Quality Inspection Methods for Stainless Steel Products
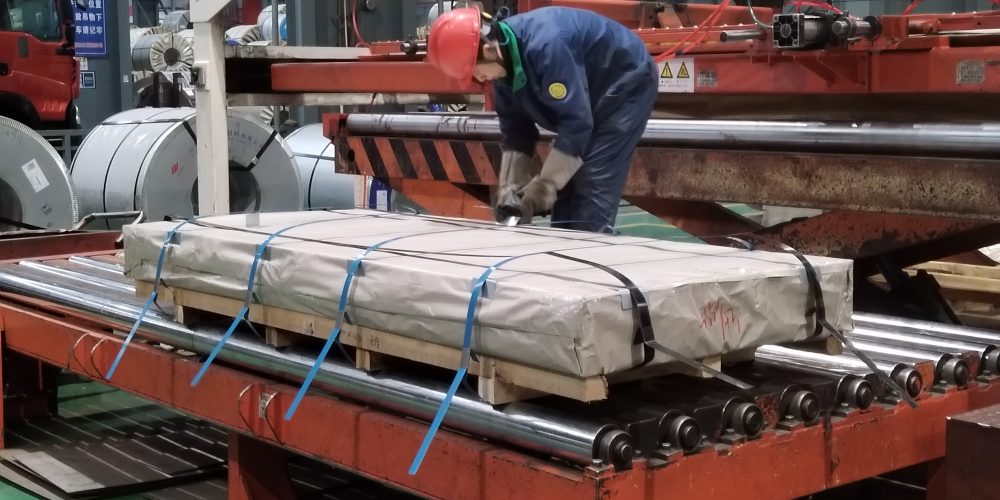
As stainless steel products supplier in the metal materials industry, we often emphasize the importance of thorough quality inspection methods for stainless steel products. Ensuring the integrity and performance of stainless steel is crucial for various applications, from kitchen utensils to chemical equipment. This blog post will delve into the common quality inspection methods used to evaluate stainless steel products, ensuring they meet stringent industry standards.
Visual Inspection
Visual inspection is the first line of defense in quality control. By examining the stainless steel surface with the naked eye or magnification tools, inspectors can identify surface defects such as cracks, dents, scratches, and corrosion spots. Aesthetic aspects, including surface finish and polish, are also assessed to ensure they meet the desired standards.
Chemical Composition Analysis
To verify the alloy composition of stainless steel products, chemical analysis is performed using advanced instruments like spectrometers. This method ensures that the stainless steel conforms to the specified grades and standards, such as ASTM or ISO. Accurate chemical composition analysis is essential to guarantee the material’s performance and corrosion resistance.
Mechanical Properties Testing
Tensile Testing
Tensile testing measures the material’s tensile strength, yield strength, and elongation. This test helps determine the stainless steel products’ ability to withstand stretching forces without breaking, which is crucial for applications requiring high strength.
Hardness Testing
Hardness tests, including Brinell (HB), Rockwell (HRB, HRC), and Vickers (HV), are conducted to evaluate the material’s resistance to deformation. These tests provide insights into the durability and wear resistance of stainless steel products.
Impact Testing
Impact testing assesses the material’s toughness and its ability to absorb energy during a high-velocity impact. This test is particularly important for applications exposed to sudden or extreme forces.
Corrosion Testing
Corrosion resistance is a key property of stainless steel products. Common corrosion tests include salt spray testing and acid immersion testing. These tests simulate harsh environments to evaluate how well the stainless steel can resist corrosion, ensuring long-term performance.
Non-Destructive Testing (NDT)
NDT methods are used to detect internal and surface defects without damaging the material.
Ultrasonic Testing
Ultrasonic testing uses high-frequency sound waves to detect internal flaws such as cracks and voids. This method provides detailed information about the integrity of the stainless steel.
Magnetic Particle Inspection
Magnetic particle inspection is effective for detecting surface and near-surface defects. It involves magnetizing the stainless steel and applying magnetic particles to reveal any discontinuities.
X-Ray Inspection
X-ray inspection is used for deep internal defect detection. It provides a clear image of the internal structure, revealing hidden flaws that might compromise the material’s strength.
Dimensional and Shape Measurement
Accurate measurement of dimensions and shapes is essential for maintaining consistency in production. Tools like calipers, micrometers, and coordinate measuring machines (CMM) are used to ensure the stainless steel products meet the specified tolerances and geometries.
Standards and Certifications
Compliance with international standards and certifications, such as ISO 9001, is crucial for ensuring consistent quality. Certifications like CE and UL also demonstrate adherence to industry standards and regulations.
Fatigue Testing
Fatigue testing evaluates the material’s durability under cyclic loading conditions. This test helps predict the stainless steel’s lifespan and performance in applications subjected to repeated stress.
Environmental Testing
Stainless steel products are often exposed to extreme temperatures and humidity. Environmental testing ensures that the material maintains its properties under such conditions, confirming its suitability for specific applications.
In conclusion, rigorous quality inspection methods are essential for ensuring the performance and reliability of stainless steel products. By employing a combination of visual inspection, chemical analysis, mechanical testing, corrosion testing, non-destructive testing, dimensional measurement, and adherence to standards, manufacturers can guarantee high-quality stainless steel products that meet the demands of various industries. These practices not only enhance product performance but also ensure customer satisfaction and safety.
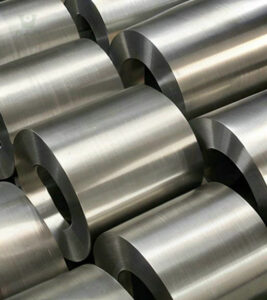
Duplex Steel 2205 Coils: Understanding the Applications and Uses
Duplex Steel 2205 Coils: Understanding the Applications and Uses Duplex Steel 2205 Coils Duplex Steel 2205 coils are widely used duplex stainless steel alloy known
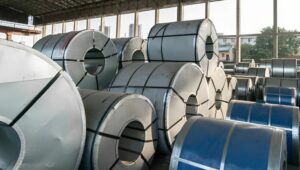
What Are Steel Coils Used For ?
What are steel coils used for? stainless steel coils supplier in China Steel has been at the core of industrial development for centuries, and steel coils play
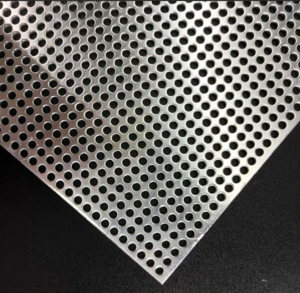
Top 10 Applications of Perforated Metal in Architectural Projects
Top 10 Applications of Perforated Metal in Architectural Projects perforated metal (stainless steel sheet) Perforated metal has long been a staple in industrial design, but
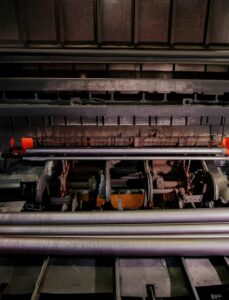
Guide to Stainless Steel Pipe Rolling: Process, Benefits, and Applications
Guide to Stainless Steel Pipe Rolling: Process, Benefits, and Applications stainless steel pipe What is Stainless steel pipe rolling? Stainless steel pipe rolling is a
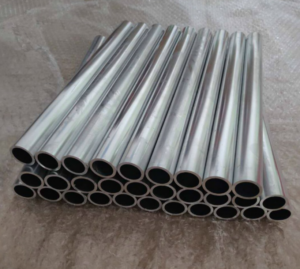
How Are Stainless Steel Welded Tubes Made?
How Are Stainless Steel Welded Tubes Made? stainless steel welded tubes Stainless steel welded tubes are a vital component in various industries, including construction, automotive,
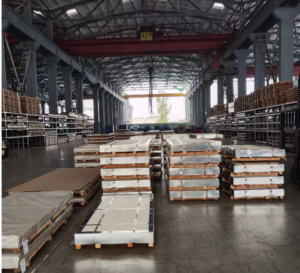
Comparing Stainless Steel Sheets: 409 vs. 410 vs. 410S vs. 420 vs. 430 vs. 440 vs. 446
Comparing Stainless Steel Sheets: 409 vs. 410 vs. 410S vs. 420 vs. 430 vs. 440 vs. 446 Each stainless steel sheet has its own unique
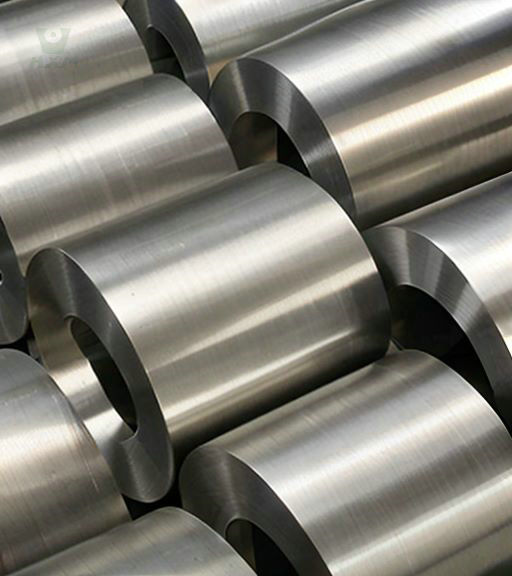
Duplex Steel 2205 Coils: Understanding the Applications and Uses
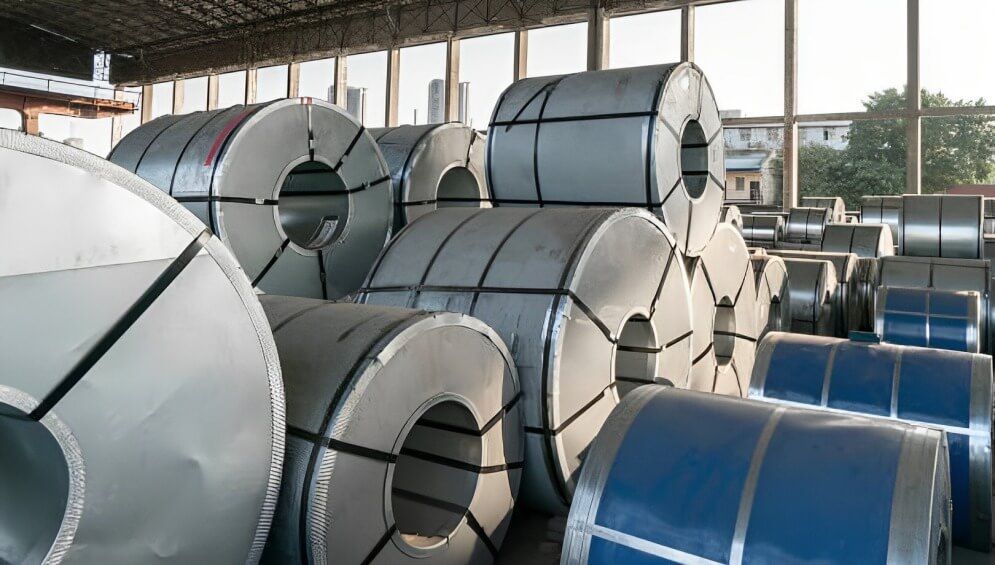
What Are Steel Coils Used For ?
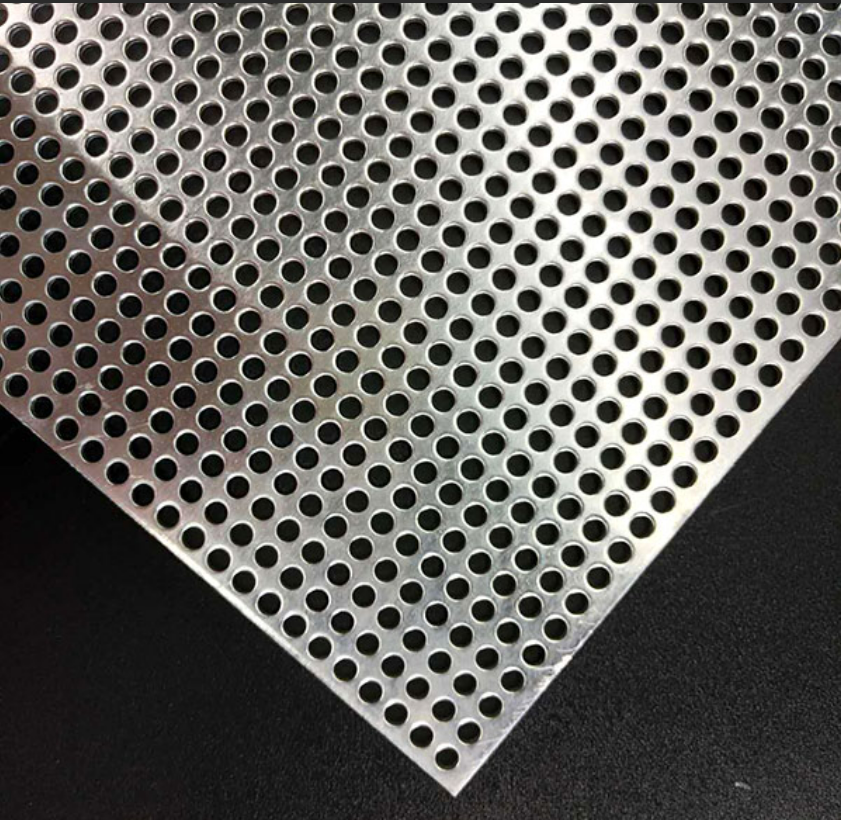
Top 10 Applications of Perforated Metal in Architectural Projects
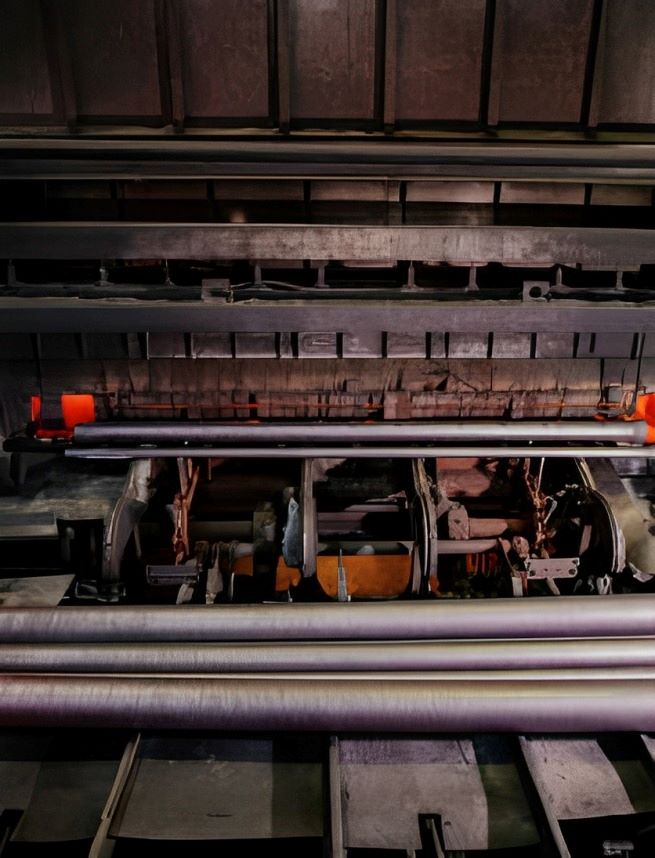