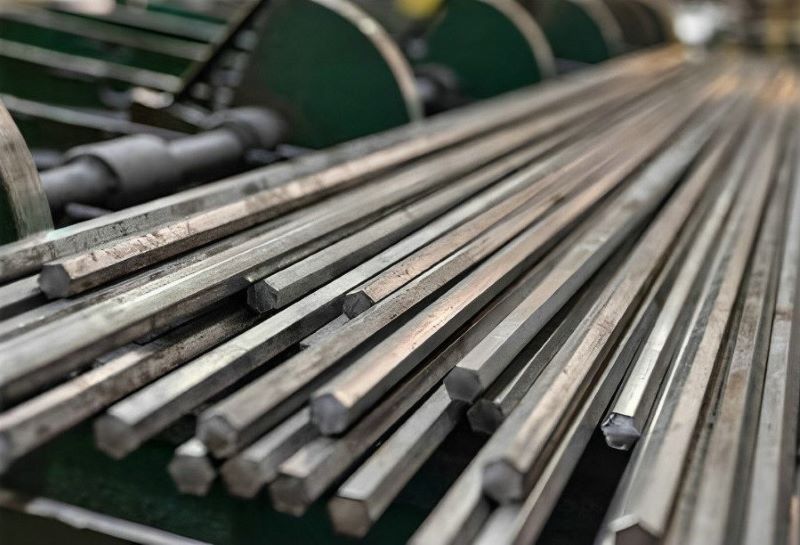
301 stainless steel bar supplier
Diameter: 3mm-480mm, 1/8″ to 2 1/4″
Standard: GB1220, ASTM A484/484M, EN 10060/ DIN 1013 ASTM A276, EN 10278, DIN 671
Main Grade: 201, 304, 316, 316L, 310s, 430
Finish: Black, NO.1, mill finish, cold draw, H9, H11
Product Description Of 301 stainless steel bar
Introducing our versatile 301 stainless steel bar, a modification of grade 304, offering exceptional properties for various applications. Renowned for its high strength, excellent ductility, and corrosion resistance, this material is a top choice. Type 301 boasts comparable corrosion resistance to type 302 and 304, with optimal performance in its cold worked and annealed state. Additionally, it is non-magnetic in the annealed condition, becoming slightly magnetic with cold working. Ideal for aircraft structures, marine components, architectural elements, auto parts, kitchenware, and much more. Elevate your projects with the reliability of 301 stainless steel.
specification Of 301 stainless steel bar
chemical composition of 301 stainless steel bar
Element | Composition Range |
---|---|
Chromium (Cr) | 16.0 – 18.0% |
Nickel (Ni) | 6.0 – 8.0% |
Carbon (C) | ≤ 0.15% |
Manganese (Mn) | ≤ 2.0% |
Silicon (Si) | ≤ 1.0% |
Phosphorus (P) | ≤ 0.045% |
Sulfur (S) | ≤ 0.03% |
physical property of 301 stainless steel bar
Property | Value |
---|---|
Density | 0.285 lb/in³ |
Melting Point | 2,550-2,590 °F |
Specific Heat | 1.1 x 10^-1 BTU/lb-°F |
Electrical Resistivity | 1 ohm/sq inch at 20°C |
Elastic Modulus (Modulus of Elasticity) | 28,000 ksi |
Thermal Conductivity | 108 BTU-in/hr-ft²-°F |
mechanical property of 301 stainless steel bar
Property | Value |
---|---|
Tensile Strength | 180,000 – 200,000 psi |
Yield Strength (0.2% offset) | 140,000 – 175,000 psi |
Elongation at Break | 40 – 45% |
Modulus of Elasticity | 28,000,000 psi |
Hardness (Rockwell C) | 25 – 39 |
characteristics Of 301 stainless steel bar
Corrosion resistance is a critical property of stainless steel, and type 301 stainless steel bar is no exception. Type 301 exhibits impressive corrosion resistance, comparable to that of type 302 and 304 stainless steels. However, its corrosion resistance is most optimal when it has undergone cold working and annealing processes.
The corrosion resistance of type 301 stainless steel is primarily attributed to its composition, which includes chromium (Cr) content in the range of 16.0% to 18.0%. Chromium forms a passive oxide layer on the surface of the steel, known as chromium oxide (Cr2O3), which acts as a protective barrier against environmental factors such as moisture, oxygen, and corrosive chemicals.
In the cold worked and annealed condition, type 301 stainless steel achieves its highest level of corrosion resistance. This condition involves a controlled deformation process at low temperatures, which refines the microstructure and enhances the material’s ability to withstand corrosive environments. As a result, type 301 stainless steel is an excellent choice for applications where corrosion resistance is paramount, ensuring the longevity and reliability of components and structures in challenging conditions.
High strength and ductility are fundamental characteristics that define the exceptional performance of type 301 stainless steel bar:
High Strength: Type 301 stainless steel is renowned for its remarkable strength. This strength is primarily attributed to its carefully balanced alloy composition, which includes chromium and nickel. Chromium contributes to the steel’s hardness and tensile strength, while nickel enhances its overall toughness and ductility. The result is a material that can withstand substantial mechanical loads and stresses, making it suitable for a wide range of demanding applications.
Ductility: In addition to its high strength, type 301 stainless steel is highly ductile. Ductility is the ability of a material to deform without fracturing or breaking when subjected to tensile forces. This characteristic allows type 301 stainless steel to be formed and shaped into various intricate designs and configurations. It can be easily fabricated through processes like cold working, rolling, and bending without compromising its structural integrity. The combination of strength and ductility makes type 301 stainless steel a versatile choice for applications where both structural integrity and design flexibility are essential.
These properties, combined with its corrosion resistance, non-magnetic nature, and other advantageous characteristics, establish type 301 stainless steel as a material of choice across a wide spectrum of industries, including aerospace, automotive, architectural, and more, where high-performance components are required to meet stringent mechanical demands.
The non-magnetic nature of type 301 stainless steel is a notable characteristic that distinguishes it from many other materials:
Type 301 stainless steel exhibits non-magnetic properties in its annealed condition, meaning that it does not attract or respond to magnetic fields. This behavior arises from its austenitic crystalline structure, which is inherently non-magnetic. The austenitic structure is formed due to the presence of significant amounts of nickel (Ni) within the alloy composition.
The non-magnetic quality of type 301 stainless steel is particularly advantageous in applications where magnetic interference or attraction could pose issues. For instance, in sensitive electronic equipment or medical devices, the absence of magnetic properties ensures that the material does not disrupt nearby magnetic fields or cause unwanted electromagnetic effects. It is also valuable in applications involving magnetic resonance imaging (MRI) machines, where magnetic materials can distort imaging results.
Additionally, type 301 stainless steel retains its non-magnetic nature even after cold working or deformation processes, making it suitable for applications that require both mechanical strength and non-magnetic characteristics.
This unique combination of non-magnetic behavior, corrosion resistance, high strength, and ductility positions type 301 stainless steel as a versatile material across industries ranging from electronics and healthcare to aerospace and automotive, where precision and reliability are paramount.
application Of 301 stainless steel bar
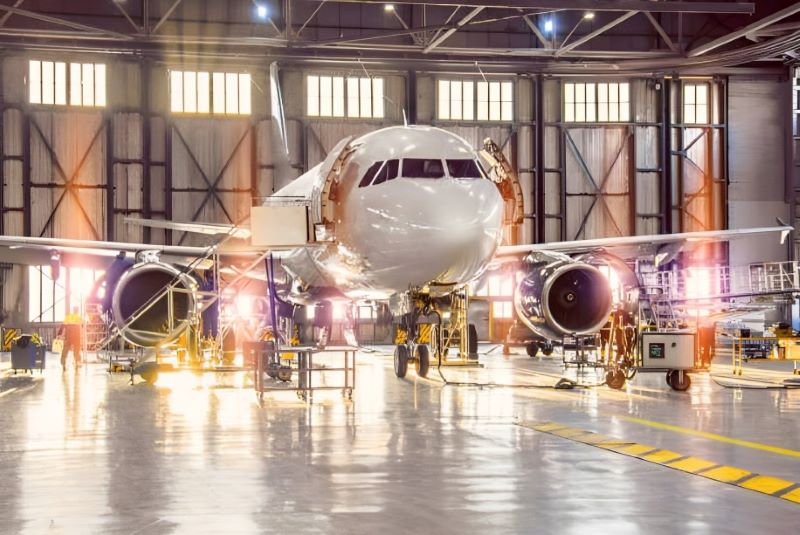
Aircraft Structures
Type 301 stainless steel is widely used in aircraft structures due to its exceptional combination of high strength and excellent corrosion resistance. These properties help ensure the structural integrity and longevity of components critical to aviation safety.
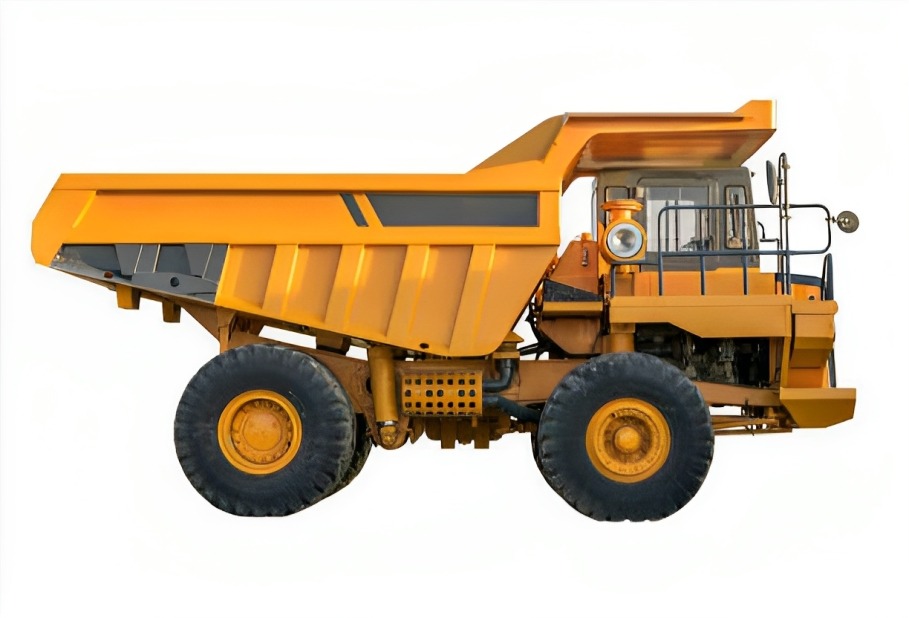
Trailer Bodies
In the transportation industry, 301 stainless steel finds application in the construction of trailer bodies. Its high strength and resistance to corrosion make it suitable for enduring the rigors of road and weather conditions, enhancing the durability and longevity of trailers.
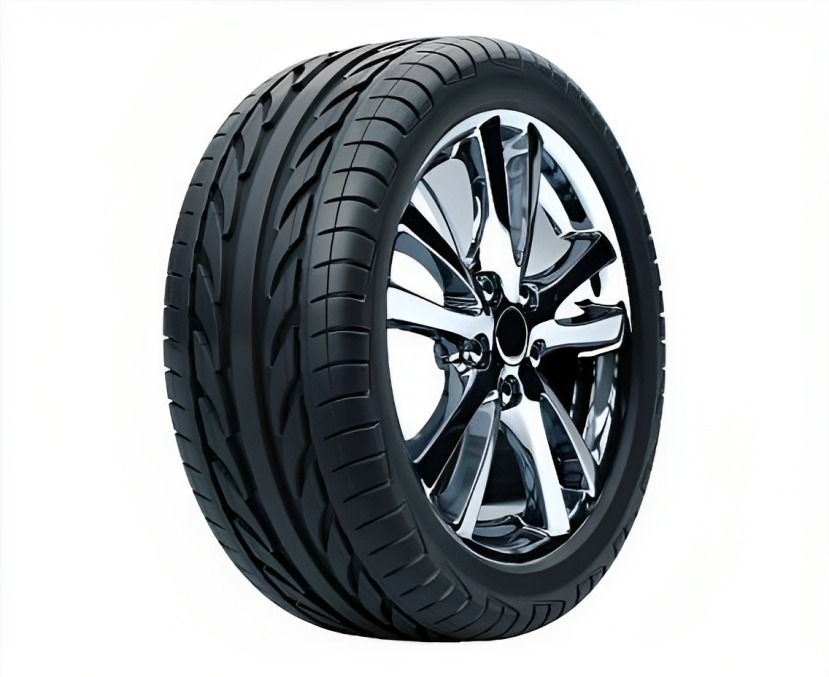
Automotive Rim
Automotive rims, an integral part of a vehicle's wheel system, benefit from the use of 301 stainless steel. Its high strength ensures the structural integrity of rims, especially in demanding driving conditions.
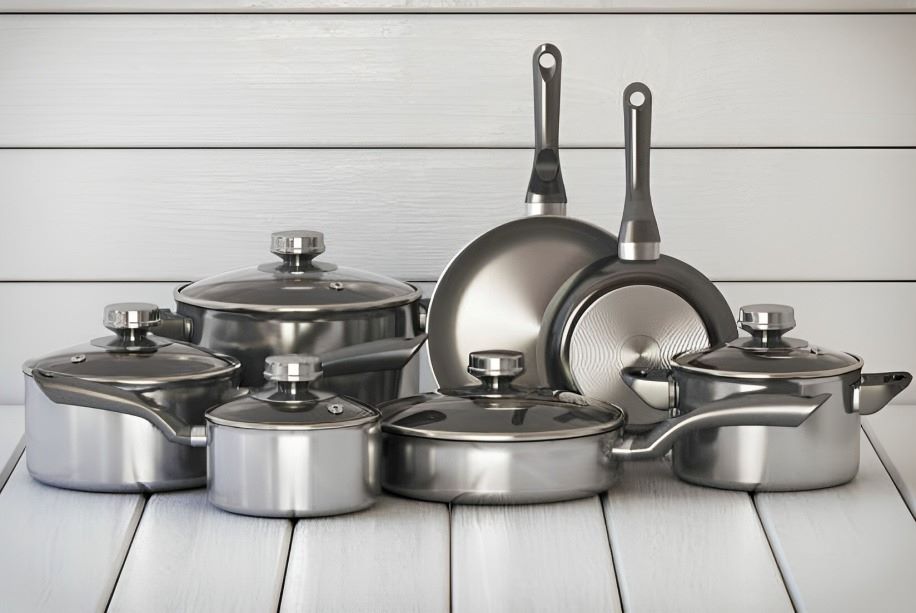
Utensils and Tableware
Due to its outstanding durability, ease of cleaning, resistance to bacterial growth, and non-reactivity with food, type 301 stainless steel is commonly employed in the manufacturing of utensils and tableware. These properties make it a preferred material for cutlery, cookware, and various dining accessories, providing reliability and safety in food preparation and consumption.
FAQ
301 stainless steel bars differ from 304 and 316 stainless steel bars primarily in their composition and properties:
Composition: 301 stainless steel has a lower chromium and nickel content compared to 304 and 316 stainless steels. It contains around 16-18% chromium and 6-8% nickel, while 304 and 316 typically have higher nickel content (8-10% for 304 and 10-14% for 316).
Corrosion Resistance: While all three grades offer good corrosion resistance, 316 stainless steel provides the highest resistance, particularly in chloride environments. 304 stainless steel follows closely in corrosion resistance, and 301 offers comparable resistance to type 302 and 304.
Strength and Ductility: 301 stainless steel is known for its high strength and ductility, making it suitable for applications where these properties are essential. 304 and 316 stainless steels are generally less strong but offer better overall corrosion resistance.
Magnetic Properties: 301 stainless steel is non-magnetic in its annealed condition but becomes more magnetic with cold working. In contrast, 304 and 316 stainless steels are typically non-magnetic.
Applications: 301 stainless steel is often chosen for its high strength and corrosion resistance, making it suitable for applications like aircraft structures, automotive components, and trailer bodies. On the other hand, 304 and 316 stainless steels are preferred in applications where superior corrosion resistance is required, such as food processing equipment and marine components.
So, the choice between these stainless steel grades depends on the specific requirements of your application, considering factors like corrosion resistance, strength, ductility, and magnetic properties.
The corrosion resistance of 301 stainless steel bars is comparable to that of other stainless steel grades, such as 304 and 316. However, the specific performance depends on various factors, including the environment and conditions to which the material is exposed.
301 Stainless Steel: In its cold-worked and annealed condition, type 301 stainless steel achieves its most optimal resistance to corrosion. While it provides good corrosion resistance, it may not be as corrosion-resistant as 304 and 316 stainless steels in certain aggressive environments.
304 Stainless Steel: Type 304 stainless steel offers excellent general corrosion resistance and is widely used in various applications. It is particularly resistant to corrosion in atmospheric and mildly corrosive environments.
316 Stainless Steel: Type 316 stainless steel is known for its exceptional corrosion resistance, especially in chloride-rich environments. It is often chosen for applications where exposure to corrosive substances is significant, such as marine environments and chemical processing equipment.
In summary, while 301 stainless steel provides good corrosion resistance, it may not match the superior corrosion resistance of 304 and 316 stainless steels in specific corrosive conditions. Therefore, the choice of stainless steel grade should consider the particular environment and corrosion challenges of the application.
Yes, 301 stainless steel bars are generally magnetic in their annealed condition. However, they can become more magnetic with cold working or mechanical deformation. The degree of magnetism can vary based on the extent of cold working and processing the material has undergone. It’s important to note that while 301 stainless steel may exhibit some magnetic properties, it is not as strongly magnetic as some other stainless steel grades, like the ferritic stainless steels.
Properly cleaning and maintaining 301 stainless steel bars is essential to ensure their longevity and performance. Here are some guidelines:
Regular Cleaning: Clean the bars regularly with mild soap or a stainless steel cleaner. Use a soft cloth or sponge to wipe away dirt, grime, or fingerprints.
Avoid Abrasives: Avoid using abrasive cleaners, steel wool, or scouring pads, as they can scratch the surface and damage the finish.
Directional Cleaning: When cleaning, follow the grain or polish lines of the stainless steel to maintain its appearance.
Rinse Thoroughly: After cleaning, rinse the bars with clean water and wipe them dry to prevent water spots.
Avoid Harsh Chemicals: Avoid using harsh chemicals or acids, such as bleach or chlorine-based cleaners, as they can corrode stainless steel.
Stainless Steel Polish: Periodically, you can use a stainless steel polish to restore the shine and protect against corrosion.
Routine Inspection: Regularly inspect the bars for signs of corrosion, especially if used in corrosive environments. Address any corrosion promptly to prevent further damage.
Proper Storage: Store stainless steel bars in a clean, dry environment away from exposure to moisture or chemicals.
By following these maintenance tips, you can keep your 301 stainless steel bars looking and performing their best over time. For more specific recommendations or products, consult your stainless steel bar supplier.
The welding process for 301 stainless steel bars involves specific techniques to ensure a strong and durable bond. Here are the key steps:
Preparation: Clean the welding area thoroughly to remove any contaminants, oils, or dirt. Proper preparation is crucial for a successful weld.
Use Low Carbon Welding Electrodes: Select welding electrodes with low carbon content to minimize the risk of carbide precipitation, which can reduce corrosion resistance. Common choices include 308L or 316L electrodes.
Shielding Gas: Use an appropriate shielding gas, typically argon or helium, to protect the weld area from atmospheric contamination and oxidation.
Welding Technique: Employ the Gas Tungsten Arc Welding (GTAW) or Tungsten Inert Gas (TIG) welding process for precise control over the heat input. This helps prevent distortion and overheating.
Control Heat Input: Maintain proper heat input during welding to avoid excessive temperatures that can lead to sensitization and reduced corrosion resistance.
Back Purging: In critical applications, consider using back purging with inert gas to protect the inside of the weld and prevent oxidation.
Post-Weld Cleaning: After welding, clean the weld area to remove any contaminants, including heat-tint and oxides, which can affect corrosion resistance.
Passivation: Passivate the welded area by applying a citric acid solution or other suitable passivation methods. This helps restore the stainless steel’s protective oxide layer.
Inspection: Inspect the weld for any defects, such as cracks or inclusions, and perform any necessary repairs.
Testing: In some cases, perform non-destructive testing, such as dye penetrant or X-ray inspection, to ensure the quality of the weld.
It’s essential to follow industry standards and best practices for welding 301 stainless steel bars to maintain their corrosion resistance and mechanical properties. Consult your stainless steel bar supplier for specific welding guidelines and recommendations based on your application.
The manufacturing process of 301 stainless steel bars involves several stages to achieve the desired properties and dimensions. Here is an overview of the typical manufacturing process:
Raw Material Selection: High-quality raw materials, primarily stainless steel billets or blooms, are carefully selected based on their chemical composition and quality. These materials are usually sourced from reputable steel suppliers.
Melting: The selected stainless steel materials are melted in an electric arc furnace or other suitable melting methods. During this process, the chemical composition is precisely controlled to meet the desired specifications for 301 stainless steel.
Casting: The molten stainless steel is cast into semi-finished shapes, such as billets or slabs, using continuous casting or other casting methods. These semi-finished products will be further processed into bars.
Hot Rolling: The semi-finished products are heated to high temperatures and then passed through a series of rolling mills. This hot rolling process reduces the thickness and shapes the stainless steel into the desired bar profile. Hot rolling also refines the microstructure of the steel.
Cooling: After hot rolling, the bars are rapidly cooled using various cooling methods to achieve the desired mechanical properties.
Cold Working: In some cases, cold working processes like cold drawing or cold rolling may be employed to further refine the dimensions and improve the surface finish of the bars. Cold working can also enhance the mechanical properties of the stainless steel.
Heat Treatment: Depending on the specific requirements, the bars may undergo heat treatment processes such as annealing or solution annealing to optimize their mechanical properties, corrosion resistance, and ductility.
Finishing: The bars are subjected to surface finishing processes like pickling, passivation, or polishing to remove any oxides or contaminants and improve their surface quality.
Cutting and Inspection: The finished bars are cut into desired lengths and thoroughly inspected for dimensional accuracy, surface quality, and mechanical properties. Non-destructive testing may also be conducted to ensure quality.
Packaging and Shipment: The final 301 stainless steel bars are packaged according to industry standards to protect them during transportation and storage. They are then shipped to distributors, manufacturers, or end-users.
Throughout the manufacturing process, strict quality control measures are implemented to meet industry standards and customer specifications. Stainless steel bar suppliers play a crucial role in ensuring the quality and consistency of the final products.
Get In touch
Ready to Elevate Your Projects? Dive into our Stainless Steel Collection and Submit Your Specifications Today!
Phone/WhatsApp/WeChat:
+86 13052085117
Email: [email protected]
Address: RM557, NO.1388 Jiangyue Road, Shanghai China