accuracy and improved surface finish. Cold rolling is done with greater precision and typically requires more energy and time.
Characteristics and Benefits
Surface Finish: Cold rolled stainless steel has a much smoother and shinier surface compared to hot rolled steel. This makes it ideal for applications where aesthetics are important.
Dimensional Precision: Cold rolling allows for tighter dimensional tolerances, making it suitable for applications that require precise measurements.
Strength and Hardness: The cold rolling process increases the strength and hardness of the steel through work hardening. This makes cold rolled stainless steel more resistant to deformation under stress.
Surface Quality: Cold rolled steel is free from scale, and the surface quality is higher, making it suitable for applications that require a clean, polished finish.
Disadvantages of Cold Rolling
1. Although there is no hot plastic compression during the forming process, there are still residual stresses in the cross section, which will inevitably affect the overall and local buckling characteristics of the steel;
2. The cold-rolled steel section is generally an open section, which makes the free torsional stiffness of the cross section low. It is easy to torsion when bent, and it is easy to bend-torsion buckling when compressed, and the torsion resistance is poor;
3. The wall thickness of cold-rolled steel is small, and there is no thickening at the corners where the plates are connected, so the ability to withstand local concentrated loads is weak.
Common Applications
Cold rolled stainless steel is typically used in applications where high precision, a smooth surface, and strength are important. These include:
- Home appliances (e.g., refrigerators, washing machines)
- Aerospace components
- Automotive body panels
- Food and beverage processing equipment
- Decorative architectural elements
The main differences between hot rolling and cold rolling are:
Cold-rolled steel allows local buckling of the cross section, so that the bearing capacity of the rod after buckling can be fully utilized; while hot-rolled steel does not allow local buckling of the cross section.
The causes of residual stress in hot-rolled steel and cold-rolled steel are different, so the distribution on the cross section is also very different. The residual stress distribution on the cross section of cold-bent thin-walled steel is bending type, while the residual stress distribution on the cross section of hot-rolled steel or welded steel is film type.
The free torsional stiffness of hot-rolled steel is higher than that of cold-rolled steel, so the torsional performance of hot-rolled steel is better than that of cold-rolled steel.
Hot Rolling vs. Cold Rolling: Impact on Stainless Steel Performance
Hot Rolled Stainless Steel
Hot rolled stainless steel is ideal for structural applications where strength and toughness are more important than surface finish and precision. Its ductility allows it to be formed into large structural components, and its rough surface can be easily machined or coated as needed.
Cold Rolled Stainless Steel
Cold rolled stainless steel, on the other hand, is preferred in applications that require a high level of finish and precise dimensions. The increased strength and hardness make it suitable for load-bearing applications, while the smooth surface is ideal for decorative elements or products where appearance is critical.
Conclusion
Understanding the differences between hot rolling and cold rolling is essential for selecting the right type of stainless steel for your application. Hot rolling is best suited for structural and high-volume applications where cost and ductility are important. Cold rolling, with its superior surface finish, dimensional precision, and enhanced strength, is the preferred choice for high-quality, precision-required products.
Huaxiao Stainless Steel: Hot Rolling and Cold Rolling Stainless Steel Supplier
As a leading stainless steel supplier in Asia, Huaxiao Stainless Steel offers customers high-quality stainless steel products at very competitive prices.
<contact us to get a quote>
Recommended Articles
Our Stainless Steel Bar Products