Laser Cutting and Its Precision in Stainless Steel Fabrication
Laser cutting is the most important application technology in the laser processing industry, accounting for more than 70% of the entire laser processing industry. Laser cutting is the most advanced cutting technology in the world. Because it has the advantages of precision manufacturing, flexible cutting, special-shaped processing, one-time forming, fast speed and high efficiency, it solves many problems that cannot be solved by conventional methods in industrial production. Laser can cut most metal materials and non-metal materials.
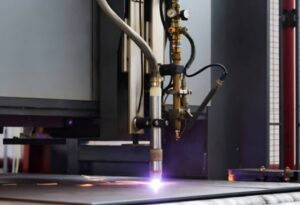
Laser cutting is a process that uses a concentrated beam of light to melt, burn, or vaporize materials, allowing for clean and precise cuts. The laser used is typically a high-powered gas laser, such as a CO2 laser, or a fiber laser. In stainless steel fabrication, laser cutting is widely used due to its ability to deliver highly accurate cuts on both thin and thick materials, often with no need for post-processing.
How Laser Cutting Works in Stainless Steel Fabrication
The laser cutting process involves focusing a high-powered laser beam onto the stainless steel surface. This beam, when combined with a gas (like nitrogen or oxygen), either melts or vaporizes the material along a precise line, allowing the excess material to be blown away. The result is a clean, smooth edge that requires little to no further finishing.
Advantages of Laser Cutting in Stainless Steel Fabrication
1. Precision and Accuracy
One of the key benefits of laser cutting in stainless steel fabrication is its precision. Laser cutting can achieve extremely tight tolerances, often as fine as 0.1 mm. This level of accuracy is essential for industries like aerospace, automotive, and medical device manufacturing, where even the smallest error can lead to product failure.
- High Precision: Laser cutting offers tight dimensional accuracy and clean edges, reducing the need for secondary processes.
- Intricate Designs: The technology can easily handle complex and intricate patterns that would be difficult or impossible to achieve with traditional cutting methods.
2. Speed and Efficiency
Compared to traditional cutting techniques such as plasma cutting or waterjet cutting, laser cutting is significantly faster. The combination of speed and accuracy means that large batches of stainless steel parts can be processed quickly and efficiently, reducing lead times for manufacturers.
- Increased Production Speed: Faster cutting times allow for quicker turnaround on projects.
- Minimal Waste: The focused laser beam minimizes material waste, making the process more efficient.
3. Versatility in Material Thickness
Laser cutting is versatile enough to handle a wide range of material thicknesses. Whether working with thin sheets or thicker stainless steel plates, the laser cutting process provides consistent results without compromising the quality of the cut.
- Thin Sheets: Ideal for applications requiring detailed designs, such as architectural components.
- Thick Plates: Laser cutting can handle up to 20mm thick stainless steel plates with precision, making it suitable for industrial applications like structural components.
4. Reduced Heat-Affected Zones (HAZ)
Traditional cutting methods, such as plasma or oxy-fuel cutting, often produce large heat-affected zones (HAZ) that can alter the mechanical properties of the material. This is especially problematic in stainless steel fabrication, where maintaining corrosion resistance is crucial. Laser cutting, on the other hand, has a much smaller HAZ, ensuring that the stainless steel retains its inherent properties.
- Small HAZ: The focused laser beam reduces the heat-affected area, preserving the strength and corrosion resistance of stainless steel.
- Improved Material Integrity: The reduced thermal distortion ensures that the structural integrity of the material is maintained.
5. Clean and Smooth Edges
One of the most noticeable benefits of laser cutting in stainless steel is the clean, smooth edges it produces. Unlike mechanical cutting methods, laser cutting leaves little to no burrs or imperfections, reducing the need for secondary finishing processes like grinding or sanding.
- Minimal Finishing Required: The clean cuts reduce post-processing, saving both time and money.
- Aesthetic Quality: For applications like decorative stainless steel panels or furniture, the smooth edges offer a visually appealing finish.
Applications of Laser Cutting in Stainless Steel Fabrication
Laser cutting is used in a wide range of industries, including automotive, aerospace, construction, and medical manufacturing. Some specific applications of laser cutting in stainless steel fabrication include:
- Automotive Parts: Laser cutting allows for precise production of stainless steel components used in engines, exhaust systems, and body structures.
- Architectural Design: Laser-cut stainless steel is often used for decorative panels, facades, and custom designs in modern architecture.
- Medical Devices: In the medical field, stainless steel is a common material for surgical instruments, and laser cutting ensures the accuracy needed for these delicate tools.
- Industrial Equipment: Stainless steel components in heavy machinery often require precise cuts to ensure proper fit and function.
Future Trends in Laser Cutting and Stainless Steel Fabrication
As technology continues to evolve, laser cutting is becoming even more efficient and precise. The introduction of high-powered fiber lasers has made it possible to cut thicker materials at faster speeds without sacrificing quality. Additionally, advancements in automation are allowing for laser cutting machines to operate with minimal human intervention, further increasing efficiency in manufacturing environments.
- Fiber Lasers: Offering higher efficiency and faster processing times than traditional CO2 lasers, fiber lasers are becoming the go-to technology for stainless steel cutting.
- Automation: CNC-controlled laser cutting machines are enabling faster production with fewer errors, further reducing lead times.
Conclusion
Laser cutting has revolutionized stainless steel fabrication by offering unparalleled precision, speed, and versatility. Whether you’re working with thin stainless steel sheets for intricate designs or thick plates for industrial applications, laser cutting ensures that your project meets the highest standards of accuracy and quality. As the technology continues to evolve, it is poised to remain an essential tool in the fabrication industry for years to come.
By understanding the benefits of laser cutting in stainless steel fabrication, you can make informed decisions that will enhance both the quality and efficiency of your projects. Whether you are a manufacturer, designer, or engineer, laser cutting technology will help you meet the demands of modern metal fabrication with confidence.
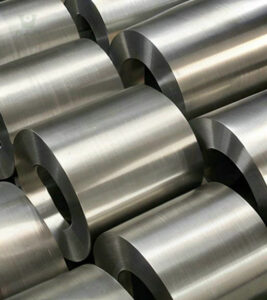
Duplex Steel 2205 Coils: Understanding the Applications and Uses
Duplex Steel 2205 Coils: Understanding the Applications and Uses Duplex Steel 2205 Coils Duplex Steel 2205 coils are widely used duplex stainless steel alloy known
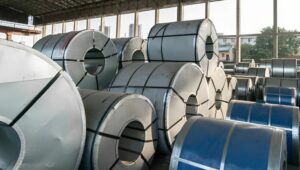
What Are Steel Coils Used For ?
What are steel coils used for? stainless steel coils supplier in China Steel has been at the core of industrial development for centuries, and steel coils play
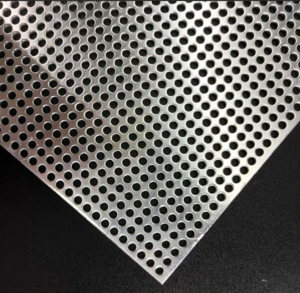
Top 10 Applications of Perforated Metal in Architectural Projects
Top 10 Applications of Perforated Metal in Architectural Projects perforated metal (stainless steel sheet) Perforated metal has long been a staple in industrial design, but
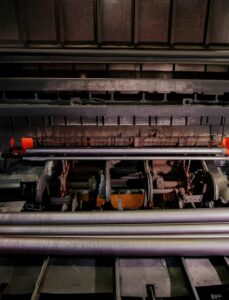
Guide to Stainless Steel Pipe Rolling: Process, Benefits, and Applications
Guide to Stainless Steel Pipe Rolling: Process, Benefits, and Applications stainless steel pipe What is Stainless steel pipe rolling? Stainless steel pipe rolling is a
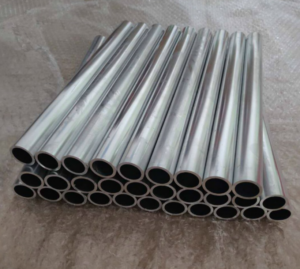
How Are Stainless Steel Welded Tubes Made?
How Are Stainless Steel Welded Tubes Made? stainless steel welded tubes Stainless steel welded tubes are a vital component in various industries, including construction, automotive,
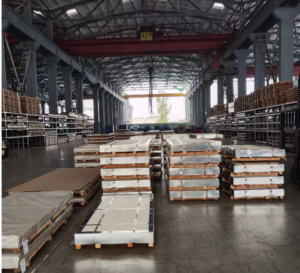
Comparing Stainless Steel Sheets: 409 vs. 410 vs. 410S vs. 420 vs. 430 vs. 440 vs. 446
Comparing Stainless Steel Sheets: 409 vs. 410 vs. 410S vs. 420 vs. 430 vs. 440 vs. 446 Each stainless steel sheet has its own unique