How to Weld Stainless Steel?
Stainless steel, with its distinct alloy composition, demands a specialized approach to welding. The gleam of this metal belies its intricacies, and a successful weld requires more than just technical skill—it necessitates an understanding of the material’s behavior under heat and the art of preserving its corrosion-resistant properties.
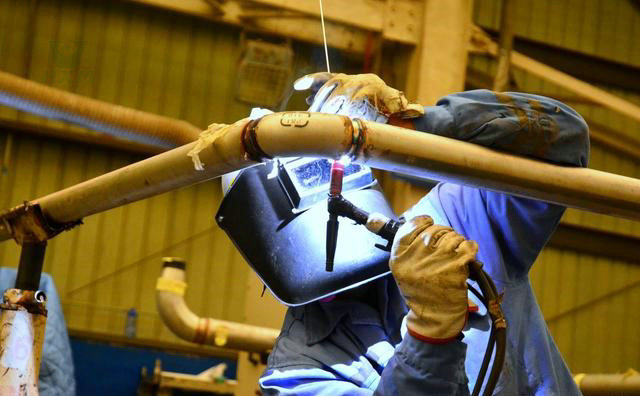
Table of Contents
Three Methods to Weld Stainless Steel
Fusion Welding
- Definition: Fusion welding is a method of welding stainless steel by heating the interface of the workpieces to a molten state and completing the welding without applying pressure.
- Process: During fusion welding, a heat source (such as an arc or flame) rapidly heats the interface of the two workpieces to create a molten pool. The molten pool advances as the heat source moves, and upon cooling, the melted metal solidifies to form a continuous weld seam, thus connecting the two workpieces together.
- Challenges: During fusion welding, the molten pool comes into direct contact with the atmosphere, which may cause the oxidation of metal and alloy elements, as well as the introduction of impurities such as nitrogen and water vapor into the molten pool. These impurities may form defects such as porosity, slag inclusion, and cracks during the cooling process, thus affecting the quality and performance of the weld seam.
Pressure Welding
- Definition: Pressure welding, also known as solid-state welding, is a welding method where two workpieces are bonded together in a solid state under pressure.
- Process: In pressure welding, techniques such as resistance spot welding are commonly used. When current passes through the connection point of the two workpieces, a large amount of heat is generated due to the high resistance, heating the interface to a plastic state. Subsequently, under axial pressure, the two workpieces are bonded together in the solid state.
- Features: Pressure welding applies pressure during the welding process without using filler material. Since most pressure welding methods do not involve melting, they avoid the burning loss of beneficial alloy elements and the intrusion of harmful elements into the weld seam. Additionally, the low heating temperature and short heating time of pressure welding result in a smaller heat-affected zone. This makes pressure welding an effective method for welding stainless steel materials where fusion welding is difficult, allowing for high-quality joints with strength equivalent to the base material.
Brazing
- Definition: Brazing is a welding method that uses a metal material with a lower melting point than the workpieces, known as brazing filler metal, to heat the workpieces and filler metal to a temperature higher than the melting point of the filler metal but lower than that of the workpieces, allowing the liquid brazing filler metal to wet the workpieces and fill the interface gap, achieving welding through interatomic diffusion.
- Process: In brazing, the brazing filler metal is heated to a molten state while the workpieces remain solid. The liquid brazing filler metal fills the gaps between the workpieces through capillary action and undergoes interatomic diffusion with the workpiece surfaces to form a strong joint.
- Applications: Brazing is suitable for joining different stainless steel materials, especially when there is a significant difference in the melting points of the two materials. Since brazing temperatures are relatively low and have minimal impact on the workpieces, it is commonly used in the welding of precision instruments, electronic components, and thin-walled structures.
Types of Techniques to weld stainless steel
Gas Tungsten Arc Welding (GTAW)
- Widely used, particularly suitable for welding stainless steel with thicknesses ranging from 0.5 to 3mm.
- Offers excellent protection, with minimal alloy element burning, and produces aesthetically pleasing weld seams without slag.
- Manual tungsten inert gas (TIG) welding is commonly used for thin plate welding, while consumable electrode TIG welding is more suitable for stainless steel components thicker than 3mm.
- Consumable electrode TIG welding offers advantages such as high productivity, minimal heat-affected zone, low distortion, and excellent corrosion resistance.
Gas Welding
- Gas weld stainless steel is flexible and convenient, suitable for welding seams in various spatial positions.
- It is a viable choice for thin plate structures and thin-wall pipes of stainless steel where corrosion resistance is not a requirement.
- Care should be taken to control flame type, torch angle, and welding speed to avoid overheating and ensure weld seam quality.
Submerged Arc Welding (SAW)
- Suitable for welding stainless steel plates with medium thicknesses (6-50mm).
- Offers high productivity and good weld seam quality but requires attention to alloy element segregation and impurity issues.
Manual Welding
- Manual welding is a widely used and user-friendly welding method.
- The arc length can be adjusted manually, making it suitable for various materials.
- The welding electrode serves as both the arc carrier and the filler material.
- Manual welding also demonstrates good adaptability in outdoor and underwater environments.
Metal Inert Gas/Metal Active Gas (MIG/MAG) Welding
- This is an automatic gas-shielded arc welding method.
- The arc burns between the metal wire and the workpiece under the shield of protective gas.
- It is suitable for steel, non-alloy steel, low-alloy steel, and materials based on high-alloy steel.
- MIG/MAG welding offers the advantages of versatility and specificity, making it a widely used welding method.
Tungsten Inert Gas (TIG) Welding
- The arc is generated between the tungsten electrode and the workpiece, using pure argon gas as the shielding gas.
- The welding wire is not electrically charged and can be manually or mechanically fed.
- TIG welding possesses deep penetration capabilities and is suitable for various types of steel, although it lacks a “cleaning effect” on the weld pool.
Materials and equipment you need to weld stainless steel
- Welding Machine: Suitable for stainless steel welding processes like TIG (Tungsten Inert Gas), MIG (Metal Inert Gas), or stick welding.
- Stainless Steel Filler Rods or Wire: Matching the grade of stainless steel being welded (e.g., 308, 309, 316).
- Inert Gas Supply: Argon or a mixture of argon and helium for shielding to prevent oxidation during welding.
- Welding Torch: For TIG welding, a torch with a tungsten electrode is necessary to strike the arc.
- Protective Gear: Welding helmet, gloves, and fire-resistant clothing to ensure safety from sparks and UV light.
- Stainless Steel Brush: For cleaning the weld area and post-weld cleanup to maintain corrosion resistance.
- Clamps: To hold the workpieces in place securely during welding.
- Grinding Discs or Flap Discs: For prepping the material and cleaning up welds.
- Back Purging Kit: To prevent oxidation on the backside of the weld, especially for thin stainless steel sheets.
- Ventilation System: Ensures proper air circulation to remove any harmful gases or fumes during welding.
Steps to weld stainless steel
- Preparing Welding Materials and Tools: Before starting the welding process, it’s essential to prepare the necessary welding materials and tools, such as stainless steel welding rods, welding machine, protective mask, flux, grinder, cleaning agent, and cloth. Ensure that these materials and tools meet the requirements and are in good working condition.
- Inspecting Pipe Quality: If welding stainless steel pipes, it’s crucial to inspect the pipe diameter, wall thickness, and quality to ensure they meet specifications.
- Cleaning the Welding Area: Stainless steel surfaces may have oxide layers, rust, oil stains, etc., so it’s necessary to use a grinder to remove the oxide film from the stainless steel and wipe off stains with a cleaning agent. If the thickness exceeds 6 millimeters, V-grooves should be created using tools like grinders.
- Preheating the Welding Area: Some stainless steels (such as martensitic stainless steel) require preheating before welding. Connect the welding machine’s wires according to the product manual, ensure proper grounding of the welding machine, and adjust the current. Use the welding gun to evenly heat the welding area, ensuring that the preheating temperature does not exceed 150 degrees Celsius.
- Adjusting Welding Parameters: Adjust welding parameters such as current, voltage, and preheating temperature based on the specific thickness and material of the pipe to ensure good welding results.
- Welding with Welding Rods: Apply flux evenly to the stainless steel welding area. Hold the welding rod in one hand and the welding gun in the other. Place one end of the welding rod on the stainless steel welding point while using the welding machine to heat the welding rod and stainless steel. Once the welding rod melts to the required quantity, quickly move the welding rod and welding gun.
conclusion
In summary, weld stainless steel is a task that requires a meticulous attitude and professional skills. Only by mastering the correct welding methods and techniques, and strictly following the operating procedures, can we ensure the production of high-quality stainless steel products.
Huaxiao Metal is a stainless steel supplier with over 15 years of experience in exporting stainless steel products. We have rich industry experience and professional knowledge, equipped with multiple stainless steel production lines to ensure stable supply and meet various customer needs. Whether you need consultation on stainless steel welding techniques or have purchasing requirements for stainless steel products, we are committed to providing you with high-quality services. If you have any questions or needs, please feel free to contact us, and we will be happy to assist you.
Get In touch
Ready to Elevate Your Projects? Dive into our Stainless Steel Collection and Submit Your Specifications Today!
Phone/WeChat:
+86 133 8167 3250
Email: [email protected]
Address: RM557, NO.1388 Jiangyue Road, Shanghai China