The impact of rolling techniques on stainless steel strength
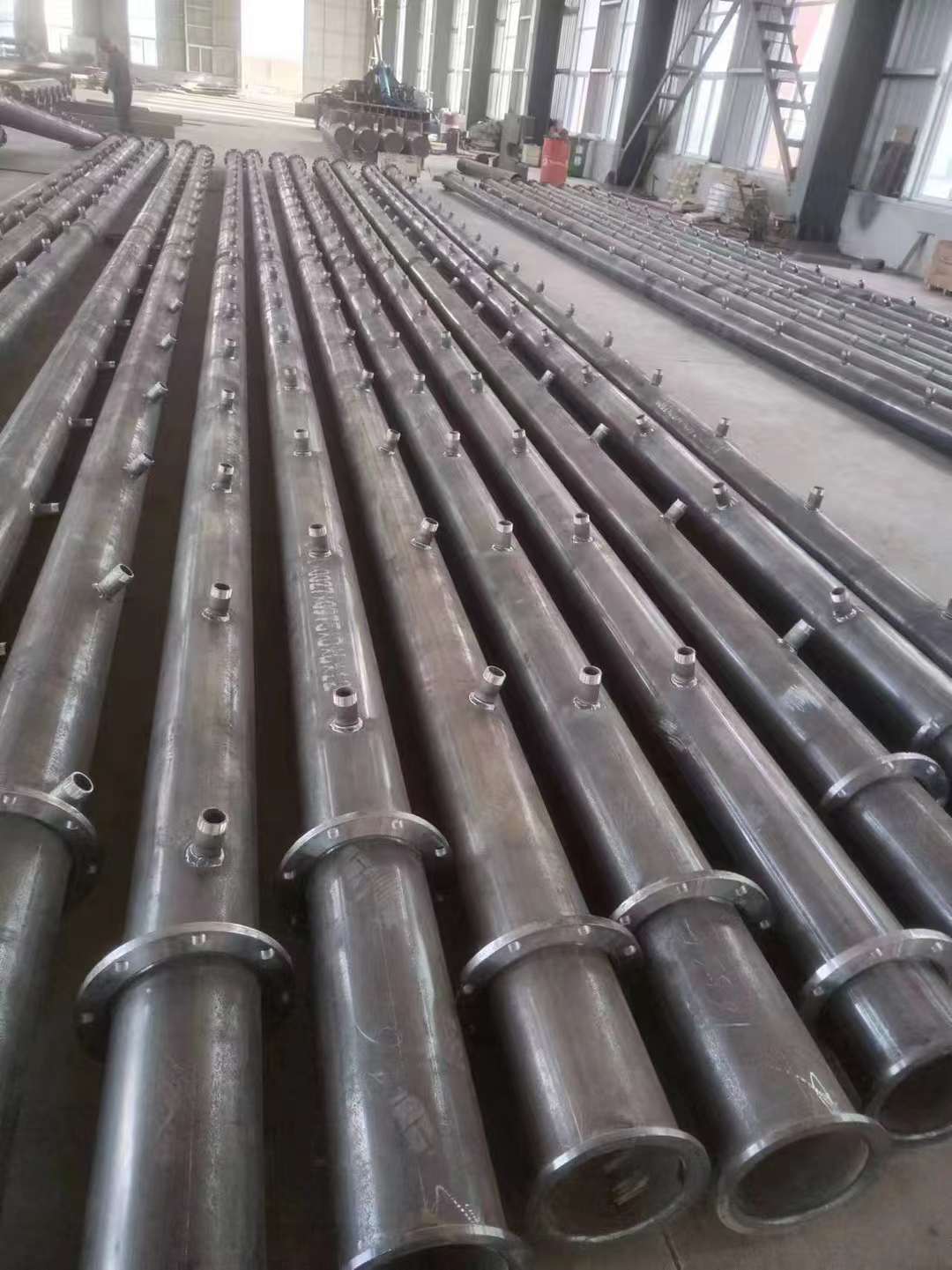
In the stainless steel industry, the strength and durability of the final product are of paramount importance, especially for applications requiring high performance under extreme conditions. One of the critical factors influencing the strength of stainless steel is the rolling technique used during the manufacturing process. Rolling techniques, such as hot rolling and cold rolling, play a significant role in determining the mechanical properties, microstructure, and performance characteristics of stainless steel.
Rolling of Techniques on Stainless Steel Strength
---Understanding the Basics of Rolling Techniques
Rolling is a crucial process in the manufacturing of stainless steel, where the material is passed through a set of rollers to reduce its thickness and achieve the desired shape and surface finish. The process can be classified into two primary categories based on the temperature at which the rolling is performed: hot rolling and cold rolling.
Hot Rolling: In hot rolling, stainless steel is heated to temperatures above its recrystallization point, typically around 1100°C (2000°F). This high temperature allows the steel to become more malleable, making it easier to shape and form. The process results in a rough surface finish but enhances the steel’s ductility.
Cold Rolling: Cold rolling is performed at or near room temperature, below the recrystallization point of stainless steel. Unlike hot rolling, cold rolling involves higher mechanical stresses, which improve the surface finish, enhance strength, and reduce thickness with more precision. Cold-rolled stainless steel is known for its high strength and excellent surface quality.
Rolling of Techniques on Stainless Steel Strength
---The Impact of Rolling Techniques on Strength
Hot Rolling: Improved Ductility, Lower Strength
Hot rolling is advantageous when higher ductility is required, allowing stainless steel to be easily formed into various shapes. However, since hot-rolled stainless steel is produced at elevated temperatures, it tends to have a lower overall strength compared to cold-rolled products. The high temperature allows the grains in the metal to recrystallize and grow, which improves ductility but reduces tensile strength.
Advantages of Hot Rolling:
- Improved ductility and workability.
- Suitable for large-scale production and structural components.
- Lower production costs compared to cold rolling.
- Ideal for producing thicker steel plates and sheets.
Limitations of Hot Rolling:
- Lower tensile strength and hardness.
- Rough surface finish.
- Limited dimensional accuracy.
Cold Rolling: Enhanced Strength and Surface Quality
Cold rolling significantly improves the mechanical properties of stainless steel. The process introduces strain hardening, which increases the material’s tensile strength and hardness. As a result, cold-rolled stainless steel is preferred for applications where high strength and a smooth surface finish are essential.
The increased strength of cold-rolled stainless steel comes from the dislocations created during the rolling process. These dislocations hinder the movement of atoms within the metal structure, making it harder for the material to deform under stress.
Advantages of Cold Rolling:
- Higher tensile strength and hardness due to strain hardening.
- Superior surface finish and dimensional accuracy.
- Greater precision in achieving the desired thickness.
- Enhanced resistance to deformation.
Limitations of Cold Rolling:
- Reduced ductility and workability compared to hot rolling.
- Higher production costs due to additional processing steps.
- Limited to producing thinner sheets and coils.
Rolling of Techniques on Stainless Steel Strength
---Microstructure and Its Role in Strength
The microstructure of stainless steel is closely linked to the rolling technique used. During hot rolling, the metal’s grains recrystallize and grow, resulting in a more uniform grain structure. This enhances the ductility of the material, making it easier to shape and form. However, the larger grain size also contributes to a reduction in tensile strength.
In contrast, cold rolling refines the grain structure of stainless steel. The mechanical deformation caused by cold rolling introduces dislocations and refines the grains, resulting in a higher density of grain boundaries. These refined grains act as barriers to dislocation movement, increasing the material’s strength and hardness.
Grain Size and Strength: The relationship between grain size and strength in stainless steel is governed by the Hall-Petch equation, which states that smaller grain sizes lead to higher strength. Cold rolling promotes finer grain sizes, making it the preferred choice for applications requiring high strength and toughness.
Rolling of Techniques on Stainless Steel Strength
---Applications of Hot Rolled vs. Cold Rolled Stainless Steel
Hot Rolled Stainless Steel Applications:
Hot-rolled stainless steel is commonly used in structural applications, where strength is essential but surface finish and precision are less critical. Typical applications include:
- Construction beams and columns.
- Shipbuilding components.
- Pressure vessels.
- Heavy-duty machinery parts.
Cold Rolled Stainless Steel Applications:
Cold-rolled stainless steel is ideal for applications that require high strength, a smooth surface finish, and precise dimensions. Some of the common applications include:
- Automotive components (e.g., body panels, frames).
- Medical devices and surgical instruments.
- Home appliances (e.g., refrigerators, ovens).
- Aerospace components.
- Decorative architectural elements.
Rolling of Techniques on Stainless Steel Strength
---The Influence of Heat Treatment
In addition to rolling techniques, the heat treatment process plays a significant role in further modifying the mechanical properties of stainless steel. Heat treatment, such as annealing, is often used to relieve internal stresses induced by cold rolling, improve ductility, and enhance corrosion resistance.
Annealing After Cold Rolling: Cold-rolled stainless steel can become brittle and hard due to strain hardening. To restore its ductility, manufacturers often subject the steel to an annealing process, where the material is heated to a specific temperature and then cooled slowly. This treatment allows the grains to recrystallize, enhancing the material’s toughness without sacrificing too much strength.
Conclusion
The rolling technique used in stainless steel production has a profound impact on the final product’s strength, ductility, surface finish, and overall performance. Hot rolling is preferred for applications where ductility and large-scale production are required, while cold rolling is the go-to method for achieving high strength, superior surface quality, and dimensional precision.
Choosing the right rolling technique depends on the specific requirements of the application, whether it’s for structural components, automotive parts, or precision instruments. Understanding the differences between hot rolling and cold rolling allows engineers and manufacturers to make informed decisions, ensuring that the stainless steel used meets the performance demands of the intended use.
In conclusion, both hot rolling and cold rolling offer distinct advantages and limitations. By selecting the appropriate rolling technique and incorporating necessary heat treatments, manufacturers can produce stainless steel products with the desired combination of strength, ductility, and precision for a wide range of applications across industries.
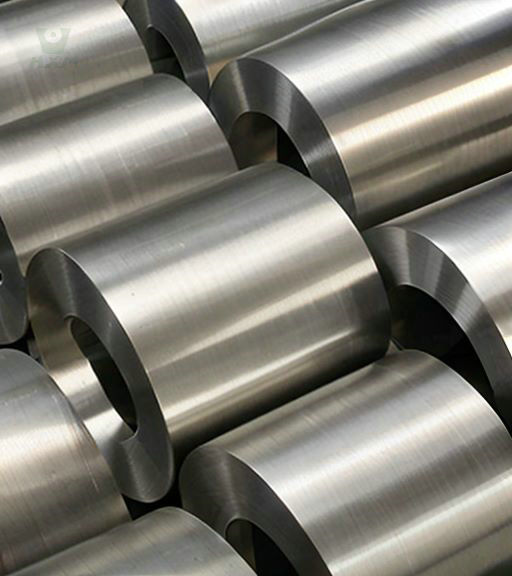
Duplex Steel 2205 Coils: Understanding the Applications and Uses
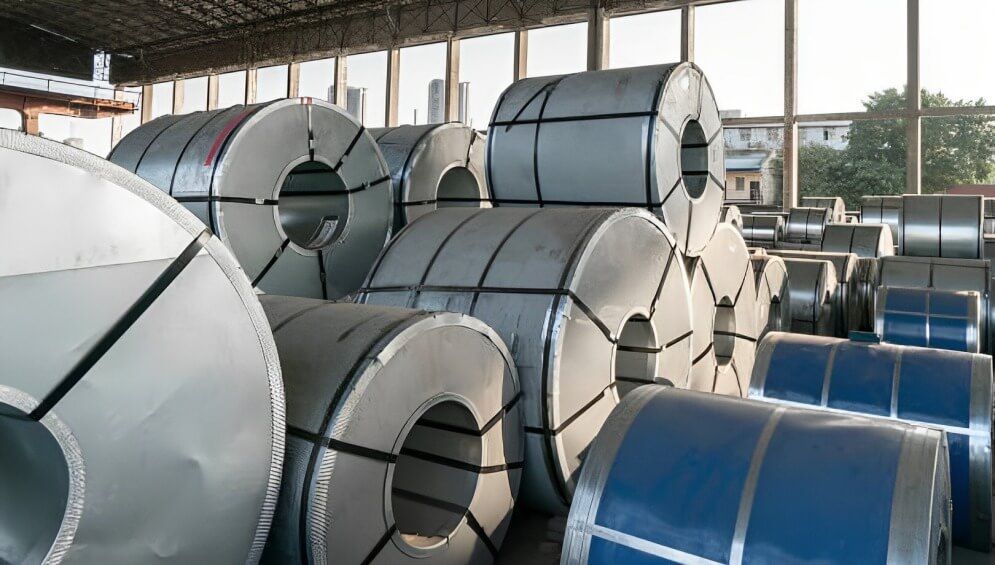
What Are Steel Coils Used For ?
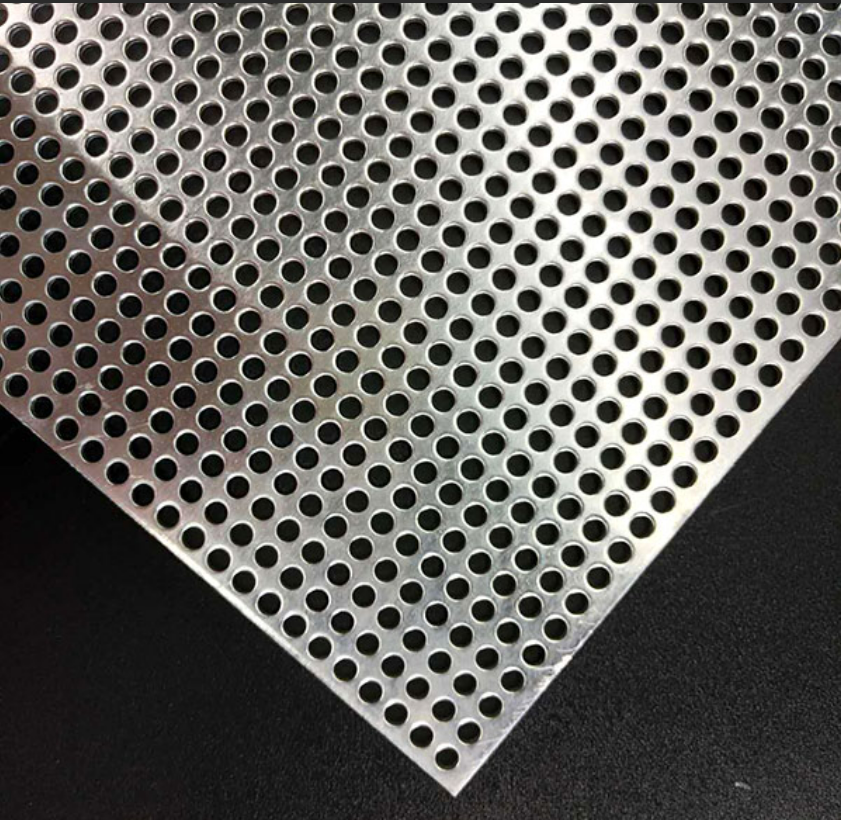
Top 10 Applications of Perforated Metal in Architectural Projects
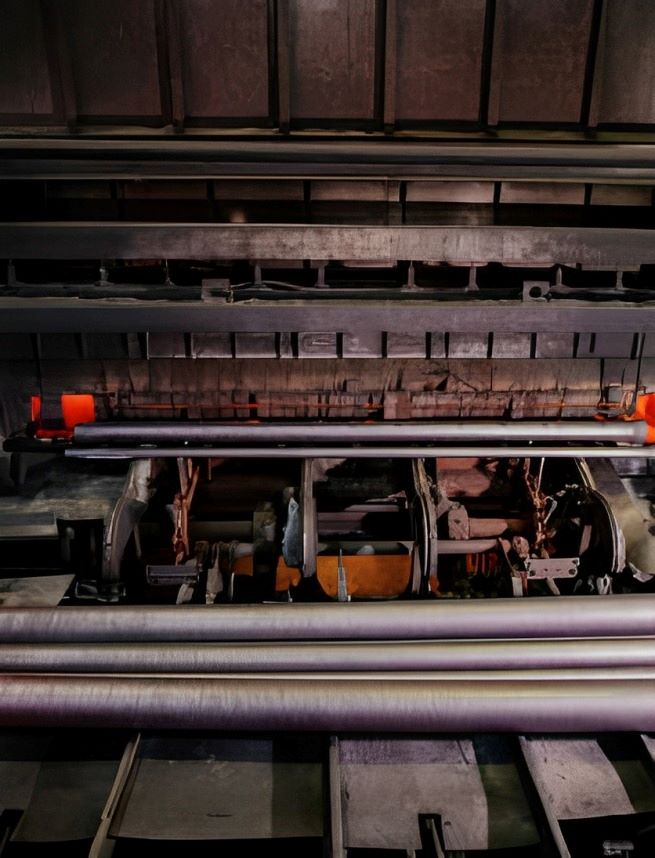
Guide to Stainless Steel Pipe Rolling: Process, Benefits, and Applications
Huaxiao Stainless Steel is Here to Help
Contact us today to learn more about our Stainless Steel Products selection. You can also request a quote to start your order.