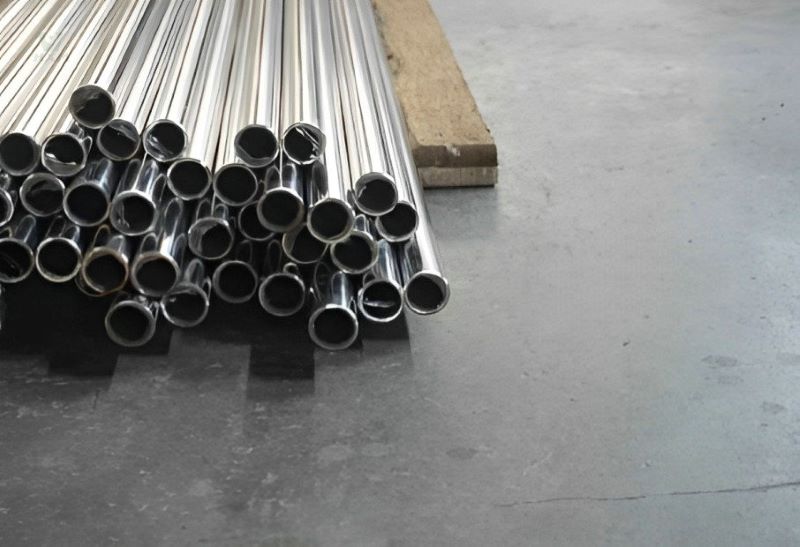
2507 Duplex Stainless Steel Welded Tube Suppliers
-
Specification: Alloy 2507 Super Duplex Tubing, ASTM A789 UNS S32750 Super Duplex 2507, ASTM A789 Super Duplex Steel SAF 2507 Tube, UNS S32750, 2507 Super Duplex Steel Pipes, super duplex • uns s32750 • wnr 1.4410
-
Size Range: From 4mm to 800mm
-
Wall Thickness Range: From 1mm to 150mm (SCH10-XXS)
-
Length Options: 4000mm, 5800mm, 6000mm, 12000mm, or as required.
-
Finish: 2B, BA,4K,8K, NO.1,2D,3#, HL
-
Type: Round, square, rectangular, hexagonal, flat, angle
-
Technique: Cold rolled, hot rolled
-
Payment method: T/T, LC
-
Price: Inquiry Now
Product Description Of 2507 Duplex Stainless Steel Welded Tube
Chemical Components Of 2507 Duplex Stainless Steel Welded Tube
2507 | C% | Si% | Mn% | P% | S% | Ni% | Cr% | Mo% | N |
ASTM | ≤ 0.03 | ≤ 0.8 | ≤ 1.2 | ≤ 0.035 | ≤ 0.02 | 6.0-8.0 | 24.0-26.0 | 3.0-5.0 | 0.24-0.32 |
EN | ≤ 0.03 | ≤ 1.00 | ≤ 2.00 | ≤ 0.035 | ≤ 0.015 | 6.0-8.0 | 24.0-26.0 | 3.0-5.0 | 0.20-0.30 |
JIS | ≤ 0.03 | ≤ 1.00 | ≤ 1.2 | ≤ 0.035 | ≤ 0.02 | 6.0-8.0 | 11.5-14.5 | 3.0-5.0 | 0.24-0.32 |
GB | ≤ 0.03 | ≤ 0.08 | ≤ 1.2 | ≤ 0.035 | ≤ 0.02 | 6.0-8.0 | 24.0-26.0 | 3.0-5.0 | 0.20-0.32 |
Mechanical Properties Of 2507 Duplex Stainless Steel Welded Tube
2507 | Y.S./Mpa ≥ | T.S./Mpa ≥ | E.L./% ≥ | HB ≤ | HRB ≤ | HBW ≤ | HV ≤ |
ASTM | 550 | 795 | 15 | 310 | 32 | 310 | 320 |
JIS | 550 | 800 | 15 | 290 | 32 | 310 | 320 |
GB | 550 | 800 | 15 | 290 | 32 | 310 | 320 |
Product Description Of 2507 Duplex Stainless Steel Welded Tube
Experience the strength and corrosion resistance of 2507 Duplex Stainless Steel Welded Tubes. Designed for demanding applications like chemical processing, petrochemicals, and marine equipment, this super duplex alloy boasts excellent chloride stress corrosion cracking resistance, high thermal conductivity, and low thermal expansion. With its high chromium, molybdenum, and nitrogen content, it offers exceptional pitting, crevice corrosion, and general corrosion resistance. The dual-phase structure ensures remarkable chloride stress corrosion cracking resistance. Please note that 2507 usage is recommended below 600°F (316°C) to maintain toughness and corrosion resistance. Its outstanding mechanical properties often allow achieving design strength using lighter gauge material, reducing overall manufacturing costs.
Features Of 2507 Duplex Stainless Steel Welded Tube
Experience unparalleled corrosion resistance with 2507 Duplex Stainless Steel Welded Tubes. Featuring a high chromium and nickel content, these tubes exhibit exceptional resistance to corrosive environments, including chlorides and acids. Their dual-phase structure ensures prolonged durability against pitting, crevice, and stress corrosion cracking, making them a reliable choice for demanding applications in harsh conditions.
Benefit from exceptional strength with 2507 Duplex Stainless Steel Welded Tubes. Comprising 25% chromium, 4% molybdenum, and 7% nickel, these tubes offer superior mechanical properties, making them ideal for applications requiring both structural integrity and corrosion resistance. Their dual-phase structure contributes to higher tensile and yield strengths compared to conventional stainless steels, ensuring reliable performance in demanding environments.
Experience unparalleled resistance to chloride stress corrosion cracking with 2507 Duplex Stainless Steel Welded Tubes. Thanks to their high chromium, molybdenum, and nitrogen content, these tubes exhibit exceptional resilience against the detrimental effects of chloride-rich environments. Their dual-phase structure further enhances their ability to withstand the corrosive challenges posed by chloride stress, making them a reliable choice for critical applications in harsh conditions.
Benefit from remarkable resistance to crevice and pitting corrosion with 2507 Duplex Stainless Steel Welded Tubes. Engineered with a high concentration of chromium, molybdenum, and nitrogen, these tubes excel in preventing localized corrosion damage. Their dual-phase structure reinforces their capability to withstand corrosive attack, ensuring enhanced durability and performance, especially in challenging environments prone to crevice and pitting corrosion.
Experience excellent thermal conductivity with 2507 Duplex Stainless Steel Welded Tubes. Thanks to their unique composition featuring high chromium and molybdenum content, these tubes offer efficient heat transfer properties. This enables them to effectively manage temperature variations, making them a reliable choice for applications demanding optimal thermal performance.
Benefit from low thermal expansion characteristics with 2507 Duplex Stainless Steel Welded Tubes. Their carefully engineered composition, including a blend of chromium, nickel, and molybdenum, results in minimal expansion and contraction in response to temperature changes. This property makes them ideal for applications where dimensional stability and precise performance are essential, even in varying thermal conditions.
Application Of 2507 Duplex Stainless Steel Welded Tube
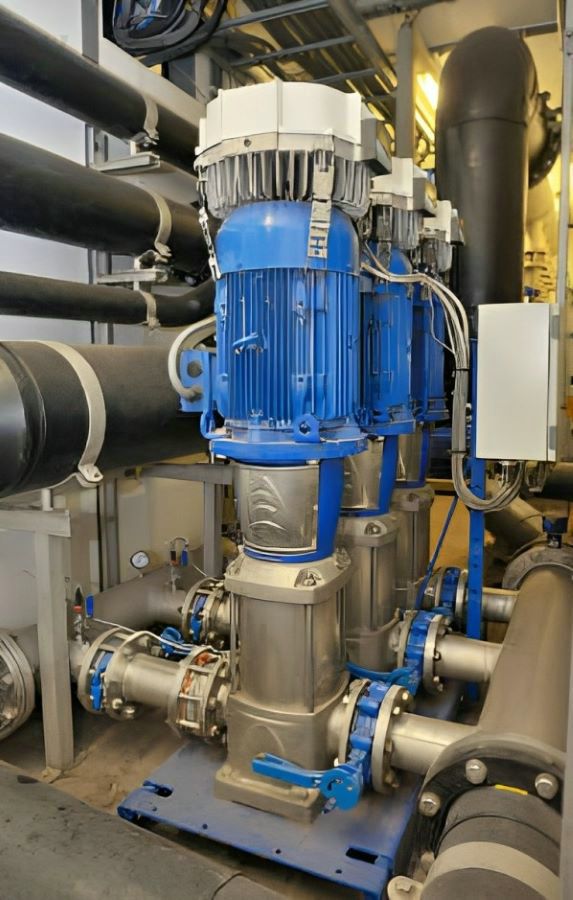
desalination equipment
The application of 2507 Duplex Stainless Steel Welded Tubes in desalination equipment is crucial for ensuring the efficiency and reliability of the desalination process. These tubes exhibit superior corrosion resistance, particularly in high chloride environments, making them ideal for handling seawater. Their resistance to pitting and crevice corrosion further enhances their suitability for desalination applications. By utilizing 2507 Duplex Stainless Steel Welded Tubes in desalination equipment, manufacturers can ensure the durability and longevity of their systems. These tubes effectively withstand the aggressive conditions of the desalination process, contributing to the production of clean and potable water. For sourcing high-quality 2507 Duplex Stainless Steel Welded Tubes, Huaxiao stainless steel tube suppliers can provide reliable solutions to meet the demands of desalination projects.
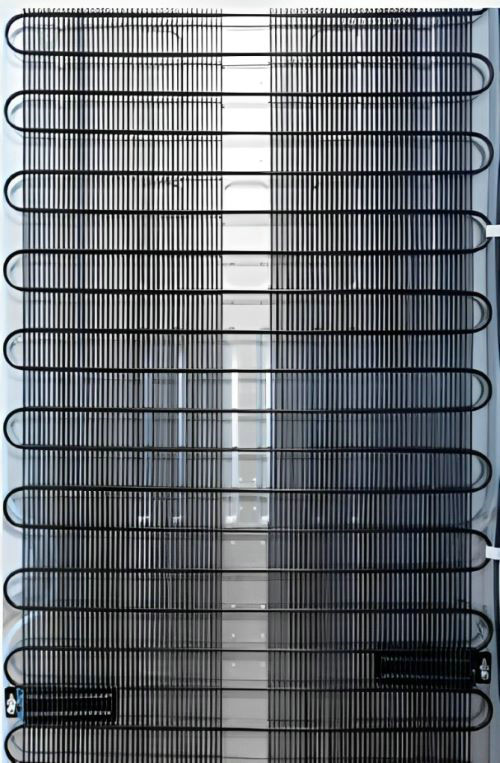
chemical process pressure vessels, piping, and heat exchangers
The application of 2507 Duplex Stainless Steel Welded Tubes in chemical process pressure vessels, piping, and heat exchangers is integral to the chemical industry. These tubes offer exceptional resistance to corrosion and stress corrosion cracking, making them suitable for handling aggressive chemicals and corrosive environments. Their high strength and durability make them a reliable choice for containing and transporting various chemicals. In chemical processing, maintaining the integrity of equipment is crucial to ensure safety and efficiency. 2507 Duplex Stainless Steel Welded Tubes, known for their corrosion resistance and robustness, play a pivotal role in maintaining the reliability of pressure vessels, piping systems, and heat exchangers. For sourcing high-quality tubes, Huaxiao stainless steel tube suppliers can provide the necessary expertise and products tailored to the needs of chemical process industries.
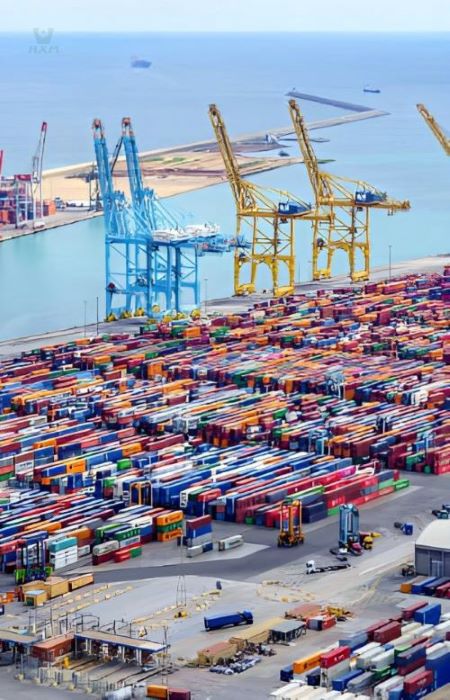
marine applications
The use of 2507 Duplex Stainless Steel Welded Tubes in marine applications is essential due to their exceptional resistance to corrosion and harsh marine environments. These tubes are particularly suited for various marine structures, such as offshore platforms, ship hulls, and subsea equipment. Their high strength, combined with superior corrosion resistance, makes them a reliable choice for prolonged exposure to saltwater, seawater, and marine atmospheres. In marine environments, the durability of materials is crucial to ensure the longevity and safety of maritime structures. 2507 Duplex Stainless Steel Welded Tubes provide the necessary reliability and performance required for withstanding the challenges posed by marine conditions. For sourcing top-quality tubes for marine applications, Huaxiao stainless steel tube suppliers offer the expertise and products tailored to the demands of the marine industry.
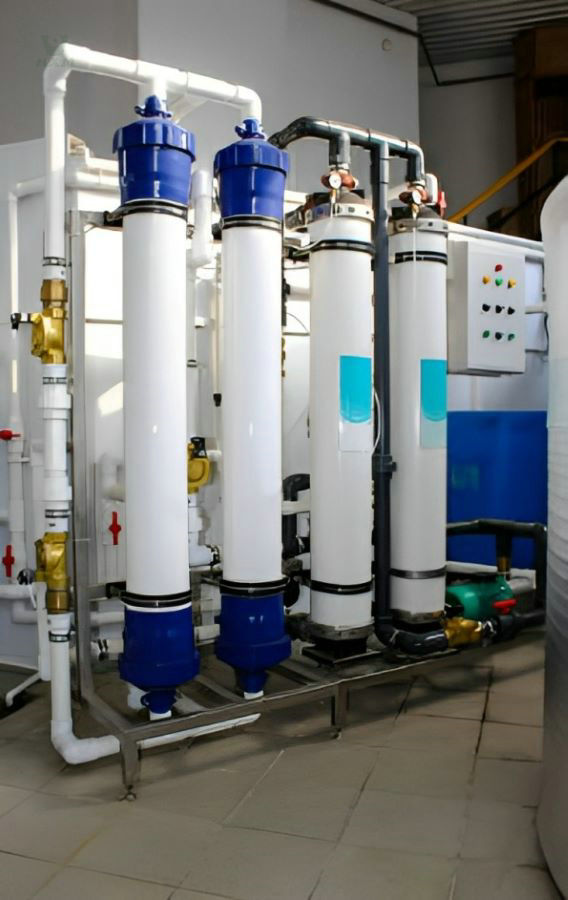
flue gas scrubbing equipment
2507 Duplex Stainless Steel Welded Tubes find a valuable application in flue gas scrubbing equipment. Flue gas scrubbers are crucial components in industries that aim to reduce emissions and pollutants from exhaust gases. The corrosive nature of flue gases, containing acids and other harmful compounds, requires materials with excellent corrosion resistance. The high corrosion resistance of 2507 Duplex Stainless Steel ensures that the tubes can withstand the aggressive environment of flue gas scrubbing systems. These tubes play a critical role in conveying and treating flue gases without undergoing deterioration due to chemical reactions or corrosion. In such demanding applications, partnering with Huaxiao stainless steel tube suppliers ensures access to tubes that meet the stringent requirements of flue gas scrubbing equipment for long-lasting and efficient performance.
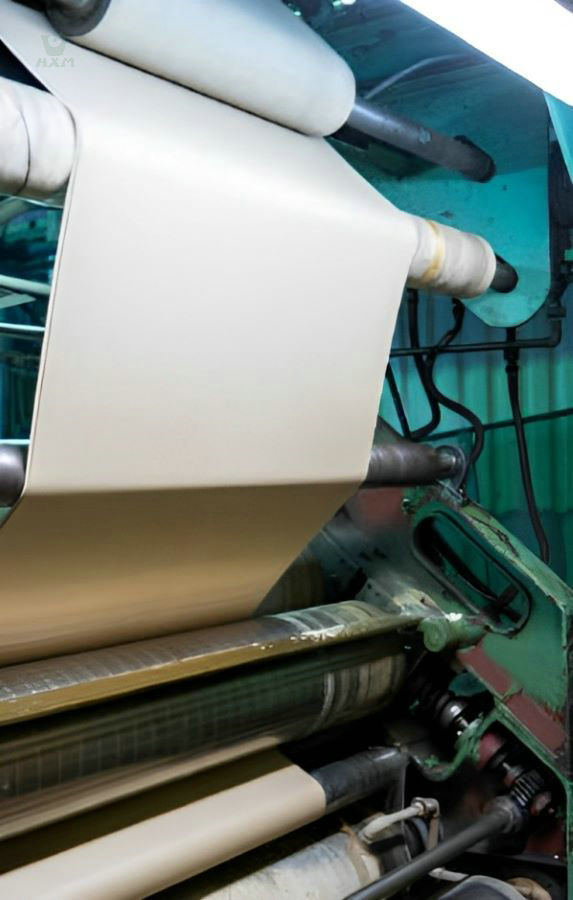
pulp and paper mill equipment
2507 Duplex Stainless Steel Welded Tubes are extensively utilized in pulp and paper mill equipment, where they serve in demanding and corrosive environments. These tubes are an ideal choice for various equipment components, including digester vessels, bleach towers, and pulp washers. The harsh conditions within pulp and paper processing involve exposure to chemicals, high temperatures, and corrosive liquids, making the corrosion resistance and durability of 2507 Duplex Stainless Steel crucial. In the challenging settings of pulp and paper mills, where equipment is subjected to a combination of mechanical stress and corrosive agents, 2507 Duplex Stainless Steel Welded Tubes excel. The material's resistance to corrosion, pitting, and stress-related issues contributes to the prolonged lifespan of the equipment and ensures reliable performance. Collaborating with Huaxiao stainless steel tube suppliers guarantees access to high-quality tubes designed to withstand the rigorous demands of pulp and paper mill equipment.
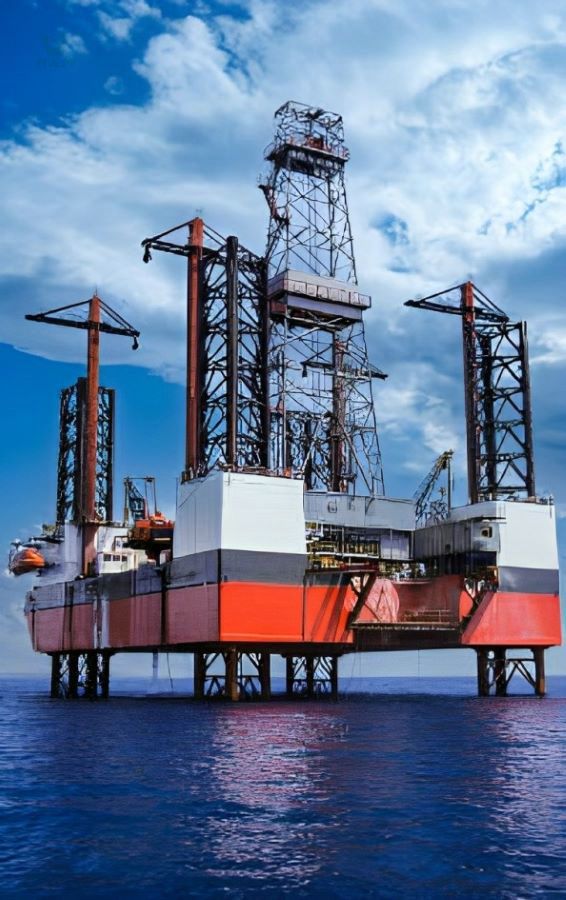
Offshore Oil production/technology
The application of 2507 Duplex Stainless Steel Welded Tubes in offshore oil production and technology is paramount. These tubes are employed in various critical components of offshore platforms, subsea equipment, and pipelines. The harsh and corrosive marine environment, coupled with the need for high strength and corrosion resistance, makes 2507 Duplex Stainless Steel an excellent choice. Offshore oil production requires materials that can withstand aggressive conditions, including exposure to seawater, extreme temperatures, and high pressures. 2507 Duplex Stainless Steel Welded Tubes offer exceptional resistance to corrosion, pitting, and crevice corrosion, ensuring the longevity and reliability of offshore equipment. Incorporating 2507 Duplex Stainless Steel Welded Tubes in offshore oil production/technology not only enhances the operational efficiency and safety of installations but also contributes to the overall sustainability and success of offshore endeavors.
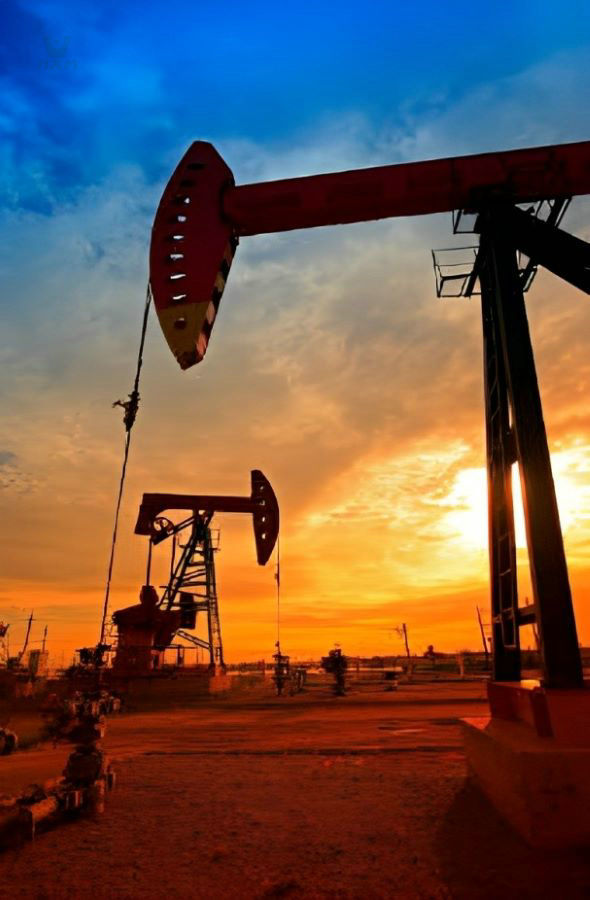
Oil and gas industry equipment
The application of 2507 Duplex Stainless Steel Welded Tubes in offshore oil production and technology is paramount. These tubes are employed in various critical components of offshore platforms, subsea equipment, and pipelines. The harsh and corrosive marine environment, coupled with the need for high strength and corrosion resistance, makes 2507 Duplex Stainless Steel an excellent choice. Offshore oil production requires materials that can withstand aggressive conditions, including exposure to seawater, extreme temperatures, and high pressures. 2507 Duplex Stainless Steel Welded Tubes offer exceptional resistance to corrosion, pitting, and crevice corrosion, ensuring the longevity and reliability of offshore equipment. Incorporating 2507 Duplex Stainless Steel Welded Tubes in offshore oil production/technology not only enhances the operational efficiency and safety of installations but also contributes to the overall sustainability and success of offshore endeavors.
FAQ
The terms “S32750” and “2507” both refer to the same material: a super duplex stainless steel. “S32750” is the UNS designation for this material, while “2507” is a common trade name used to refer to the same alloy. The numbers denote the chemical composition of the material. In practical terms, there is no difference between S32750 and 2507 – they both represent the same high-performance super duplex stainless steel with excellent corrosion resistance, high strength, and other desirable properties for demanding applications.
The main difference between 2205 and 2507 stainless steel lies in their composition and performance characteristics. Both are duplex stainless steels, which means they have a mixed microstructure of austenite and ferrite. However, 2507 is known as a “super duplex” stainless steel due to its higher alloy content and enhanced properties compared to 2205.
- Chemical Composition:
2205 (UNS S31803/S32205) contains about 22% chromium, 3% molybdenum, and 5-6% nickel.
2507 (UNS S32750) is a “super duplex” with higher alloy content, including about 25% chromium, 4% molybdenum, and 7% nickel.
- Corrosion Resistance:
2507 has superior corrosion resistance compared to 2205, especially in highly corrosive environments with chlorides and acidic solutions.
- Strength and Toughness:
2507 generally exhibits higher strength and toughness due to its higher alloy content, making it suitable for more demanding applications.
Chloride Stress Corrosion Cracking Resistance:
2507 offers better resistance to chloride-induced stress corrosion cracking, making it highly suitable for applications involving seawater and marine environments.
- Applications:
2205 is widely used in various industries, including chemical, petrochemical, and paper processing.
2507 is chosen for more critical applications where higher corrosion resistance and strength are required, such as offshore oil and gas platforms, desalination plants, and aggressive chemical environments.
In summary, while both 2205 and 2507 are duplex stainless steels with similar structures, 2507 offers enhanced properties and is particularly suitable for harsher environments and more demanding applications due to its higher alloy content and improved corrosion resistance.
While 2507 Duplex Stainless Steel Welded Tubes offer excellent mechanical properties and corrosion resistance, they can be more challenging to fabricate and weld compared to traditional austenitic stainless steels. This is primarily due to their dual-phase microstructure of austenite and ferrite. The combination of these phases can result in differences in thermal expansion, which may lead to distortion or warping during welding.
To address these challenges, it’s important to use proper welding procedures, filler materials, and techniques. Preheating and post-weld heat treatment might be required to minimize the risk of cracking and achieve optimal mechanical properties. Additionally, experienced welders familiar with duplex stainless steel characteristics should be employed to ensure high-quality welds.
Working with Huaxiao stainless steel tube suppliers and consulting with experienced professionals can provide guidance on the best practices for fabricating and welding 2507 Duplex Stainless Steel Welded Tubes while maintaining their superior properties and performance.
Using 2507 Duplex Stainless Steel Welded Tubes offers several advantages over using two separate materials for specific applications:
- Corrosion Resistance: 2507 Duplex Stainless Steel provides superior corrosion resistance compared to many individual materials. It offers resistance to a wide range of corrosive environments, including those with high chloride content and aggressive chemicals.
- Cost Savings: Instead of using two separate materials, which might require additional coatings or treatments to achieve corrosion resistance, using 2507 can result in cost savings over the long term due to reduced maintenance and replacement needs.
- Strength and Durability: 2507 Duplex Stainless Steel combines the high strength of ferritic stainless steels with the excellent toughness of austenitic stainless steels. This results in a material that can withstand demanding conditions and mechanical stresses.
- Reduced Risk of Galvanic Corrosion: When using two different materials, galvanic corrosion between dissimilar metals can be a concern. By using 2507 Duplex Stainless Steel, which is a single material, this risk is minimized.
- Simplified Design: Designing with a single material like 2507 can simplify the engineering and fabrication process. There’s no need to accommodate different material properties or interface issues between two separate materials.
- Consistent Properties: 2507 Duplex Stainless Steel offers consistent properties throughout the material, ensuring uniform performance across the entire structure or system.
- Ease of Welding: While welding dissimilar materials can be complex, using 2507 Duplex Stainless Steel eliminates the need for joining different materials, simplifying the welding process.
- Longevity: 2507 Duplex Stainless Steel’s combination of corrosion resistance and strength contributes to the longevity of the structure or equipment, reducing the need for frequent repairs or replacements.
By using 2507 Duplex Stainless Steel Welded Tubes, you can achieve the benefits of multiple materials without the challenges and potential issues associated with using separate materials, ultimately leading to improved performance, longevity, and cost-effectiveness.
Yes, passivation is recommended for 2507 Duplex Stainless Steel Welded Tubes to enhance their corrosion resistance and maintain their surface quality. Passivation is a chemical treatment that removes contaminants and impurities from the surface of the stainless steel, forming a protective oxide layer that helps prevent corrosion and staining.
Despite its excellent corrosion resistance properties, 2507 Duplex Stainless Steel can still benefit from passivation, especially after welding or fabrication processes. Welding can introduce heat-affected zones and alter the surface composition, making these areas more susceptible to corrosion.
Passivation helps to:
- Remove Contaminants: Passivation removes surface contaminants such as iron particles, grease, and other potential sources of corrosion.
- Restore the Oxide Layer: During welding or machining, the protective oxide layer on stainless steel can be compromised. Passivation helps to restore and enhance this layer.
- Improve Corrosion Resistance: The passivation process creates a more uniform and stable oxide layer, improving the material’s resistance to corrosion and pitting.
- Enhance Appearance: Passivation can improve the aesthetic appearance of the stainless steel surface, making it more resistant to discoloration and stains.
- Extend Lifespan: Properly passivated stainless steel exhibits improved durability and longevity, reducing the need for maintenance and replacement.
While 2507 Duplex Stainless Steel already has excellent corrosion resistance properties, passivation is a proactive step to ensure the material’s long-term performance and maintain its appearance in aggressive or demanding environments. It is recommended to consult with experts or stainless steel tube suppliers to determine the appropriate passivation process for your specific application.
The nitrogen content in 2507 Duplex Stainless Steel plays a crucial role in enhancing its overall performance and properties. Nitrogen is intentionally added to the alloy to improve its strength, corrosion resistance, and other mechanical characteristics. Here’s how the nitrogen content impacts the performance of 2507 Duplex Stainless Steel:
- Enhanced Corrosion Resistance: The addition of nitrogen boosts the alloy’s resistance to pitting and crevice corrosion, especially in chloride-rich environments. Nitrogen interacts with other alloying elements to form a protective passive layer on the surface, increasing its ability to withstand corrosive attacks.
- Increased Strength: Nitrogen contributes to the alloy’s strength by solid solution strengthening. This results in higher yield and tensile strengths compared to standard austenitic stainless steels. The combination of strength and corrosion resistance makes 2507 suitable for demanding applications.
- Improved Toughness: The presence of nitrogen improves the toughness and ductility of 2507 Duplex Stainless Steel. This is particularly important in applications where the material may experience impact loads or sudden temperature changes.
- Reduced Intergranular Corrosion: Nitrogen forms nitrides that tie up carbon and prevent the formation of chromium carbides at grain boundaries. This reduces the risk of intergranular corrosion and sensitization during welding and high-temperature exposure.
- Stabilization of Austenite: Nitrogen helps stabilize the austenitic phase in the duplex microstructure, promoting a balanced mix of austenite and ferrite. This contributes to the alloy’s high mechanical strength and corrosion resistance.
- Improved Weldability: Higher nitrogen content enhances the weldability of 2507 by minimizing the formation of harmful precipitates during welding, leading to reduced susceptibility to hot cracking and embrittlement.
- Temperature Performance: Nitrogen contributes to the alloy’s ability to perform well at elevated temperatures by improving its strength retention and resistance to thermal degradation.
In summary, the nitrogen content in 2507 Duplex Stainless Steel significantly enhances its corrosion resistance, strength, toughness, weldability, and overall performance in demanding environments. The careful balance of nitrogen and other alloying elements makes 2507 an excellent choice for applications requiring superior corrosion resistance and mechanical properties.
Yes, specific welding consumables are recommended for joining 2507 Duplex Stainless Steel Welded Tubes to ensure the best results in terms of weld quality and performance. Due to the unique composition and duplex microstructure of 2507, selecting the right welding consumables is crucial to avoid issues like corrosion, cracking, and reduced mechanical properties. Here are some general recommendations for welding consumables when working with 2507 Duplex Stainless Steel:
- Filler Metal Type: For welding 2507, it’s advisable to use duplex stainless steel filler metals with a similar composition. These filler metals typically contain elements like chromium, nickel, molybdenum, and nitrogen in proportions that match the base metal.
- Matching Alloys: Welding consumables with designations like ER2209 are commonly used for welding 2507 Duplex Stainless Steel. ER2209 is a duplex filler metal designed specifically for welding similar duplex stainless steels.
- Controlled Ferrite Content: Select filler metals that can help maintain the desired ferrite content in the weld to achieve the desired balance of mechanical properties and corrosion resistance. The ferrite content is critical for avoiding issues like intergranular corrosion and brittleness.
- Low Carbon Content: Welding consumables with low carbon content are preferred to avoid the risk of carbide precipitation and sensitization during welding.
- Welding Process: Common welding processes such as gas tungsten arc welding (GTAW/TIG) and gas metal arc welding (GMAW/MIG) can be used for welding 2507 Duplex Stainless Steel. However, proper control of welding parameters and heat input is essential to maintain the integrity of the weld.
- Preheating and Post-Weld Heat Treatment: Depending on the application and thickness of the material, preheating and post-weld heat treatment may be recommended to reduce the risk of cracking and improve the mechanical properties of the weld.
It’s crucial to consult with welding professionals, engineers, or stainless steel experts who have experience with 2507 Duplex Stainless Steel to select the appropriate welding consumables and develop a suitable welding procedure. Using the right consumables and following proper welding practices will help ensure the integrity and performance of the welded joints in 2507 Duplex Stainless Steel Welded Tubes.