Can Stainless Steel
Be Colored?
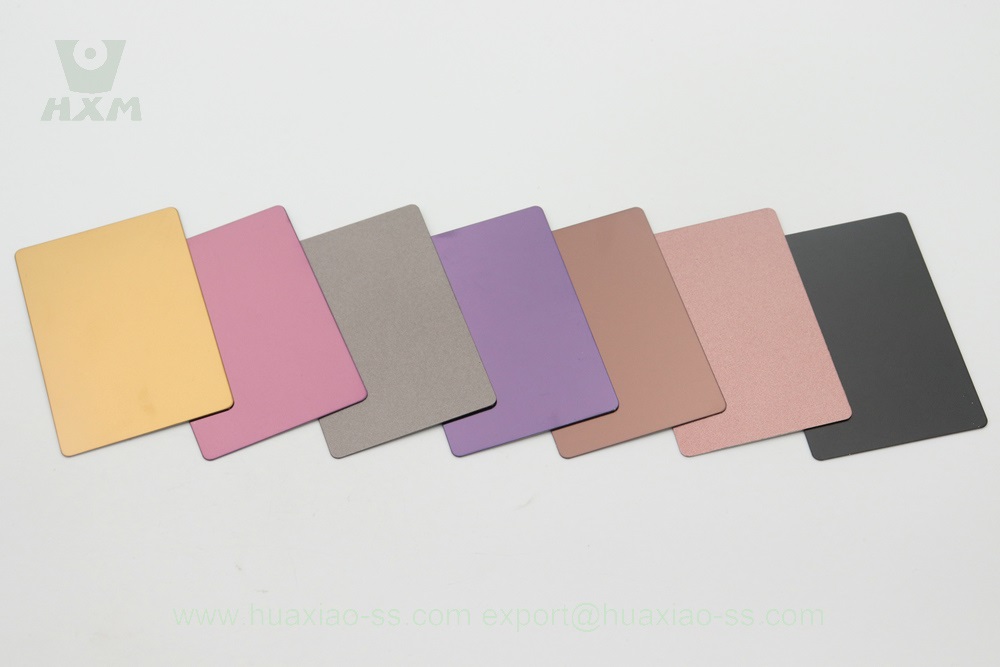
Stainless steel is beloved for its excellent corrosion resistance, high strength, and attractive appearance. However, during its application, people often find its monotonous color to be a concern, leading to frequent questions about whether stainless steel can be colored. So, can stainless steel really be colored? What scientific principles and technological methods lie behind this question?
Methods of stainless steel colouring
Stainless steel surface coloring treatment involves forming a thin layer of film on the surface of stainless steel with chemical corrosion resistance. There are many methods for stainless steel surface coloring treatment, and the process and color changes vary for each method. Among them, the most famous is the electrochemical coloring method, which is known for its simple operation, low raw material cost, and the advantage of producing rich, vibrant, and three-dimensional colors.
The commonly used methods for stainless steel surface coloring treatment include the following:
Organic Coating Method
The organic coating method is a technique for coloring stainless steel, involving a series of pretreatments of the stainless steel surface followed by the application of organic coatings, and then baking to form a colored coating. This method offers a wide range of color options for stainless steel and enhances its decorative and aesthetic appeal.
Specifically, the steps involved in the organic coating method are as follows:
Pretreatment: Before the coating process begins, the stainless steel surface needs to undergo cleaning, degreasing, rust removal, and deoxidation to ensure a clean and impurity-free surface for the subsequent coating work.
Primer Coating: To enhance the adhesion of the coating and protect the substrate, a primer coating is applied first. The primer typically contains resin, pigments, diluents, etc., and can be applied by brushing, spraying, or dipping. After application, the primer needs to be dried and cured.
Grinding and Polishing: After the primer has dried and cured, the surface undergoes grinding and polishing to achieve a smoother and more even surface. This step helps to remove surface irregularities and defects on the primer, ensuring a more uniform coating.
Topcoat Coating: On top of the primer, an organic topcoat is applied. The topcoat is usually transparent or colored and can be selected according to specific color and effect requirements. During application, attention should be paid to the uniformity and thickness of the coating.
Baking/Curing: After the coating is applied, it needs to be baked or cured by other means to ensure the coating is durable and robust. Baking conditions can be adjusted according to the requirements of the coating material, typically carried out at appropriate time and temperature settings.
It is important to note that while the organic coating method can achieve coloration of stainless steel, the process is relatively complex and requires strict control of each step to ensure the quality and stability of the coating. Additionally, the organic coatings selected should comply with relevant environmental standards to avoid environmental pollution.
Gas Phase Decomposition Method
The application of the gas-phase decomposition method in stainless steel coloring is indeed a relatively specialized and complex process. This method primarily involves the instantaneous thermal decomposition of high-molecular-weight and less volatile organic compounds into volatile small molecules through heat energy, followed by specific reactions and processes to achieve stainless steel coloring.
Specifically, the gas-phase decomposition method involves placing stainless steel in a specific decomposition environment and controlling temperature, pressure, and other conditions to induce the decomposition reaction of certain components on the stainless steel surface. These decomposition products then react with oxygen or other gases in the air, generating oxides or compounds with specific colors, thereby achieving stainless steel coloring.
However, it is important to note that the application of the gas-phase decomposition method in stainless steel coloring is not common. This is mainly because the process is relatively complex and requires precise process control and professional equipment support. Additionally, the stability and durability of the coloring effect using the gas-phase decomposition method may be affected by factors such as temperature fluctuations and changes in gas composition.
Ion Deposition Method
Ion deposition is a surface treatment technology that primarily utilizes high-energy ion beams to assist in the deposition of substances to form coatings. The working principle of this method is based on generating ion beams using a plasma source and controlling the energy and flux of the ion beams to interact with the substrate to form a uniform and dense coating on its surface.
During the ion deposition process, high-energy ion beams need to be generated first. This is typically achieved through methods such as radio frequency or direct current arc discharge, which accelerate the ion beams in the plasma to high energy levels before guiding them to the surface of the substrate to be coated. When the ion beams interact with the substrate surface, a series of physical and chemical reactions occur, depositing the coating material onto the substrate and forming a uniform and dense coating.
Ion deposition offers several advantages. For instance, it can provide highly dense thin films, enhancing the material’s performance, and allows coating at lower substrate temperatures, enabling the deposition of materials with lower melting points (such as polymers). Additionally, by using auxiliary ion sources, ion deposition can pre-clean the substrate to reduce contamination and allow for ion etching. From a cost perspective, ion deposition offers several cost advantages, including high throughput, extended normal operating times, and lower maintenance costs.
Chemical Coloring Method
Stainless Steel Chemical Coloring Method: It involves immersing stainless steel in a specific solution, where a color film forms due to chemical reactions. Methods include chromate conversion coating, sulfide treatment, acidic oxidation, and alkaline oxidation. The most commonly used method is acidic coloring, known for its easy color control and formation of highly wear-resistant films, suitable for mass production.
After stainless steel undergoes coloring treatment, depending on the thickness of the film, it can change to various colors such as blue, gold, green, red, light brown, light blue, dark blue, and brown. After coloring treatment, stainless steel surfaces require additional steps for film hardening and sealing.
The process involves: Stainless Steel Products → Mechanical Polishing → Cleaning → Alkaline Degreasing → Cleaning → Electrolytic Polishing → Cleaning → Activation → Cleaning → Chemical Coloring → Curing of Coloring Film → Cleaning → Sealing → Cleaning → Drying → Finished Product.
Electrochemical coloring
Electrochemical coloring is a technique used to form colored oxide films on the surface of materials in a specific solution through electrochemical oxidation.
The process involves: pre-treatment → rinsing → coloring → treatment → rinsing → hard film treatment → rinsing → drying → finished product.
The color variations are: black → blue → gold → red → green.
It is important to note that after stainless steel is colored using the electrochemical coloring method, cathodic sealing treatment is usually required to ensure color stability and durability. This step helps to strengthen the bond between the oxide film and the metal substrate, improving the weather resistance and abrasion resistance of the coloring layer. Additionally, hardening treatment is recommended to further enhance the hardness and corrosion resistance of the oxide film.
Electrochemical coloring offers advantages such as easy application and uniform coating, but it may have issues with weather resistance and color deviation. Therefore, in practical applications, appropriate process parameters and operating conditions should be selected based on specific requirements and conditions to achieve the best coloring effect.
High-temperature oxidation coloring
High-temperature oxidation coloring is a surface treatment technique that involves heating the workpiece in a specific molten salt environment to form a layer of oxide film with a specific color on its surface. This method mainly utilizes the chemical reaction between the workpiece and the oxidant in the molten salt at high temperatures to generate an oxide film on the surface of the workpiece.
The operational process of high-temperature oxidation coloring is as follows:
Preparation: Firstly, an appropriate molten salt is selected and heated to the molten state. Meanwhile, the workpiece to be treated needs to be cleaned and pre-treated to ensure its surface is clean and free of impurities.
Immersion of workpiece: The pre-treated workpiece is immersed in the molten salt, ensuring that it is completely covered by the molten salt. At this stage, certain process parameters such as temperature and time need to be controlled to ensure the quality and color effect of the oxide film formation.
Formation of oxide film: Under high temperature and specific process parameters, a chemical reaction occurs between the surface of the workpiece and the oxidant in the molten salt, gradually forming a layer of oxide film. This oxide film not only has a certain thickness but also presents a specific color.
Removal and cooling: After the oxide film is formed, the workpiece is removed from the molten salt and appropriately cooled. Care should be taken to avoid contamination or damage to the workpiece surface during the cooling process.
Subsequent treatment: Depending on the requirements, the workpiece can undergo further cleaning, polishing, etc., to improve its appearance and performance.
The workpiece treated by high-temperature oxidation coloring will have a hard, wear-resistant, and corrosion-resistant oxide film on its surface, while presenting a rich and colorful appearance. This method is widely used in the surface treatment of metal materials such as stainless steel and aluminum alloys, not only improving the decorative properties of the materials but also enhancing their durability.
Conclusion
Through a series of advanced surface treatment technologies such as electrolytic coloring, gas-phase decomposition, ion deposition, and chemical coloring, stainless steel not only obtains a wide range of colors but also enhances its decorative and aesthetic appeal while maintaining its excellent performance. Each of these coloring methods has its own characteristics, allowing for the selection of the most suitable coloring scheme based on different needs and scenarios.
As an outstanding stainless steel supplier in China, Huaxiao Metal has exported stainless steel products for over 15 years, reaching customers in countries and regions including Australia, North America, Central Europe, and Southeast Asia, garnering unanimous praise. With high-quality products and professional services, we are committed to providing customers with an excellent shopping experience. If you have any purchasing needs for stainless steel products, feel free to inquire anytime, and we will be dedicated to serving you.