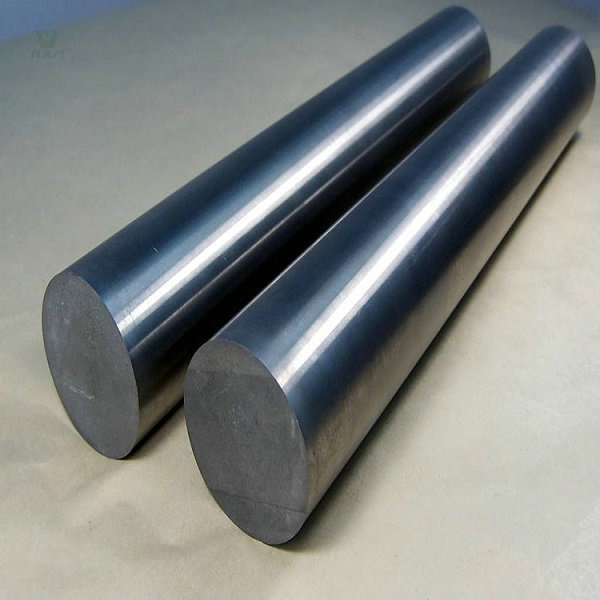
Stainless Steel Round Bar Supplier
Diameter: 3mm-480mm, 1/8″ to 2 1/4″
Standard: GB1220, ASTM A484/484M, EN 10060/ DIN 1013 ASTM A276, EN 10278, DIN 671
Main Grade: 201, 304, 316, 316L, 310s, 430
Finish: Black, NO.1, mill finish, cold draw, H9, H11
Product Description Of stainless steel round bar
· Round bar is a general shape in the stainless steel industry, is a solid round bar with a circular section. Its specifications in diameter, usually expressed in millimeters (mm), such as “50mm” means that the diameter of a 50mm round bar.
· Round Bar usually include 3 process way, hot-rolled, forged, and cold-drawn t. Hot-rolled bar specifications for the 5.5-250 mm.
· Forged for more than 250mm diameter bar, cold drawn for below 50mmsize, 5.5-25 mm small round mostly straight bundles be supplied, and commonly used as steel, bolts and various mechanical parts; more than 25 mm of round steel, mainly for the manufacture of mechanical parts, seamless steel tube blank, etc.
specification Of stainless steel round bar
Main grade description in different standard
ASTM | DIN / EN | JIS | GB | ISO Name | Other |
S20100 201 | 1.4372 | SUS201 | S35350 | X12CrMnNiN17–7-5 | J1 L1 LH 201J1 |
S20200 202 | 1.4373 | SUS202 | S35450 | X12CrMnNiN18–9-5 | 202 L4, 202 J4, 202 J3 |
S30400 304 | 1.4301 | SUS304 | S30408 | X5CrNi18-10 | 06Cr19Ni10 0Cr18Ni9 |
S31603 316L | 1.4404 | SUS316L | S31603 | X2CrNiMo17-12-2 | 022Cr17Ni12Mo2 00Cr17Ni14Mo2 |
S40900 409 | – | SUH409 | S11168 | X5CrTi12 | 0Cr11Ti |
S40910 409L | 1.4512 | SUH409L | S11163 | X2CrTi12 | 00Cr11Ti 022Cr11Ti |
S41008 410S | 1.4000 | SUS410S | S11306 | X6Cr13 | – |
S43000 430 | 1.4016 | SUS430 | 10Cr17 | X6Cr17 | 1Cr17 |
Main grade chemical components in different standard
201 | C % | Si% | Mn % | P % | S % | Ni % | Cr % | N % | Mo % |
ASTM | 0.15 | 1.00 | 5.5-7.5 | 0.050 | 0.030 | 3.5-5.5 | 16.0-18.0 | 0.25 | – |
DIN/EN | 0,15 | 1,00 | 5,5-7,5 | 0,045 | 0,015 | 3,5-5,5 | 16,0-18,0 | 0,05-0,25 | – |
JIS | 0.15 | 1.00 | 5.5-7.5 | 0.060 | 0.030 | 3.5-5.5 | 16.0-18.0 | 0.25 | – |
GB | 0.15 | 1.00 | 5.5-7.5 | 0.050 | 0.030 | 3.5-5.5 | 16.0-18.0 | 0.05-0.25 | – |
202 | C % | Si% | Mn % | P % | S % | Ni % | Cr % | N % | Mo % |
ASTM | 0.15 | 1.00 | 7.5-10.0 | 0.060 | 0.030 | 4.0-6.0 | 17.0-19.0 | 0.25 | – |
DIN/EN | 0,15 | 1,00 | 7,5-10,5 | 0,045 | 0,015 | 4,0-6,0 | 17,0-19,0 | 0,05-0,25 | – |
JIS | 0.15 | 1.00 | 7.5-10.0 | 0.060 | 0.030 | 4.0-6.0 | 17.0-19.0 | 0.25 | – |
GB | 0.15 | 1.00 | 7.5-10.0 | 0.050 | 0.030 | 4.0-6.0 | 17.0-19.0 | 0.05-0.25 | – |
304 | C % | Si% | Mn % | P % | S % | Ni % | Cr % | N % | Mo % |
ASTM | 0.08 | 0.75 | 2.00 | 0.045 | 0.030 | 8.0 – 10.5 | 18.0-20.0 | 0.10 | – |
DIN/EN | 0,07 | 1,00 | 2,00 | 0,045 | 0,015 | 8,0 – 10,5 | 17,5-19,5 | 0,10 | – |
JIS | 0.08 | 1.00 | 2.00 | 0.045 | 0.030 | 8.0 – 10.5 | 18.0-20.0 | – | – |
GB | 0.08 | 1.00 | 2.00 | 0.045 | 0.030 | 8.0 – 10.0 | 18.0-20. 0 | – | – |
316L | C % | Si% | Mn % | P % | S % | Ni % | Cr % | N % | Mo % |
ASTM | 0.030 | 0.75 | 2.00 | 0.045 | 0.030 | 10.0-14.0 | 16.0-18.0 | 0.10 | 2.00-3.00 |
DIN/EN | 0,030 | 1,00 | 2,00 | 0,045 | 0,015 | 10,0-13,0 | 16,5-18,5 | 0,10 | 2,00-2,50 |
JIS | 0.030 | 1.00 | 2.00 | 0.045 | 0.030 | 12.0-15.0 | 16.0-18.0 | – | 2.00-3.00 |
GB | 0.030 | 0.75 | 2.00 | 0.045 | 0.030 | 10.0-14.0 | 16.0-18.0 | 0.10 | 2.00-3.00 |
409 | C % | Si% | Mn % | P % | S % | Ni % | Cr % | N % | Ti % |
ASTM | 0.08 | 1.00 | 1.00 | 0.045 | 0.03 | 0.50 | 10.5-11.7 | – | 6*C% – 0.75 |
DIN/EN | – | – | – | – | – | – | – | – | – |
JIS | 0.08 | 1.00 | 1.00 | 0.040 | 0.030 | – | 10.5-11.7 | – | 6*C% – 0.75 |
GB | 0.08 | 1.00 | 1.00 | 0.045 | 0.030 | 0.60 | 10.5-11.7 | – | 6*C% – 0.75 |
409L | C % | Si% | Mn % | P % | S % | Ni % | Cr % | N % | Ti % |
ASTM | 0.03 | 1.00 | 1.00 | 0.040 | 0.020 | 0.50 | 10.5-11.7 | 0.03 | 6*(C+N)-0.5 |
DIN/EN | 0.03 | 1.00 | 1.00 | 0.040 | 0.015 | – | 10.5-12.5 | – | 6*(C+N)-0.65 |
JIS | 0.03 | 1.00 | 1.00 | 0.040 | 0.030 | – | 10.5-11.7 | – | 6*C% – 0.75 |
GB | 0.03 | 1.00 | 1.00 | 0.040 | 0.020 | – | 10.5-11.7 | 0.03 | Ti≥8*(C+N) |
410S | C % | Si% | Mn % | P % | S % | Ni % | Cr % | N % | Mo % |
ASTM | 0.08 | 1.00 | 1.00 | 0.040 | 0.030 | 0.60 | 11.5-13.5 | – | – |
DIN/EN | 0,08 | 1,00 | 1,00 | 0,040 | 0,015 | – | 12,0-14,0 | – | – |
JIS | 0.08 | 1.00 | 1.00 | 0.040 | 0.030 | – | 11.5-13.5 | – | – |
GB | 0.08 | 1.00 | 1.00 | 0.040 | 0.030 | 0.60 | 11.5-13.5 | – | – |
Main grade mechanical property in different standard
201 | Y.S./Mpa ≥ | T.S./Mpa ≥ | E.L./% ≥ | HB ≤ | HRB ≤ | HBW ≤ | HV ≤ |
ASTM | 260 | 515 | 40 | – | 95 | 217 | – |
JIS | 275 | 520 | 40 | 241 | 100 | – | 253 |
GB | 205 | 515 | 30 | - | 99 | – | - |
202 | Y.S./Mpa ≥ | T.S./Mpa ≥ | E.L./% ≥ | HB ≤ | HRB ≤ | HBW ≤ | HV ≤ |
ASTM | 260 | 620 | 40 | – | – | 241 | – |
JIS | 275 | 520 | 40 | – | 95 | 207 | 218 |
GB | – | – | – | – | – | – | – |
304 | Y.S./Mpa ≥ | T.S./Mpa ≥ | E.L./% ≥ | HB ≤ | HRB ≤ | HBW ≤ | HV ≤ |
ASTM | 205 | 515 | 40 | – | 92 | 201 | – |
JIS | 205 | 520 | 40 | 187 | 90 | – | 200 |
GB | 205 | 515 | 40 | – | 92 | 201 | 210 |
316L | Y.S./Mpa ≥ | T.S./Mpa ≥ | E.L./% ≥ | HB ≤ | HRB ≤ | HBW ≤ | HV ≤ |
ASTM | 170 | 485 | 40 | – | 95 | 217 | – |
JIS | 175 | 480 | 40 | 187 | 90 | 200 | |
GB | 170 | 485 | 40 | – | 95 | 217 | 220 |
409 | Y.S./Mpa ≥ | T.S./Mpa ≥ | E.L./% ≥ | HB ≤ | HRB ≤ | HBW ≤ | HV ≤ |
ASTM | – | – | – | – | – | – | – |
JIS | 175 | 360 | 22 | 162 | 80 | – | 175 |
GB | – | – | – | – | – | – | – |
409L | Y.S./Mpa ≥ | T.S./Mpa ≥ | E.L./% ≥ | HB ≤ | HRB ≤ | HBW ≤ | HV ≤ |
ASTM | 170 | 380 | 20 | – | 88 | 179 | – |
JIS | 175 | 360 | 25 | 162 | 80 | – | 175 |
GB | 170 | 380 | 20 | – | 88 | 179 | 200 |
410S | Y.S./Mpa ≥ | T.S./Mpa ≥ | E.L./% ≥ | HB ≤ | HRB ≤ | HBW ≤ | HV ≤ |
ASTM | 205 | 415 | 22 | – | 89 | 183 | – |
JIS | 205 | 410 | 20 | – | 88 | 183 | 200 |
GB | 205 | 415 | 20 | – | 89 | 183 | 200 |
Production Process and Feature Of stainless steel round bar
- 310S stainless steel round bar 310S stainless steel is austenitic chromium-nickel stainless steel with good oxidation resistance, and corrosion resistance, because of the higher percentage of chromium and nickel, 310S has much better creep strength, and continuous operation at high temperatures, with good high-temperature resistance.
- 316L stainless steel round bar cold-rolled products look good gloss, beautiful; due to the addition of Mo, corrosion resistance, especially excellent pitting corrosion resistance; Excellent high-temperature strength; excellent work hardening (weak magnetic processing)non-magnetic state of the solution;
- 316 stainless steel round bar 316 stainless steel is the second most widely used grade after 304, mainly for the food industry and surgical equipment, due to the addition of Mo, so its corrosion resistance, atmospheric corrosion resistance, and high-temperature strength are particularly good, Can be used in harsh conditions; excellent work hardening (non-magnetic).
- 321 stainless steel round bar Add Ti element in 304 steel to prevent grain boundary corrosion, suitable for 430℃-900℃temperature use. In addition to the titanium added to reduce the risk of material corrosion of the weld other properties similar to 304
- 304L stainless steel round bar 304L stainless steel round bar is a low carbon content of 304 stainless steel variants, for welding occasions. The lower carbon content minimizes the precipitation of carbides in the heat-affected zone adjacent to the weld, and the precipitation of carbides can cause stainless steel to cause intergranular corrosion (weld erosion) in some environments
- 304 stainless steel round bar 304 stainless steel is the most widely used chromium-nickel stainless steel, with good corrosion resistance, heat resistance, low-temperature strength, and mechanical properties. Corrosion in the atmosphere, if it is an industrial atmosphere or heavily polluted areas, you need to be promptly cleaned to avoid corrosion.
application Of stainless steel round bar
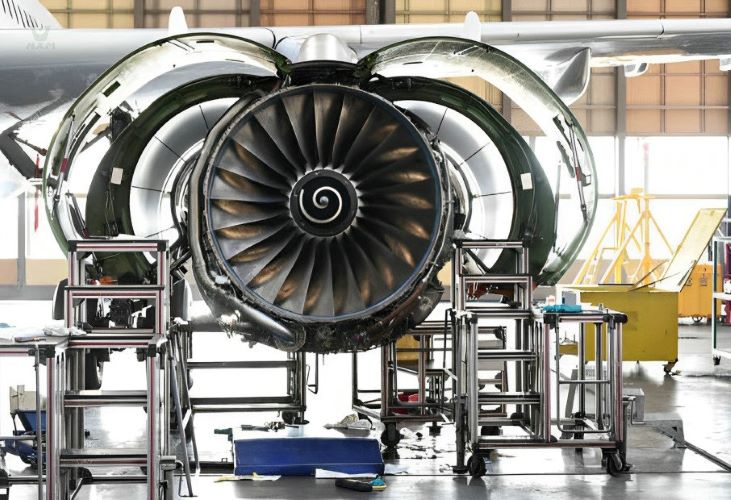
Aerospace and Aviation
Stainless steel round bars play a critical role in the aerospace and aviation industry, where precision and durability are paramount. They are used in aircraft engine blades, engine casings, fasteners, combustion chamber components, disks, and shafts, ensuring the reliability and safety of aviation equipment.
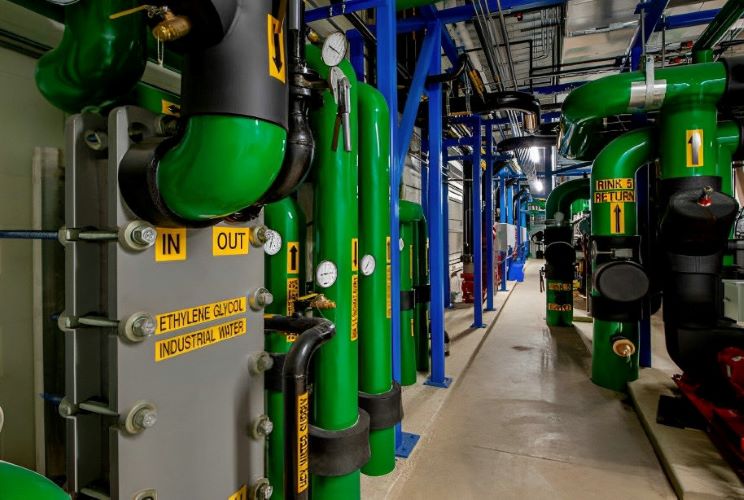
Rocketry and Propulsion
Stainless steel round bars are essential components in the field of rocketry and propulsion. They find applications in liquid oxygen kerosene engines, projectiles, and propulsion devices, where their high strength and resistance to extreme conditions are crucial.
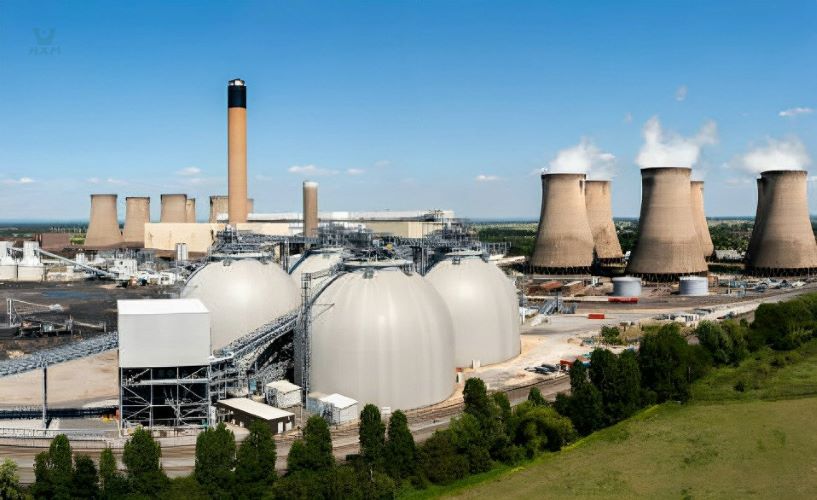
Nuclear Energy
Stainless steel round bars are employed in the nuclear energy sector due to their resistance to radiation and high-temperature environments. They contribute to the construction of nuclear energy equipment and critical components.
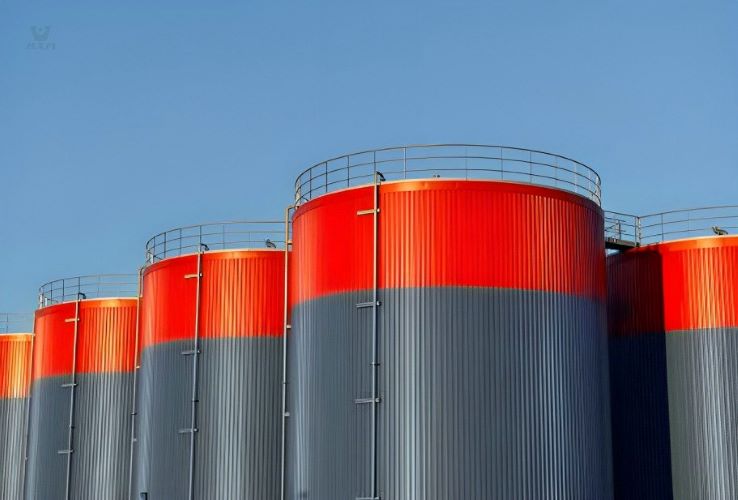
Petroleum and Chemical Industry
The petroleum and chemical industry relies on stainless steel round bars for their resistance to corrosion in aggressive chemical environments. They are used to manufacture equipment and components vital for these sectors.
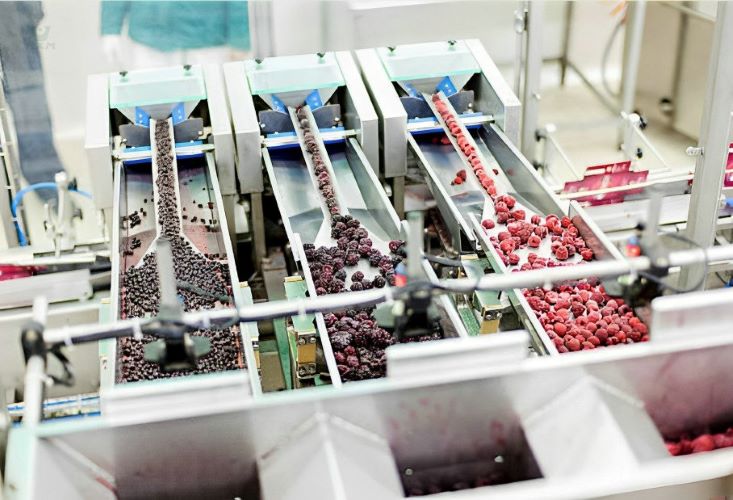
Food Industry
In the food industry, stainless steel round bars are favored for their corrosion resistance and hygienic properties. They are commonly used in food processing equipment, ensuring the safety and quality of food products.
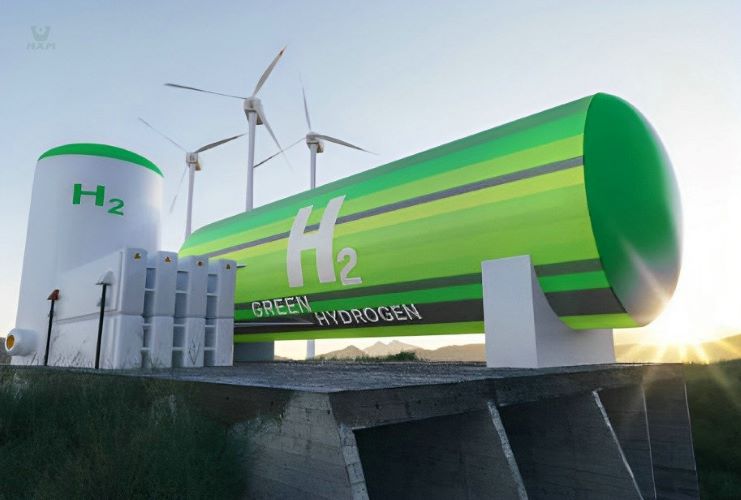
Environmental Protection
Stainless steel round bars play a role in environmental protection technologies, where their durability and resistance to harsh conditions are harnessed for various applications aimed at safeguarding the environment.
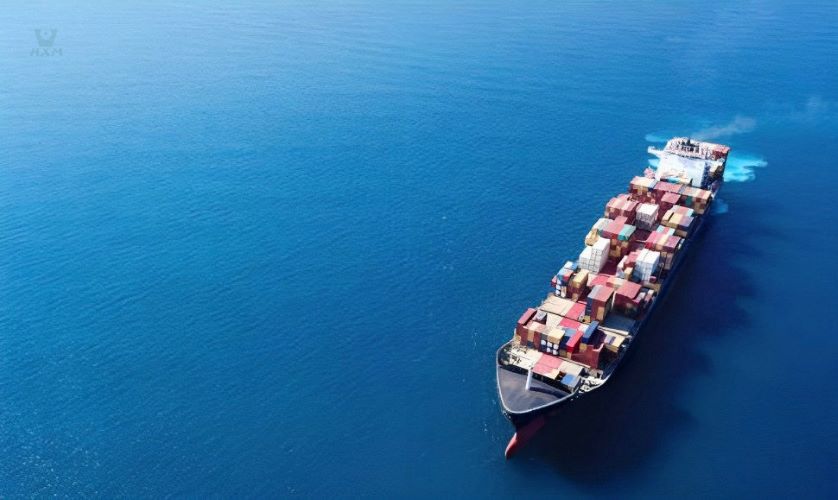
Marine Development
Marine environments are notoriously corrosive, making stainless steel bars a top choice for marine development projects. They are used in marine equipment and structures exposed to seawater, ensuring longevity and reliability.
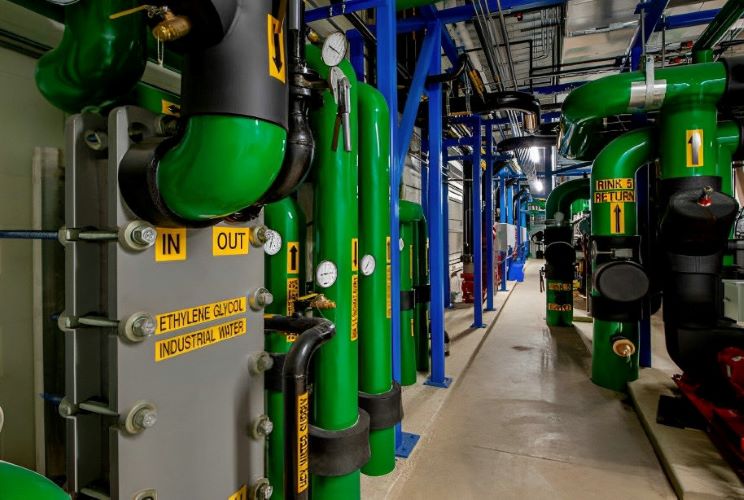
Boiler Heat Exchangers
Stainless steel bars find application in boiler heat exchangers, where they excel at withstanding high temperatures and providing efficient heat transfer in various industrial processes.
FAQ
The typical specifications and sizes of stainless steel round bars are determined by industry standards and specific project requirements. Stainless steel round bars are available in a variety of grades, including 304, 316, 410, and others, each with its own chemical composition and mechanical properties.
These bars come in standard diameters ranging from 1/16 inch to 24 inches or more, with common sizes being 1/4 inch, 1/2 inch, 3/4 inch, 1 inch, and increments of 1/4 inch thereafter. The length of stainless steel round bars typically ranges from 12 feet to 20 feet, but custom lengths can be provided as needed.
Specifications also include surface finishes like bright, polished, or rough, depending on the intended application. Tolerances are specified to ensure precision, often ranging from ±0.005 inches to ±0.03 inches, depending on the diameter and grade.
It’s important to consult with a reputable stainless steel bar supplier to determine the exact specifications and sizes that meet your project’s requirements and industry standards.
Stainless steel round bars offer several advantages:
Corrosion Resistance: Stainless steel round bars exhibit exceptional resistance to corrosion, making them suitable for a wide range of environments, including marine and chemical applications.
High Strength: They possess high tensile and yield strength, providing structural integrity and reliability in various industries.
Durability: Stainless steel’s durability ensures a long service life, reducing maintenance and replacement costs.
Temperature Resistance: These bars maintain their properties across a wide temperature range, making them suitable for extreme conditions.
Versatility: Stainless steel round bars come in various grades and sizes, offering versatility for different applications.
Aesthetic Appeal: They have a sleek and modern appearance, often chosen for architectural and decorative purposes.
Recyclability: Stainless steel is recyclable, contributing to sustainability and environmental responsibility.
Consulting a reputable stainless steel bar supplier can help you leverage these advantages for your specific project requirements.
Choosing the right stainless steel round bar for your project involves considering several factors:
Grade Selection: Determine the grade that suits your application, considering factors like corrosion resistance, temperature requirements, and mechanical properties.
Size and Dimensions: Select the appropriate diameter and length based on your project’s specifications and design requirements.
Surface Finish: Decide on the desired surface finish (e.g., polished, brushed, or mill finish) based on aesthetic and functional considerations.
Tolerance and Precision: Consider the required tolerance and precision for your project, which can vary depending on the application.
Application-Specific Features: Identify any unique features or properties needed for your project, such as high-temperature resistance or specific certifications.
Supplier Expertise: Consult a reputable stainless steel bar supplier with expertise in various industries to get guidance and recommendations.
By carefully evaluating these factors, you can make an informed choice and ensure that the selected stainless steel round bar meets the specific needs of your project.
The manufacturing process for stainless steel round bars involves several key steps:
Raw Material Selection: High-quality raw materials, including iron ore, chromium, nickel, and other alloying elements, are carefully chosen to meet the required specifications.
Melting: The selected raw materials are melted in an electric arc furnace, induction furnace, or AOD (Argon Oxygen Decarburization) converter to create molten stainless steel.
Casting: The molten stainless steel is cast into round billets or blooms using continuous casting or ingot casting methods.
Hot Rolling: The cast billets or blooms are heated and passed through a series of rolling mills to reduce their diameter and shape them into round bars. This process is known as hot rolling and helps achieve the desired size and mechanical properties.
Heat Treatment: To enhance the mechanical properties and eliminate internal stresses, the hot-rolled stainless steel bars undergo a heat treatment process. This typically involves annealing, quenching, and tempering.
Cold Drawing (Optional): In some cases, cold drawing may be performed to further refine the dimensions and surface finish of the stainless steel round bars.
Finishing: The bars are then finished by cutting to the required lengths and achieving the desired surface finish, which can range from mill finish to polished or brushed surfaces.
Inspection and Testing: Stringent quality control measures, including ultrasonic testing, visual inspection, and mechanical property testing, are conducted to ensure the bars meet industry standards and customer specifications.
Packaging and Delivery: The finished stainless steel round bars are packaged securely and delivered to customers, ready for use in various applications.
It’s essential to choose a reputable stainless steel bar supplier with a proven track record in quality control and adherence to industry standards to ensure you receive high-quality round bars for your specific project requirements.
Yes, stainless steel round bars are weldable, and there are several welding methods commonly used to join them, depending on the specific grade and application requirements. Some of the most common welding methods for stainless steel round bars include:
Shielded Metal Arc Welding (SMAW): Also known as stick welding, SMAW uses a flux-coated electrode to create an electric arc between the electrode and the workpiece. It’s a versatile method suitable for various stainless steel grades.
Gas Tungsten Arc Welding (GTAW): GTAW, or TIG (Tungsten Inert Gas) welding, employs a non-consumable tungsten electrode and an inert gas shield (usually argon) to create a precise, high-quality weld. It’s ideal for thin stainless steel round bars and produces clean welds.
Gas Metal Arc Welding (GMAW): GMAW, or MIG (Metal Inert Gas) welding, uses a consumable wire electrode and an inert gas shield, typically a mixture of argon and CO2. It’s suitable for a wide range of stainless steel grades and is relatively easy to automate for high-volume production.
Flux-Cored Arc Welding (FCAW): FCAW is similar to GMAW but uses a tubular wire electrode with a flux core. It’s often used for stainless steel round bars in thicker sections, as it provides deeper penetration and higher deposition rates.
Submerged Arc Welding (SAW): SAW is a highly efficient welding method that involves feeding a continuous wire electrode beneath a layer of granular flux. It’s commonly used for welding thicker stainless steel round bars and offers excellent weld quality.
Resistance Spot Welding: This method is used for thin stainless steel round bars and involves applying pressure and electrical current at specific points to create welds. It’s often used in manufacturing applications.
The choice of welding method depends on factors such as the stainless steel grade, thickness, joint design, and the desired weld quality. It’s essential to follow recommended welding procedures and select the appropriate filler material to ensure strong, durable, and corrosion-resistant welds in stainless steel round bars. Consulting with a qualified welding engineer or a reputable stainless steel bar supplier can help determine the best welding method for your specific application.
The price range for stainless steel round bars can vary significantly depending on various factors such as the grade of stainless steel, size, finish, quantity, and market conditions. Generally, stainless steel round bars are priced based on their weight, with higher grades and specialty finishes commanding higher prices.
As of my last knowledge update in September 2021, here’s a rough price range:
Standard Grades (e.g., 304, 316): These are some of the most common stainless steel grades and are usually more affordable. Prices can range from $1.50 to $5.00 per pound (lb) or more, depending on size and finish.
Specialty Grades (e.g., 17-4 PH): Specialty grades with unique properties can be more expensive. Prices can vary widely but may range from $6.00 to $15.00 per pound or higher.
Large Diameter Bars: Larger diameter stainless steel round bars can be more expensive due to increased material costs and manufacturing complexities. Prices can range from $5.00 to $20.00 per pound or more.
High-Quality Finishes: Stainless steel round bars with high-quality finishes like mirror-polished or precision-ground surfaces are typically more costly, and prices can vary widely.
Bulk Orders: Bulk orders or large quantities often receive discounts, which can affect the per-pound price.
Market Fluctuations: Stainless steel prices can be influenced by market conditions, including fluctuations in raw material costs and supply-demand dynamics.
Please note that these prices are approximate and can change over time. It’s essential to request a current and specific price quote from a reputable stainless steel bar supplier based on your project’s requirements and the prevailing market conditions. Additionally, factors like transportation costs and any additional processing (cutting, heat treatment, etc.) can also impact the final cost.
Machining and cutting stainless steel round bars require precision and the use of suitable tools and techniques. Different methods are employed based on the specific requirements of a project. Here are some common machining and cutting methods for stainless steel round bars:
Turning: Turning is a machining process where a lathe is used to rotate the round bar while a cutting tool removes material from its surface. This process is effective for achieving precise dimensions and smooth finishes.
Drilling: Drilling involves creating holes in the round bar using specialized drill bits. Coolants are often used to reduce heat and extend tool life during drilling.
Milling: Milling machines use rotary cutters to remove material from the round bar’s surface. This method is versatile and can be used for creating various shapes and features.
Grinding: Grinding is employed to achieve high surface precision and smoothness. It’s commonly used for achieving fine finishes on stainless steel round bars.
Sawing: Abrasive saws or band saws can be used for cutting stainless steel round bars to the desired length. This method is efficient for bulk cutting but may result in a less precise finish.
Shearing: Shearing involves the use of heavy-duty shears to cut stainless steel bars into smaller sections. It’s a quick and efficient method for basic cutting needs.
Waterjet Cutting: Waterjet cutting uses a high-pressure stream of water mixed with abrasive particles to cut through stainless steel bars. It’s suitable for achieving complex shapes and intricate designs.
Laser Cutting: Laser cutting utilizes a high-powered laser beam to melt and vaporize the stainless steel, cutting it with precision. This method is ideal for intricate shapes and fine details.
Plasma Cutting: Plasma cutting involves using a high-temperature plasma arc to melt through stainless steel. It’s effective for cutting thick bars quickly.
Electrical Discharge Machining (EDM): EDM uses electrical discharges to remove material from the stainless steel round bar. It’s useful for cutting hardened or heat-treated stainless steel.
Stainless steel bar suppliers often offer additional services like custom cutting and machining to meet specific project requirements. When choosing a method, factors such as the required precision, material thickness, and the complexity of the cuts should be considered. Consulting with a qualified supplier can help determine the most suitable method for your needs.
other products
Get In touch
Ready to Elevate Your Projects? Dive into our Stainless Steel Collection and Submit Your Specifications Today!
Phone/WhatsApp/WeChat:
+86 13052085117
Email: [email protected]
Address: RM557, NO.1388 Jiangyue Road, Shanghai China