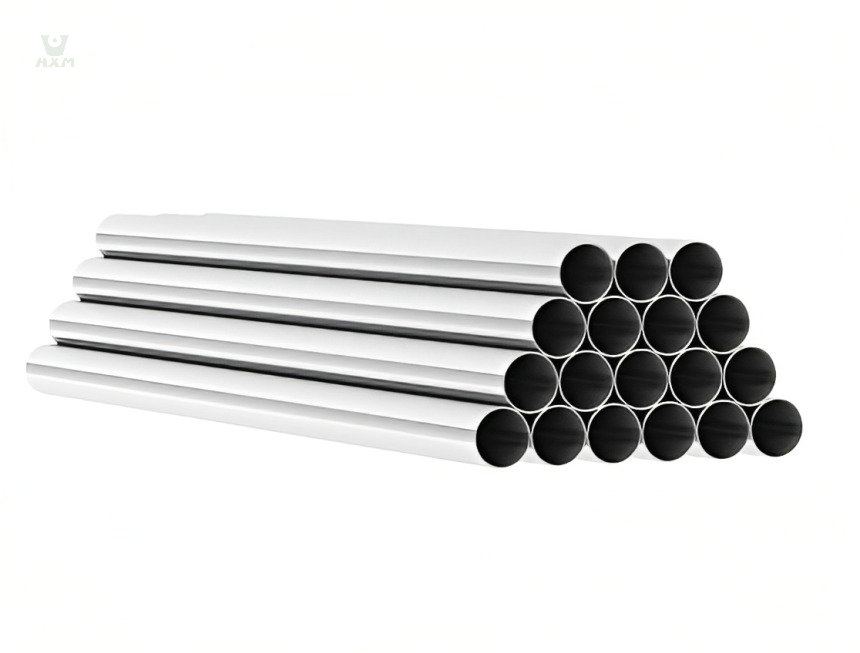
904L stainless steel welded tube Supplier
- Size Range: From 4mm4mm to 800mm800mm
- Wall Thickness Range: From 1mm to 150mm (SCH10-XXS)
- Length Options: 4000mm, 5800mm, 6000mm, 12000mm, or as required.
- Finish: 2B, BA,4K,8K, NO.1,2D,3#, HL
- Type: Round, square, rectangular, hexagonal, flat, angle
- Technique: Cold rolled, hot rolled
Product Description Of 904L Stainless Steel Welded Tube
Introducing 904L Stainless Steel Welded Tube, also known as UNS N08904, a low carbon high-alloy austenitic stainless steel. Widely used in applications where AISI 316L and AISI 317L lack sufficient corrosion resistance. The addition of copper enhances its corrosion resistance, especially against sulfuric, phosphoric, and acetic acids. However, its use in hydrochloric acid is limited. It exhibits high resistance to pitting in chloride solutions, crevice corrosion, and stress corrosion cracking. With its non-magnetic austenitic structure, 904L offers excellent formability and weldability, even at low temperatures. Its high chromium content promotes and maintains a passive film, protecting the material in various corrosive environments. Compared to other molybdenum-containing stainless steels like 316L and 317L, 904L demonstrates stronger resistance to ferrite and sigma phase precipitation during cooling and welding. Its low carbon content eliminates the risk of intergranular corrosion during cooling or welding. The maximum recommended operating temperature for 904L is 450°C. Choose 904L stainless steel welded tube for superior corrosion resistance and exceptional performance in demanding environments. Available from Huaxiao stainless steel tube suppliers.
Product Description Of 904L Stainless Steel Welded Tube
Chemical Components of 409L Stainless Steel Welded Tube
904L | C % | Si % | Mn % | P% | S% | Cr% | Ni% | Mo% | Cu |
ASTM | ≤ 0.02 | ≤ 1.0 | ≤2.0 | ≤0.045 | ≤0.035 | 19-23 | 23-28 | 4-5 | 1-2 |
JIS | ≤ 0.02 | ≤ 1.0 | ≤2.0 | ≤0.045 | ≤0.035 | 19-23 | 23-28 | 4-5 | 1-2 |
EN | ≤ 0.02 | ≤ 1.0 | ≤2.0 | ≤0.045 | ≤0.035 | 19-23 | 23-28 | 4-5 | 1-2 |
GB | ≤ 0.02 | ≤ 1.0 | ≤2.0 | ≤0.045 | ≤0.035 | 19-23 | 23-28 | 4-5 | 1-2 |
Mechanical Properties of 409L Stainless Steel Welded Tube
Physical Properties | 904L |
Density (g/cm³) | 7.95 |
Melting point (℃) | 1350-1400 |
Thermal conductivity (W/m-K) | 11.0 |
Coefficient of thermal expansion (10^-6/K) | 12-15 |
Resistivity (μΩ-cm) | 75-85 |
Magnetic Permeability (H/m) | ≤1.02 |
Features Of 904L Stainless Steel Welded Tube
One of the key features of 904L stainless steel welded tube is its exceptional corrosion resistance. This grade exhibits outstanding performance in aggressive environments containing sulfuric acid, phosphoric acid, and acetic acid, making it highly suitable for applications where traditional chrome-nickel steels may fail. The addition of copper in its composition further enhances its resistance to corrosion, especially in chloride-containing solutions. Its ability to withstand harsh conditions and resist pitting, crevice corrosion, and other forms of corrosion makes it a preferred choice for various demanding industrial applications.
904L stainless steel welded tube is characterized by its high alloy content, which contributes to its exceptional performance in various environments. The alloying elements such as chromium, nickel, and molybdenum, along with the addition of copper, enhance the material’s corrosion resistance and overall mechanical properties. This high alloy content gives 904L stainless steel welded tube superior strength and toughness, making it well-suited for challenging applications where durability and reliability are crucial. The combination of these alloying elements also imparts excellent weldability and formability, ensuring ease of fabrication and installation for a wide range of industrial uses.
One of the notable features of 904L stainless steel welded tube is its exceptional formability and weldability. The material exhibits superb malleability and ductility, allowing it to be easily shaped and formed into various complex geometries without compromising its structural integrity. This formability makes it ideal for applications that require intricate designs and precise dimensions.
Moreover, 904L stainless steel welded tube demonstrates excellent weldability, enabling seamless joining with other components or structures. It can be efficiently welded by stainless steel tube suppliers using standard welding techniques, ensuring strong and reliable connections. This characteristic is crucial for industries that demand efficient fabrication and assembly processes, saving time and resources during installation.
With its outstanding formability and weldability, 904L stainless steel welded tube proves to be a versatile and reliable solution for a wide range of applications, including petrochemical, power generation, and food processing industries, where complex shapes and secure welding joints are essential for optimal performance.
Another key characteristic of 904L stainless steel welded tube is its non-magnetic nature. The material exhibits a fully austenitic microstructure, which renders it non-magnetic in all conditions. This property is beneficial in applications where magnetic interference could cause issues or disrupt sensitive equipment.
The non-magnetic feature makes 904L stainless steel welded tube suitable for various industries, including electronics, medical equipment, and aerospace, where magnetic interference must be minimized or eliminated. Additionally, in environments where magnetic properties might interfere with precision instruments or electronic devices, the non-magnetic nature of 904L stainless steel ensures reliable performance and accuracy.
Overall, the non-magnetic property adds to the versatility and usability of 904L stainless steel welded tube, making it an excellent choice for diverse applications that demand both corrosion resistance and non-magnetic characteristics.
904L stainless steel welded tube exhibits exceptional high-temperature performance, making it well-suited for applications in extreme heat environments. With a melting point of around 1350°C (2462°F), this alloy can withstand elevated temperatures without significant loss of structural integrity or mechanical properties.
The high alloy content in 904L contributes to its excellent heat resistance, enabling it to maintain its strength and corrosion resistance even at elevated temperatures. This property is particularly advantageous in industries such as petrochemical processing, thermal processing, and power generation, where materials are exposed to intense heat and harsh conditions.
Moreover, 904L’s ability to resist oxidation and scale formation at high temperatures further enhances its durability and longevity in challenging operating conditions. The material’s stable microstructure ensures reliable performance under prolonged exposure to elevated temperatures.
In conclusion, 904L stainless steel welded tube’s remarkable high-temperature performance, coupled with its superior corrosion resistance and other beneficial characteristics, makes it a top choice for various demanding applications in industries where exposure to extreme heat is a critical factor.
904L stainless steel welded tube exhibits exceptional toughness, which is a crucial characteristic in demanding industrial applications. Its high alloy content and unique microstructure contribute to this outstanding toughness, making it highly resistant to cracking and brittleness under mechanical stress.
This toughness ensures that the tube can withstand heavy loads, impacts, and vibrations without deformation or failure, providing reliable performance and structural integrity even in challenging environments. As a result, 904L is commonly used in applications where mechanical strength and durability are paramount, such as in offshore and marine industries, chemical processing plants, and structural components subject to dynamic forces.
One of the outstanding features of 904L stainless steel welded tube is its exceptional resistance to pitting and crevice corrosion. Pitting corrosion occurs as localized holes or pits on the surface of the material, while crevice corrosion occurs in the narrow spaces between two surfaces, such as gaskets or fittings.
The high levels of chromium, nickel, and molybdenum in 904L provide excellent protection against these types of corrosive attacks. This resistance is particularly crucial in aggressive environments containing chloride ions, such as seawater, acidic solutions, and chemical processing plants.
Due to its ability to withstand pitting and crevice corrosion, 904L is widely used in various industries, including offshore and marine applications, chemical processing, and petrochemical industries. The tube’s ability to maintain its integrity in corrosive environments ensures longevity and reduces the risk of leaks or failures, making it a reliable choice for critical applications where corrosion resistance is essential.
904L stainless steel welded tube exhibits a low risk of intergranular corrosion, also known as sensitization or weld decay. Intergranular corrosion occurs along grain boundaries due to the precipitation of chromium carbides during welding or heat treatment, leading to reduced corrosion resistance in these regions.
The low carbon content of 904L stainless steel minimizes the formation of chromium carbides, thereby reducing the risk of intergranular corrosion. This characteristic is particularly crucial in applications involving exposure to elevated temperatures and aggressive environments.
The resistance to intergranular corrosion ensures the structural integrity and long-term performance of the welded tube in critical applications, such as petrochemical plants, heat exchangers, and refinery equipment. It provides peace of mind to engineers and end-users, knowing that the material will maintain its corrosion resistance and mechanical properties over extended periods of service.
Application Of 904L Stainless Steel Welded Tube
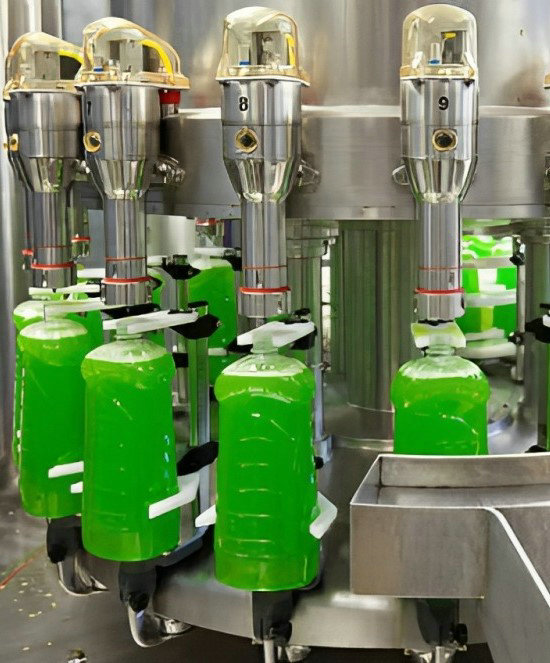
Chemical Processing
904L stainless steel welded tubes are supplied by reputable stainless steel tube suppliers. In chemical processing, 904L stainless steel welded tubes are extensively used due to their exceptional corrosion resistance and high alloy content. They are employed in various applications, including reactors, vessels, and pipelines, where they can withstand exposure to corrosive chemicals, acids, and solvents. The non-magnetic nature and resistance to pitting and crevice corrosion make them ideal for critical environments, ensuring the safety and reliability of chemical processing equipment and systems.
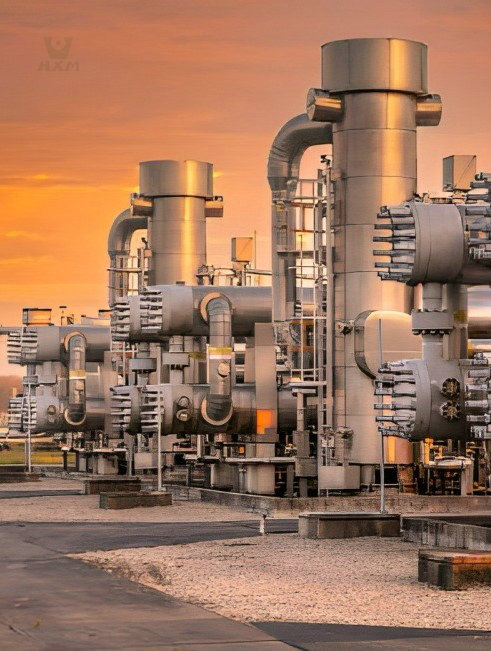
Oil and Gas
In the oil and gas industry, 904L stainless steel welded tubes are widely utilized for their remarkable resistance to corrosion and high temperature performance. These tubes are employed in various components of oil and gas production and processing, including pipelines, offshore platforms, and equipment exposed to harsh and corrosive environments. The superior toughness and low risk of intergranular corrosion make them well-suited for critical applications, ensuring reliable performance and extended service life in the challenging conditions of the oil and gas industry.

Pharmaceutical
In the pharmaceutical industry, 904L stainless steel welded tubes find essential applications due to their exceptional corrosion resistance and hygienic properties. These tubes are used in various pharmaceutical processing equipment and systems, such as pharmaceutical reactors, piping, and storage tanks. The non-magnetic nature of 904L stainless steel ensures that it does not interfere with sensitive pharmaceutical processes. Additionally, its resistance to pitting and crevice corrosion makes it a reliable choice for maintaining product purity and safety in pharmaceutical manufacturing environments. With excellent formability and weldability, 904L stainless steel tubes facilitate efficient fabrication and installation in pharmaceutical facilities, ensuring high-quality and safe production processes. For top-notch quality, trust Huaxiao stainless steel tube suppliers offering reliable solutions for pharmaceutical applications.
FAQ
Yes, 904L stainless steel welded tubes are highly resistant to corrosion in seawater and marine environments. The high alloy content, along with its nickel, chromium, and molybdenum composition, gives 904L exceptional resistance to pitting and crevice corrosion in chloride-containing solutions, making it an ideal choice for marine applications and offshore structures.
To clean and maintain 904L stainless steel tubes, follow these recommendations:
- Regular Cleaning: Clean the tubes regularly with mild soap or detergent and warm water. Avoid using abrasive cleaners or pads that may scratch the surface.
- Avoid Harsh Chemicals: Avoid using harsh chemicals or cleaning agents that may damage the protective oxide layer on the surface of the tubes.
- Rinse Thoroughly: After cleaning, rinse the tubes thoroughly with clean water to remove any residue or cleaning agents.
- Wipe Dry: Use a soft, clean cloth to wipe the tubes dry to prevent water spots or stains.
- Avoid Contact with Chlorides: Minimize exposure to chlorides, as they can cause pitting corrosion in the tubes.
- Routine Inspection: Regularly inspect the tubes for any signs of corrosion or damage. Promptly address any issues to prevent further deterioration.
- Professional Maintenance: For more extensive cleaning or maintenance, consider seeking professional help to ensure proper care of the tubes.
By following these guidelines, you can maintain the appearance and performance of 904L stainless steel tubes for extended service life in various applications.
Yes, 904L stainless steel offers excellent resistance to sulfuric acid and other harsh chemicals. Its high alloy content, particularly with the addition of copper, enhances its corrosion resistance, making it well-suited for environments with sulfuric acid, phosphoric acid, and acetic acid. Additionally, 904L exhibits superior resistance to pitting and crevice corrosion, making it a preferred choice for various industries, including chemical processing, petrochemical, and pharmaceutical, where exposure to corrosive chemicals is common. Its ability to withstand aggressive chemical environments makes 904L stainless steel a reliable and durable material in demanding applications.
Yes, custom sizes and lengths are available for 904L stainless steel welded tubes. Stainless steel tube suppliers often offer a wide range of options to meet the specific requirements of different applications. This flexibility allows customers to obtain tubes in various dimensions and lengths tailored to their project needs, ensuring an efficient and precise fit for their intended use. Customization options provide added convenience and versatility, making 904L stainless steel welded tubes suitable for a wide range of industries and applications.
Yes, 904L stainless steel is compatible with various types of fittings and connectors commonly used in piping systems. Its excellent corrosion resistance and high alloy content make it suitable for handling different fluids and chemicals, including those found in aggressive environments. As a result, 904L stainless steel welded tubes can be easily connected to a wide range of fittings and connectors without compromising their performance or integrity. This compatibility ensures seamless integration with existing systems and provides reliable and efficient solutions for various industrial applications.
The production of 904L stainless steel welded tubes is governed by various international standards to ensure their quality and performance. Some of the commonly used standards include:
- ASTM A269 – Standard Specification for Seamless and Welded Austenitic Stainless Steel Tubing for General Service.
- ASTM A312 – Standard Specification for Seamless, Welded, and Heavily Cold Worked Austenitic Stainless Steel Pipes.
- ASTM A789 – Standard Specification for Seamless and Welded Ferritic/Austenitic Stainless Steel Tubing for General Service.
- ASTM A790 – Standard Specification for Seamless and Welded Ferritic/Austenitic Stainless Steel Pipe.
These standards define the requirements for the chemical composition, mechanical properties, manufacturing methods, and testing procedures of 904L stainless steel welded tubes to ensure their compliance with industry regulations and customer specifications. Adhering to these standards guarantees the high quality and reliability of the tubes for various industrial applications.
Yes, 904L stainless steel welded tubes can be used in structural applications. Due to their high corrosion resistance, excellent formability, and superior toughness, they are suitable for a wide range of structural purposes. These tubes can be used in various industries, such as chemical processing, oil and gas, pharmaceuticals, and more, where structural integrity and durability are essential. Their non-magnetic properties, resistance to pitting and crevice corrosion, and low risk of intergranular corrosion make them a reliable choice for structural components exposed to harsh environments or aggressive chemicals. Additionally, their high temperature performance further extends their applicability in structural designs requiring elevated temperature resistance. When considering 904L stainless steel welded tubes for structural applications, it is essential to ensure compliance with relevant standards and industry regulations to guarantee safety and performance.
Other Products
Get In touch
Ready to Elevate Your Projects? Dive into our Stainless Steel Collection and Submit Your Specifications Today!
Phone/WhatsApp/WeChat:
+86 13052085117
Email: [email protected]
Address: RM557, NO.1388 Jiangyue Road, Shanghai China