Huaxiao stainless steel supplier
What Are The Differences Between Alloy And Stainless Steel?
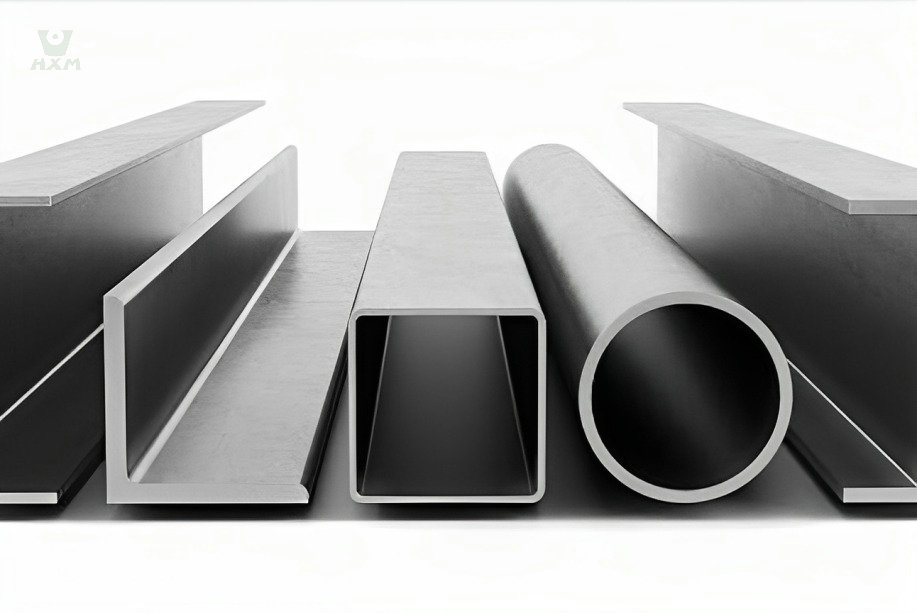
-Huaxiao stainless steel supplier
Alloy and stainless steel both possess distinct characteristics that set them apart in the world of metallurgy. Ever wondered about the disparities between alloy and stainless steel? Are they just two sides of the same metallic coin, or do they diverge significantly in composition and applications? Let’s delve deeper into this intriguing metallurgical dichotomy and unravel the contrasting features that distinguish these materials, shedding light on their uses and strengths in various industries.
Alloy is a blend of metals or a metal combined with other elements, altering its properties for specific purposes. Stainless steel, a type of alloy, that contains iron, chromium, and other elements, renowned for its corrosion resistance. The key difference lies in their composition: alloys encompass a broader category of mixed metals, while stainless steel denotes a specific alloy known for its anti-corrosive properties. Unlike some alloys, stainless steel is engineered to resist rust and staining, making it ideal for applications requiring durability and corrosion resistance, such as kitchenware, construction, and industrial settings.
What Are The Differences Between Alloy And Stainless Steel?
alloy and stainless steel
table of content
alloy and stainless steel
Definition and Composition
alloy
Alloys are composite materials formed by combining two or more metallic elements or a metal with non-metallic elements. This amalgamation alters the properties of the base metal, enhancing or introducing new characteristics to suit specific applications. The process involves melting and blending different metals or elements at precise ratios to create a homogenous mixture. The resulting alloy exhibits properties distinct from its constituent elements, such as increased strength, improved corrosion resistance, enhanced conductivity, or altered physical and mechanical attributes. Alloys cater to diverse needs across industries by offering tailored properties, ensuring versatility in applications ranging from aerospace and automotive engineering to construction and electronics manufacturing.
stainless steel
Stainless steel, a specialized alloy, primarily comprises iron, chromium, and varying additional elements like nickel, molybdenum, or manganese. The defining characteristic of stainless steel is its high chromium content, typically around 10-30%. Chromium forms a protective oxide layer on the steel’s surface, rendering it highly resistant to corrosion and rust when exposed to moisture or aggressive environments. This protective layer, known as the passive layer, acts as a shield against oxidation and staining. Stainless steel supplier play a crucial role in providing tailored compositions and grades of stainless steel, catering to diverse industrial needs, including food processing, architecture, medical equipment, and more, due to its exceptional corrosion resistance, durability, and aesthetic appeal.
alloy and stainless steel
Characteristics of Alloys
Alloys present a distinct characteristic: customizable properties, attributed to the deliberate blending of multiple metals or elements in varying proportions. This deliberate amalgamation allows engineers and metallurgists to manipulate and fine-tune the properties of the resulting alloy. By adjusting the composition, properties such as hardness, tensile strength, ductility, electrical conductivity, and corrosion resistance can be precisely tailored to meet specific industrial demands. For instance, modifying the ratio of constituent elements in steel alloys can enhance their resistance to corrosion or increase their tensile strength. This inherent versatility in altering properties makes alloys a cornerstone in material science, enabling the production of materials with precisely tailored characteristics for diverse applications across industries.
The characteristic of varying strength in alloys stems from their composition, which involves the combination of different metals or elements in controlled proportions. This results in a wide spectrum of strength levels exhibited by various alloys. The manipulation of alloy composition allows for the creation of materials with distinct mechanical properties. Some alloys possess exceptional tensile strength, crucial for applications requiring high durability and structural integrity, such as in aerospace or construction. Conversely, other alloys prioritize flexibility or malleability, making them suitable for applications where shaping or forming intricate designs is essential, such as in jewelry or specialized manufacturing processes. This variability in strength attributes empowers industries to select alloys tailored precisely to meet specific mechanical requirements across diverse applications and sectors.
The concept of specific alloy characteristics delineates the unique traits inherent in distinct alloy compositions. Various alloys exhibit specialized properties due to their specific combinations of metals or elements. For instance, brass, an alloy of copper and zinc, boasts excellent malleability, making it suitable for decorative applications and intricate designs. In contrast, bronze, composed primarily of copper and tin, showcases remarkable wear resistance, making it valuable for bearings and tools. Additionally, aluminum alloys offer exceptional lightweight properties, crucial in aerospace and automotive industries. These specific characteristics emerge from the deliberate selection and proportioning of alloying elements, enabling the tailoring of materials with targeted properties for specific industrial, engineering, and commercial applications.
The advantages of alloy formulation reside in the deliberate manipulation and combination of multiple metals or elements to create materials with superior properties compared to pure metals. This process offers several benefits:
Enhanced Properties: Alloys possess tailored characteristics, such as increased strength, improved corrosion resistance, or heightened conductivity, not inherent in individual metals.
Customization: Alloy formulation allows engineers to precisely adjust properties to meet specific industrial requirements, optimizing the material’s performance for diverse applications.
Versatility: Alloys exhibit versatility in application due to their diverse properties, contributing to advancements across industries like aerospace, automotive, construction, and electronics.
Specialized Applications: Tailored alloys cater to specialized applications; for instance, specialized steel alloys resist extreme temperatures or harsh environments, critical in industrial settings.
Economic Benefits: Alloys often provide cost-effective solutions by combining less expensive metals to achieve properties akin to more costly materials, balancing performance and cost efficiency.
In essence, alloy formulation stands as a pivotal aspect of material science, offering a spectrum of superior properties and enabling the development of materials optimized for specific industrial needs.
Examples of common alloy types
- Composition: Brass is primarily an alloy of copper and zinc.
- Characteristics: It exhibits excellent malleability, corrosion resistance, and acoustic properties.
- Applications: Brass finds usage in musical instruments, decorative hardware, plumbing fittings, and electrical components due to its malleability and attractive appearance.
- Composition: Bronze primarily consists of copper and tin, sometimes with additional elements like aluminum or silicon.
- Characteristics: Bronze offers superior wear resistance, strength, and ductility.
- Applications: Its durability makes it suitable for sculpture, architectural fittings, bearings, tools, and historical artifacts.
- Composition: Aluminum alloys contain primarily aluminum, combined with other elements like copper, zinc, magnesium, or silicon.
- Characteristics: These alloys possess lightweight properties, corrosion resistance, and excellent strength-to-weight ratios.
- Applications: Aluminum alloys are extensively used in aerospace, automotive manufacturing, construction, and consumer electronics for their lightweight and durable nature.
- Composition: Steel alloys primarily consist of iron and carbon, with varying amounts of other elements such as chromium, nickel, manganese, or molybdenum.
- Characteristics: Steel alloys offer high strength, durability, and corrosion resistance, depending on their composition.
- Applications: Steel alloys are crucial in structural applications, manufacturing machinery, automotive parts, and various industrial tools due to their strength and versatility.
These common alloy types illustrate the diverse applications and specialized properties that result from the deliberate combination of elements, showcasing the versatility and utility of alloys across numerous industries.
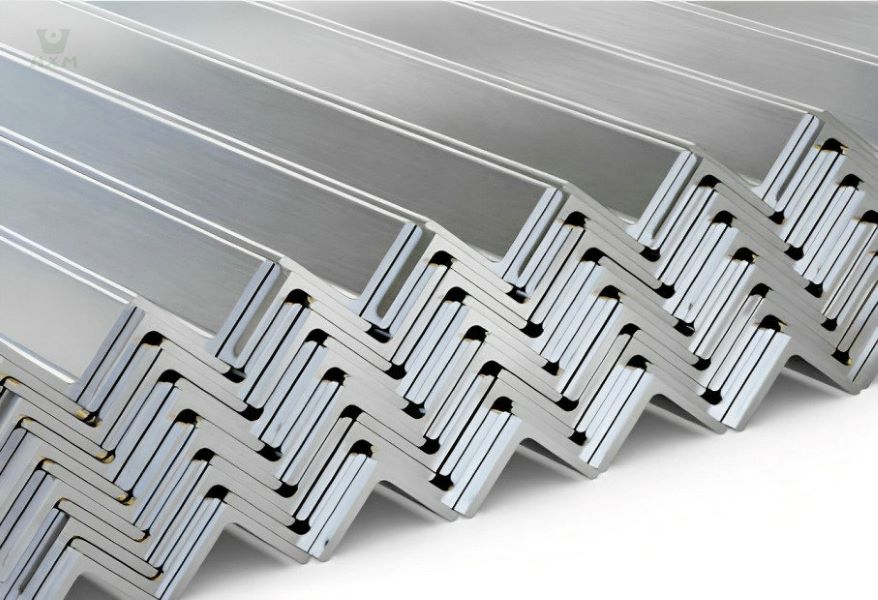
-Huaxiao stainless steel supplier
alloy and stainless steel
Characteristics of stainless steel
Chromium, typically present in stainless steel at levels of 10% or more, plays a pivotal role in imparting corrosion resistance. When exposed to oxygen, chromium forms a thin, self-repairing oxide layer on the surface of stainless steel. This passive oxide layer, known as chromium oxide (Cr2O3), acts as a protective shield, preventing further oxidation or corrosion of the underlying metal. This layer is highly stable, even in harsh environments, providing enduring protection against corrosion, rust, and staining.
Moreover, other alloying elements such as nickel, molybdenum, and nitrogen also contribute significantly to stainless steel’s corrosion resistance. Nickel enhances the stability of the passive film, increasing the alloy’s resistance to both general and localized corrosion. Molybdenum further enhances stainless steel’s resistance to corrosion, particularly in chloride-rich environments, preventing pitting and crevice corrosion.
This robust resistance to corrosion due to the synergistic effects of chromium and other alloying elements makes stainless steel a preferred material in applications where corrosion protection is crucial, including chemical processing, marine environments, architectural structures, food and beverage processing, and medical equipment. The careful selection and control of alloying elements by stainless steel supplier ensure the production of materials with superior corrosion-resistant properties, ensuring longevity and reliability in diverse industrial applications.
Examples of stainless steel types
Stainless steel encompasses various grades and types, each with unique compositions and characteristics tailored for specific applications. Stainless steel supplier play a crucial role in offering these diverse grades to meet industry-specific requirements. Here are some prominent types:
- Composition: Contains high levels of chromium and nickel, exhibiting excellent corrosion resistance and formability.
- Uses: Widely used in food processing, chemical industries, and architectural applications due to its corrosion resistance and ease of fabrication.
- Composition: Contains higher chromium content and little to no nickel, offering good corrosion resistance, particularly in mild environments.
- Uses: Commonly used in automotive applications, kitchen appliances, and architectural trim due to its resistance to corrosion and oxidation.
- Composition: Contains higher carbon content, along with chromium, providing good hardness and strength but moderate corrosion resistance.
- Uses: Applied in cutlery, surgical instruments, and industrial equipment where high strength and wear resistance are crucial.
- Composition: Combines elements from both austenitic and ferritic stainless steels, offering a balanced mix of strength and corrosion resistance.
- Uses: Utilized in chemical processing, oil and gas industries, and marine applications due to its improved strength and corrosion resistance in harsh environments.
- Composition: Contains elements such as copper, aluminum, and niobium, offering excellent strength and corrosion resistance through heat treatment.
- Uses: Employed in aerospace components, high-performance equipment, and offshore applications requiring exceptional strength and corrosion resistance.
Each stainless steel type possesses distinct properties suited for specific environments and applications. Stainless steel supplier cater to these diverse needs by providing various grades, enabling industries to select the most suitable material for optimal performance in their respective fields.
alloy and stainless steel
Comparing Alloy and Stainless Steel
Alloys: Alloys are composite materials formed by blending multiple metals or a metal with non-metallic elements. They comprise a diverse range of mixtures, altering properties such as strength, conductivity, or resistance to suit specific applications.
Stainless Steel: Stainless steel is a specific type of alloy primarily composed of iron, chromium, and other elements like nickel, molybdenum, or manganese. Its distinguishing feature is its high chromium content, forming a protective layer against corrosion.
Alloys: They offer tailored properties, enabling customization for specific industrial needs. Alloys vary widely in characteristics, with brass for malleability, bronze for wear resistance, and aluminum alloys for lightweight properties.
Stainless Steel: Notably known for its exceptional corrosion resistance due to the presence of chromium. Stainless steel serves diverse industries, with austenitic types ideal for corrosion-prone environments, ferritic for general purposes, and martensitic for high strength applications.
Alloys: Versatile in applications across industries, alloys cater to specialized requirements. They are used in automotive, aerospace, construction, and electronics, offering a broad spectrum of properties suited to varied purposes.
Stainless Steel: Stainless steel finds extensive use in industries like food processing, architectural design, medical equipment, and marine engineering due to its exceptional corrosion resistance, durability, and aesthetic appeal.
In summary, while both alloys and stainless steel are composite materials, stainless steel is a specialized type of alloy renowned for its corrosion resistance, specifically tailored for a myriad of applications across industries, distinguishing itself from other alloys by its unique properties and extensive utility.
alloy and stainless steel
conclusion
Here’s a recap emphasizing the key differences between alloys and stainless steel, highlighting their significance and widespread utilization in various industries while acknowledging their distinct properties:
Alloys and stainless steel represent diverse categories of composite materials with unique attributes, catering to multifaceted industrial needs.
Alloys encompass a broad spectrum of mixed metals or metal/non-metal blends tailored for specific properties. They offer versatility across industries, exemplified by brass for malleability, bronze for wear resistance, and aluminum alloys for lightweight properties.
Stainless steel, a specialized alloy, distinguished by its high chromium content, exhibits unparalleled corrosion resistance, making it a vital material in diverse applications. It finds extensive use in food processing, architecture, medicine, and marine engineering due to its durability and resistance to corrosion.
Significantly, stainless steel supplier play a pivotal role in providing tailored compositions of this alloy, ensuring precise chromium content and additional elements to enhance corrosion resistance for specific industrial applications.
The significance of alloys lies in their versatility, offering a wide array of tailored properties, while stainless steel’s significance lies in its exceptional corrosion resistance, durability, and aesthetic appeal, making it indispensable in critical industries.
Acknowledging their distinct properties, the diverse applications of alloys and stainless steel underscore their immense value in meeting specialized industrial requirements, providing essential solutions across sectors while offering unique properties suited to their specific purposes.