What is Metal pickling? Which products need to be pickled and why?
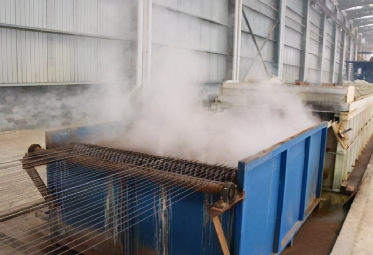
What is Metal Pickling?
Metal pickling is a surface treatment process used to remove impurities such as oxides, rust, scale, and other contaminants from metal surfaces. The process involves immersing the metal in an acid solution, which dissolves the unwanted layers, leaving behind a clean and smooth surface. Common acids used for pickling include hydrochloric acid, sulfuric acid, and nitric acid. The purpose of pickling is to prepare the metal for further processing, such as welding, coating, or painting, by ensuring a contaminant-free surface.
The Purpose of Metal Pickling
The primary purpose of metal pickling is to remove surface impurities such as oxides, rust, scale, and other contaminants that accumulate during manufacturing processes like hot rolling, forging, or welding. This cleaning process is essential to ensure that the metal is ready for further treatments, such as coating, painting, welding, or anodizing.
Key reasons for pickling include:
Restoring Corrosion Resistance:
Metals like stainless steel lose their protective chromium oxide layer due to heat or chemical exposure. Pickling restores this layer, improving the material’s resistance to corrosion.Enhancing Surface Quality:
By removing contaminants, pickling ensures a smoother, cleaner surface. This is crucial for applications where a high-quality finish is needed, such as painting, electroplating, or anodizing.Preventing Future Corrosion:
Leftover scale and oxides can act as sites for corrosion to develop. Pickling eliminates these residues, reducing the risk of future rust or corrosion, especially in critical industries like oil and gas, construction, or chemical processing.Preparing for Welding or Coating:
Clean, contaminant-free surfaces are essential for successful welding or coating adhesion. Pickling ensures that metals are in the ideal condition for these processes, improving the overall quality and durability of the finished product.
Which Products Need to Be Pickled and Why?
Stainless Steel
Why: During manufacturing processes like heat treatment or welding, stainless steel often develops a layer of oxide scale. Pickling removes this scale, restoring the material’s corrosion resistance and ensuring a clean surface for subsequent finishing processes.Carbon Steel
Why: Carbon steel typically undergoes pickling to remove rust, scale, and other contaminants formed during hot rolling or welding. This ensures the surface is smooth and clean, making it ideal for further applications such as painting or galvanizing.Aluminum
Why: Although not as commonly pickled as steel, aluminum surfaces can also develop oxides or impurities during manufacturing. Pickling helps remove these contaminants, especially before anodizing or applying surface coatings.Copper and Brass
Why: Copper and brass products are pickled to eliminate oxidation and tarnish formed during fabrication. Pickling improves conductivity for electrical components and enhances the appearance of decorative items.Piping and Tubing
Why: Pickling is crucial for pipes and tubes, especially those used in industries such as oil & gas or chemical processing. It removes residues from manufacturing and restores corrosion resistance, extending the life of these components in harsh environments.
When is it Necessary to Pickle Metal?
Metal pickling is necessary in specific scenarios where surface contaminants or scale must be removed to improve the performance, appearance, or preparation of the metal for further processing. Here are the key situations where pickling becomes essential:
After Hot Working Processes
Why: Metals like steel and stainless steel often undergo hot rolling, forging, or heat treatment, during which a layer of oxide scale forms on the surface. Pickling is necessary to remove this scale, restoring the metal’s clean surface and original properties.Before Welding
Why: Contaminants such as rust, dirt, or oxides on metal surfaces can interfere with the welding process. Pickling cleans the metal, ensuring stronger welds and preventing impurities from compromising the weld quality.Before Coating or Painting
Why: Coatings, paints, and finishes adhere poorly to dirty or contaminated surfaces. Pickling cleans the metal, creating an ideal surface for optimal adhesion and ensuring a smooth, uniform finish that lasts longer.For Corrosion Resistance Restoration
Why: Stainless steel loses its chromium oxide protective layer during fabrication processes such as heat treatment or welding, which reduces its corrosion resistance. Pickling removes contaminants and helps restore the material’s corrosion-resistant properties.In High-Corrosion Environments
Why: Metals used in aggressive environments (e.g., marine, chemical, or industrial) need to be free of surface defects like rust or scale that can accelerate corrosion. Pickling is necessary to remove these impurities and extend the metal’s lifespan.Pipe and Tubing Manufacturing
Why: In the production of pipes and tubes, especially for the oil & gas or chemical industries, internal and external surfaces can become contaminated with oxides and residues. Pickling cleans these surfaces, preventing potential blockages and ensuring smooth operation in service.When Preparing for Anodizing or Electroplating
Why: For processes like anodizing aluminum or electroplating metals, a clean and smooth surface is critical for achieving a uniform and high-quality finish. Pickling is necessary to remove all impurities and enhance the final result.For Refurbishment of Metal Components
Why: Used metal parts, particularly in industrial settings, can accumulate rust, scale, or other corrosive materials over time. Pickling is necessary to clean and restore these components to a usable condition.
Benefits of Metal Pickling
- Improved Corrosion Resistance: By removing oxides and impurities, pickling helps metals retain their resistance to rust and corrosion.
- Enhanced Surface Finish: The process leaves the surface smoother, which is essential for high-quality finishes like painting, galvanizing, or electroplating.
- Preparation for Welding and Coating: Pickling ensures that surfaces are contaminant-free, making it easier for welding and coatings to adhere properly.
Precautions for Metal Pickling
Use Proper Personal Protective Equipment (PPE):
Workers should wear appropriate PPE, including acid-resistant gloves, safety goggles, face shields, aprons, and protective footwear, to prevent contact with the acids used in pickling.Ensure Adequate Ventilation:
Acid fumes, particularly from hydrochloric, sulfuric, or nitric acids, can be harmful if inhaled. Pickling areas must be well-ventilated to disperse fumes and prevent respiratory issues. Use fume extraction systems when necessary.Handle Acids with Care:
Acids used in pickling are highly corrosive. Always follow safe handling procedures, such as adding acid to water (never water to acid) when diluting, to prevent dangerous reactions like splashing or boiling over.Monitor Acid Concentration:
The concentration of the pickling solution must be carefully controlled. Overly concentrated acids can damage the metal surface, while insufficient concentration may lead to incomplete pickling. Regular monitoring is essential to maintain the correct balance.Proper Waste Disposal:
Pickling generates hazardous waste, including spent acids and dissolved metal ions. These substances must be disposed of in accordance with environmental regulations to prevent soil and water contamination. Neutralizing acid waste before disposal is critical.Use Acid-Resistant Equipment and Containers:
Ensure that all tanks, containers, and tools used in the pickling process are made from acid-resistant materials, such as plastic or specially coated metals, to prevent corrosion and accidental leaks.Avoid Over-Pickling:
Prolonged exposure to pickling solutions can lead to metal degradation, pitting, or excessive material loss. Follow recommended times for different metals to prevent damage to the material.Neutralize and Rinse Thoroughly:
After pickling, the metal should be thoroughly rinsed with water to remove all acid residues. Failure to properly neutralize and clean the metal can result in residual acid causing ongoing corrosion or damage.Train Employees Properly:
Workers involved in the pickling process should be trained in handling acids safely, recognizing hazards, and using emergency equipment like eye wash stations and chemical spill kits.Store Acids Safely:
Acids must be stored in secure, labeled containers away from incompatible materials (e.g., bases or reactive metals) in cool, dry environments to minimize the risk of spills, leaks, or hazardous reactions.
In summary, metal pickling is a vital step for maintaining the durability, performance, and aesthetics of metal products, especially in demanding industrial environments.
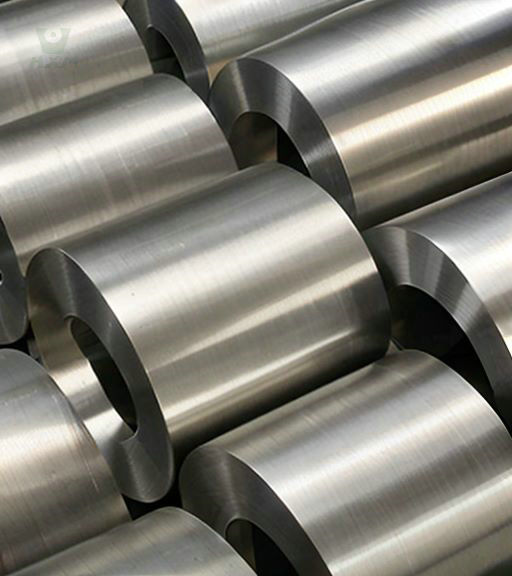
Duplex Steel 2205 Coils: Understanding the Applications and Uses
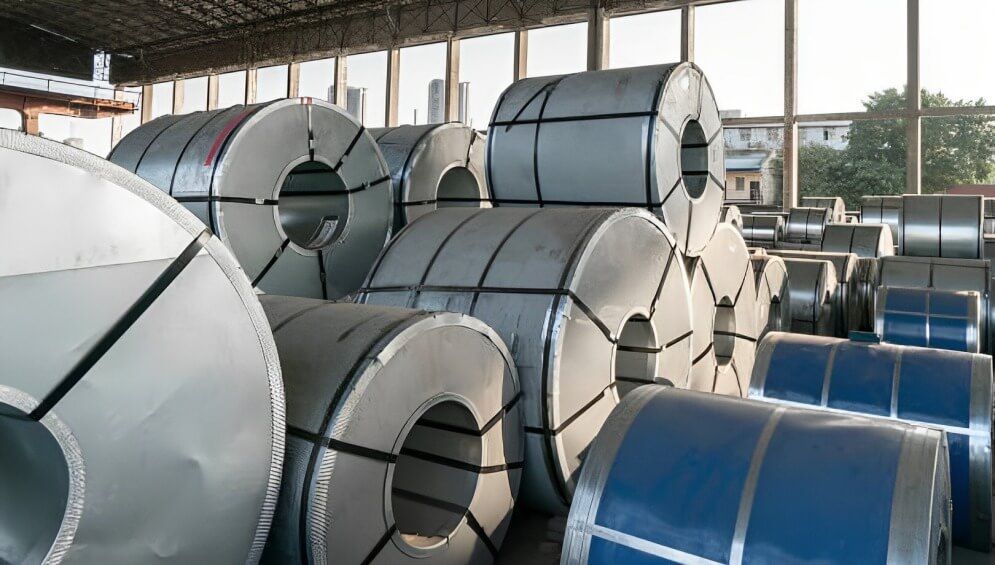
What Are Steel Coils Used For ?
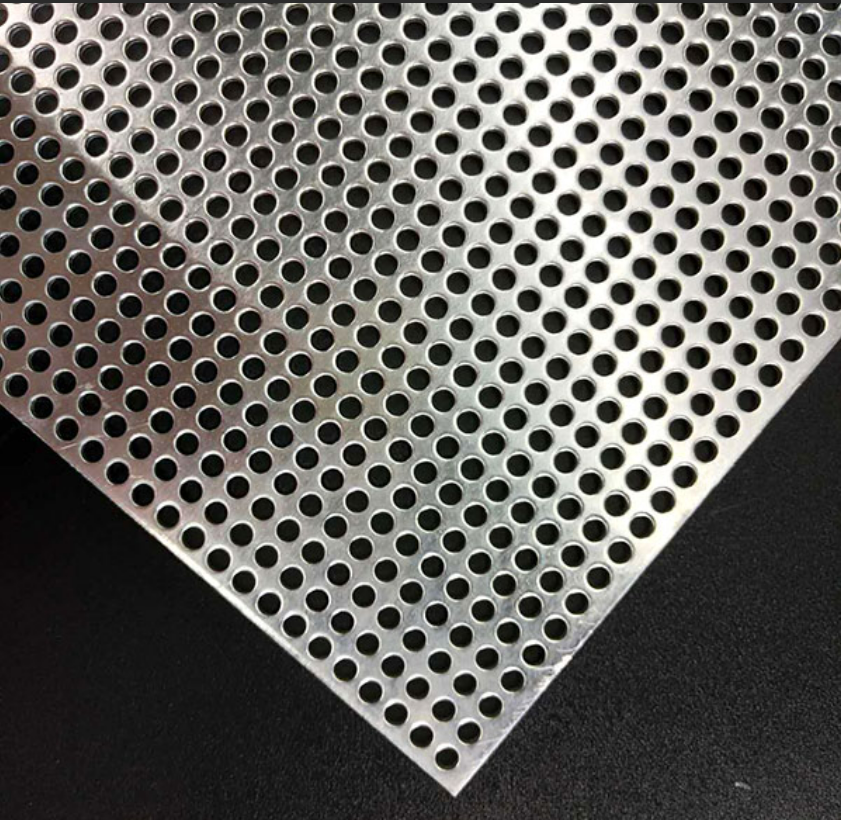
Top 10 Applications of Perforated Metal in Architectural Projects
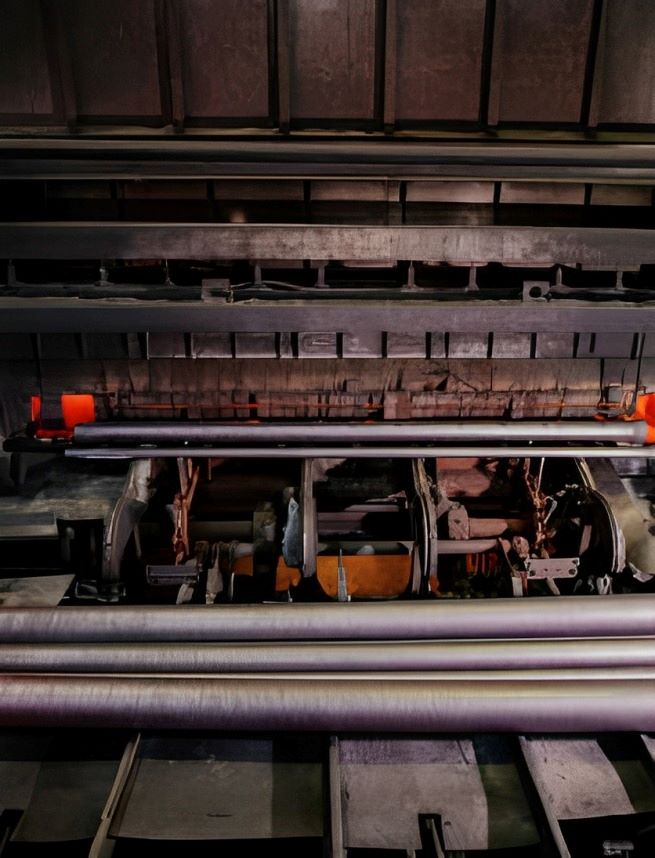
Guide to Stainless Steel Pipe Rolling: Process, Benefits, and Applications
Huaxiao Stainless Steel is Here to Help
Contact us today to learn more about our Stainless Steel Products selection. You can also request a quote to start your order.