What is the effect of carbon in stainless steel?
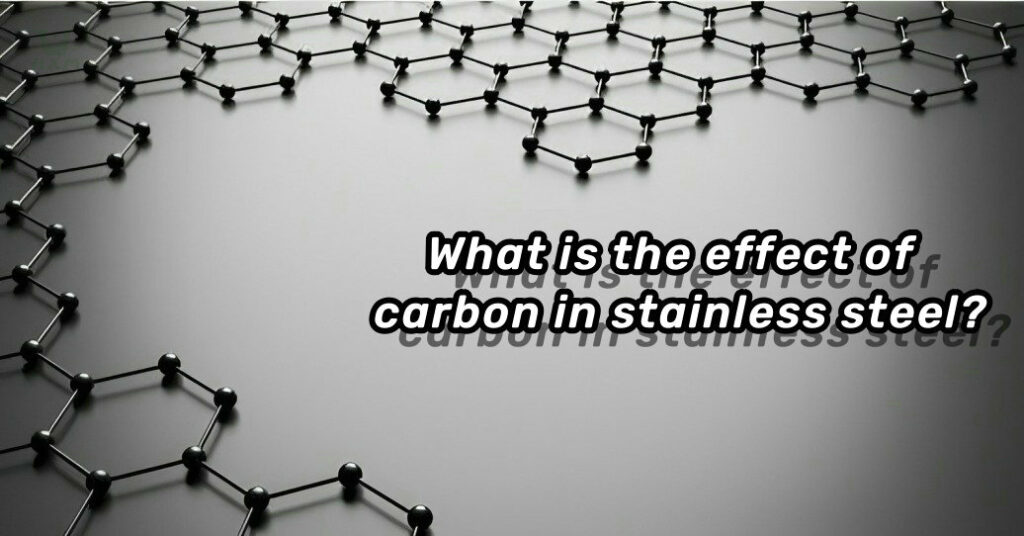
When it comes to the composition of stainless steel, its main components usually include iron, chromium, nickel and other alloying elements. Stainless steel is known for its excellent corrosion resistance, but there is one element that, while it may be added in small amounts, plays a key role in its performance: carbon
What is the effect of carbon in stainless steel?
Carbon, despite being present in low quantities within stainless steel, carbon content and its distribution directly impact the physical, mechanical, and chemical properties of stainless steel.
Hardness and Strength: Carbon content contributes to enhancing the hardness and strength of stainless steel. Increased carbon levels alter the steel’s crystal lattice, resulting in more solid solutions within the structure, leading to increased hardness and resilience.
Machinability: Moderate carbon content can improve the machinability of stainless steel. In certain instances, the addition of carbon aids in enhancing the material’s machinability, making it more amenable to various shaping processes.
Corrosion Resistance: While beneficial for strength, excessive carbon content might compromise stainless steel’s corrosion resistance. Higher carbon levels promote the formation of carbides within the crystal lattice, reducing the available chromium, and consequently diminishing the steel’s resistance to corrosion.
In summary, Careful consideration of carbon content and its influence on stainless steel’s performance is essential in engineering design and material selection to meet the specific requirements of different applications.
Stainless steel grades with carbon content
In stainless steel, various grades contain trace amounts of carbon, contributing to their overall composition. Here are some common stainless steel grades where carbon is present:
Austenitic Stainless Steel: Examples include grades like 304 (UNS S30400) and 316 (UNS S31600), which typically contain relatively low levels of carbon (usually below 0.08%) to enhance corrosion resistance and weldability.
Ferritic Stainless Steel: Grades such as 430 (UNS S43000) contain higher chromium and lower carbon content (usually around 0.12%), aimed at increasing hardness and corrosion resistance.
Martensitic Stainless Steel: For instance, grades like 410 (UNS S41000) and 420 (UNS S42000) possess relatively higher carbon content (usually ranging from 0.15% to 0.4%) to enhance hardness and wear resistance.
Despite its minimal presence, carbon significantly influences stainless steel properties, especially in terms of hardness, strength, and machinability. It’s important to note that variations in carbon content affect the mechanical properties and corrosion resistance of stainless steel. Therefore, when selecting suitable stainless steel materials, consideration of carbon content and its impact on performance is essential.
One crucial aspect in the production of stainless steel grades lies within the stainless steel factory. This manufacturing facility plays a pivotal role in ensuring quality, precision, and consistency in producing various stainless steel alloys. The expertise and technology employed in a stainless steel factory contribute significantly to the development and delivery of stainless steel products across diverse industries.
chemical composition of common stainless steel grades
Stainless Steel Grade | Carbon (C) | Chromium (Cr) | Nickel (Ni) | Manganese (Mn) | Silicon (Si) | Phosphorus (P) | Sulfur (S) |
---|---|---|---|---|---|---|---|
304 (UNS S30400) | ≤ 0.08% | 18 – 20% | 8 – 10.5% | ≤ 2% | ≤ 1% | ≤ 0.045% | ≤ 0.03% |
316 (UNS S31600) | ≤ 0.08% | 16 – 18% | 10 – 14% | ≤ 2% | ≤ 0.75% | ≤ 0.045% | ≤ 0.03% |
430 (UNS S43000) | ≤ 0.12% | 16 – 18% | – | ≤ 1% | ≤ 0.75% | ≤ 0.04% | ≤ 0.03% |
410 (UNS S41000) | ≤ 0.15% | 11.5 – 13.5% | – | ≤ 1% | ≤ 1% | ≤ 0.04% | ≤ 0.03% |
420 (UNS S42000) | 0.15 – 0.4% | 12 – 14% | – | ≤ 1% | ≤ 1% | ≤ 0.04% | ≤ 0.03% |
Please note that these percentage values are for reference only and the actual composition may vary depending on the stainless steel factory, manufacturer, production lot, or standard requirements. The accuracy and range of chemical compositions may vary according to specific standards and stainless steel grades.
Within the intricate world of stainless steel, subtle changes in carbon content wield significant influence over the alloy’s properties. While carbon exists in small amounts in these alloys, its presence—no matter how modest—wields a remarkable impact, steering the material’s behavior in diverse directions.
Effects of Low Carbon in Stainless Steel
The carbon in stainless steel plays a pivotal role in shaping its properties. When considering alloys with low carbon content, typically below 0.03%, several notable effects come into play:
- Improved Corrosion Resistance: Low-carbon stainless steel exhibits enhanced resistance to intergranular corrosion due to reduced carbide precipitation along the grain boundaries. This effect is particularly crucial in applications where corrosion resistance is paramount, such as in aggressive environments within chemical and petrochemical industries.
- Increased Weldability: A lower carbon concentration contributes to improved weldability in stainless steel grades. Reduced carbon minimizes the formation of chromium carbides during welding, preventing the depletion of chromium around the weld area. As a result, it maintains the material's corrosion resistance post-welding, making it suitable for fabrication in the stainless steel factory.
- Maintained Mechanical Properties: While low-carbon stainless steel may exhibit marginally decreased strength compared to higher carbon counterparts, it retains sufficient mechanical properties for many applications. This ensures adequate structural integrity while benefiting from improved corrosion resistance.
- Suitability for Cold Working: Stainless steel with lower carbon content allows for enhanced formability and ductility, making it more amenable to cold working processes such as bending, drawing, and forming without encountering excessive brittleness.
In the stainless steel factory, the effects of carbon content are carefully considered during alloy production. Manufacturers control the carbon content to engineer stainless steel grades with desired properties. The selection of low carbon in stainless steel, owing to its improved corrosion resistance and weldability, finds application in various industries ranging from architecture to food processing and medical devices.
In conclusion, the deliberate manipulation of carbon in stainless steel, particularly in the case of lower concentrations, significantly impacts the material’s corrosion resistance, weldability, mechanical properties, and suitability for fabrication processes.
Effects of Moderate Carbon Content in Stainless Steel
The moderate presence of carbon, typically ranging between 0.03% to 0.15%, within stainless steel alloys introduces several notable effects:
- Enhanced Strength and Hardness: A moderate level of carbon infusion contributes to bolstering the stainless steel's strength and hardness. This effect stems from the formation of carbon-rich martensite during heat treatment, thereby increasing the material's overall hardness and wear resistance.
- Impact on Machinability: While a moderate carbon concentration augments strength, it can also impact the material's machinability. Increased carbon content tends to elevate the steel's hardness, which can lead to greater tool wear during machining processes, influencing production efficiency in a stainless steel factory.
- Effect on Weldability: Moderately carbonized stainless steel grades may pose challenges during welding. Elevated carbon levels can precipitate chromium carbides, diminishing the chromium available for corrosion resistance around the welded zones. Thus, careful welding techniques are required to mitigate potential issues while maintaining the alloy's corrosion resistance.
- Balanced Ductility and Formability: Stainless steel with moderate carbon content strikes a balance between strength and ductility. This allows for sufficient formability and ductility while retaining considerable strength, making it suitable for applications requiring a blend of these properties.
In the realm of stainless steel production within a factory setting, the controlled manipulation of carbon content is crucial. Manufacturers meticulously adjust carbon concentrations to craft stainless steel alloys that exhibit desired properties while considering factors such as machinability, weldability, and mechanical strength.
The effect of carbon in stainless steel at a moderate level intricately influences its overall performance. The balance between strength, hardness, machinability, and weldability is delicately managed to meet diverse industrial requirements, from automotive components to machinery parts and architectural structures.
In summary, moderate carbon content in stainless steel significantly influences its mechanical properties, machinability, and weldability. The stainless steel factory plays a pivotal role in calibrating carbon levels to engineer alloys that align with specific application needs.
Effects of High Carbon Content in Stainless Steel
Elevated carbon content, typically above 0.15%, within stainless steel alloys introduces distinctive effects that significantly influence the material’s properties:
- Enhanced Hardness and Wear Resistance: High carbon content contributes to the formation of robust carbides, notably increasing the material's hardness and wear resistance. This hardness is beneficial in applications where abrasion resistance is critical, such as cutting tools or certain machine components.
- Impact on Toughness and Ductility: However, a trade-off exists between hardness and toughness with increased carbon. High carbon levels can reduce the steel's toughness and ductility, making it more brittle and less capable of withstanding impact or dynamic loads.
- Challenges in Weldability: High carbon content poses challenges during welding processes due to increased carbon's tendency to form chromium carbides, reducing the chromium available for maintaining corrosion resistance. This necessitates precise control and specialized techniques in welding applications, impacting the production processes within a stainless steel factory.
- Potential for Hardenability: The higher carbon levels in stainless steel offer increased potential for hardenability through heat treatment processes. This allows for tailored adjustments to achieve desired material properties in specific applications.
In the domain of stainless steel manufacturing within a factory setting, the management of high carbon content demands precision. The stainless steel factory employs meticulous control over carbon levels to craft alloys suitable for applications that prioritize hardness and wear resistance over toughness.
The effect of carbon in stainless steel at higher concentrations significantly influences its mechanical properties and poses challenges in terms of maintaining a balance between hardness and toughness. High carbon content grades find utilization in applications where hardness and wear resistance are of paramount importance, such as certain industrial tooling and specialized equipment components.
In summary, high carbon content in stainless steel alloys distinctly impacts their hardness, wear resistance, and brittleness. The stainless steel factory ‘s role is pivotal in adjusting carbon levels to create alloys tailored for specific applications while considering trade-offs between hardness and other mechanical properties.
What is the effect of carbon in stainless steel?
Exploring various common materials that contain carbon and understanding their significance in engineering and industrial applications:
- Characteristics: Carbon steel is primarily an alloy of iron and carbon. Typically, it contains carbon in the range of 0.05% to 2.0%, offering high strength and hardness.
- Applications: Widely used in manufacturing machinery parts, structural components, tools, and blades. Classified into low carbon, medium carbon, and high carbon steel based on carbon content.
- Characteristics: Cast iron is a carbon-rich iron-carbon alloy, often exceeding 2% carbon, along with elements like silicon and manganese.
- Applications: Utilized for manufacturing engine components, pipelines, architectural structures, and kitchenware. Different types include gray cast iron, ductile cast iron, among others, based on compositions and properties.
- Characteristics: Alloy steel incorporates elements beyond carbon (such as chromium, molybdenum, nickel) into the steel matrix, usually ranging from 0.05% to 1.5% carbon.
- Applications: Employed in automotive parts, industrial equipment, cutting tools, and aerospace due to superior strength, wear resistance, and corrosion resistance.
- Characteristics: Tool steel, a specialized alloy steel, contains higher carbon levels (typically between 0.5% to 1.5%) alongside other alloying elements.
- Applications: Used in producing cutting tools, dies, drills, and components operating under high temperatures and pressures due to its hardness and wear resistance.
- Characteristics: Cellulose constitutes the primary cell wall component in plants, comprised of carbon, oxygen, and hydrogen elements.
- Applications: Widely applied in papermaking, textiles, wood, and biomass fuels, serving as a common renewable resource.
These carbon-containing materials play vital roles in engineering, construction, manufacturing, and other industries. Carbon, as a key constituent, significantly influences their properties and suitability for various applications, shaping their performance and relevance in diverse contexts, including those in the stainless steel factory for tailored alloy production.
This knowledge of carbon’s influence aids in tailoring material properties to meet specific requirements, ensuring optimal performance in different applications.