How Are Stainless Steel Welded Tubes Made?
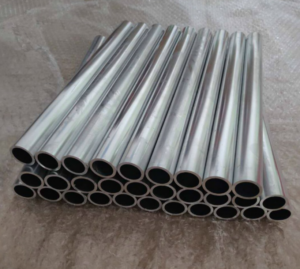
Stainless steel welded tubes are a vital component in various industries, including construction, automotive, and food processing. Understanding how these tubes are made can provide valuable insights into their properties and applications. In this article, we will explore the entire process of manufacturing stainless steel welded tubes, from the selection of raw materials to the final quality inspection.
Selection of Raw Materials for Stainless Steel Welded Tubes
The first step in producing stainless steel welded tubes involves selecting the appropriate raw materials. Stainless steel is known for its corrosion resistance, strength, and aesthetic appeal. Various grades of stainless steel can be used, such as 304, 316, and 430, depending on the intended application.
Manufacturers typically choose high-quality stainless steel sheets or strips as the primary raw material for welding. These materials must meet strict industry standards to ensure optimal performance in the final product. Suppliers of stainless steel sheets play a crucial role in providing manufacturers with reliable materials that meet specifications.
Forming the Stainless Steel Strips into Tubes
After cutting, the stainless steel strips are formed into tubular shapes. This process can be done through various methods, including roll forming and bending.
Roll Forming: In this method, the stainless steel strips are fed through a series of rollers that progressively shape the strip into a tube. This technique is efficient and produces consistent results.
Bending: For certain applications, stainless steel strips may need to be bent at specific angles. This is achieved using specialized bending machines that apply controlled pressure to form the strips into the desired shape.
The formed tubes must be checked for uniformity and consistency before moving to the welding stage. This quality control step ensures that any defects are identified early in the production process.
Welding the Stainless Steel Tubes
The most critical step in making stainless steel welded tubes is the welding process itself. There are several welding methods available, but the most common for tube production are TIG (Tungsten Inert Gas) welding and MIG (Metal Inert Gas) welding.
TIG Welding
TIG welding is known for its precision and ability to produce high-quality welds. In this process, a non-consumable tungsten electrode is used to create an arc that melts the edges of the stainless steel strips. A filler material may be added to strengthen the weld. The key advantage of TIG welding is the control it offers, allowing for clean and aesthetically pleasing welds, which is especially important in applications where appearance matters.
MIG Welding
MIG welding, on the other hand, uses a continuously fed wire as both the electrode and filler material. This method is faster than TIG welding and is suitable for larger production runs. While MIG welding may not achieve the same level of precision as TIG welding, it is often preferred for its speed and efficiency.
Regardless of the method used, maintaining the right temperature and welding speed is crucial to achieving strong, durable welds. Properly welded stainless steel tubes exhibit excellent mechanical properties and corrosion resistance, making them suitable for a wide range of applications.
Post-Welding Treatment
- Improved Corrosion Resistance: By removing oxides and impurities, pickling helps metals retain their resistance to rust and corrosion.
- Enhanced Surface Finish: The process leaves the surface smoother, which is essential for high-quality finishes like painting, galvanizing, or electroplating.
- Preparation for Welding and Coating: Pickling ensures that surfaces are contaminant-free, making it easier for welding and coatings to adhere properly.
Quality Control in Stainless Steel Welded Tube Production
Quality control is a critical aspect of manufacturing stainless steel welded tubes. Throughout the production process, various inspections are performed to ensure that the tubes meet industry standards and specifications.
Manufacturers often adhere to quality management systems such as ISO 9001, which outlines processes and requirements for maintaining consistent quality. Regular audits and checks help identify areas for improvement and ensure that the final products meet customer expectations.
Applications of Stainless Steel Welded Tubes
Stainless steel welded tubes find applications in a diverse range of industries. Their corrosion resistance and strength make them ideal for use in:
- Construction: Used in structural applications, handrails, and architectural features.
- Automotive: Employed in exhaust systems and fuel lines.
- Food and Beverage: Essential for hygienic piping systems in food processing plants.
- Chemical Processing: Used for transporting corrosive substances due to their durability.
These applications highlight the versatility of stainless steel welded tubes and their importance in modern manufacturing.
Conclusion
In conclusion, the production of stainless steel welded tubes is a complex process that involves careful selection of raw materials, precision cutting, and skilled welding techniques. From the initial stages of cutting stainless steel sheets to the final quality inspection, each step plays a crucial role in ensuring the durability and reliability of the finished product. Understanding how stainless steel welded tubes are made can help industries select the right materials for their specific applications and appreciate the value of these essential components.
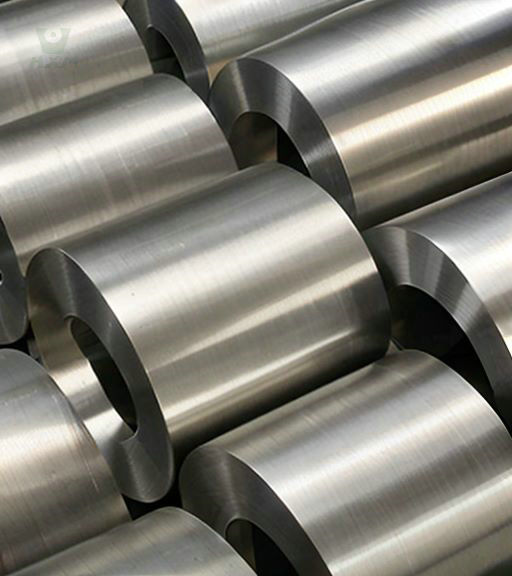
Duplex Steel 2205 Coils: Understanding the Applications and Uses
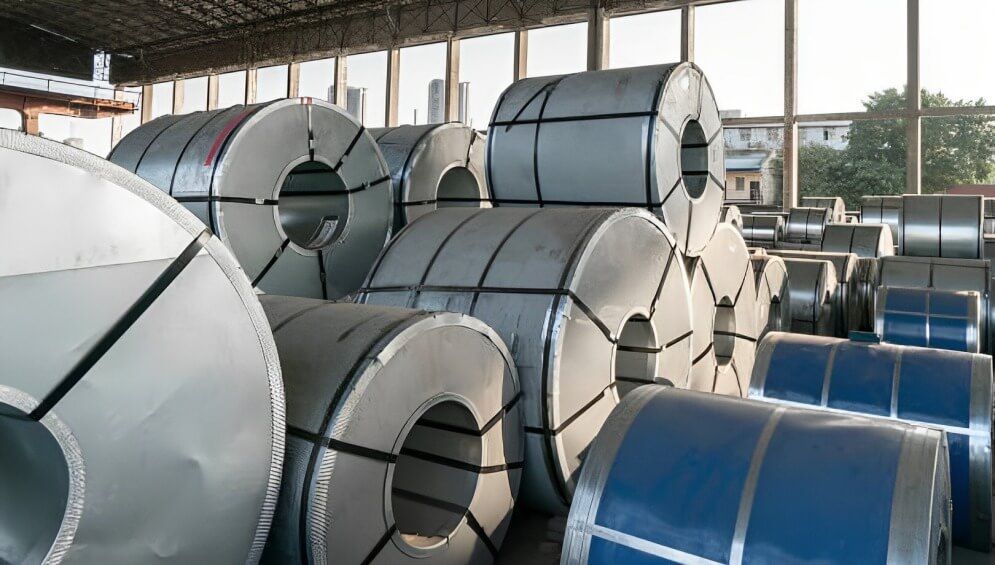
What Are Steel Coils Used For ?
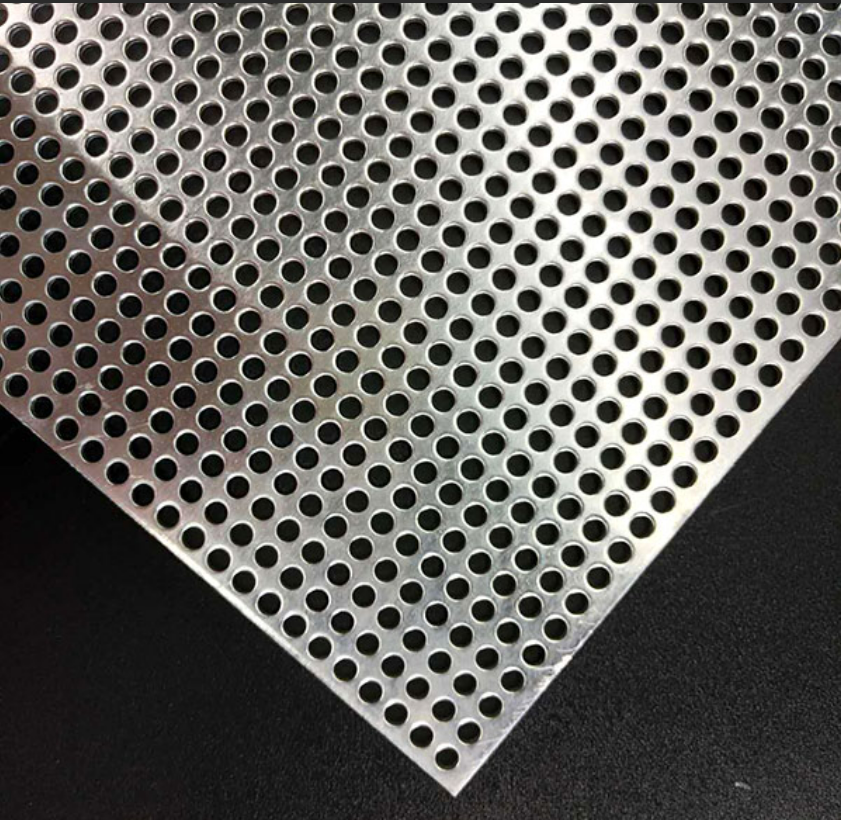
Top 10 Applications of Perforated Metal in Architectural Projects
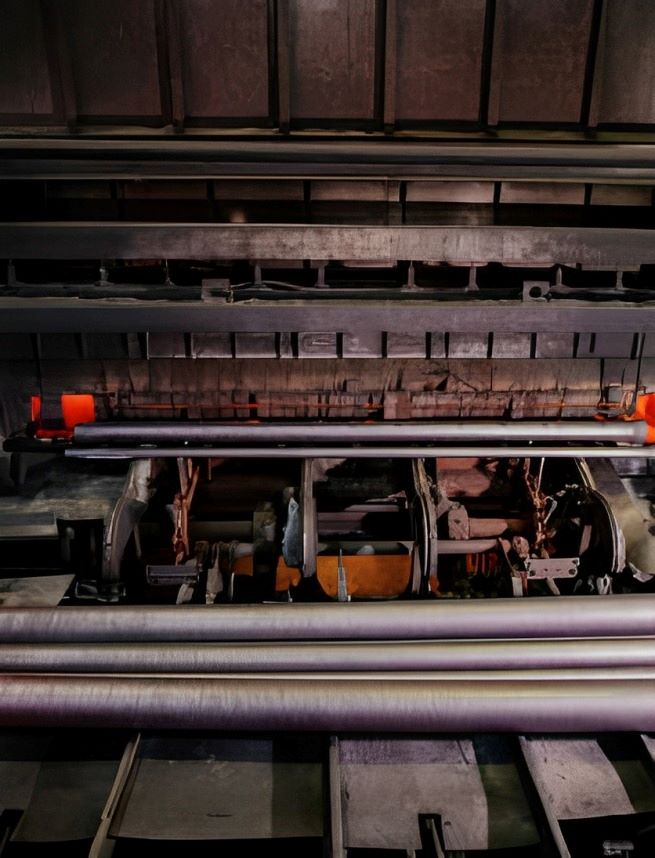
Guide to Stainless Steel Pipe Rolling: Process, Benefits, and Applications
Huaxiao Stainless Steel is Here to Help
Contact us today to learn more about our Stainless Steel Products selection. You can also request a quote to start your order.