how to passivate stainless steel?
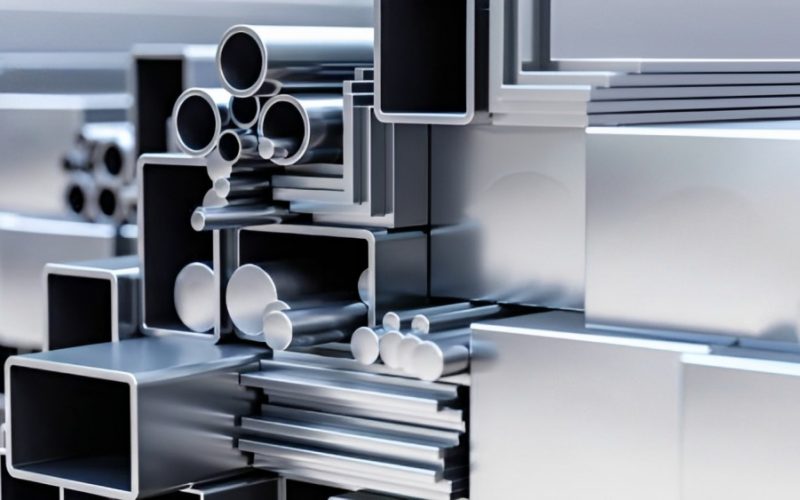
Stainless steel is widely used in daily life and industrial production due to its excellent corrosion resistance and beautiful appearance. However, in order to further improve the corrosion resistance of stainless steel, passivation is usually required. Stainless steel passivation is a process of forming a protective film on the surface of stainless steel through a chemical reaction, which can effectively enhance the corrosion resistance of stainless steel. In this blog, we will introduce the methods, advantages, and precautions of stainless steel passivation in detail to help you better understand this process.
What is passivation of stainless steel?
Passivation of stainless steel is a process of forming a dense oxide film on the surface of stainless steel by chemical methods to improve the corrosion resistance of stainless steel. After the passivation treatment of stainless steel, the metal elements on its surface react chemically with the passivator to produce a stable oxide film, which effectively prevents further erosion of the stainless steel substrate by air, moisture, and harmful substances.
The main purpose of passivation treatment is to remove oxides and contaminants on the surface of stainless steel, and then react with the metal surface to form a uniform, dense oxide layer. The thickness of this oxide film is usually between 1~5 microns, which has high corrosion resistance, electrical resistance, and mechanical strength.
Passivation of stainless steel usually uses a variety of methods and passivation, such as nitric acid, copper nitrate, sulfuric acid, and so on. Under specific environmental conditions, these passivators react chemically with the metal elements on the surface of stainless steel to produce a passivation film. This treatment not only improves the corrosion resistance of stainless steel but also enhances its anti-pollution properties and extends its service life.
In general, the passivation treatment of stainless steel is an effective rust prevention process that can significantly improve the rust resistance and service life of stainless steel products.
how to passivate stainless steel?
Acid washing prior to passivation removes all contaminants and selectively removes smaller corrosion-resistant areas of the metal surface.
For effective acid washing and passivation, all organic contaminants, oils and greases must be removed prior to acid washing and passivation.
Therefore, the common operating procedures are as follows:
A. Pre-cleaning / degreasing
B. Primary cleaning
C. Acid washing
D. Second cleaning
E. Passivation / Degreasing
F. Final Cleaning and Drying
Pre-cleaning and Degreasing
To ensure effective acid cleaning and passivation, it is necessary to remove all organic contaminants, such as grease and other debris, from the metal surface. Organic contaminants will prevent acid cleaning and passivation and have the potential to cause pitting corrosion.
Pre-cleaners are sprayed on the metal surface for cleaning and degreasing, and must be cleaned off with a high-pressure water jet to improve the quality of the after-treatment.
The effectiveness of the pre-cleaning can be checked by means of a water film.
Acid washing and passivation in bath solution
1.Immerse each block in the following solution.
- Nitric acid 36℃——100L
- 65% Oxyfluoric acid ——20 L or Sodium fluoride ——20kg
- Water —— 900 L
The soaking time is ten minutes at 60°C and two hours at room temperature.
2. After soaking, rinse quickly with water until the pH value of the wash-out solution is equal to the pH value of the rinse water.
Each piece should be re-immersed in another solution as follows
- Nitric acid 36°C ——250L
- Water——750L
Soaking time: 15 minutes at 50°C and 2 hours at room temperature.
3. After soaking, rinse quickly with water until the pH value of the effluent is equal to the pH value of the rinse water.
Plating treatment
Acid baths and colloids for spray plating consist mainly of nitric acid (20-25%) and hydrofluoric acid (about 5%) doped with binder and surfactants to form a solution of suitable consistency and thixotropic properties.
The composition of the passivate and colloid for spray plating is similar to that of an acid-wash spray plating solution, except that it does not contain oxyfluoric acid.
The procedure is as follows:
1. Acid Wash
- After careful pre-cleaning and degreasing, a uniform coat of acid cleaner should be sprayed onto the dry metal surface with acid-resistant equipment.
- Allow the acid cleaner to act for a period of time under the direction of the stainless steel manufacturer. If necessary, heavily colored welds and heat-sensitive areas should then be carefully swabbed with a stainless steel brush to remove any discoloration.
- Rinse carefully with a high-pressure water gun and check that no residue remains on the metal surface.
2. Passivation
- After acidizing and immediate cleaning, a uniform layer of passivation should be sprayed onto the dry metal surface with acid-resistant equipment.
- Allow the acid cleaner to act for a period of time under the direction of the stainless steel manufacturer. If necessary, remove all discoloration from heavily colored welds and heat-sensitive areas by carefully swabbing with a stainless steel brush.
- Rinse carefully with a high-pressure water gun check that no residue remains on the metal surface and keep the surface dry.
When to Passivate Stainless Steel
Post-Manufacturing: After fabrication processes like machining, welding, grinding, or forming, stainless steel is often exposed to contaminants, including iron particles and other surface debris. These foreign materials can interfere with the natural protective layer of the steel, making it prone to rust. Passivation helps remove these contaminants and restores the material’s corrosion resistance.
After Surface Contamination: In industrial environments where stainless steel may come in contact with carbon steel or other contaminants, passivation is required to remove any foreign particles that may lead to rust or corrosion.
Before Use in Aggressive Environments: Stainless steel components that will be used in highly corrosive environments, such as marine or chemical processing applications, benefit from passivation. It enhances the material’s natural oxide layer, providing added protection against corrosion.
After Heat Treatment: When stainless steel undergoes heat treatments such as annealing, there can be oxidation or scale formation on the surface. Passivation helps clean the surface and restore the material’s resistance to rust.
Before Sterilization in Medical or Pharmaceutical Settings: Medical and pharmaceutical applications require stainless steel to be free of contaminants and have optimal corrosion resistance to prevent contamination. Passivation ensures that the stainless steel is clean and safe for sterile environments.
When Corrosion is Detected: Even though stainless steel is corrosion-resistant, occasional surface corrosion (such as tea staining or rust spots) can still occur, especially if the material is exposed to harsh conditions. Passivation can help to mitigate these issues by re-establishing the passive layer.
Before Painting or Coating: If stainless steel components are to be painted or coated, passivation beforehand helps in ensuring that the surface is free from any oils, residues, or contaminants, allowing better adhesion of the paint or coating.
Precautionary Measures
- All products are acidic and hazardous and all operators should wear masks, goggles, rubber gloves, aprons, and boots.
- The entire process must be kept sufficiently clean and well-ventilated. Potassium ferroammonium is a simple cyanide and is not toxic, but it releases toxic cyanide gas when it decomposes with heat or comes into contact with concentrated acids.
- If the air is contaminated by dust, carbon steel, grease, and organic particles, the effect of cleaning, acid washing, and passivation will be ineffective.
- In all cases, the stainless steel manufacturer’s instructions should be followed.
Conclusion
We understand the application scope of different formulations and treatment solutions through the introduction of stainless steel pickling passivation treatment solution formulations. In practice, the correct choice and treatment solution are essential to improve the corrosion resistance and extend the service life of stainless steel. When pickling passivation treatment, please follow the safety operation procedures to ensure personnel safety and environmental protection.
Huaxiao Stainless Steel specializes in providing high-quality stainless steel products, and our products can be customized to meet the specific needs of our customers. Whether you need stainless steel products in different finishes, sizes, or shapes, Huaxiao Metal can meet your needs. With our professional team and advanced production equipment, we can provide personalized solutions according to the characteristics of your industry to ensure that the products meet your requirements.
Table of Contents
Maybe You Reads