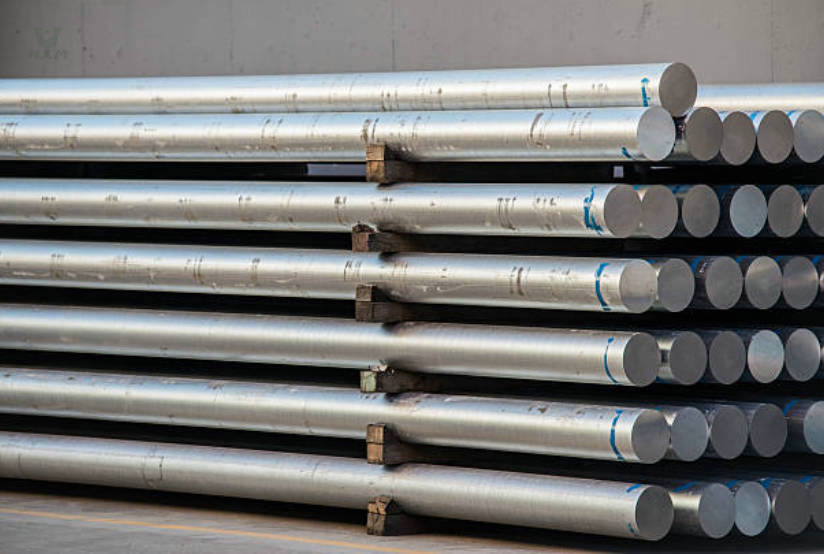
310 Stainless Steel Bar Supplier
Diameter: 3mm-480mm, 1/8″ to 2 1/4″
Standard: GB1220, ASTM A484/484M, EN 10060/ DIN 1013 ASTM A276, EN 10278, DIN 671
Shape: round, flat, square, angle, hexagonal
Finish: Black, NO.1, mill finish, cold draw, H9, H11
Product Description Of 310 Stainless Steel Bar
Stainless Steel 310 Bars stand as the paragon of heat-resistant alloys, meticulously engineered to thrive in the most extreme high-temperature environments. With an exceptional heat resistance reaching up to 1,200°C (2,192°F), these bars are indispensable in industries such as heat treatment, chemical processing, aerospace, and petrochemical. Their corrosion resistance is unparalleled, rendering them impervious to oxidation and corrosion. What sets Stainless Steel 310 Bars apart is their extraordinary versatility. They offer superb formability, allowing for ease of shaping and welding. Furthermore, their toughness remains uncompromised, even when subjected to the harshest conditions. These bars provide a foundation for exceptional performance and durability, making them a top choice for critical applications where resilience and longevity are non-negotiable. Whether you’re in the aerospace industry, refining petrochemicals, or engaged in precision heat treatments, Stainless Steel 310 Bars are your unwavering ally, ready to withstand the heat and pressure of your most demanding endeavors. Elevate your projects with the strength, durability, and reliability of Stainless Steel 310 Bars.
Types Of Stainless Steel 310 Bar
1. 310 Stainless Steel Bar
- Composition: This type contains 25% chromium and 20% nickel, providing exceptional resistance to oxidation and corrosion.
- Properties: It retains its strength and toughness at temperatures up to 2100°F (1150°C). It’s ideal for high-temperature applications such as furnace parts, heat treatment baskets, and jet engine parts.
2. 310S Stainless Steel Bar
- Composition: Similar to 310, but with a lower carbon content (0.08% max).
- Properties: The reduced carbon content minimizes carbide precipitation during welding, maintaining corrosion resistance and making it easier to fabricate. It is commonly used in environments where high temperatures are coupled with moderate corrosion.
3. 310H Stainless Steel Bar
- Composition: Similar to 310, but with a higher carbon content (0.04-0.10%).
- Properties: The higher carbon content ensures better creep resistance. It is preferred in high-temperature, high-pressure environments such as petrochemical processing and power generation.
Choosing the right type of stainless steel 310 bar depends on the specific requirements of your application, such as the operating temperature, the environment, and the need for weldability or creep resistance.
specification Of 310 Stainless Steel Bar
chemical composition of 310 stainless steel bar
Element | Carbon (C) | Silicon (Si) | Manganese (Mn) | Phosphorus (P) | Sulfur (S) | Chromium (Cr) | Nickel (Ni) |
---|---|---|---|---|---|---|---|
Weight Percentage | 0.08% max | 1.50% max | 2.00% max | 0.045% max | 0.03% max | 24.0 – 26.0% | 19.0 – 22.0% |
physical property of 310 stainless steel bar
Property | Value |
---|---|
Density | 7.9 g/cm³ |
Melting Point | 1402 – 1454°C (2556 – 2650°F) |
Specific Heat Capacity | 0.502 J/g·°C |
Thermal Conductivity | 14.2 W/(m·K) at 100°C (212°F) |
Coefficient of Expansion | 15.9 x 10^-6 /°C (20-100°C) |
Electrical Resistivity | 720 nΩ·m at 20°C (68°F) |
Magnetic Properties | Non-magnetic |
mechanical property of 310 stainless steel bar
Property | Value |
---|---|
Tensile Strength | 515 MPa (74,700 psi) |
Yield Strength | 205 MPa (29,750 psi) |
Elongation | 40% (in 50mm) |
Hardness (Brinell) | 217 |
Modulus of Elasticity | 200 GPa (29,000 ksi) |
Poisson’s Ratio | 0.30 |
features Of 310 Stainless Steel Bar
The term “austenitic stainless steel” refers to a specific crystalline structure that is characterized by its remarkable high-temperature properties. In the case of 310 stainless steel, this austenitic structure plays a pivotal role in its exceptional performance under elevated temperatures.
Austenitic stainless steels like 310 are primarily composed of iron, chromium, and nickel, with low carbon content. This unique composition grants 310 stainless steel its outstanding heat resistance, making it well-suited for applications involving extreme temperatures.
The austenitic structure allows 310 stainless steel to maintain its integrity and mechanical properties even at temperatures reaching up to 2100°F (1149°C). This remarkable high-temperature stability is a result of the alloy’s ability to resist phase transformations and retain its strength and corrosion resistance in demanding environments.
Whether in furnace components, heat treating boxes, or other high-temperature applications, the austenitic nature of 310 stainless steel ensures reliability and performance in situations where many other materials would fail. This exceptional characteristic is a key reason why 310 stainless steel is highly regarded in industries where extreme heat is a critical factor.
The chemical composition of 310 stainless steel is a fundamental aspect that defines its properties and performance. This austenitic stainless steel is meticulously engineered with specific primary elements to achieve its exceptional characteristics:
Carbon (C): 310 stainless steel maintains a maximum carbon content of 0.25%. This low carbon concentration minimizes the risk of carbide precipitation, improving weldability and corrosion resistance.
Manganese (Mn): With a maximum manganese content of 2%, this element enhances the steel’s mechanical properties, contributing to its overall strength and formability.
Silicon (Si): The silicon content is capped at 1.5%, aiding in the steel’s resistance to oxidation and providing additional strength.
Chromium (Cr): Chromium content falls within the range of 24% to 26%, serving as a pivotal contributor to the alloy’s high-temperature corrosion resistance.
Nickel (Ni): The nickel content ranges from 19% to 22%. Nickel enhances the steel’s ductility and corrosion resistance, making it suitable for various applications, especially in high-temperature environments.
Sulfur (S) and Phosphorus (P): Traces of sulfur and phosphorus are present within the alloy, ensuring that these impurities are kept to a minimum to maintain the steel’s high-quality standards.
Iron (Fe): The remaining balance of the alloy is primarily composed of iron, the base element that forms the matrix for these essential alloying elements.
This precise chemical composition of 310 stainless steel underpins its remarkable heat resistance, oxidation resistance, and corrosion resistance, making it a preferred choice in industries where these characteristics are paramount.
The high-temperature performance of 310 stainless steel is a defining characteristic that makes it exceptionally suitable for demanding applications in extreme heat. This austenitic stainless steel showcases remarkable attributes that enable its superior performance at elevated temperatures:
1. Impressive Heat Resistance: 310 stainless steel is renowned for its ability to maintain structural integrity in high-temperature environments, withstanding temperatures as high as 2100°F (1150°C). This outstanding heat resistance ensures that the material remains stable and retains its mechanical properties even under extreme thermal conditions.
2. Ideal for High-Temperature Applications: Due to its exceptional heat resistance, 310 stainless steel is an ideal choice for applications that involve exposure to elevated temperatures. It is commonly used in industries where equipment and components must operate efficiently and reliably in extreme heat, such as in furnace components, heat treating boxes, and parts for hydrogenation processes.
3. Oxidation and Corrosion Resistance: In addition to withstanding high temperatures, 310 stainless steel maintains excellent oxidation and corrosion resistance. Its high chromium and nickel content provide a protective layer that shields the material from degradation due to oxidation and chemical reactions, further enhancing its longevity in demanding heat-related settings.
4. Superior Durability: The combination of its heat resistance, oxidation resistance, and corrosion resistance ensures that 310 stainless steel bars maintain their durability and functionality even in the most challenging high-temperature environments. This reliability is crucial in applications where safety and performance are paramount.
In summary, 310 stainless steel’s outstanding high-temperature performance makes it an indispensable material for industries requiring reliable operation under extreme heat conditions. Its ability to resist heat, oxidation, and corrosion ensures that it continues to excel in applications where elevated temperatures are a constant challenge.
The weldability and ductility of 310 stainless steel bars are noteworthy features that significantly contribute to its versatility and usability in various applications. Here’s a detailed explanation of this particular characteristic:
Weldability: 310 stainless steel is recognized for its excellent weldability. This property stems from its low carbon content, which minimizes the formation of carbides during welding. Carbides can make stainless steel more susceptible to corrosion and reduce its weldability. The lower carbon content in 310 stainless steel, especially the 310S variation, helps prevent the precipitation of carbides, allowing for smooth and reliable welding processes. Welding methods such as fusion or resistance welding are commonly used with 310 stainless steel, with acetylene welding being best avoided to ensure optimal results.
Ductility: Ductility refers to a material’s ability to undergo deformation or changes in shape without breaking. 310 stainless steel exhibits good ductility, making it capable of withstanding bending, stretching, or other forms of mechanical manipulation without fracturing. This property is particularly valuable in applications where the material needs to be formed into various shapes or structures.
The combination of weldability and ductility in 310 stainless steel makes it a versatile choice for industries that require components with precise dimensions and complex geometries. Whether it’s in the manufacturing of custom-designed parts or the fabrication of intricate equipment, 310 stainless steel’s weldability and ductility play a pivotal role in ensuring that it can be seamlessly integrated into a wide range of applications.
In summary, 310 stainless steel’s commendable weldability and ductility make it a preferred material for industries and applications that demand precision, flexibility, and reliability in both the manufacturing and operation of equipment and components.
The strength and toughness of 310 stainless steel bars are integral characteristics that contribute to their exceptional performance in various environments. Here’s a detailed explanation of this particular feature:
Strength at High Temperatures: One of the notable properties of 310 stainless steel is its ability to maintain moderate strength at elevated temperatures. This is attributed to its unique alloy composition, which includes high chromium and nickel content. Chromium enhances the steel’s resistance to oxidation and corrosion, while nickel provides stability and strength. As a result, 310 stainless steel retains its structural integrity and strength even when exposed to high temperatures, making it an ideal choice for applications in industries like aerospace, manufacturing, and heat treatment.
Toughness: Toughness refers to a material’s ability to absorb energy without fracturing or failing. 310 stainless steel exhibits impressive toughness, enabling it to withstand mechanical stress, impacts, and varying environmental conditions. This toughness is vital in applications where the material may encounter challenging conditions or loading, ensuring that it remains durable and reliable over time.
Strength at Cryogenic Temperatures: In addition to its high-temperature strength, 310 stainless steel also retains its mechanical strength at cryogenic temperatures. This feature is particularly advantageous for applications in industries like aerospace and medical, where components may be subjected to extremely low temperatures. The material’s ability to maintain strength in these conditions ensures that it can perform reliably in diverse settings.
In summary, the combination of strength and toughness in 310 stainless steel bars makes them a preferred choice for applications that demand consistent performance across a wide range of temperatures and environmental challenges. Whether in high-temperature industrial processes or cryogenic storage, 310 stainless steel’s ability to maintain strength and toughness is a key factor in its widespread use.
application Of 310 Stainless Steel Bar
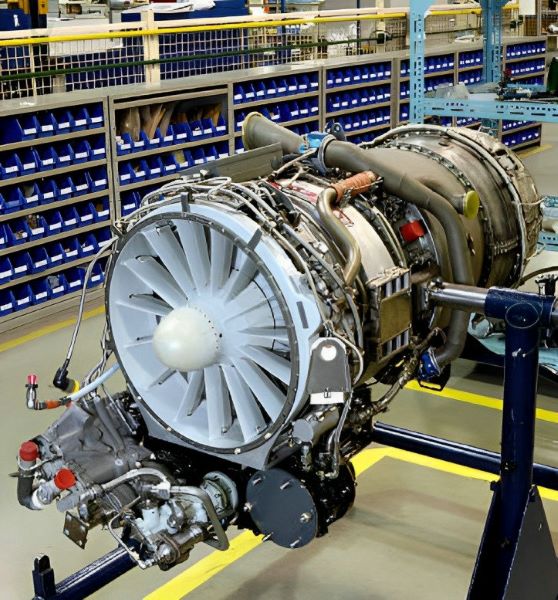
Aerospace
310 stainless steel bars find critical applications in the aerospace industry due to their exceptional strength and resistance to high temperatures. They are used in various components of aircraft and spacecraft, ensuring the structural integrity and reliability of these vital systems, even under extreme thermal conditions. Whether in engine components, exhaust systems, or other aerospace parts, 310 stainless steel's ability to withstand high-temperature environments is crucial to the safety and performance of aerospace equipment.
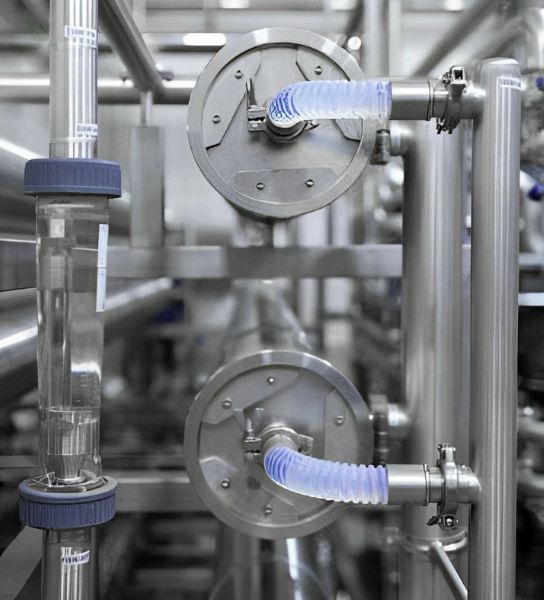
Chemical Processing
In the realm of chemical processing, 310 stainless steel bars are highly valued for their remarkable corrosion resistance. Chemical processing plants often handle corrosive substances and operate in harsh environments. The superior resistance of 310 stainless steel to chemical corrosion makes it an ideal material for equipment used in these facilities. From storage tanks to pipelines and reaction vessels, 310 stainless steel ensures the longevity and safety of chemical processing equipment.
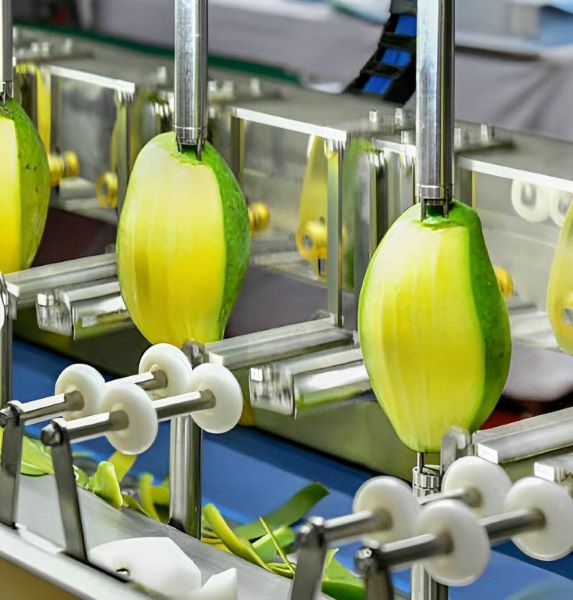
Food Processing
Food processing equipment demands strict hygiene standards and resistance to corrosion from acidic or caustic substances. 310 stainless steel bars are extensively employed in this industry due to their resistance to corrosion and ability to maintain a clean and sterile environment. They are utilized in the construction of machines, conveyors, and containers for food production, preserving the quality and safety of food products.
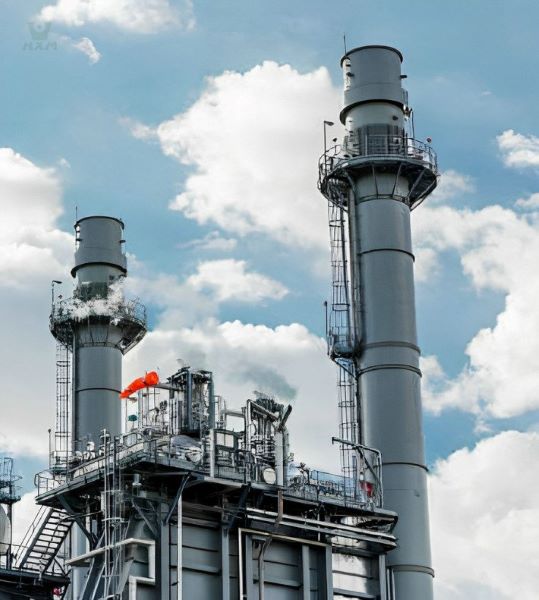
Oil and Gas Refineries
The demanding conditions of oil and gas refineries require materials that can withstand high temperatures, pressure, and exposure to potentially corrosive elements. 310 stainless steel bars are used in heat exchangers, tube hangers, and steam boilers within refineries. These components are critical for efficient and safe operations in the oil and gas industry. The ability of 310 stainless steel to maintain strength and corrosion resistance under these harsh conditions ensures the reliability of refinery equipment.
FAQ
310 stainless steel bar differs from 309 stainless steel bar in its composition and specific characteristics. While both belong to the austenitic stainless steel family, here are the key distinctions:
Chemical Composition: 310 stainless steel contains a higher chromium and nickel content compared to 309 stainless steel. It typically comprises about 24% to 26% chromium and 19% to 22% nickel, while 309 has approximately 22% chromium and 12% nickel. This difference in composition results in enhanced oxidation resistance for 310 stainless steel.
High-Temperature Performance: 310 stainless steel demonstrates better high-temperature performance, with a maximum operating temperature of up to 2100°F (1149°C), whereas 309 is recommended for temperatures up to 2000°F (1093°C). The increased nickel content in 310 contributes to its improved thermal stability.
Oxidation Resistance: 310 stainless steel provides superior oxidation resistance at elevated temperatures. It can withstand prolonged exposure to high heat, making it suitable for applications involving heat treatment, furnaces, and industrial ovens.
Corrosion Resistance: Both 309 and 310 stainless steel offer excellent corrosion resistance in various environments. However, 310 stainless steel exhibits slightly better resistance to specific corrosive elements due to its higher chromium and nickel content.
In summary, 310 stainless steel excels in applications where high-temperature and oxidation resistance are critical. Its enhanced composition and performance make it a preferred choice for industries that require reliable performance under extreme heat, such as the aerospace and heat treatment industries. While 309 stainless steel is also corrosion-resistant and suitable for high-temperature environments, 310 outperforms it in specific applications requiring the highest level of heat resistance. Consulting a stainless steel bar supplier can help determine the most appropriate choice for your specific needs.
310 stainless steel bar and 304 stainless steel bar are distinct in terms of their composition, characteristics, and applications. Here’s a detailed comparison:
Chemical Composition:
310 Stainless Steel: 310 stainless steel is an austenitic stainless steel with a specific composition, including approximately 24-26% chromium and 19-22% nickel. It also contains minimal amounts of sulfur and phosphorus. The higher nickel and chromium content enhances its heat and corrosion resistance properties.
304 Stainless Steel: In contrast, 304 stainless steel, another austenitic stainless steel, consists of around 18-20% chromium and 8-10.5% nickel. It has a lower percentage of both nickel and chromium compared to 310 stainless steel.
Heat Resistance:
310 Stainless Steel: 310 stainless steel is renowned for its exceptional resistance to high temperatures. It can withstand operating temperatures of up to 2100°F (1149°C). This makes it ideal for applications in heat treatment equipment, furnaces, and other high-temperature environments.
304 Stainless Steel: While 304 stainless steel offers good corrosion resistance, it is not designed for prolonged exposure to extreme heat. It is suitable for general-purpose applications, including food processing and construction, but not for high-temperature conditions.
Corrosion Resistance:
- 310 Stainless Steel: Both 310 and 304 stainless steel provide excellent corrosion resistance. However, 310 stainless steel exhibits superior corrosion resistance in specific environments due to its higher chromium and nickel content. This makes it more appropriate for applications involving harsh corrosive elements.
Applications:
310 Stainless Steel: 310 stainless steel is primarily employed in industries that demand resistance to extreme heat, such as aerospace, heat treatment, and industrial furnace components. Its oxidation resistance and strength at high temperatures set it apart.
304 Stainless Steel: 304 stainless steel is widely used in various general applications, including construction, food processing equipment, and architectural structures, where its corrosion resistance and formability are advantageous.
In summary, 310 stainless steel excels in high-temperature and corrosion-resistant applications, while 304 stainless steel is versatile and suited to a broad range of general applications. Consulting a stainless steel bar supplier is crucial to determine the most suitable choice for your specific project, considering the environmental conditions and performance requirements.
310 stainless steel bar and 316 stainless steel bar are two distinct stainless steel alloys, each with its own set of characteristics and applications. Let’s explore their differences:
Chemical Composition:
310 Stainless Steel: 310 stainless steel is an austenitic stainless steel alloy with approximately 24-26% chromium and 19-22% nickel. It also contains a minimal amount of sulfur and phosphorus. The high chromium and nickel content contributes to its excellent heat and corrosion resistance.
316 Stainless Steel: On the other hand, 316 stainless steel, also an austenitic alloy, contains about 16-18% chromium, 10-14% nickel, and a higher percentage of molybdenum (2-3%). The added molybdenum enhances its resistance to chlorides and other corrosive substances.
Heat Resistance:
310 Stainless Steel: 310 stainless steel is well-known for its exceptional heat resistance and can withstand operating temperatures of up to 2100°F (1149°C). This makes it ideal for applications in high-temperature environments, such as heat treatment equipment and industrial furnaces.
316 Stainless Steel: While 316 stainless steel offers good corrosion resistance, it is not designed for extended exposure to extremely high temperatures. It is often used in applications involving exposure to corrosive environments, particularly those containing chlorides, such as marine settings.
Corrosion Resistance:
310 Stainless Steel: 310 stainless steel excels in resisting oxidation and scaling at high temperatures, making it suitable for heat treatment and furnace applications. It also offers excellent general corrosion resistance.
316 Stainless Steel: 316 stainless steel is celebrated for its exceptional corrosion resistance, especially in chloride-rich environments. This makes it the preferred choice for marine equipment, chemical processing, and applications where exposure to corrosive solutions is a concern.
Applications:
310 Stainless Steel: 310 stainless steel is primarily employed in industries requiring resistance to extreme heat, such as aerospace, heat treatment equipment, and industrial furnace components.
316 Stainless Steel: 316 stainless steel is widely used in applications where corrosion resistance is paramount, such as marine equipment, chemical processing, pharmaceuticals, and medical devices.
In summary, while both 310 and 316 stainless steel bars offer outstanding corrosion resistance, their primary differentiators are their temperature resistance and specific applications. A stainless steel bar supplier can provide guidance on choosing the appropriate alloy based on your project’s unique requirements and environmental conditions.
Yes, welding 310 stainless steel requires careful consideration of specific techniques to ensure optimal results. A stainless steel bar supplier can provide valuable guidance on welding this alloy. Here are some essential considerations:
1. Selection of Filler Material:
- Use filler metals designed for high-temperature applications, such as AWS A5.4 E310-16 or E310-15. These fillers match the composition of 310 stainless steel and provide excellent resistance to heat.
2. Preheating:
- Preheating the base metal can help reduce the risk of cracking during welding. The specific preheating temperature depends on the thickness of the material and the welding process used.
3. Welding Processes:
- Common welding processes for 310 stainless steel include shielded metal arc welding (SMAW), gas tungsten arc welding (GTAW), and gas metal arc welding (GMAW). The choice of the process depends on the application’s requirements.
4. Heat Input Control:
- Controlling the heat input is crucial to prevent overheating and distortion. Ensure proper amperage and voltage settings for the chosen welding process.
5. Back Purging:
- Back purging with an inert gas like argon is recommended to protect the backside of the weld from oxidation. This is particularly important when welding thick sections.
6. Post-Weld Heat Treatment:
- In some cases, post-weld heat treatment (PWHT) may be necessary to relieve residual stresses and improve the weld’s properties. The specific PWHT requirements will depend on the application.
7. Cleanliness:
- Thoroughly clean the base material and filler metal to remove any contaminants, such as oils, paints, or rust, which can affect the weld’s quality.
8. Testing:
- Non-destructive testing methods like radiography and ultrasonic testing can be used to ensure the integrity of the welds.
It’s crucial to consult with a stainless steel bar supplier and, if possible, a welding specialist when working with 310 stainless steel. They can offer recommendations tailored to your specific welding needs and ensure that the welds meet the necessary quality and performance standards.
310 stainless steel is known for its excellent performance at high temperatures. It can withstand temperatures of up to 2100°F (1149°C) without significant loss of strength. The high chromium and nickel content in 310 stainless steel contribute to its exceptional resistance to oxidation and heat. For precise temperature limits and application-specific recommendations, consulting a stainless steel bar supplier is advisable, as they can provide detailed guidance based on your specific requirements.
While 310 stainless steel offers excellent high-temperature properties and corrosion resistance, there are some limitations and specific situations where it may not be the ideal choice. One limitation is its relatively high cost compared to other stainless steel grades. Additionally, in applications where extremely high temperatures exceeding 2100°F are involved, alternative materials may be preferred. It’s essential to consult with a stainless steel bar supplier to determine whether 310 stainless steel is the right choice for your specific project and to explore alternatives if necessary. Their expertise can help you make an informed decision based on your application’s unique requirements.