introduction
production process of stainless steel
Stainless steel, this sounds full of modern sense of the term, in fact, behind contains a wealth of scientific principles and complex processes. Hot rolling and cold rolling as the two core technologies of stainless steel production, but also determines the final quality and application of stainless steel materials. In the next section, we will analyze in detail the principles and characteristics of these two production methods and their important role in the production of stainless steel. Whether you are a material science enthusiast, or interested in the manufacturing process of the explorer, I believe that this article can bring you a new understanding and inspiration.
Let's take a journey together and delve into the wonderful world of stainless steel!
Crude steel smelting process flow
At present the world, the production process of stainless steel smelting process is mainly divided into one-step, two-step and three-step method, as well as new integrated production methods.
- One-step smelting is: Iron + AOD (Argon Oxygen Refining Furnace)
- Two-step method is: EAF (Electric Arc Furnace) + AOD (Argon Oxygen Refining Furnace)
- Three-step method is: EAF (Electric Arc Furnace) + AOD (Argon Oxygen Refining Furnace) + VOD (Vacuum Refining Furnace)
In addition to the traditional several production process of stainless steel, the current integrated production process, i.e., from the iron directly to the stainless steel production process, is also used by many stainless steel factories, the production process is: RKEF (Rotary Kiln Electric Furnace) + AOD (Argon Oxygen Refining furnace).
production process of stainless steel: hot rolled
Production process of hot rolled stainless steel is to slab (mainly for continuous casting billet) as raw material, after heating by the roughing mill unit and finishing mill unit made of strip steel. From the finishing mill last mill out of the hot steel strip through the laminar flow cooling to a set temperature, by the coiler rolled into a steel coil, after cooling the steel coil appearance of oxide skin, showing black, commonly known as “stainless steel black coil”.
Specific stainless steel hot rolled production process is as follows:
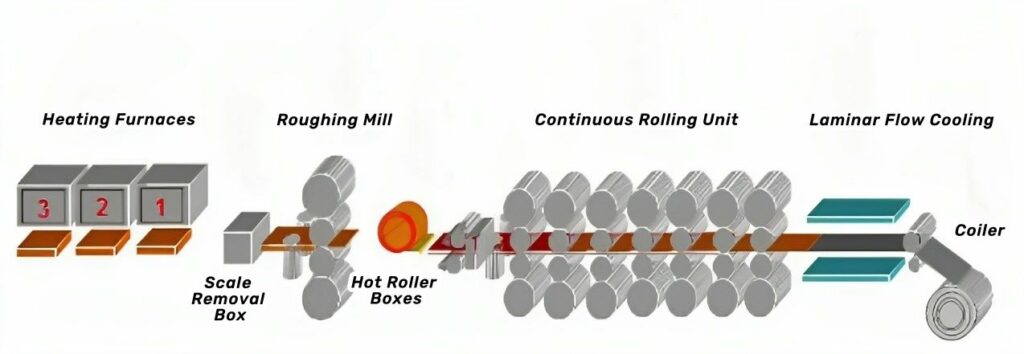
production process of stainless steel: cold rolled
After the hot rolled stainless steel, some of the hot rolled stainless steel products are directly used by the downstream, and some of the hot rolled products need to continue to be processed into cold rolled before use.
Stainless steel cold rolled, mostly hot rolled thickness of 3.0-5.5mm thickness of stainless steel hot rolled products, after the cold rolling equipment calendering process, the production process of stainless steel cold rolled products. Currently, the main production process of stainless steel cold rolled for two categories: stainless steel single rack cold rolled, stainless steel multi-rack cold rolled. The specific production process is shown below:
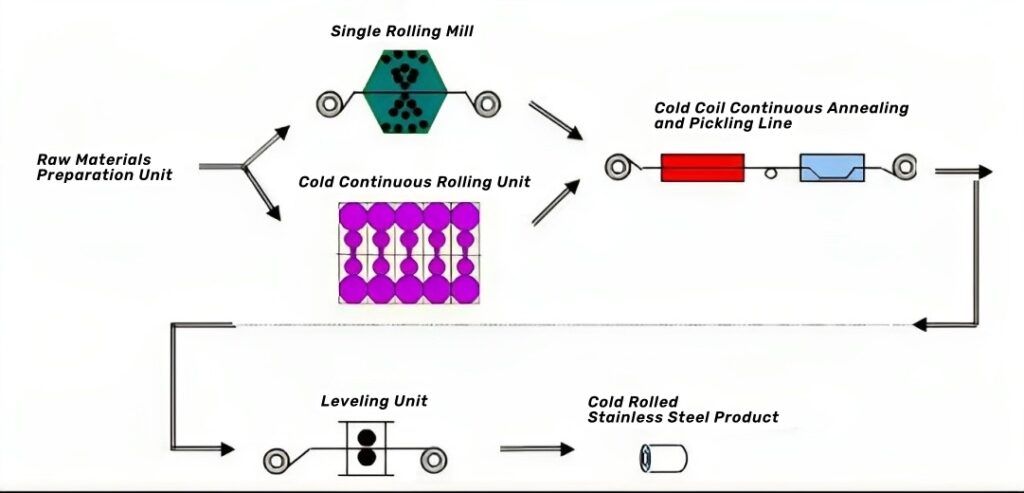
After the stainless steel is cold rolled, it needs to go through annealing and pickling unit. The annealing of stainless steel after cold rolling is to eliminate work hardening through the process of recrystallization to achieve the purpose of softening; the purpose of pickling is to remove the oxidized layer formed on the surface of the steel strip during the annealing process, and the second is to passivate the surface of the stainless steel to improve the corrosion resistance of the steel plate.
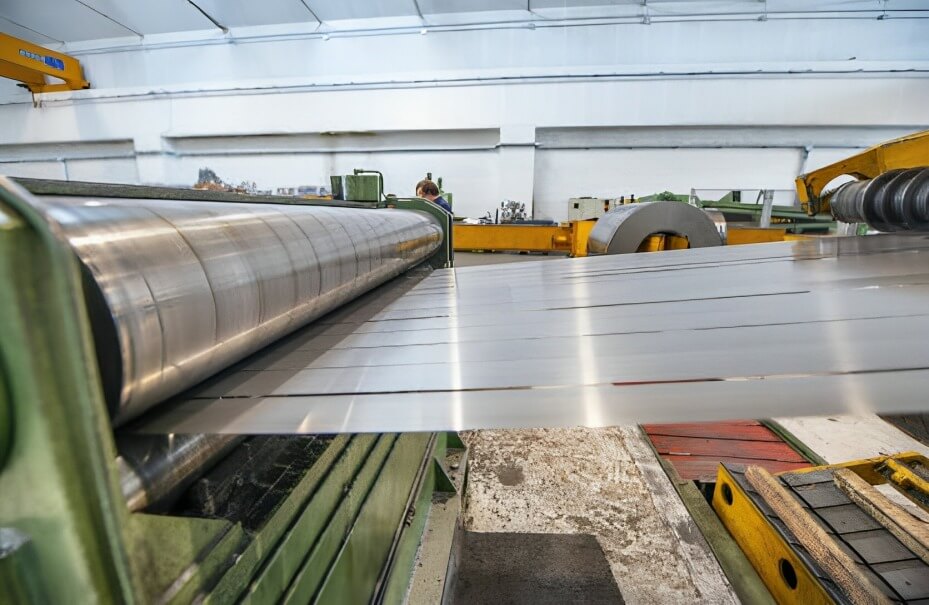
difference of hot rolled and cold rolled
Cold rolled and hot rolled stainless steel differ significantly in several ways. Below is a detailed point-by-point comparison:
Temperature and Process:
- Hot Rolled: Usually carried out at high temperatures between 900°C and 1200°C, the original material is heated to a suitable temperature range and then rolled to plastically deform the material to obtain the desired shape and size. Hot rolling eliminates internal stresses in the original material and improves the plasticity and toughness of the material.
- Cold Rolled: At room temperature, usually after the material is processed into a material, further by cold working (such as rolling) to change its shape and size. Cold rolling can significantly increase the strength and hardness of a material, but may lead to an increase in internal stresses.
Thickness Range:
- Hot rolled is usually used to produce thicker materials with regular thicknesses starting at 3.0mm and going up.
- Cold rolled has a narrower range of conventional thicknesses, usually between 0.3mm and 6.0mm, with the thickest not exceeding 6.0mm.
Material Deformation:
- During hot rolled process, the deformation resistance of the material is lower and it can withstand larger plastic deformations, thus obtaining thicker plates or thicker bars.
- In cold rolled, the deformation resistance of the material is higher as it is processed at room temperature and is usually suitable for thin plates or fine bars.
Surface Quality and Gloss:
- After hot rolled, the surface may be rougher and require further processing to obtain a smooth surface.
- Cold rolled is capable of obtaining a smoother, shinier surface because it produces fewer oxides during processing.
Through an in-depth discussion of the hot rolling and cold rolling production process of stainless steel, we understand the significant differences between the two in terms of temperature, material deformation, thickness, and surface quality. With its advantages in plasticity and toughness, hot rolling is widely used in the production of thick plates and large structural parts. Cold rolled, on the other hand, with its high hardness and excellent corrosion resistance, dominates in areas such as kitchenware and medical equipment.
Huaxiao Metal is committed to providing a full range of stainless steel material solutions. We offer a wide range of grades of stainless steel materials, including 304, 316L, etc., to meet the special needs of different industries. Meanwhile, we offer various shapes of stainless steel products, such as round steel, flat steel, shaped steel, etc., and we can customize the size according to customers’ requirements. In addition, we also provide surface treatment services, such as spraying and plating, to enhance the corrosion resistance and aesthetics of the materials. Our services cover the globe, providing customers with fast and efficient one-stop services. By choosing Huaxiao Metal, you will get high quality materials and professional service support.