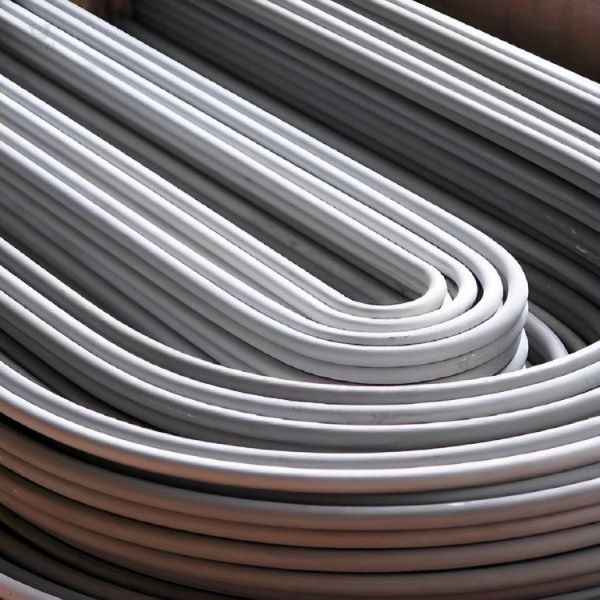
Stainless Steel U Tube Supplier
ASTM A 182 F304/304L, F316/316L, F316H, F310, F321, F904L, F44 (UNS S31254) etc.
Stainless steel U tubes are widely used in heat exchanger systems. Heat exchange equipment based on seamless stainless steel U shaped tubes and welded stainless steel U tubes is indispensable in the key
field of strategic importance – nuclear and petrochemical machinery manufacturing.
Product Description of Stainless Steel U Tube
Stainless Steel U Tubes are precisely bent into U-shaped configurations, commonly employed in heat exchanger systems. Available in a range of sizes and grades, including 316/316L stainless steel, these tubes are meticulously crafted using specialized bending equipment, tailored to match customer-provided blueprints and specifications. The seamless SS U tubes find extensive utility in heat exchange systems, finding prominence in the assembly of high-pressure heaters and low-pressure feedwater heaters within large-scale thermal power plants. Characterized by their small diameter, thin walls, and extraordinary length, U tubes play a pivotal role in maximizing heat transfer efficiency. Their unique design allows for effective exchange of thermal energy, serving as a fundamental component in the energy generation process. The combination of exceptional craftsmanship, corrosion-resistant stainless steel, and precision bending ensures these U tubes offer robust performance in demanding industrial applications. With their intricate shape and specialized manufacturing, stainless steel U tubes contribute to the seamless operation of vital systems across a diverse array of sectors, ensuring efficient heat exchange and energy optimization.
specification of Stainless Steel U Tube
Production Standard of Stainless Steel U Tube
ASTM A312, JIS G3459, GB/T 12771, EN 10217-7, etc.
Production Range of Stainless Steel U Tube
Normal Pipe Size | Outside Diameter | Normal Wall Thickness (mm) | |||||
NPS | in | BN | mm | SCH5s | SCH10s | SCH40s | SCH80s |
1/8 | 0.405 | 6 | 10.3 | — | 1.24 | 1.73 | 2.41 |
1/4 | 0.540 | 8 | 13.7 | — | 1.65 | 2.24 | 3.02 |
3/8 | 0.675 | 10 | 17.1 | — | 1.65 | 2.31 | 3.2 |
1/2 | 0.840 | 15 | 21.3 | 1.65 | 2.11 | 2.77 | 3.73 |
3/4 | 1.050 | 20 | 26.7 | 1.65 | 2.11 | 2.87 | 3.91 |
1 | 1.315 | 25 | 33.4 | 1.65 | 2.77 | 3.38 | 4.55 |
1 1/4 | 1.660 | 32 | 42.2 | 1.65 | 2.77 | 3.56 | 4.85 |
1 1/2 | 1.900 | 40 | 48.3 | 1.65 | 2.77 | 3.68 | 5.08 |
2 | 2.375 | 50 | 60.3 | 1.65 | 2.77 | 3.91 | 5.54 |
2 1/2 | 2.875 | 65 | 73.0 | 2.11 | 3.05 | 5.16 | 7.01 |
3 | 3.500 | 80 | 88.9 | 2.11 | 3.05 | 5.49 | 7.62 |
3 1/2 | 4.000 | 90 | 101.6 | 2.11 | 3.05 | 5.74 | 8.08 |
4 | 4.500 | 100 | 114.3 | 2.11 | 3.05 | 6.02 | 8.56 |
5 | 5.563 | 125 | 141.3 | 2.77 | 3.4 | 6.55 | 9.53 |
6 | 6.625 | 150 | 168.3 | 2.77 | 3.4 | 7.11 | 10.97 |
8 | 8.625 | 200 | 219.1 | 2.77 | 3.76 | 8.18 | 12.7 |
10 | 10.750 | 250 | 273.1 | 3.4 | 4.19 | 9.27 | 12.7 |
12 | 12.750 | 300 | 323.9 | 3.96 | 4.57 | 9.53 | 12.7 |
14 | 14.000 | 350 | 355.6 | 3.96 | 4.78 | 9.53 | — |
16 | 16.000 | 400 | 406.4 | 4.19 | 4.78 | 9.53 | — |
18 | 18.000 | 450 | 457.2 | 4.19 | 4.78 | 9.53 | — |
20 | 20.000 | 500 | 508.0 | 4.78 | 5.54 | 9.53 | — |
22 | 22.000 | 550 | 558.8 | 4.78 | 5.54 | — | — |
24 | 24.000 | 600 | 609.6 | 5.54 | 6.35 | 9.53 | — |
26 | 26.000 | 650 | 660.4 | — | — | — | — |
28 | 28.000 | 700 | 711.2 | — | — | — | — |
30 | 30.000 | 750 | 762.0 | 6.35 | 7.92 | — | — |
32 | 32.000 | 800 | 812.8 | — | 7.92 | — | — |
34 | 34.000 | 850 | 863.6 | — | 7.92 | — | — |
36 | 36.000 | 900 | 914.4 | — | 7.92 | — | — |
38 | 38.000 | 950 | 965.2 | — | — | — | — |
40 | 40.000 | 1000 | 1016.0 | — | 9.53 | — | — |
If you need more sizes, please consult with us |
Product Description of Stainless Steel U Tube
The characteristic of “Precision Bent Design” refers to the meticulous and accurate bending process employed in the creation of Stainless Steel U Tubes. These tubes are skillfully shaped into U-shaped configurations using specialized bending equipment and techniques. The precision bending process ensures that each tube maintains a consistent and uniform U shape, meeting specific dimensional and geometric requirements.
The precision bent design is crucial for several reasons:
The accuracy of the U shape is essential for the effective functioning of the U tubes in heat exchange systems. A precisely bent U tube ensures that heat transfer occurs efficiently between the fluids within the tube, enhancing the overall performance of the heat exchanger.
The precise bending minimizes the risk of gaps or inconsistencies that could lead to leakage. This is particularly important in applications involving corrosive or high-pressure fluids.
A uniform U shape ensures uniform flow distribution and heat exchange across the tube’s length. This contributes to maintaining consistent fluid temperatures and efficient energy transfer.
Accurate bending reduces stress concentrations and the potential for material fatigue, enhancing the longevity of the U tubes and minimizing the risk of premature failures.
The precision bending process allows for customization according to specific project requirements. Whether it’s meeting specific dimensions or accommodating unique installation constraints, precision bending ensures tailored solutions.
The precision bent design is a hallmark of quality and craftsmanship. Tubes that undergo precise bending are subjected to strict quality control measures to ensure they meet industry standards and customer expectations.
In summary, the “Precision Bent Design” characteristic underscores the importance of accuracy and attention to detail in the fabrication of Stainless Steel U Tubes. This level of precision ensures optimal performance, reliability, and durability, making these tubes vital components in various heat exchange applications across industries.
application of Stainless Steel U Tube
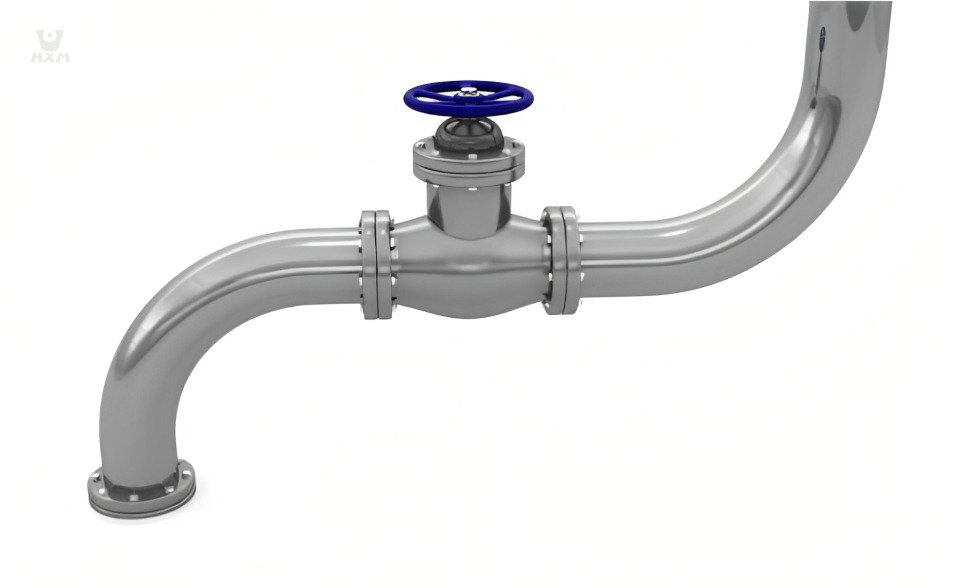

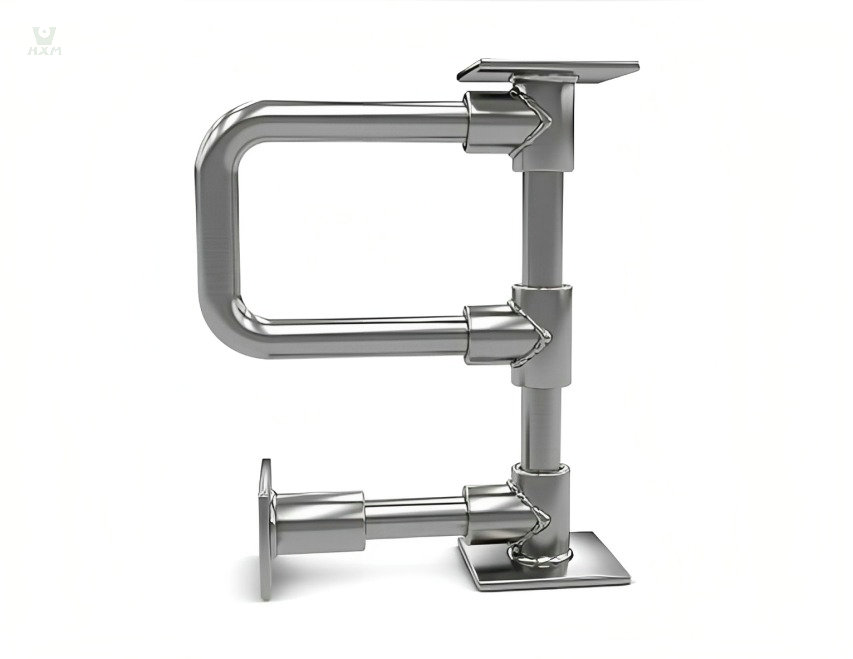
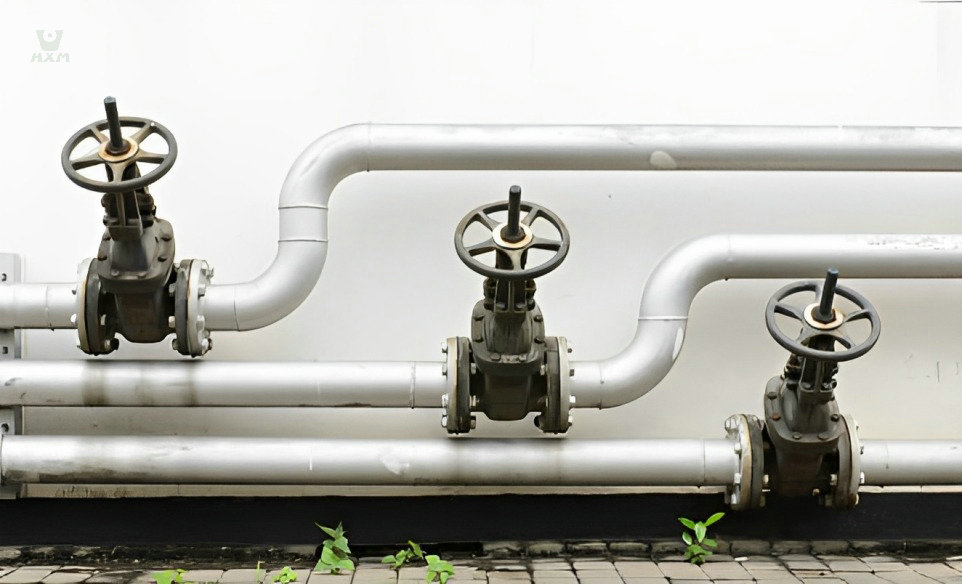
Stainless Steel U Tubes are crucial components in heat exchanger systems, where they play a vital role in facilitating efficient heat transfer between two fluids. The unique U-shaped design of these tubes enhances their ability to perform this crucial function, making them indispensable in various industrial applications.
Fluid-to-Fluid Heat Exchange: In a typical heat exchanger, two fluids flow through separate pathways within the U tube. One fluid, often a hot fluid, transfers its heat to the outer surface of the tube, while the other fluid, usually cooler, absorbs the heat from the tube’s surface. This fluid-to-fluid heat exchange enables effective temperature regulation, energy recovery, and various thermal processes.
Stainless Steel U Tubes find extensive use in diverse industries. In power plants, they are utilized in boilers and condensers to manage high temperatures and pressures. Chemical processing plants utilize U tubes for various chemical reactions requiring controlled temperature conditions. HVAC systems benefit from U tubes to regulate air temperature, while oil refineries employ them for heating and cooling processes.
Stainless steel’s innate corrosion resistance makes U tubes ideal for heat exchangers that handle corrosive fluids or operate in challenging environments. This characteristic ensures the tubes’ longevity and reliability over time.
FAQ
Stainless steel U tubes are meticulously crafted to achieve their distinctive U-shaped design, ensuring optimal performance in various applications. Here’s a comprehensive outline of the manufacturing process, highlighting the essential steps involved:
- Material Selection: High-quality stainless steel, often grades like 304 or 316, is chosen for its exceptional corrosion resistance and mechanical properties. These seamless tubes form the base material for U tube fabrication.
- Precision Tube Bending: The selected stainless steel tubes undergo precision tube bending, a critical step to achieve the desired U shape. Specialized bending machinery, operated by skilled technicians, ensures accurate shaping without compromising tube integrity.
- Cold or Hot Bending: Tube bending can be performed using either cold or hot methods. Cold bending is conducted at ambient temperatures, while hot bending involves heating the tubes prior to shaping, allowing for tighter radii and more intricate designs.
- Custom Radii and Dimensions: Depending on the application, specific bend radii and dimensions are tailored to meet the project’s requirements, ensuring seamless integration within existing systems.
- Heat Treatment: Some U tubes may undergo heat treatment processes, such as annealing, to relieve stress and optimize mechanical properties. This step enhances tube longevity and structural integrity.
- Surface Finishing: Surface treatments like pickling and passivation may be applied to enhance corrosion resistance and eliminate impurities, ensuring the tubes meet industry standards.
- Stringent Quality Checks: Each stage of the manufacturing process is subjected to rigorous quality inspections. Dimensional accuracy, shape conformity, and material integrity are carefully verified to meet stringent specifications.
- Final Testing: Prior to shipment, U tubes undergo final testing to ensure their performance under varying conditions. Hydrostatic or pneumatic pressure tests may be conducted to verify their strength and leak-free operation.
- Packaging and Distribution: After successful testing, the stainless steel U tubes are meticulously packaged to prevent damage during transit. They are then shipped to customers, ready for installation.
By adhering to this meticulous manufacturing process, stainless steel U tubes are crafted with precision, offering exceptional strength, corrosion resistance, and dimensional accuracy. This ensures their reliability in diverse applications, from heat exchangers to pressure vessels. To obtain the highest quality U tubes, partnering with reputable stainless steel pipe suppliers is crucial to ensure consistent performance and durability.
Stainless steel U tubes play a pivotal role in the efficiency and reliability of heat exchanger systems, making them indispensable components in various industrial applications. Here’s an in-depth exploration of their significance:
Optimized Heat Transfer: The U-shaped design of stainless steel U tubes is specifically engineered to maximize heat transfer efficiency. This configuration enhances the surface area available for heat exchange, enabling rapid and effective thermal energy transfer between fluids.
Corrosion Resistance: Stainless steel’s inherent corrosion resistance is a paramount advantage in heat exchanger systems. U tubes made from high-quality stainless steel, such as 316 or 304 grades, are well-equipped to withstand corrosive environments, ensuring prolonged operational lifespan and reduced maintenance needs.
Versatile Applications: Stainless steel U tubes find application in both industrial and commercial sectors, including chemical processing, HVAC systems, power generation, and more. Their adaptability to diverse operating conditions makes them a reliable choice for various industries.
Reliability Under Pressure: Heat exchanger systems often operate under varying pressures. The robust construction of stainless steel U tubes ensures their integrity, preventing leakages and maintaining system stability even in high-pressure environments.
Temperature Resistance: Heat exchangers frequently encounter extreme temperatures. Stainless steel U tubes possess exceptional temperature resistance, allowing them to efficiently transfer heat across a wide range of thermal conditions.
Low Maintenance: The corrosion resistance and durability of stainless steel U tubes contribute to reduced maintenance requirements. This translates to extended service life, minimized downtime, and lower operational costs.
Energy Efficiency: Efficient heat transfer facilitated by U tubes contributes to enhanced energy efficiency within heat exchanger systems. This results in reduced energy consumption and operational expenses.
Customization: Stainless steel U tubes can be customized in terms of dimensions, materials, and bending radii to suit specific project requirements. This adaptability ensures seamless integration within existing systems.
Stringent Standards: In critical applications such as chemical processing and power generation, compliance with industry standards is imperative. Stainless steel U tubes, provided by reputable stainless steel pipe suppliers, are manufactured to meet stringent quality and performance criteria.
In summary, stainless steel U tubes are vital components that facilitate optimal heat transfer, corrosion resistance, and reliability within heat exchanger systems. Their ability to withstand demanding conditions while delivering efficient thermal performance makes them a fundamental choice in diverse industrial settings. Collaborating with trusted stainless steel pipe suppliers ensures access to high-quality U tubes, contributing to the overall effectiveness and longevity of heat exchanger systems.
Stainless steel U tubes are primarily crafted from corrosion-resistant stainless steel alloys renowned for their exceptional mechanical properties and durability. These alloys offer an ideal balance of strength, corrosion resistance, and thermal conductivity, making them a preferred choice for U tube fabrication. The material composition predominantly consists of:
Chromium (Cr): A key component, chromium provides stainless steel with its corrosion-resistant properties. The formation of a passive oxide layer on the surface of the steel enhances its ability to resist chemical reactions and rust.
Nickel (Ni): Nickel contributes to the alloy’s resistance to both corrosion and high temperatures. It also enhances the material’s ductility, facilitating the U-bending process during fabrication.
Molybdenum (Mo): Molybdenum further enhances corrosion resistance, particularly in harsh environments containing chloride ions or sulfur compounds.
Other Alloying Elements: Depending on the specific grade, stainless steel U tubes may contain other alloying elements such as manganese, silicon, and nitrogen. These elements can influence the material’s mechanical properties and performance in various conditions.
Stainless steel U tubes are available in different grades, with 316 and 304 being common choices. Grade 316 stainless steel, for instance, is known for its exceptional resistance to both corrosion and pitting, making it suitable for demanding applications, including those involving exposure to corrosive chemicals or marine environments.
Collaboration with reputable stainless steel pipe suppliers ensures access to U tubes made from high-quality stainless steel alloys that adhere to industry standards. These suppliers provide materials that undergo rigorous testing and quality checks, assuring the integrity and reliability of the stainless steel U tubes for heat exchanger systems and various industrial applications.
Choosing the right size for stainless steel U tubes involves careful consideration of various factors to ensure optimal performance and compatibility within heat exchanger systems. The following steps outline the process:
- System Requirements: Understand the specific requirements of the heat exchanger system, including the intended fluid flow rates, temperature ranges, and pressure levels. These parameters will influence the size and diameter of the U tubes needed.
- Heat Transfer Needs: Calculate the required heat transfer capacity of the heat exchanger. The size of the U tubes should allow for efficient heat exchange between the fluids while maintaining suitable flow rates.
- Geometry and Bending Radius: The U tube’s geometry, including the bending radius, determines its compatibility with the available space within the heat exchanger. Collaborate with stainless steel pipe suppliers to ensure the chosen U tube size can be accurately fabricated while meeting the system’s constraints.
- Material Compatibility: Ensure the selected stainless steel U tube size is made from an alloy that is compatible with the fluids and environmental conditions within the heat exchanger system. Different alloys offer varying levels of corrosion resistance and thermal conductivity.
- Supplier Consultation: Engage with reputable stainless steel pipe suppliers who specialize in U tube fabrication. Their expertise can guide you in selecting the appropriate size based on your system’s requirements, ensuring a seamless integration of the U tubes.
- Industry Standards: Adhere to industry standards and guidelines for sizing and selecting U tubes for heat exchanger applications. Stainless steel pipe suppliers well-versed in these standards can provide valuable insights.
By collaborating closely with experienced stainless steel pipe suppliers, you can confidently choose the right size for your stainless steel U tubes, ensuring efficient heat exchange, durability, and long-term performance within heat exchanger systems.
Proper maintenance of stainless steel U tubes is crucial to ensure their longevity, performance, and integrity within heat exchanger systems. Follow these detailed steps for effective maintenance:
- Regular Inspection: Conduct routine visual inspections to identify signs of corrosion, pitting, or mechanical damage on the U tubes’ surfaces. Address any issues promptly to prevent further deterioration.
- Cleaning: Clean the U tubes periodically to remove debris, fouling, and deposits that can hinder heat transfer efficiency. Use appropriate cleaning agents that are compatible with stainless steel and the fluids within the system.
- Corrosion Protection: Apply corrosion-resistant coatings or paints to the external surfaces of the U tubes to provide an additional layer of protection against environmental factors. Consult stainless steel pipe suppliers for suitable coating options.
- Fluid Analysis: Regularly analyze the fluids circulating through the heat exchanger system to monitor for potential corrosive elements or contaminants. Adjust the maintenance schedule based on fluid analysis results.
- Passivation: Perform passivation treatments on the U tubes’ internal surfaces to enhance their corrosion resistance. This process removes free iron and forms a protective oxide layer.
- Tube Supports: Ensure proper tube supports and clamps are in place to prevent vibration-induced wear or damage to the U tubes. Improper support can lead to premature failure.
- Documentation: Maintain detailed records of maintenance activities, inspections, repairs, and any issues encountered. This documentation aids in tracking the U tubes’ condition over time and planning future maintenance.
- Supplier Guidance: Collaborate with reputable stainless steel pipe suppliers for maintenance recommendations specific to the U tubes’ material and application. They can provide valuable insights into best practices for upkeep.
- Emergency Response: Have a contingency plan in place for addressing any unexpected failures or leaks in the U tubes. Quick response and repair can minimize downtime and prevent further damage.
- Training: Train maintenance personnel on proper handling, cleaning procedures, and maintenance protocols for stainless steel U tubes to ensure consistent and effective upkeep.
By adhering to these maintenance guidelines and seeking guidance from experienced stainless steel pipe suppliers, you can maximize the lifespan and performance of your stainless steel U tubes in heat exchanger systems.
Stainless steel U tubes are well-suited for high pressure and high-temperature applications due to their robust material properties and precision manufacturing. These tubes, often made from corrosion-resistant stainless steel grades, are designed to withstand the challenging conditions encountered in various industrial sectors. Here’s a detailed explanation of their suitability:
- Material Resilience: Stainless steel, renowned for its exceptional mechanical properties and resistance to corrosion, is a preferred choice for U tubes in demanding environments. Grades like 316/316L stainless steel offer enhanced corrosion resistance and thermal stability.
- Pressure Endurance: U tubes are designed and manufactured to handle elevated pressures. Their seamless construction and precision bending ensure uniform wall thickness and structural integrity, allowing them to withstand the stresses imposed by high-pressure fluids.
- Temperature Resistance: Stainless steel U tubes can operate effectively at elevated temperatures. The choice of stainless steel grade depends on the specific temperature range. For example, 316/316L stainless steel can handle temperatures ranging from cryogenic levels up to approximately 870°C (1600°F).
- Thermal Expansion: U tubes are able to accommodate thermal expansion and contraction without compromising their integrity. This is particularly crucial in high-temperature applications where temperature fluctuations are common.
- Heat Exchangers: U tubes find extensive use in heat exchanger systems, where they facilitate efficient heat transfer between fluids at varying temperatures. In applications like power plants, chemical processing, and petrochemical industries, U tubes play a pivotal role in maintaining operational efficiency.
- Precision Bending: The precise bending of U tubes ensures minimal stress concentrations and maintains uniform wall thickness, vital for withstanding the pressures and temperatures encountered in demanding conditions.
- Supplier Expertise: Reputable stainless steel pipe suppliers can recommend suitable grades based on the specific pressure and temperature requirements of your application. Their expertise ensures that you select the right stainless steel U tubes for optimal performance and longevity.
In conclusion, stainless steel U tubes are engineered to excel in high-pressure and high-temperature scenarios. With their material resilience, precision manufacturing, and ability to handle thermal expansion, they contribute to the reliability and efficiency of various industrial systems. Consult trusted stainless steel pipe suppliers to ensure that the selected U tubes are tailored to your application’s exacting demands.
other products
Get In touch
Ready to Elevate Your Projects? Dive into our Stainless Steel Collection and Submit Your Specifications Today!
Phone/WhatsApp/WeChat:
+86 13052085117
Email: [email protected]
Address: RM557, NO.1388 Jiangyue Road, Shanghai China